Zastosowania komputerów w przemyśle
Kontakt w sprawie artykułu: Mateusz Fas - 2025-02-26
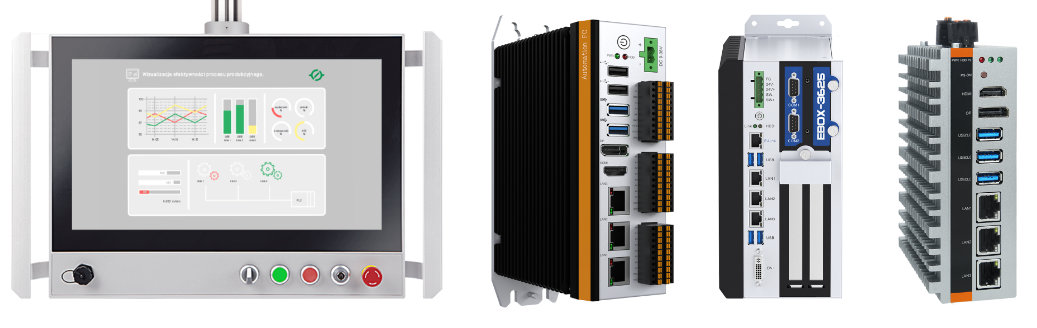
Z tego artykułu dowiesz się:
- jakie są kluczowe cechy komputerów przemysłowych (IPC),
- jakie są najpopularniejsze zastosowania IPC.
Komputery są dziś wszędzie – i są praktycznie niezastąpione. Towarzyszą nam w codziennym życiu i w pracy. W erze Przemysłu 4.0 automatycy coraz częściej mają do czynienia z komputerami przemysłowymi, dlatego dzisiaj przyjrzymy się trendowi komputeryzacji i cyfryzacji firm, a także przybliżymy przykładowe zastosowania komputerów w przemyśle.
W zasadzie czym jest ten komputer przemysłowy? Czym on się różni od tradycyjnych komputerów biurkowych?
Komputery przemysłowe (Industrial PC – IPC) to niezawodne urządzenia, pozwalające na pracę w ciężkich warunkach przemysłowych. W przemyśle nie ma miejsca na awarie, dlatego komputery IPC charakteryzują się m.in. zwiększoną odpornością na zapylenie, kurz, wodę i wstrząsy w stosunku do tradycyjnych PC. Dodatkowo są przystosowane do pracy w skrajnie niskich oraz wysokich temperaturach.
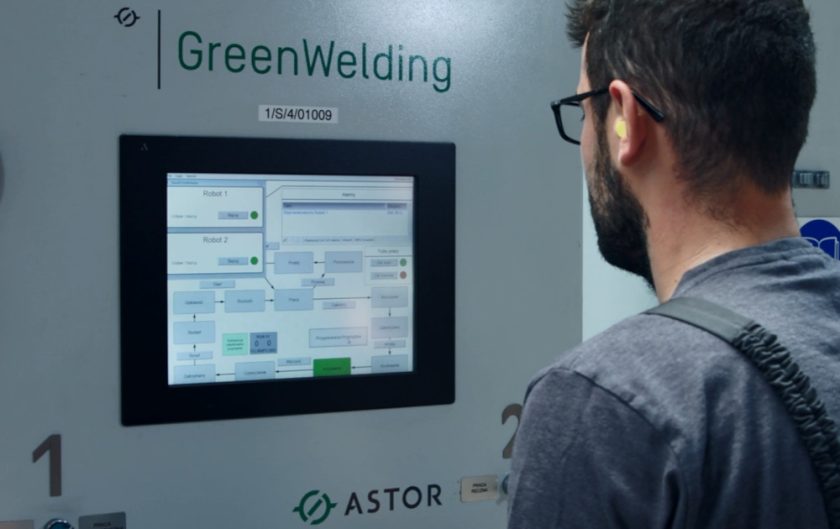
Natomiast z punktu widzenia oprogramowania IPC nie różnią się niczym od zwykłych domowych lub biurowych pecetów. Można na nich uruchamiać standardowe systemy operacyjne i aplikacje. Wyróżnia je jedynie przemysłowe wykonanie, zapewniające wysoką niezawodność i bezawaryjną pracę niezależnie od warunków.
Przeczytaj też: „Komputer przemysłowy” to nie tylko „bardziej solidny”
Komputery przemysłowe doskonale sprawdzają się w bardzo wielu zastosowaniach. Zobaczmy kilka najważniejszych.
Automatyzacja i digitalizacja produkcji
Komputery przemysłowe są często używane do sterowania maszynami i urządzeniami na liniach produkcyjnych. Mogą one zarządzać różnorodnymi procesami, takimi jak montaż, obróbka, pakowanie czy kontrola jakości.
Komputery na produkcji często współpracują z systemami SCADA oraz sterownikami PLC. SCADA zbiera dane z różnych punktów w procesie produkcyjnym, które następnie są przetwarzane i analizowane na komputerze. Sterowniki PLC realizują bezpośrednie sterowanie maszynami, natomiast IPC mogą zarządzać ich pracą na wyższym poziomie, koordynując zadania i zapewniając, że procesy przebiegają zgodnie z planem.
Firmy produkcyjne przetwarzają coraz większe ilości danych, w związku z tym rośnie zapotrzebowanie na moc obliczeniową. Coraz częściej zdarza się, że komputer IPC zastępuje standardowy sterownik PLC, oferując znacznie większą moc obliczeniową. W komputerach pojawiają się porty CAN oraz wejścia i wyjścia cyfrowe – czyli elementy, które dawniej były kojarzone ze sterownikami PLC. Dodatkowo komputer może bez problemu komunikować się z wykorzystaniem popularnych protokołów, takich jak EtherCAT albo Profinet.
Kontrola jakości
Nadzór jest nieodzownym elementem produkcji czegokolwiek. Komputer w połączeniu z systemem wizyjnym stanowi istotne narzędzie w kontroli jakości procesów. Systemy wizyjne wykorzystują kamery i oprogramowanie do przechwytywania, analizy i interpretacji obrazów, a IPC przetwarzają te dane w czasie rzeczywistym. W związku z tym w komputerach przemysłowych pojawiły się porty PoE, wspierające między innymi komunikację z kamerami. Dzięki temu możemy zautomatyzować wiele zadań, które wcześniej wymagały interwencji człowieka.
W praktyce kamery w połączeniu z komputerem mogą identyfikować wady, takie jak zarysowania, nierówności, błędy w montażu, a nawet subtelne różnice w kolorach czy kształtach. Dzięki temu produkty niespełniające norm jakościowych mogą być automatycznie odrzucane lub oznaczane do dalszej inspekcji.
Komputery coraz częściej posiadają również wbudowany kanały PWM do sterowania oświetleniem. Odpowiednie oświetlenie ma kluczowe znaczenie dla rejestrowania wysokiej jakości obrazów, co z kolei przekłada się na dokładniejszą analizę i wykrywanie wad.
Zbieranie, raportowanie, analiza oraz archiwizowanie danych
Systemy SCADA zbierają ogromne ilości danych z czujników, urządzeń i maszyn w fabryce. Komputery IPC są wykorzystywane do przechowywania tych danych lokalnie. W zależności od potrzeb firmy mogą one przechowywać dane na różnych nośnikach, od dysków SSD po redundantne macierze RAID, które zapewniają zarówno wysoką wydajność, jak i bezpieczeństwo danych. IPC mogą także przetwarzać te dane w czasie rzeczywistym, agregując je, analizując i wizualizując na potrzeby operatorów i inżynierów.
Komputery IPC mogą być również odpowiedzialne za długoterminowe archiwizowanie danych. Archiwizacja jest kluczowa dla analizy trendów, raportowania zgodności z normami, oraz dla celów audytowych i historycznych. Dane mogą być archiwizowane lokalnie na IPC lub przesyłane do zewnętrznych serwerów, systemów chmurowych lub magazynów danych, w zależności od polityki bezpieczeństwa i wymagań firmy.
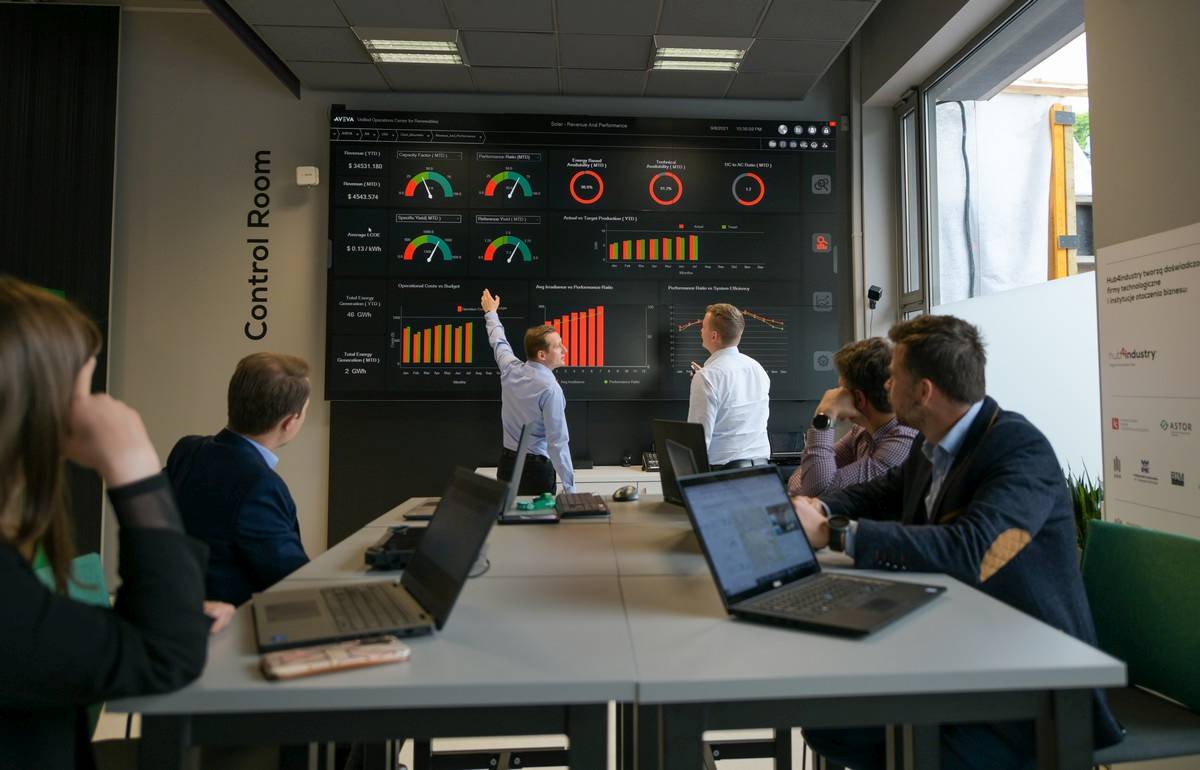
Edge Computing w przemyśle
Edge Computing to podejście, które polega na przetwarzaniu danych blisko źródła ich powstawania, zamiast przesyłania ich do centralnych serwerów lub chmury. W kontekście przemysłowym oznacza to, że dane zbierane z czujników, sterowników PLC, układów I/O i urządzeń produkcyjnych są analizowane na miejscu na jednym urządzeniu, co pozwala na szybsze reakcje na zmieniające się warunki i redukuje opóźnienia w komunikacji.
Typowym przykładem zastosowania Edge Computing jest monitorowanie stanu maszyn w czasie rzeczywistym, będące elementem Predictive Maintenance. Pozwala ono w przypadku wykrycia anomalii automatycznie wysłać alert lub nawet zaplanować konserwację urządzeń, zanim dojdzie do awarii. Systemy oparte na Edge mogą również skutecznie monitorować zużycie energii w różnych częściach zakładu i dostosowywać pracę maszyn tak, aby zoptymalizować koszty, co w dobie rosnących cen energii może przekładać się na znaczne oszczędności.
W miarę jak zakłady produkcyjne będą stawały się coraz bardziej złożone i zautomatyzowane, rola Edge Computing będzie rosła. Integracja z sztuczną inteligencją (AI) może dodatkowo zwiększyć możliwości i efektywność przemysłowych systemów opartych na Edge Computing. Stosując przetwarzanie blisko źródła dążymy do optymalizacji czasu i kosztów oraz podniesienia bezpieczeństwa i dostępności.
Przeczytaj też: Edge Computing. Co to jest przetwarzanie brzegowe?
Cyberbezpieczeństwo
Coraz większa liczba zakładów przemysłowych wdraża technologie cyfrowe, automatyzację oraz Internet Rzeczy (IoT), ponieważ przynosi to ogromne korzyści w zakresie efektywności i jakości. Cyfryzacja otwiera jednak drzwi dla nowych zagrożeń w obszarze cyberbezpieczeństwa. Komputery przemysłowe mogą działać jako bramki lub routery, zarządzając ruchem sieciowym w fabrykach. Integracja z zaporami sieciowymi, systemami wykrywania włamań oraz innymi narzędziami bezpieczeństwa pozwala na monitorowanie i filtrowanie ruchu sieciowego w czasie rzeczywistym. W dużych firmach produkcyjnych komputery IPC mogą być używane do zarządzania uprawnieniami i dostępem do różnych systemów i urządzeń. Dodatkowo komputery przemysłowe mogą obsługiwać szyfrowane protokoły komunikacji, minimalizując ryzyko przechwycenia danych.
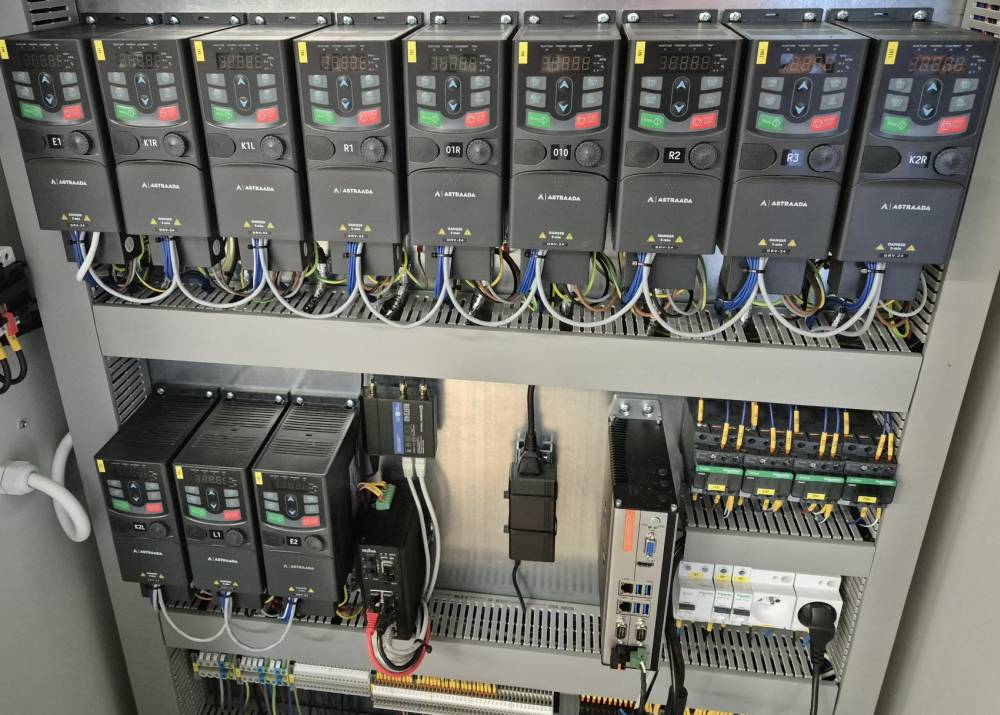
Interfejsy HMI (Human-Machine Interface)
Komputery przemysłowe, a dokładniej komputery panelowe „all in one”, są często używane jako interfejsy HMI, które pozwalają operatorom na interakcję z maszynami. Komputery wyposażone w dotykowy ekran umożliwiają operatorom monitorowanie stanu maszyn i wprowadzanie zmiany w ustawieniach, a także pozwalają reagować na alerty w czasie rzeczywistym. W zależności od warunków firmy mogą zdecydować się na ekrany pojemnościowe lub rezystancyjne. Te pierwsze oferują większą precyzję i szybkość reakcji na dotyk oraz obsługują funkcję multitouch. Ich wadą może być utrudnienie obsługi w rękawiczkach. Z kolei ekrany rezystancyjne reagują na nacisk, co oznacza, że można je obsługiwać nie tylko palcem, ale także dowolnym przedmiotem, takim jak rysik, długopis, czy nawet rękawice robocze.
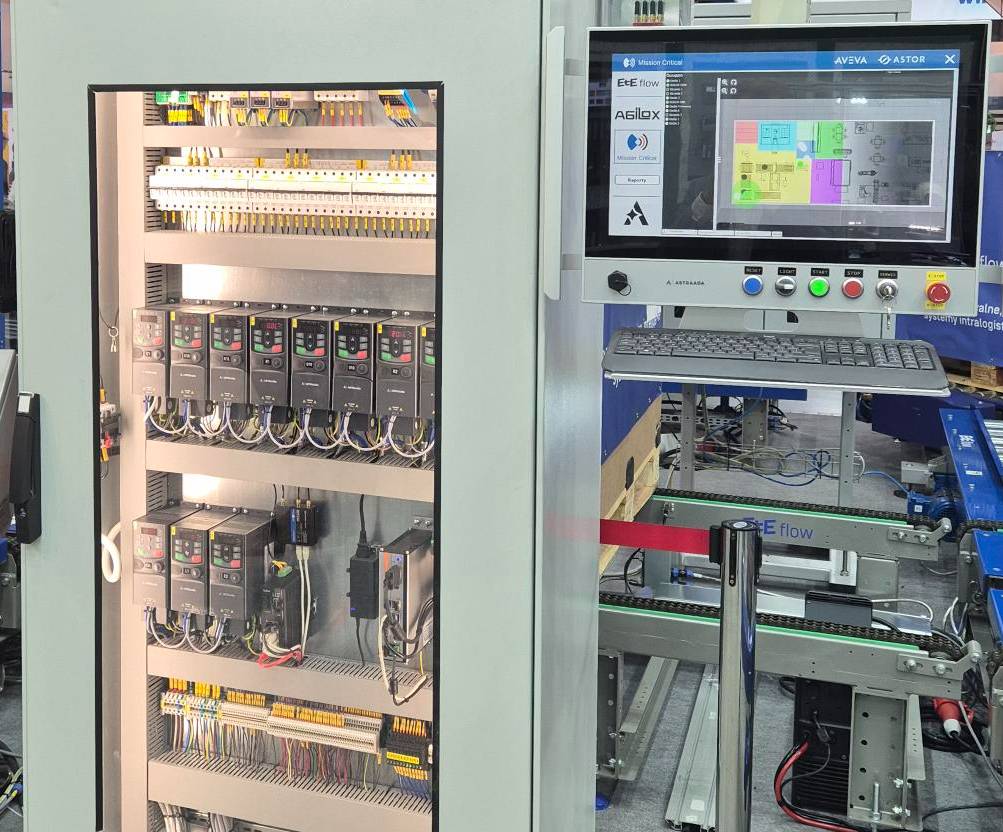
Oczywiście to nie wszystkie możliwe zastosowania komputerów przemysłowych. W kolejnych artykułach pokażemy, jak można wykorzystać komputery IPC w poszczególnych branżach przemysłu.
Zachęcamy do sprawdzenia oferty komputerów przemysłowych Astraada PC oraz oprogramowania przemysłowego AVEVA.