Robotowe porady techniczne: jak zrobić korektę trajektorii spawania zrobotyzowanego?
Kontakt w sprawie artykułu: Kamil Majcher - 2019-11-22
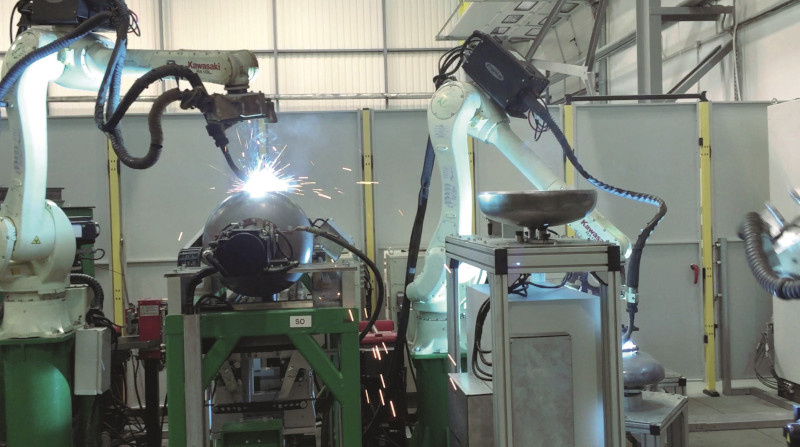
Z tego artykułu dowiesz się:
- Jakie są typy korekcji laserowej
- Z czego składa się system laserowy
- Jaka jest zasada działania RTPM
Programujesz roboty spawalnicze? Pracujesz z nimi na co dzień? Na pewno wiesz, że spawanie zrobotyzowane jest bardzo wymagającym procesem ze względu na pracę materiału, sposób przygotowania, prowadzenie palnika czy pozycję względem detalu, w którym operatorem jest robot, który bez systemów pomiarowych wykonuje powtarzalną pracę, realizując zadaną trajektorię ruchu.
Aby utrzymać wysoką jakość procesu, należy:
- przygotować materiał z wysoką dokładnością,
- zapewnić właściwe utrzymanie kąta palnika względem detalu,
- zamontować precyzyjny przyrząd, umożliwiający powtarzalny montaż elementów przed spawaniem, oraz zabezpieczający przed zmianą pozycji podczas spawania,
- poprawnie ustawić parametry spawania.
W przypadku małych gabarytów detali, powyższe punkty są proste do zrealizowania.
Typy korekcji laserowej
Podczas spawania detali wielkogabarytowych, zachodzi konieczność zastosowania systemu laserowej korekcji trajektorii:
- online (Seam Tracking) – niezbędne pomiary wykonywane są w trakcie trwania procesu; dzięki tej funkcjonalności robot spawalniczy jest w stanie skorygować pozycję w zależności od zmian kształtu ścieżki spawania; w przypadku robotów Kawasaki istnieje możliwość wyszukiwania punktu startowego oraz końcowego, według parametrów zdefiniowanych na robocie, m. in referencyjnego punktu startowego definiującego kierunek wyszukiwania, określenie odległości w jakiej należy rozpocząć wyszukiwanie punktu końcowego spawania,
- offline (Seam Finding) – pomiary wykonywane są przed rozpoczęciem spawania; zastosowanie tego typu rozwiązania pozwala na podstawie dojazdu do punktu referencyjnego, następnie wykonanie pomiaru określającego właściwe położenie punktu; przykładowo: wykonując odpowiednie obliczenia, robot jest w stanie określić linię prostą, według której powinien podążać lub wykryć początek i koniec złącza spawanego na podstawie zdefiniowanego profilu.
Opis systemu laserowego
Systemy składają się z czujnika laserowego montowanego na robocie oraz jednostki centralnej, przetwarzającej informacje otrzymywane z lasera. Każdy czujnik laserowy posiada zdefiniowane pole robocze, w którym wykonuje pomiar. Na podstawie pomiaru laserowego budowany jest w systemie kontur spoiny, na którym wbudowany algorytm systemu nanosi punkt, traktowany jako rowek spawalniczy.
Oprogramowanie takich systemów posiada możliwość wyboru parametrów rozpoznawanego profilu spoiny – doczołowa bez rowka, doczołowa z rowkiem, pachwinowa, zakładkowa, otworowa itp.
Każdy z zawartych wzorów można dodatkowo doprecyzować o szczegółowe parametry definiowane w zależności od wybranego profilu, np. o kąt rozwarcia spoiny pachwinowej, maksymalną szczelinę spoiny doczołowej, czy położenie punktu na wykrytym profilu. Dzięki tej funkcjonalności zyskasz możliwość zapewnienia powtarzalnej jakości spoiny.
Roboty Kawasaki mają wbudowaną obsługę protokołu komunikacyjnego dla systemów laserowych marki Scansonic oraz Servorobot. Komunikują się z jednostkami centralnymi poprzez protokół TCP/IP w standardzie Ethernet. W zależności od modelu wybranych producentów, można używać czujników zarówno w trybie offline oraz online.
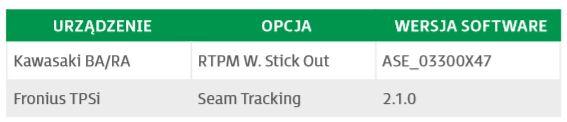
Automatyczna korekcja ścieżki spawania na podstawie wejścia Wire Stick Out
Inną formą automatycznej korekcji trajektorii spawania jest funkcjonalność RTPM (Real Time Path Modification). Roboty Kawasaki wspierają obsługę wartości Actual real value for seam tracking (Wire Stick Out), wysyłaną w protokole Ethernet IP jako zmienną ze źródeł Fronius. Aby zapewnić poprawne działanie funkcji, należy użyć ściegów zakosowych w procesie spawania – dzięki temu manipulator jest w stanie korygować się w kierunku poziomym oraz pionowym.
Opis działania RTPM
Aby funkcja działała prawidłowo, należy wykonać pomiar referencyjny, podczas którego zebrane zostaną wartości wejścia, na podstawie których zostanie wyznaczona wartość referencyjna.
W momencie wystąpienia zakłócenia, np. odchylenia palnika od linii wtopienia, czy zmiany szerokości rowka, następuje zmiana wolnego wylotu drutu. Źródło Fronius oblicza wartość wyjścia Wire Stick Out na podstawie zmian prądu i napięcia.
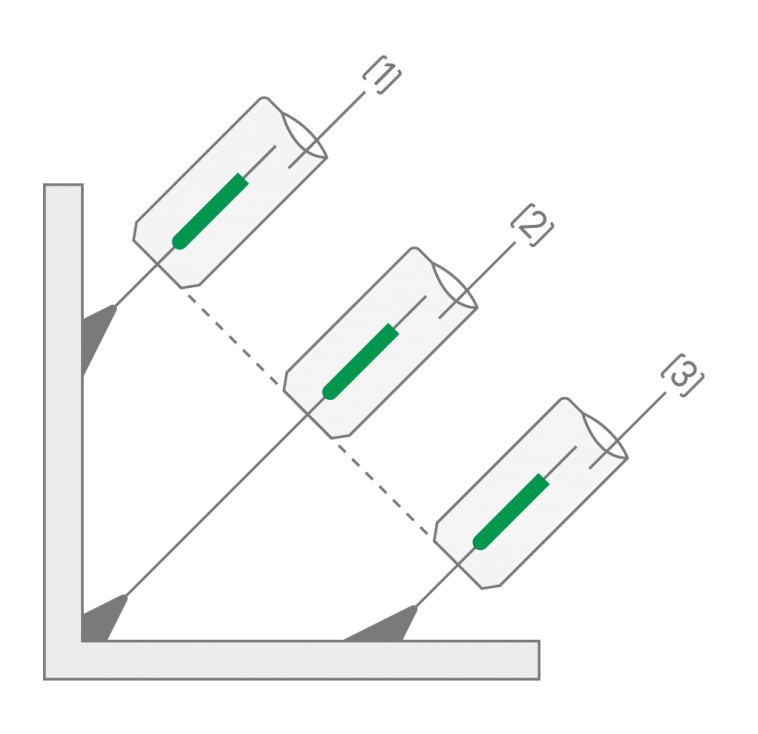
Rozważając spoinę pachwinową w punkcie (1) oraz (3), wartość wolnego wylotu elektrody wynosi 10 mm, prędkość spawania 7 m/min oraz przybliżona wartość wyjścia Wire Stick Out to 7650. W punkcie (2) wartość wolnego wylotu to 25 mm, prędkość spawania pozostaje stała, natomiast zmianie ulega wartość wyjścia Wire Stick Out – 5853. Robot Kawasaki otrzymuje parametr i porównuje go do odczytanej wartości referencyjnej.
Na podstawie różnicy wartości aktualnej i referencyjnej, robot wprowadza korektę do trajektorii spawania. Istnieje możliwość zdefiniowania dodatkowych parametrów, np. filtra odcinającego zakłócenia (z zadaną częstotliwością i w zakresie), czy rozdzielczości korekty na wejście Wire Stick Out.
Podsumowanie
Opisane opcje są coraz częściej stosowane w przemyśle. Zapewniają precyzję pracy oraz właściwą oczekiwaną jakość. Należy jednak pamiętać, że nie w każdym typie aplikacji sprawdzą się omówione rozwiązania, ze względu na ograniczenia mechaniczne, dostęp do rowka spawalniczego czy typ złącza. Każdy projekt należy rozpatrywać indywidualnie i dobierać rozwiązanie na miarę wskazanych potrzeb.