Podstawa systemów automatyki. Czym jest sterownik PLC?
Kontakt w sprawie artykułu: Piotr Adamczyk - 2022-09-19
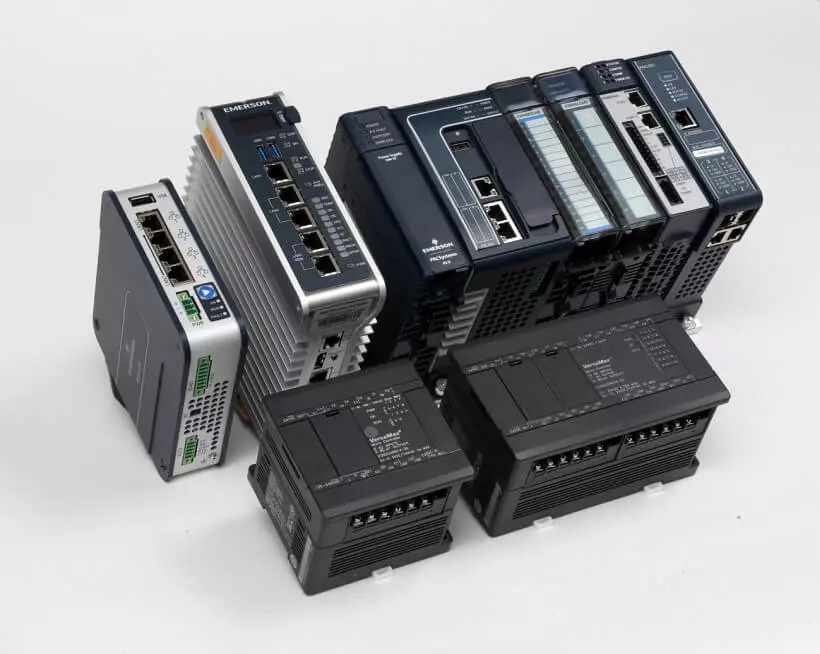
Z tego artykułu dowiesz się:
- czym jest sterownik PLC,
- jak jest zbudowany i jak go programować,
- jakie funkcje ma sterownik PLC i do czego można go wykorzystać.
Sterownik PLC jest jednym z najważniejszych urządzeń używanych w automatyce przemysłowej. Do jego powstania przyczyniła się ewolucja automatyki przemysłowej. Dzisiaj ciężko wyobrazić sobie zautomatyzowane procesy technologiczne bez sterowników PLC. Czym jednak właściwie one są i do czego służą? Co sprawia, że zastosowanie sterowników PLC w systemie automatyzacji jest korzystne, a często nawet nieodzowne? Na te pytania znajdziesz odpowiedź w poniższym artykule.
Czym jest sterownik PLC i do czego jest wykorzystywany?
Skrót PLC pochodzi od Programmable Logic Controller, czyli Programowalny Sterownik Logiczny. Jest to urządzenie wykorzystujące układ mikroprocesorowy, które służy do sterowania pracą maszyny lub innego urządzenia stosowanego w przemyśle. Używane może być do sterowania liniami produkcyjnymi, oświetleniem oraz innymi urządzeniami elektrycznymi.
Sterownik PLC został skonstruowany, aby zastąpić układy stycznikowo-przekaźnikowe. Pozwala on wyeliminować oraz uprościć skomplikowane okablowanie pomiędzy stycznikami i przełącznikami. Wszystkie działania realizowane przez układ sterowania, takie jak włączanie i wyłączanie urządzeń, zadawanie wartości parametrów, zliczanie czasu, a nawet obsługa receptur, są wykonywane wewnątrz sterowników. Dołącza się zwykle do nich odpowiednią liczbę układów wejściowych oraz wyjściowych. Układy wejść służą do zbierania informacji o stanie sterowanego obiektu, a układy wyjść – do połączeń z elementami sygnalizacyjnymi, wykonawczymi lub do transmisji danych.
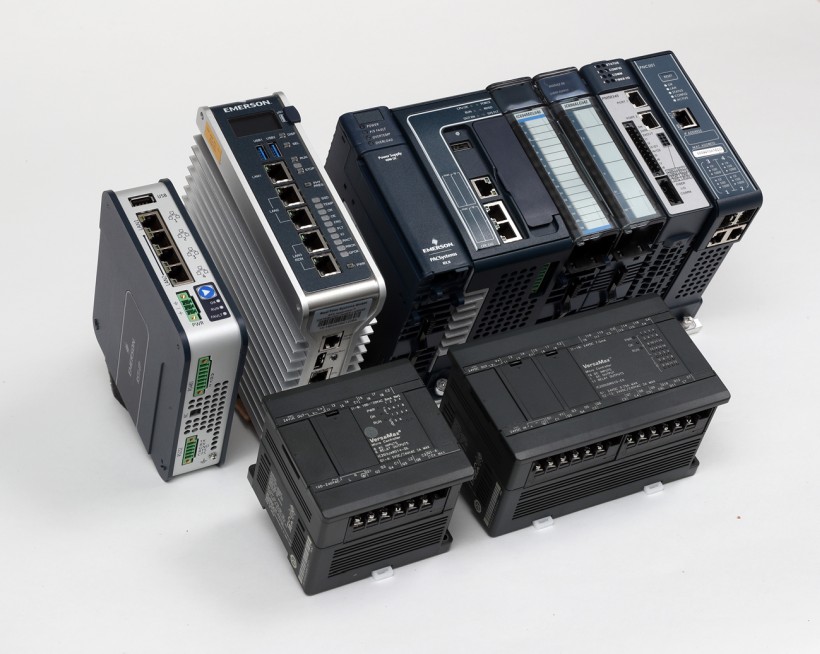
Sterowniki PLC są powszechnie używane w praktycznie każdej gałęzi przemysłu – ze względu na uniwersalność tego urządzenia. Sterownik ma też wiele innych zastosowań, nawet w życiu codziennym – na przykład do sterowania sygnalizatorami świetlnymi, ruchomymi schodami, windami czy rozmaitymi systemami, w jakie wyposażone są nowoczesne inteligentne domy.
Jak działa sterownik PLC?
Sterownik PLC pracuje w zamkniętej pętli programowej, czyli wykonuje program, który zawiera zapętlony ciąg rozkazów. Dzięki temu sterownik może reagować na dostarczane do niego informacje. Program sterownika składa się ze zmiennych oraz rozkazów, wśród których znajdują się operacje logiczne, arytmetyczne i wiele innych, a także polecenia związane z odczytem lub zapisem danych. Aby przygotować program, musisz to zrobić za pomocą komputera lub programatora. Gdy już to zrobisz, program jest przekształcany do postaci zrozumiałej dla układu mikroprocesorowego, przesyłany i zapisywany w pamięci sterownika.
Sterowniki otrzymują informację za pośrednictwem swoich wejść, które mogą być cyfrowe (zwane też dyskretnymi lub binarnymi) lub analogowe. Do wejść mogą być podłączone różnego typu czujniki np. zbliżeniowe. Z kolei sterowanie (wysyłanie sygnałów sterujących) odbywa się za pośrednictwem wyjść, które również mogą być binarne lub analogowe. Dodatkowo sterownik może wymieniać dane z otoczeniem za pomocą portów komunikacyjnych pracujących w rozmaitych standardach (szeregowych, Ethernet itp.) oraz różnych protokołach komunikacyjnych. W przypadku nowszych urządzeń praca sterownika może być kontrolowana z poziomu przeglądarki internetowej w komputerze bądź smartfonie.
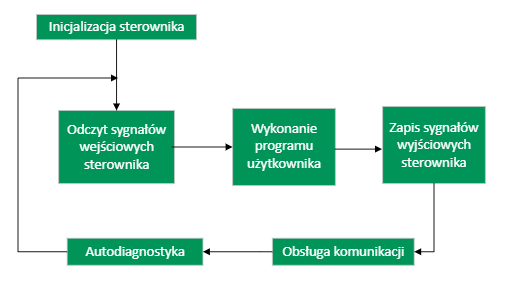
Powyższy schemat blokowy ilustruje podstawową zasadę działania sterownika PLC. Realizacja programu składa się z następujących etapów:
- Inicjalizacja sterownika – przy każdym uruchomieniu sterownika następuje sprawdzenie poprawności działania
- Odczyt sygnałów wejściowych sterownika – pętla programu w sterowniku analizuje sygnały wejściowe i kopiuje ich wartości do pamięci.
- Wykonanie programu użytkownika – sterownik przetwarza program, realizując kolejno wszystkie rozkazy, wykonując obliczenia i zapisując w pamięci stany sygnałów wyjściowych.
- Zapis sygnałów wejściowych sterownika – wszystkie zapisane w pamięci w trakcie przetwarzania programu stany wyjściowe są ustawiane w postaci odpowiednich sygnałów na wyjściach fizycznych sterownika.
- Obsługa komunikacji – obsługa portów komunikacyjnych, wysyłanie i odbiór informacji do innych urządzeń, jeżeli są połączone.
- Autodiagnostyka – sterownik zbiera informacje o błędach. W przypadku wykrycia błędu, sterownik przerywa działanie.
Jak programować sterownik PLC?
Do programowania sterownika PLC najczęściej wykorzystuje się komputer, na którym zainstalowane jest specjalistyczne środowisko programistyczne. Oczywiście dla każdej marki sterownika producenci oferują różne środowiska. Na przykład sterowniki Horner korzystają ze środowiska Cscape, Emerson – z PAC Machine Edition, a Astraada One – ze środowiska Codesys.
By połączyć komputer ze sterownikiem, używamy jego portów komunikacyjnych. Kiedyś najpopularniejsze były porty szeregowe RS232/485, obecnie najczęściej wykorzystuje się USB lub Ethernet. Dzięki temu połączeniu możliwa jest komunikacja między komputerem a sterownikiem – i przesyłanie informacji o programie czy konfiguracji.
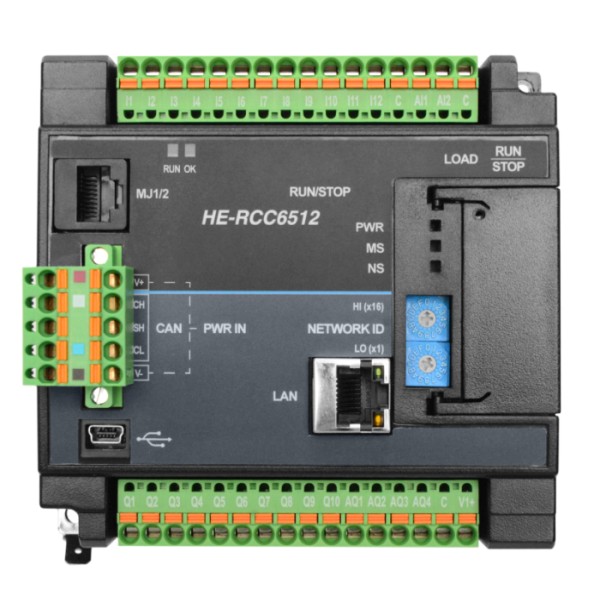
Gdy już połączysz swój sterownik z komputerem, możesz przejść do tworzenia programu w środowisku. Programowanie sterownika PLC odbywa się za pośrednictwem języków tekstowych lub graficznych. Najpopularniejsze języki programowania to:
- LD – Schemat drabinkowy (ang. Ladder Diagram), jeden z pierwszych języków, przypominający schemat elektryczny.
- ST – Tekst Strukturalny (ang. Structured Text), podobny do języka C, składający się w całości z poleceń tekstowych.
- FBD – Funkcjonalny Schemat Blokowy (ang. Functional Block Diagram), bazujący na odwzorowywaniu przepływu sygnału pomiędzy blokami funkcyjnymi, funkcjami oraz bramkami logicznymi.
- IL – Lista Instrukcji (ang. Instruction List), składający się z zestawu instrukcji, łatwych do zapamiętania i analizy.
- SFC – Sekwencyjny Schemat Funkcjonalny (ang. Sequential Function Chart), opisujący zadania w sposób graficzny, za pomocą kroków i warunków, które regulują przejścia między krokami.
O programowaniu sterowników PLC dowiesz się więcej z bezpłatnych kursów dostępnych na Poradniku Automatyka.
Z czego składa się sterownik PLC?
Sterowniki PLC składają się z:
- jednostki centralnej, czyli procesora (CPU),
- wejść cyfrowych,
- wejść analogowych,
- wyjść cyfrowych,
- wyjść analogowych,
- modułu zasilania,
- modułu komunikacji,
- modułów pamięci – stałej (ROM lub Flash, do przechowywania systemu operacyjnego) oraz ulotnej (RAM, do przechowywania danych i programu).
Moduły I/O w sterownikach PLC
Moduły I/O, czyli wejścia/wyjścia, są jednym z podstawowych elementów funkcjonalnych sterownika programowalnego. W uproszczeniu można powiedzieć, że moduły I/O działają jako przekaźniki pomiędzy procesorem sterownika a urządzeniami sterującymi procesem oraz pomiarowymi.
W sterowniku PLC funkcjonują moduły I/O, które mogą być analogowe i cyfrowe. Do wejść cyfrowych możemy podłączyć np. przyciski i przełączniki, a także np. krańcówki i inne czujniki generujące sygnał dyskretny (a więc 0 lub 1). Z kolei wyjścia cyfrowe obsługiwać mogą dowolne urządzenia wymagające do sterowania sygnału dyskretnego (typu włącz/wyłącz) – a więc np. grzałki czy pompy.
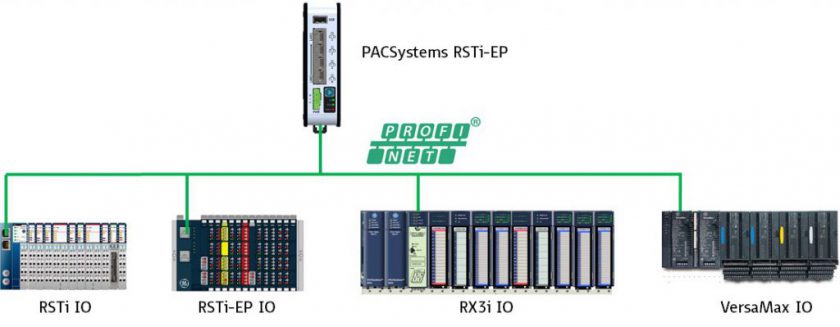
Natomiast wejścia i wyjścia analogowe obsługują urządzania generujące analogowy sygnał pomiarowy (takie jak np. wagi lub czujniki temperatury) lub wymagające takiego sygnału do sterowania nimi. Są one wyposażone w odpowiednie przetworniki analogowo-cyfrowe (w przypadku wejść) i cyfrowo-analogowe (w przypadku wyjść). Przetworniki wejściowe zamieniają analogowy sygnał prądowy (wartości prądu od 0 do 20 mA lub od 4 do 20 mA) lub napięciowy (wartości napięcia od 0 do 10 V lub od -10 do 10 V) na wartości cyfrowe zrozumiałe dla procesora sterownika (a więc liczby całkowite o rozdzielczości najczęściej od 12 do 16 bitów). Z kolei w przypadku przetworników wyjściowych dokonywane jest odwrotne przetworzenie – liczby na odpowiedni sygnał prądowy lub napięciowy.
Poza wejściami i wyjściami sterownik PLC wyposażony jest też w moduły komunikacyjne, które pozwalają połączyć sterownik z innymi urządzeniami (w tym z komputerem PC) albo włączyć go do większej sieci przemysłowej, w której mogą się znajdować inne sterowniki, czujniki, panele operatorskie itd. Za pomocą modułów komunikacyjnych do sterownika można również podłączyć oddalone moduły I/O, co pozwala zbierać sygnały oraz sterować urządzeniami na większą odległość.
Jakie są rodzaje sterowników PLC?
Wszystkie sterowniki PLC składają się z opisanych wyżej elementów, ale nie wszystkie wyglądają tak samo. Mogą one znacznie różnić się konstrukcją, która może być kompaktowa lub modułowa.
Sterowniki kompaktowe są najmniejszymi i najtańszymi urządzeniami. Ich obudowa jest zwykle niewielka, a ze względu na swoje wymiary posiadają one mniejszą liczbę wejść i wyjść. Większość tego rodzaju urządzeń da się – w pewnym stopniu – rozszerzyć za pomocą dołączanych modułów. Możliwość taka jest jednak zwykle ograniczona i – często – nieefektywna pod względem kosztów. Tracimy też w ten sposób największą zaletę tego rodzaju sterownika, czyli kompaktowość.
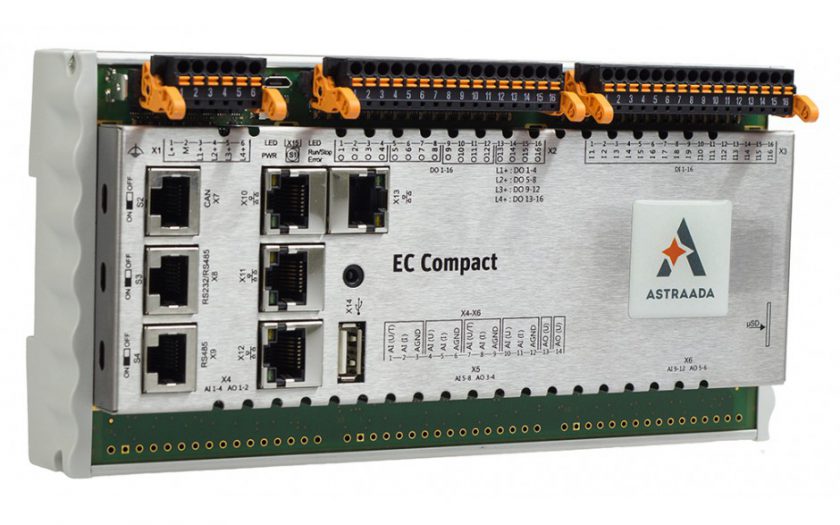
Z tych względów sterowniki kompaktowe znajdują swoje zastosowanie w sterowaniu prostymi instalacjami a także pojedynczymi urządzeniami i maszynami. Są często wykorzystywane przez producentów maszyn, którzy chętnie stosują szczególną odmianę sterownika kompaktowego, czyli sterownik zintegrowany z panelem operatorskim. Rozwiązanie takie pozwala połączyć w niewielkiej obudowie prosty układ sterowania z niewielkim (ale np. w przypadku pulpitu sterowniczego maszyny – całkowicie wystarczającym) panelem HMI.
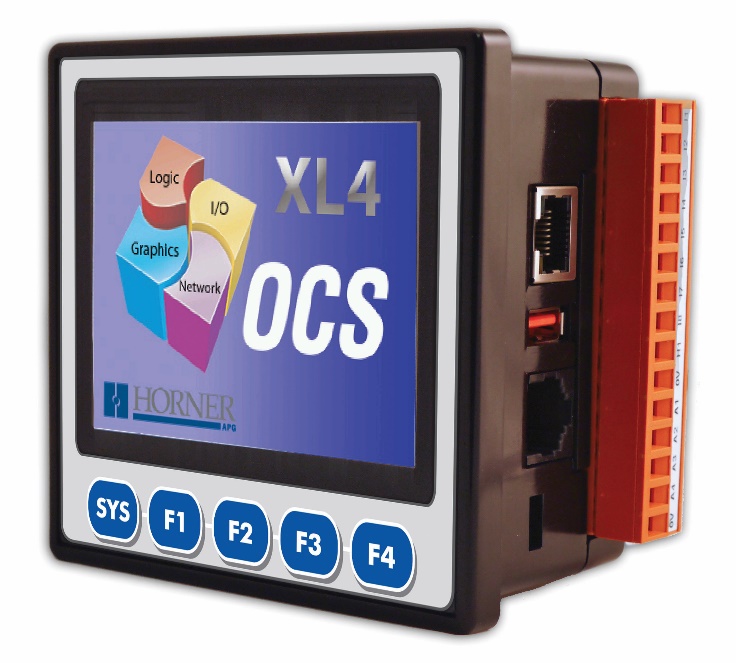
Sterowniki modułowe można swobodnie konfigurować w zależności od potrzeb, dodając nowe moduły. Modułowość jest największą zaletą tego typu sterownika. Oznacza to, że możesz dowolnie łączyć moduły, modyfikować je lub rozszerzać w zależności od Twoich wymagań. Przez rozszerzanie rozumiemy możliwość dołączenia modułu do sterownika, aby rozbudować jego funkcje oraz liczbę wejść i wyjść. Sterowniki modułowe mają też zwykle mocniejsze procesory (można je wybierać spośród kilku lub kilkunastu dostępnych), większą pamięć i właściwie nieograniczone możliwości komunikacyjne. Dlatego są one używane do sterowania dużymi instalacjami i złożonymi procesami produkcyjnymi.
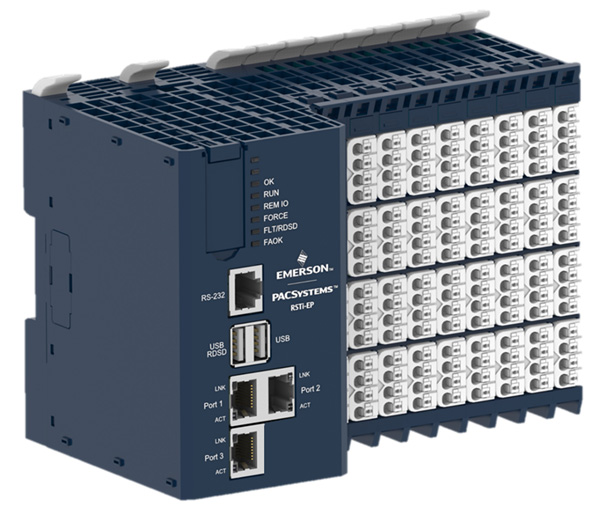
Wśród modułów, które możemy zastosować w typowych sterownikach modułowych, znajdziemy między innymi:
- moduł pozycjonowania osi (APM),
- moduł szybkich liczników (HSC),
- moduł wejściowy dla czujników temperatury,
- moduł do pomiaru energii,
- moduł regulatora PID,
- liczne moduły komunikacyjne dla różnych sieci przemysłowych i protokołów komunikacyjnych
i wiele innych.
Kontrolery PAC
Kontrolery PAC są doskonałym wyborem w sytuacji, gdy potrzebujemy w aplikacji sterującej przetwarzać duże ilości danych. Stanowią one, mówiąc w pewnym uproszczeniu, połączenie zwykłych sterowników przemysłowych PLC i komputerów przemysłowych. Skrót PAC pochodzi od Programmable Application Controller, czyli Programowalny Kontroler Aplikacji. Są to konstrukcje modułowe, oferujące bardzo bogate możliwości rozbudowy i dostosowania do potrzeb konkretnej aplikacji. Wyposażone są także w wydajne procesory, dużą pamięć operacyjną oraz możliwość instalacji kart PCI i PCIexpress.
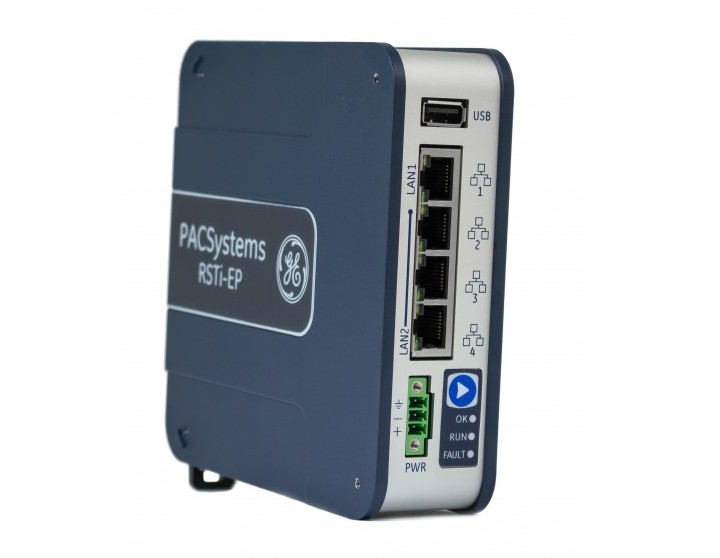
Dlaczego warto stosować sterowniki PLC w przemyśle?
Jak wspomniałem, sterowniki PLC są urządzeniami uniwersalnymi, które mogą doskonale sprawdzić się w wielu zastosowaniach. Charakteryzuje je duża wydajność, dlatego mogą być stosowane nawet w bardzo wymagających aplikacjach.
Jedną z największych zalet sterownika PLC względem układów stycznikowo-przekaźnikowych jest możliwość modyfikacji programu sterowania bez zmian sprzętowych – np. w zakresie okablowania. Prowadzi to do znaczącego skrócenia czasu związanego ze zmianą sterowania danej instalacji. Oznacza to zmniejszenie kosztów poprzez eliminację w danej instalacji przekaźników czasowych oraz styczników pomocniczych. Poza tym sterowniki PLC charakteryzują się niskim zużyciem energii oraz bardzo wysoką niezawodnością w porównaniu do układów stycznikowo-przekaźnikowych.
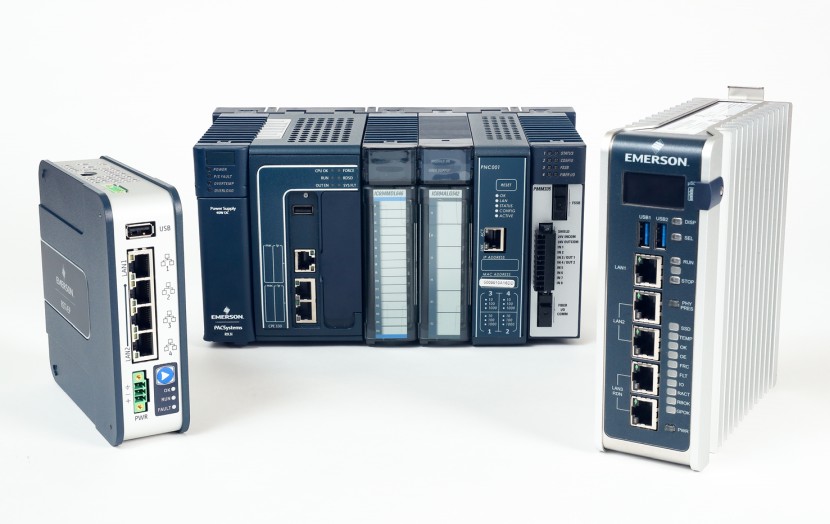
Realizacja wszystkich funkcji sterowania, np. zliczania czasu, jest realizowana wewnątrz sterownika. Zmniejsza to koszty, ponieważ przy takim rozwiązaniu nie musisz używać przekaźników czasowych czy styczników pomocniczych. Program sterownika można kopiować i używać wielokrotnie, a także dodawać w nim komentarze, aby inny użytkownik mógł łatwiej zrozumieć zasadę działania programu.
Mała ilość prac montażowych oraz mniejsze koszty okablowania i materiału pozwalają na realizację projektów w krótszym czasie. Gdy stosujesz nowoczesne sterowniki, wyposażone w możliwość podłączenia do Internetu, możesz zarządzać aplikacją i serwisować ją z dowolnego miejsca na świecie.
Można jednak postawić pytanie: czy istnieje jakaś alternatywa dla sterowników PLC? Owszem, w pewnych sytuacjach można zastąpić je komputerami przemysłowymi, realizującymi funkcję sterowania logicznego (tzw. SoftPLC). Może zapewnić to większą wydajność oraz moc obliczeniową, a także większą funkcjonalność i bardziej rozbudowane możliwości komunikacyjne.
Jednakże komputer przemysłowy nigdy nie będzie działał dokładnie tak samo, jak sterownik. Po pierwsze, ze względu na wykorzystanie standardowego sytemu operacyjnego rozwiązania SoftPLC wciąż nie są deterministyczne, w odróżnieniu od sterowników PLC. Zastosowanie komputera w roli sterownika stawia też zupełnie nowe wyzwania w zakresie zapewnienia bezpieczeństwa aplikacji.
Autor artykułu: Mateusz Steczkowski
Więcej na ten temat możesz przeczytać w artykule Komputer przemysłowy jako PLC – czy to możliwe?.