Sieci przemysłowe, które powinien znać każdy automatyk
Kontakt w sprawie artykułu: Mateusz Pytel - 2025-01-02
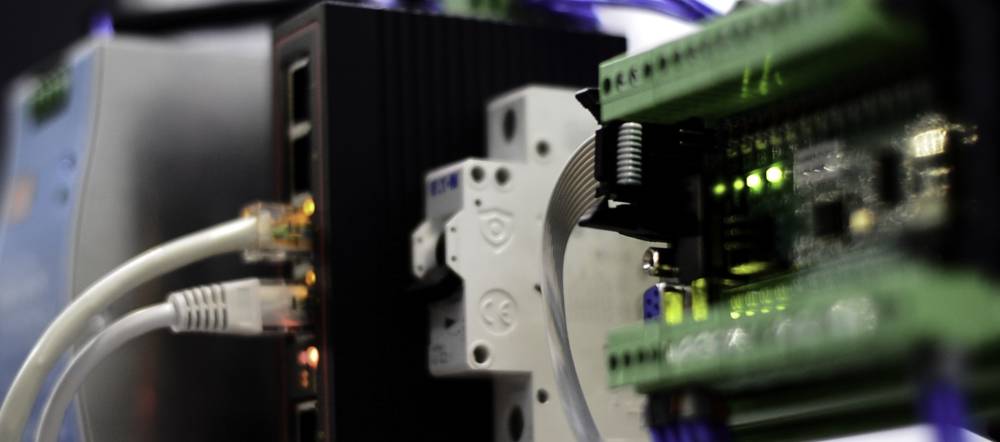
Dzisiejszy automatyk to człowiek orkiestra. Powinien nie tylko znać się na programowaniu sterowników PLC, projektowaniu systemów SCADA czy analizie danych, ale również na sieciach przemysłowych – krwiobiegu nowoczesnej automatyki. Wybór odpowiedniej sieci, jej konfiguracja i utrzymanie to klucz do efektywnego działania zakładów produkcyjnych. Jakie sieci przemysłowe są dziś najczęściej wykorzystywane w zakładach produkcyjnych i powinien znać je każdy automatyk?
Ethernet przemysłowy – klasyk, który dominuje na halach produkcyjnych
Ethernet przemysłowy, czyli odmiana klasycznego Ethernetu znanego z biur, to podstawa nowoczesnych zakładów. Jego największą zaletą jest elastyczność – umożliwia integrację urządzeń od czujników po systemy zarządzania produkcją. Dzięki niemu można szybko przesyłać dane między maszynami, a także integrować starsze i nowsze technologie w jednym systemie.
Jako przykład można sobie wyobrazić fabrykę produkującą wszelkiego rodzaju maszyny, w której architektura sterowania łączy sterowniki PLC, panele HMI oraz roboty – za pomocą jednej sieci Ethernet. Dzięki temu operator może np. w czasie rzeczywistym monitorować i optymalizować procesy. W przypadku nagłej zmiany projektu, np. innego kształtu części maszyny, możliwe jest natychmiastowe przesłanie nowych danych.
Omówmy krótko najbardziej popularne standardy Ethernetu przemysłowego.
Profinet: stosowany do szybkiej komunikacji między sterownikami PLC a urządzeniami wykonawczymi. Standard ten oferuje wsparcie dla funkcji czasu rzeczywistego i zaawansowanego monitorowania. Jest bardzo elastyczny, co pozwala na stosowanie go zarówno w małych maszynach, jak i w dużych liniach produkcyjnych. Jego funkcje diagnostyczne pomagają szybko wykrywać i usuwać problemy, minimalizując przestoje, przez co jest on często wybierany jako standard komunikacji w nowoczesnych zakładach.
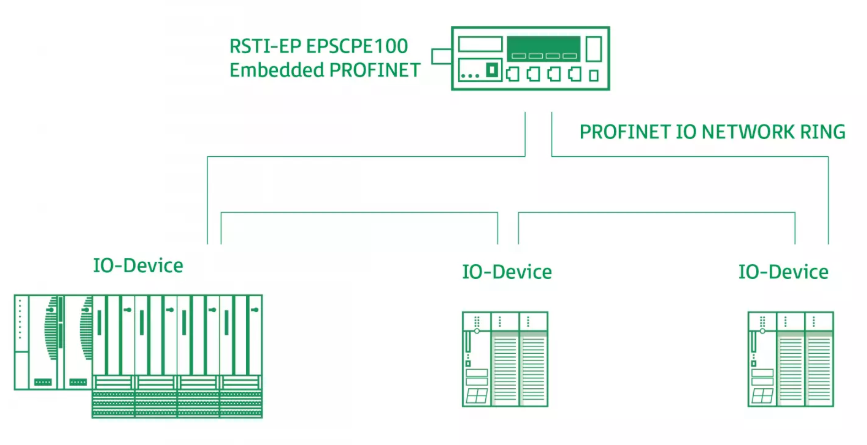
Więcej informacji na temat Profinetu znajdziesz w artykule Profinet – przemysłowy standard komunikacji
EtherCAT: najlepiej dopasowujący się do zadań wymagających synchronizacji, np. w maszynach CNC. Standard ten charakteryzuje się bardzo niskimi opóźnieniami i dużą przepustowością, co czyni go idealnym rozwiązaniem w aplikacjach wymagających precyzyjnej kontroli ruchu. Jako przykład możemy podać zastosowanie w wielkogabarytowej drukarce 3D do zadań konstrukcyjnych, gdzie dzięki wykorzystaniu struktury pierścieniowej uzyskaliśmy wysoką odporność na awarię oraz zapewniliśmy bardzo dużą szybkość i wydajność przesyłu danych dużych rozmiarów. Dodatkowo jego modułowa budowa pozwala na skalowanie architektury sterowania w zależności od potrzeby aplikacji. Kompatybilność EtherCAT z wieloma urządzeniami zdobyła uznanie w szerokim wachlarzu dedykowanych branż.
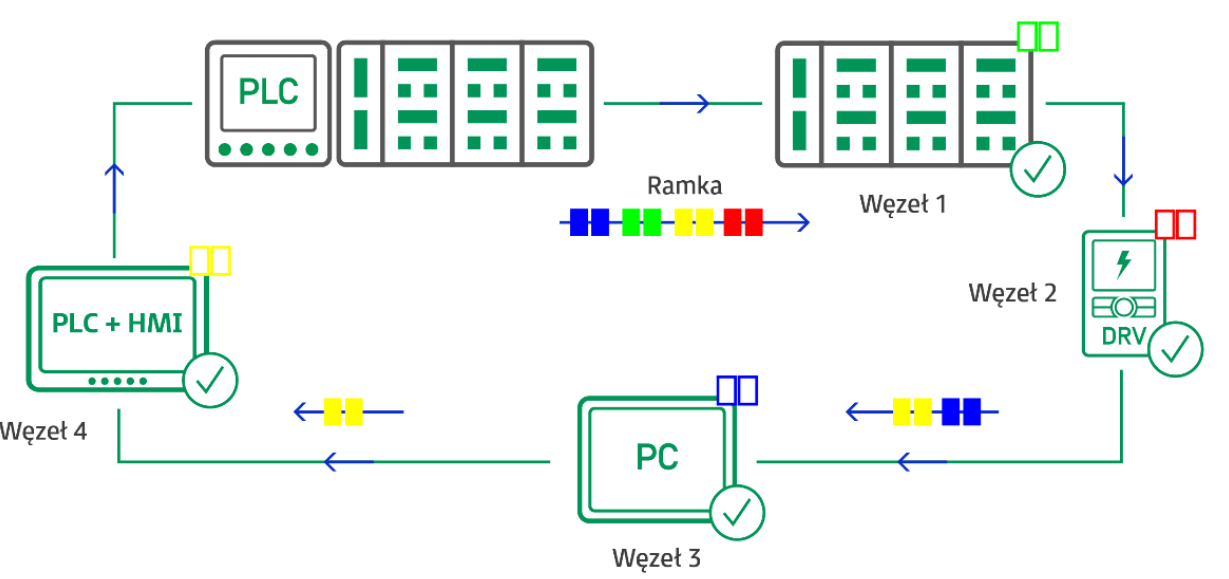
Więcej o EtherCAT dowiesz się z artykułu EtherCAT – czym jest i jak działa?
Modbus TCP: prosty w implementacji i najbardziej popularny w aplikacjach typu SCADA. Standard ten, jako rozszerzenie klasycznego Modbusa, oferuje możliwość łatwej integracji z nowoczesnymi systemami sieciowymi. Dzięki swojej prostocie stał się popularnym rozwiązaniem w mniejszych zakładach oraz tam, gdzie istotne są niskie koszty wdrożenia. Modbus TCP pozwala na efektywne przesyłanie danych w czasie rzeczywistym między systemami sterowania a urządzeniami wykonawczymi. Często wykorzystywany jest w systemach zarządzania energią, gdzie umożliwia monitorowanie zużycia oraz sterowanie urządzeniami.
Zachęcamy do zapoznania się z 14 odcinkiem naszego kursu programowania w środowisku Codesys.
Ethernet/IP: obsługuje wiele urządzeń jednocześnie, co czyni go idealnym rozwiązaniem dla dużych zakładów. Standard ten jest przeznaczony do przesyłania danych w czasie rzeczywistym, umożliwiając komunikację między sterownikami PLC, czujnikami, urządzeniami wykonawczymi oraz systemami nadrzędnymi. Kluczową cechą Ethernet/IP jest wykorzystanie modelu CIP (Common Industrial Protocol), który zapewnia jednolitą strukturę danych i funkcji, niezależnie od producenta urządzenia. Protokół wspiera zarówno komunikację cykliczną (I/O), jak i komunikację konieczną do np. przesyłania danych diagnostycznych. Dzięki zastosowaniu standardowych mechanizmów TCP/IP, jest on również łatwo integrowany z sieciami IT.
Zachęcamy do zapoznania się z kursem Ethernet/IP w robotach Kawasaki.
Sieci polowe – Fieldbus wciąż żywy
Choć mogłoby się wydawać, że Fieldbus to technologia minionej epoki, nadal ma swoje miejsce w świecie automatyki. Sieci te są niezawodne i świetnie sprawdzają się tam, gdzie potrzebna jest komunikacja o wysokiej niezawodności. Na przykład w zakładzie produkującym napoje gazowane linia rozlewnicza oparta na jednej z sieci polowych, zapewnia synchronizację pracy pomp, zaworów i czujników przepływu. Stabilność sieci umożliwia utrzymanie wysokiej jakości i minimalizację strat. Każda butelka jest napełniana z dokładnością co do mililitra, a system natychmiast reaguje na ewentualne awarie, zapewniając ciągłość produkcji.
Najczęściej stosowane standardy sieci polowych to:
- Profibus: lider w przemyśle, szczególnie w aplikacjach procesowych. Jego dwa główne warianty to Profibus DP, dedykowany do szybkiej wymiany danych w systemach automatyki, oraz Profibus PA, przeznaczony do aplikacji procesowych, w tym tych w strefach zagrożonych wybuchem, gdzie wymagana jest m.in. wysoka niezawodność.
- CAN/CANopen: to protokół komunikacyjny zaprojektowany pierwotnie dla przemysłu motoryzacyjnego, który później znalazł zastosowanie w automatyce przemysłowej. Jest ceniony za swoją odporność na zakłócenia i wysoką niezawodność. Rozwinięciem CAN jest standard CANopen, który ułatwia integrację w bardziej złożonych aplikacjach, umożliwiając efektywną komunikację w systemach sterowania maszynami czy robotami. Jednym z przykładów może być zastosowanie w przemyśle nowoczesnych technik drukarskich, czyli fleksografii.
- DeviceNet: to standard oparty na technologii CAN, używany głównie w przemyśle motoryzacyjnym oraz w maszynach przemysłowych. Umożliwia łatwą integrację urządzeń polowych, takich jak czujniki, siłowniki i sterowniki, eliminując potrzebę skomplikowanego okablowania. Wspiera również zasilanie urządzeń przez tę samą magistralę, co upraszcza instalację i redukuje koszty systemu.
OPC UA – uniwersalny tłumacz przemysłowy
OPC UA (Open Platform Communications Unified Architecture) to nie tylko standard komunikacji, ale prawdziwy ambasador między różnymi technologiami. Pozwala na wymianę danych między urządzeniami różnych producentów w sposób bezpieczny i niezależny od platformy. Jedną z kluczowych cech jest wysoki poziom bezpieczeństwa, obejmujący szyfrowanie, uwierzytelnianie użytkowników oraz integralność danych. OPC UA oferuje także możliwość zintegrowania systemów w chmurze, co ułatwia monitorowanie procesów w czasie rzeczywistym. Dzięki temu jest on podstawą dla Przemysłu 4.0 oraz IoT i umożliwia przez to bezproblemowe łączenie różnych technologii.
Więcej informacji na ten temat można znaleźć w artykule Przemysł 4.0: „Wybieram OPC UA dla mojego Internetu Rzeczy”
Bezprzewodowe sieci przemysłowe – przyszłość na wyciągnięcie ręki
W erze Przemysłu 4.0 rośnie również popularność sieci bezprzewodowych. Technologie takie jak Wi-Fi 6, Bluetooth Low Energy (BLE) czy Zigbee znajdują zastosowanie w monitorowaniu stanu maszyn, śledzeniu aktywów czy integracji z IoT. Wi-Fi 6 oferuje nie tylko większą szybkość, ale również stabilność w środowiskach o dużym zagęszczeniu urządzeń. BLE to z kolei idealne rozwiązanie do aplikacji o niskim zużyciu energii.
Podsumowanie
Dzisiejszy automatyk musi znać różnorodne sieci przemysłowe, bo każda z nich ma swoje charakterystyczne zastosowanie i zalety. Ethernet przemysłowy dominuje na hali, Fieldbus wciąż ma swoje wierne grono fanów, a technologie bezprzewodowe i OPC UA otwierają drzwi do przyszłości. Niezależnie od tego, które sieci wykorzystujesz, pamiętaj – kluczem do sukcesu jest nie tylko znajomość technologii, ale także kreatywność i oryginalność w jej zastosowaniu.