Sterowniki PLC i PAC – jak wybrać podstawowy element każdego systemu automatyki?
Kontakt w sprawie artykułu: Piotr Adamczyk - 2021-04-30
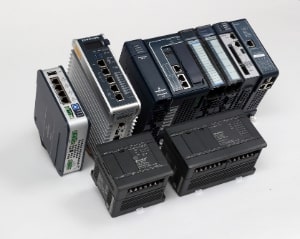
Z tego artykułu dowiesz się:
- czym są sterowniki PLC i skąd się wzięły,
- czym są systemy DCS i PAC,
- czym się różni sterownik PAC od sterownika PLC,
- w jakiej sytuacji wybrać sterownik PLC, a kiedy PAC
Kiedy mówimy o systemie sterowania, większość osób z branży automatyki od razu myśli o sterownikach programowalnych PLC. Nic dziwnego. PLC to nazwa, która znana jest na rynku od końca lat 60. ubiegłego wieku.
Sterownik PAC pojawił się później i choć pod pewnymi względami był podobny do sterownika PLC, wiele dzieliło te dwa rozwiązania. Jak dziś wygląda świat PLC, a jak PAC? Czy te urządzenia w dalszym ciągu różnią się od siebie tak, jak kiedyś? Przeczytaj artykuł i dowiedz się więcej o PLC i PAC.
W 1969 roku Modicon wprowadził do swojej oferty sterownik PLC (ang. Programmable Logic Controller). Te sterowniki zastąpiły wcześniej stosowane układy przekaźnikowo-stycznikowe. Podążając za potrzebami użytkowników tego typu systemów, dostawcy automatyki wprowadzili kolejne rozwiązanie. Sterownik PAC, (ang. Programmable Application Controller) pod względem funkcjonalności był podobny do sterownika PLC. Miał nowe, dodatkowe funkcje, więc jego przeznaczenie się zmieniło.
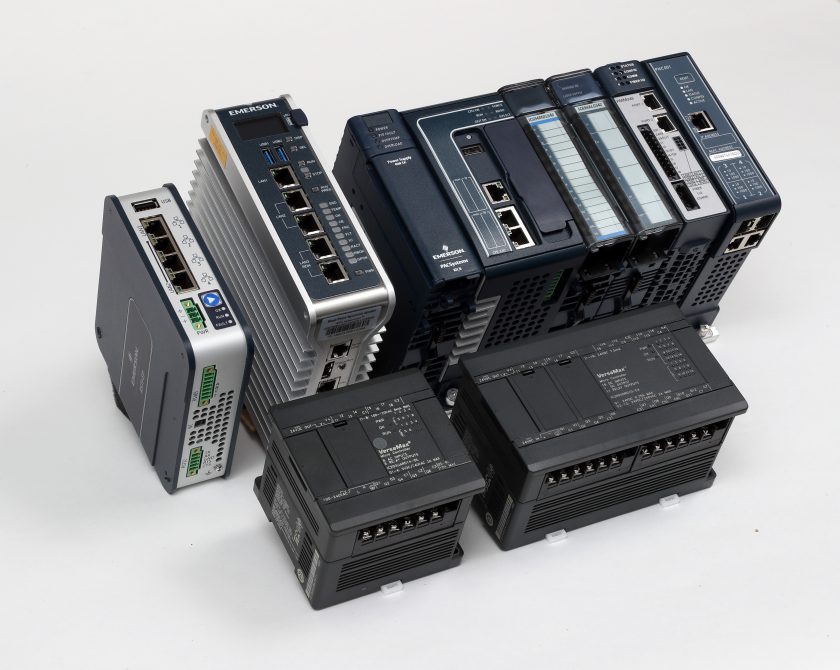
Skąd się wziął sterownik PLC?
Sterownik PLC powstał jako produkt, którego celem było inteligentne sterowanie układem automatyki. Wyeliminował tym samym stare, proste układy przekaźnikowo-stycznikowe. Układy przekaźnikowe były tylko szeregiem urządzeń, które w zależności od stanu pojawiającego się na wejściu sygnału, w odpowiedni sposób ustawiały wyjście.
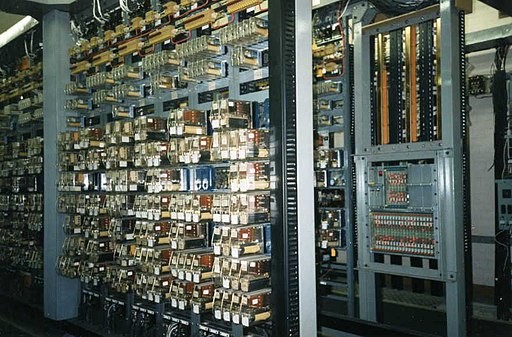
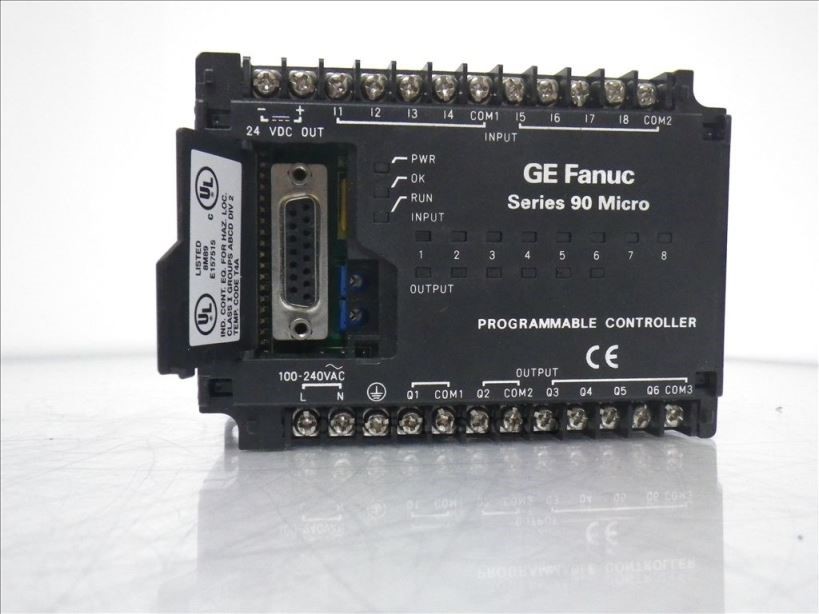
Układ taki, z założenia prosty, komplikował się wykładniczo przy rozbudowie systemu o kolejne przekaźniki. Pętle sprzężenia zwrotnego, elementy opóźniające załączenie wyjścia, blokady, zabezpieczenia urządzeń przed uszkodzeniem czy sygnalizacja stanów pracy poszczególnych urządzeń, to tylko niektóre z funkcji, jakie realizował układ przekaźnikowy. Wszystko działało mechanicznie i – jak to z mechaniką bywa – każdy element miał swoją żywotność. Pojawiały się więc awarie, które mogły unieruchamiać całe ciągi technologiczne. Dodatkowo układy takie zajmowały bardzo dużo miejsca w dedykowanych pomieszczeniach sterowniczych, przez co konieczne było bardzo dobre zaplanowanie architektury oraz przestrzeni montażowej.
Szukając rozwiązań tego problemu, podjęto próby projektowania nowych systemów. Ich funkcjonalność miała pozostać podobna, ale sterowanie byłoby opisane za pomocą algorytmu sterującego, a cały układ zostałby zamknięty w jednym urządzeniu z odpowiednią ilością wejść-wyjść. I tak powstał sterownik PLC – urządzenie, które w jednej obudowie zamyka funkcjonalność setek styczników i przekaźników oraz prostych funkcji sterujących, przeznaczonych do obsługi małych i średnich systemów automatyki.
Dużym wyzwaniem przy projektowaniu sterownika PLC okazała się jego podatność na zakłócenia, które zawsze występują w środowisku przemysłowym. Miało to ogromne znaczenie, gdyż sterownik PLC z założenia działał na niskich napięciach i, jak na tamte czasy, był naszpikowany elektroniką. Co więcej wykorzystywał do komunikacji magistrale komunikacyjne, a nie tradycyjne sterowania „po drutach”.
Kolejną bolączką sterownika PLC była temperatura pracy, która jak wiadomo w instalacjach przemysłowych podlega wahaniom w znacznych granicach.
Pierwsze urządzenia PLC zaczęły pojawiać się z początkiem lat 80. XX wieku, natomiast dopiero po około 10 latach i po rozwiązaniu szeregu problemów, zaczęły stawać się standardem w przemyśle.
Aktualnie aby sterownik PLC mógł poprawnie działać, musi być wyposażony w elementy takie jak:
- port komunikacyjny, służący do podłączenia do PC w celu wgrania programu,
- odpowiednia konfiguracja wejść oraz wyjść cyfrowych,
- jednostka centralna, która może wykonywać algorytm sterujący,
- pamięć, w której ten algorytm może być przechowywany.
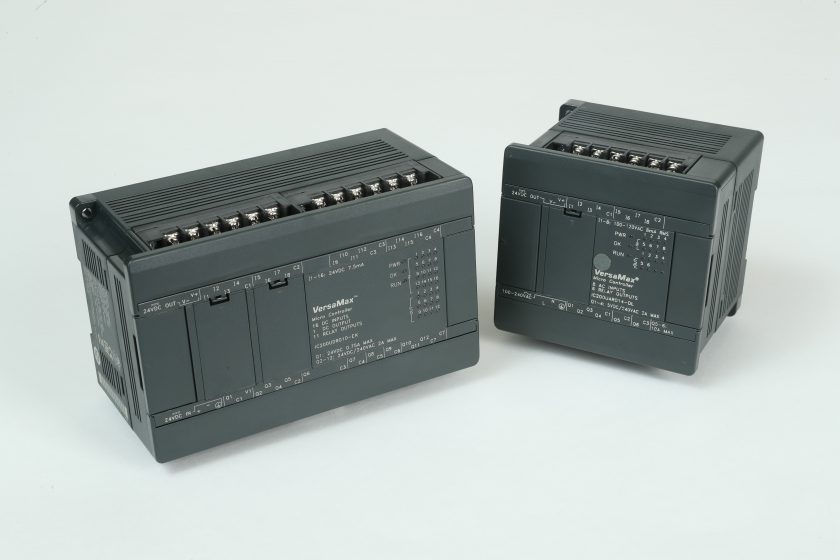
Sterownik PLC – przełom na rynku systemów automatyki
Sterownik PLC to był przełom na rynku. Budowa systemów automatyki stała się łatwiejsza, a ich konfiguracja, z uwagi na bardzo prostą składnię języka drabinkowego, dużo bardziej przejrzysta.
Proste w obsłudze oprogramowanie narzędziowe oraz wierne odwzorowanie układu przekaźnikowo-stycznikowego w programie logicznym, spowodowało, że struktura stała się przyjazna nie tylko dla automatyków, ale także dla elektryków, którzy byli kolejną grupą sięgającą coraz częściej po rozwiązania klasy PLC.
Dużą zaletą PLC jest to, że zmiana programu sterującego nie wymaga modyfikacji struktury sprzętowej sterownika. Nie ma też potrzeby zmiany sieci połączeń między urządzeniami, która w przypadku stycznikowo-przekaźnikowych układów sterowania pełniła funkcję programu.
Dla jakich systemów automatyki jest więc przeznaczony sterownik PLC? Jest to urządzenie dedykowane dla prostych systemów sterowania dyskretnego, którego język programowania opiera się o drabinkę, a funkcjonalność urządzenia zastępuje tradycyjne sterowanie dyskretne.
Taka definicja sterownika PLC funkcjonowała przez kolejne lata, dopóki oczekiwania użytkowników nie urosły do tego stopnia, że pojawiła się potrzeba wprowadzenia na rynek kolejnej rodziny urządzeń.
Kiedy sterownik PLC to za mało – systemy DCS i PAC
Równolegle do rozwoju systemów opartych o sterowniki PLC, prowadzono też prace nad nowym systemem, który odpowiadałby na potrzeby innej grupy docelowej – klientów realizujących na produkcji procesy ciągłe.
Specyficzne oczekiwania tej grupy użytkowników zdeterminowały powstanie kolejnego produktu, który różnił się w znaczący sposób od tradycyjnego sterownika PLC. Architektura i funkcje tego rozwiązania musiały być odmienne od poprzedniego: wymagały komunikacji z innymi urządzeniami automatyki, konieczne było sterowanie pętlami analogowymi, oczekiwano też innego sposobu programowania czy możliwości rozproszenia systemu na dużym obszarze. Zmieniony został również model sterowania.
W przeciwieństwie do typowo dyskretnego modelu sterowania, w którym cykl miał swój początek i koniec, w analogowym modelu sterowania wyglądało to zupełnie inaczej. Pomiary analogowe zmieniały się w odmienny sposób niż sygnał dyskretny, a pętla regulacji nie miała już wyraźnego początku ani końca, tylko była procesem ciągłym, w którym szybki cykl programu na poziomie kilkunastu milisekund, jak w przypadku sterownika PLC, nie miał znaczenia. W ten sposób zdefiniowano systemy klasy DCS (ang. Distributed Control System).
System taki, z uwagi na inne przeznaczenie, w znaczący sposób różnił się architekturą i budową od tradycyjnych sterowników PLC. Podczas, gdy w systemach PLC mówiliśmy wyłącznie o sterowaniu, w przypadku DCS mamy do czynienia z całkowitą kontrolą nad systemem i pełną integracją warstwy polowej, sterującej oraz operatorskiej.

W kolejnych latach na rynku automatyki funkcjonowały rozwiązania PLC, które były przeznaczone dla systemów dyskretnych oraz rozwiązania DCS dedykowane dla systemów ciągłych i analogowych. Jednak oczekiwania użytkowników rosły przez cały czas i wraz z coraz większą złożonością kompleksowych ciągów produkcyjnych, konieczne było łączenie cech obu rozwiązań, a tym samym stworzenie nowej klasy urządzeń.
Błędne jest założenie, że nowo powstałe rozwiązanie stanie się substytutem dla systemów PLC i systemów DCS. DCS w dalszym ciągu stosuje się w procesach ciągłych, a PLC jest systemem wykorzystywanym w aplikacjach dyskretnych. Nowe rozwiązanie miało zachować charakter sterownika PLC przy jednoczesnym doposażeniu go w funkcje znane z systemów DCS. Dzięki temu zakres jego stosowania mógł się znacząco zwiększyć. Nowe rozwiązanie zostało określone mianem PAC (ang. Programmable Application Controller). Choć ma kilka funkcji wspólnych z DCS, w dalszym ciągu bliżej mu do tradycyjnych sterowników PLC.
Sterownik PAC a sterownik PLC – czym się od siebie różnią?
Sterownik PAC to urządzenie, którego funkcjonalność jest bardzo podobna do działania tradycyjnych sterowników PLC. Jednak sterownik PAC daje nowe możliwości w zakresie sterowania oraz integracji z innymi urządzeniami automatyki.
Kontroler PAC, aby zachować dużą uniwersalność konfiguracji, swoją budowę opiera wyłącznie o architekturę modułową. Już sama konstrukcja urządzeń klasy PAC zdradza dodatkowe możliwości w zakresie obsługi systemów automatyki.
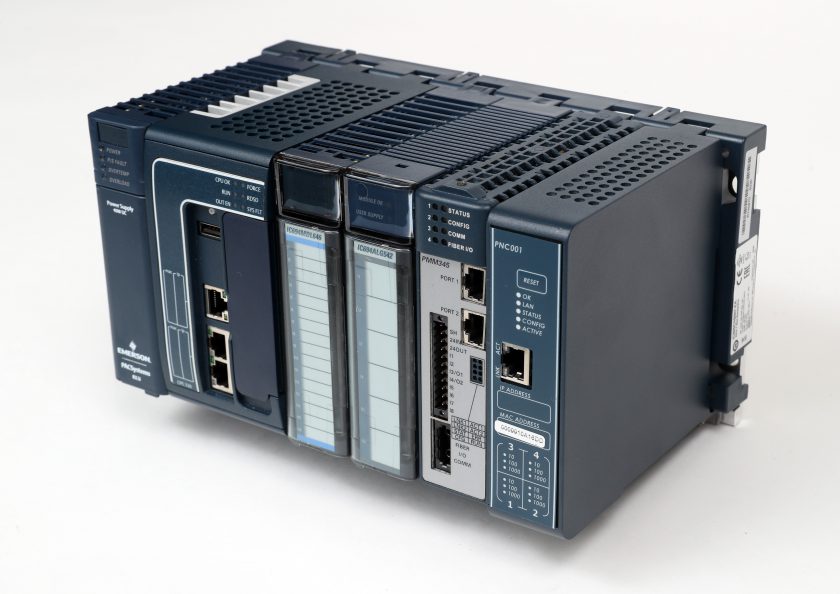
Możliwość elastycznego doboru karty rozszerzeń IO czy możliwość stosowania równolegle kilku modułów komunikacyjnych, to podstawowe różnice sterownika PAC w stosunku do sterownika PLC. Dzięki temu sterownik PAC jest świetnym rozwiązaniem, które pozwala w jednym urządzeniu zebrać dane z wielu innych układów automatyki i być koncentratorem danych dla systemów klas wyższych.
Kolejną różnicą jest sposób programowania. Kontrolery PAC, które pozwalają przygotować algorytm sterowania w kilku różnych językach programowania, dysponują znacznie większą ilością pamięci, pozwalającą budować algorytmy bardziej kompleksowe. W ramach programu sterującego jako wejścia możemy stosować zarówno sygnały dyskretne, jak i analogowe – podobnie jak na wyjściach kontrolera.
Znaczącą różnicą pomiędzy sterownikiem PAC a sterownikiem PLC jest wbudowana diagnostyka systemu oraz sposoby rozbudowy. Z uwagi na to, że sterownik PAC może być stosowany w systemach sterowania ciągłego, rozbudowa i serwis systemu możliwy jest na ruchu, bez wpływu na pozostałe elementy systemu. Rozbudowa – w zależności od obiektu, na jakim sterownik PAC będzie pracował – może mieć charakter lokalny lub rozproszony.
Na innym poziomie rozwiązane są również aspekty związane z bezpieczeństwem i niezawodnością całego układu. W sterowniku PAC redundancja na poziomie jednostek centralnych, zasilaczy czy modułów komunikacyjnych jest czymś naturalnym, podczas gdy w sterowniku PLC takie możliwości praktycznie nie występują.
Ostatnią, bardzo istotną różnicą pomiędzy sterownikami PLC i PAC jest wielowątkowość. Modułowa architektura PAC pozwala rozproszyć poszczególne funkcje pomiędzy różne moduły, zmniejszając tym samym obciążalność procesora głównego. Moduły komunikacyjne odpowiadają wyłącznie za wymianę danych z innymi układami, moduły motion są odpowiedzialne tylko za obsługę napędów, a moduły analogowe lokalnie dostosowują sygnał analogowy do wartości inżynierskich i dokonują odpowiednich przeliczeń. To gwarantuje, że kontroler główny ma wystarczająco dużo mocy obliczeniowej i zasobów do realizacji wymagającego algorytmu sterowania w czasie pojedynczych milisekund. W sterowniku PLC za te wszystkie funkcje odpowiada jeden procesor, co negatywnie wpływa na jego wydajność.
Ciągły rozwój sterowników PLC i PAC
Nieustanny rozwój elektroniki, a także ciągłe zwiększanie wydajności CPU i ilości pamięci powoduje, że granica pomiędzy sterownikami PLC i PAC powoli zaciera się, jednak w dalszym ciągu obserwujemy rozwój zarówno jednego, jak i drugiego rozwiązania.
W sterownikach PLC od dłuższego czasu obserwuje się przejmowanie funkcjonalności motion. Taki kierunek jest jak najbardziej słuszny. Charakteryzujące się szybkim czasem cyklu sterowniki PLC świetnie współpracują z systemami serwonapędowymi, w których precyzja i szybkość działania są na porządku dziennym.
Dzięki temu sterowniki PLC z powodzeniem można stosować w aplikacjach maszynowych, w których występuje konieczność precyzyjnej obsługi ruchu. Elementem uzupełniającym taką architekturę stają się proste systemy bezpieczeństwa maszynowego.
Zmiany nastąpiły także w obszarze komunikacji z innymi urządzeniami. Dodatkowe porty komunikacyjne pozwalają lepiej integrować się z pozostałymi elementami automatyki, które wykorzystywane są na poziomie maszyn i urządzeń. Nie sposób nie dostrzec także zmian na poziomie dostępnych języków programowania. Drabinka, pomimo tego, że nadal aktualna, w wielu przypadkach ustępuje miejsca językom strukturalnym i listom instrukcji.
Rozwój kontrolerów PAC idzie w inną stronę. Coraz częściej stosuje się technologie zwiększania dostępności zarówno na poziomie urządzeń sterujących, jak i magistral i modułów komunikacyjnych. Wkraczają nowe standardy związane z wymianą dużych ilości danych w systemach, które wykorzystują różne platformy sprzętowe i systemy operacyjne. Przykładem może być tutaj protokół komunikacyjny OPC-UA czy MQTT.
Kontrolery PAC – do dużych systemów sterowania
Z uwagi na przeznaczenie kontrolerów PAC oraz ich pracę w systemach rozproszonych, nie bez znaczenia pozostaje także kwestia bezpieczeństwa i niezawodności systemu. U kluczowych dostawców standardem są mechanizmy uniemożliwiające dostęp do kontrolera osobom niepowołanym, zabezpieczenia przed cyberatakami czy chociażby mechanizmy testujące wgrywanie wersji firmware lub systemu operacyjnego (wgranie możliwe jest tylko wtedy, gdy pliki z firmware i OS mają cyfrowy podpis nadawany wyłącznie przez producenta). Mechanizmy zabezpieczające są potwierdzone odpowiednim certyfikatem.
Wielkimi krokami wkracza także technologia wieloprocesorowa oraz wirtualizacja, która pozwala wydzielić na poziomie jednego kontrolera dwa urządzenia pracujące niezależnie, ale współdzielące ze sobą kluczowe zasoby. Mowa tu o kontrolerach PAC, obsługujących funkcje sterujące oraz komputerach przemysłowych IPC, uruchamiających narzędzia do optymalizacji i predykcji sterowanego procesu.
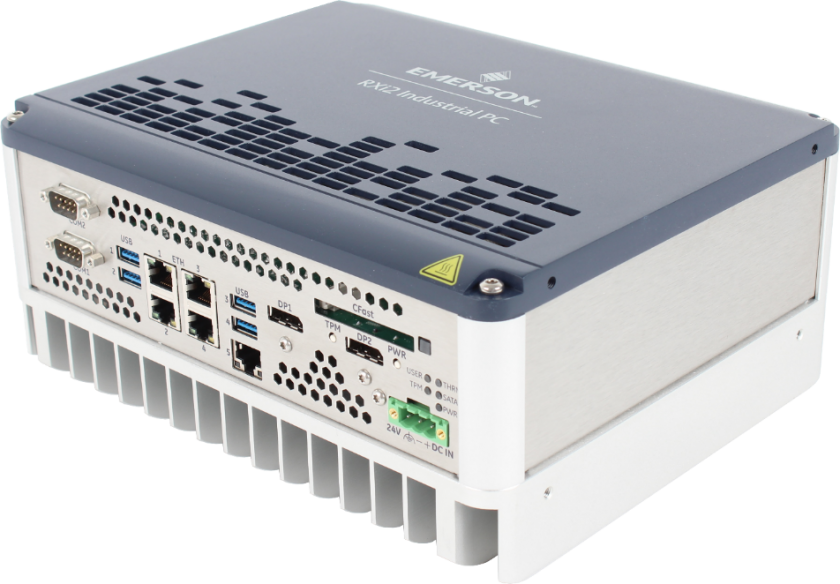
Komputer przemysłowy IPC na poziomie kontrolera PAC daje kolejne możliwości sterowania i wykorzystania technologii znanych wyłącznie ze świata IT. Uruchamianie algorytmów pisanych w językach wysokiego poziomu, takich jak Python, wykorzystywanie gotowych narzędzi dostarczanych w modelu open source, takich jak Grafana czy uruchamianie i obsługa na kontrolerze PAC systemów bazodanowych u niektórych dostawców jest już standardem.
Kiedy sterownik PLC, a kiedy sterownik PAC – jak wybrać?
Bardzo często zdarza się, że klienci mówią o stosowaniu sterowników PLC, nieświadomi tego, że w rzeczywistości korzystają z rozwiązań PAC.
Nie ma jasno określonej zasady, kiedy stosować jedno rozwiązanie, a kiedy drugie. Warto jednak zwrócić uwagę na kilka aspektów, które mogą nakierować nas na właściwą technologię. Pomocna może być tabelka, w której zestawiliśmy poszczególne cechy sterowników PLC i PAC:
Porównanie funkcjonalności sterownika PLC i kontrolera PAC
Kontroler PAC | Sterownik PLC | |
Praca w środowisku przemysłowym | ● | ● |
Sterowania dyskretne/sekwencyjne | ● | ● |
Sterowanie analogowe (ciągłe i wsadowe) | ● | ○ |
Współpraca ze SCADA i HMI | ● | ● |
Sterowanie napędami | ● | ● |
Rozproszenie funkcji zmniejszające obciążenie procesora głównego | ● | ○ |
Rozbudowa lokalna | ● | ● |
Rozbudowa oddalona | ● | ● |
Wielozadaniowość | ● | ○ |
Elastyczna/modułowa architektura | ● | ● |
Rozbudowane opcje komunikacyjne | ● | ○ |
Kompatybilność ze standardowymi protokołami i językami programowania | ● | ● |
Współpraca ze sprzętem różnych dostawców | ● | ○ |
Zintegrowane narzędzie programistyczne dla różnych aplikacji | ● | ○ |
Redundancja | ● | ○ |
Programowanie w językach wysokiego poziomu | ● | ○ |
Obsługa gotowych narzędzi open source | ● | ○ |
Rozbudowana diagnostyka | ● | ○ |
Szybkie wykonywanie pętli sterowania | ● | ● |
Cyberbezpieczeństwo | ● | ○ |
Sterowniki PLC i kontrolery PAC stanowią obecnie fundament każdego systemu sterowania. Dzisiaj już nikt nie jest w stanie wyobrazić sobie systemu automatyki, w którym nie ma dedykowanych układów, pełniących funkcje sterujące.
Bez względu na branżę i przeznaczenie, układ sterowania jest elementem kluczowym w każdej, nawet najprostszej, aplikacji przemysłowej. To dzięki niemu praca zarówno małych maszyn, jak i całych ciągów technologicznych może być realizowana w sposób automatyczny, powtarzalny oraz z zachowaniem najwyższej wydajności i jakości.
O ciągłej potrzebie stosowania sterowników PLC i kontrolerów PAC świadczyć może ogromne zapotrzebowanie na urządzenia tej klasy, sięgające setek tysięcy sztuk rocznie na całym świecie.
Jeśli chcesz dowiedzieć się, jak skonfigurować systemy oparte o proste sterowniki PLC i budować programy sterujące, zobacz kurs programowania sterowników PLC od podstaw, dedykowany dla automatyków i elektryków.
Jeśli chcesz zobaczyć, jak połączyć i skonfigurować prosty system w oparciu o kontrolery PAC, to sprawdź https://www.astor.com.pl/poradnikautomatyka/kurs-konfiguracji-sterownika-plc-w-proficy-machine-edition/