Kurs projektanta systemów HMI/SCADA cz.6 – Jak przeprowadzić testy, kontrolę i utrzymanie nowej wizualizacji HMI/SCADA?
Kontakt w sprawie artykułu: Wojciech Pawełczyk - 2019-08-02
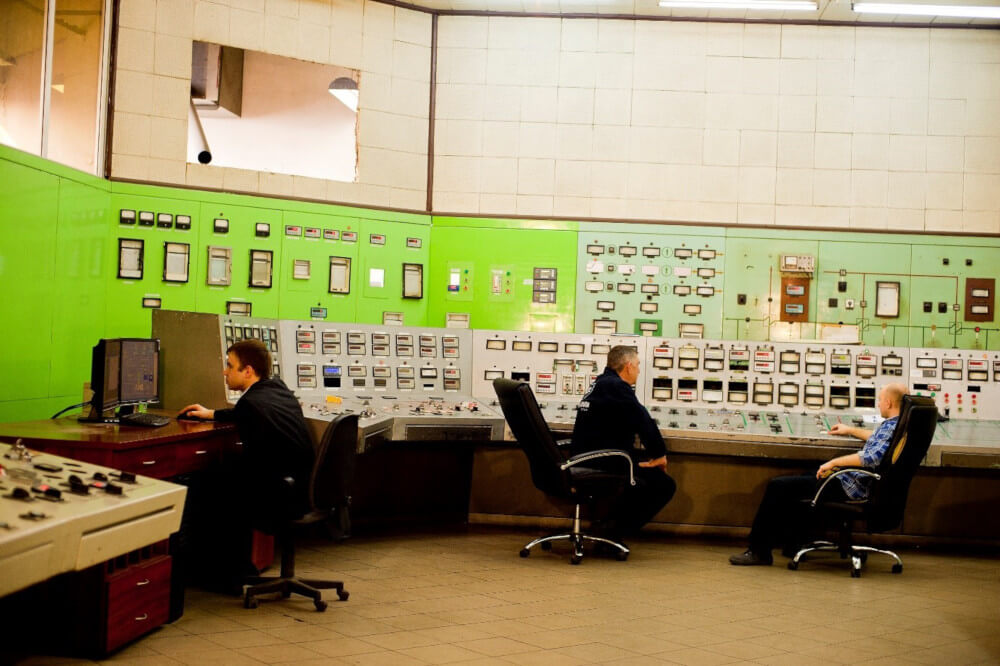
Z tego artykułu dowiesz się:
- Dlaczego należy prowadzić regularny przegląd działania wizualizacji?
- Dobór ekranów i koniecznego sprzętu – na co zwrócić uwagę?
- Control room – jak zweryfikować komfort pracy operatora?
W piątym odcinku „Kursu projektanta systemów HMI/SCADA cz.5 – Jak zacząć projektowanie i tworzenie wydajnej wizualizacji zgodnie z dobrymi praktykami – hierarchia projektowania” pokazaliśmy, na czym polega hierarchiczne podejście do projektowania ekranów wizualizacji, jakie elementy umieszczać na poszczególnych ekranach wizualizacji oraz ich funkcjonalności. Celem takiego podejścia jest oczywiście uzyskanie maksymalnie wydajnej wizualizacji.
W tym odcinku kursu skupimy się na kilku aspektach wdrożenia wizualizacji, a więc na pomieszczeniu control room, a szczególnie na jego części sprzętowej, czyli komputerach przemysłowych i panelach operatorskich.
Ten odcinek pokaże Ci, o czym jeszcze powinnaś/powinieneś wiedzieć jako projektant/ka – oprócz zasad projektowania wizualizacji. Zazwyczaj zadanie wdrożenia wizualizacji nie należy do projektanta, ale warto znać ten proces, bo często konieczne jest wprowadzanie zmian i poprawek wizualizacji po jej weryfikacji w trakcie wdrożenia.
Ten artykuł jest częścią cyklu „Kurs projektanta systemów HMI/SCADA”
„Kurs projektanta systemów HMI/SCADA” przeznaczony jest zarówno dla początkujących w projektowaniu SCADA, jak również dla tych, którzy chcą poszerzyć swoją wiedzę w zakresie nowych technik projektowania.
Kurs składa się z 7 części, w których zostaną przedstawione i opisane nowoczesne techniki projektowania systemów HMI/SCADA. Każdy uczestnik kursu ma możliwość przećwiczenia w zadaniach kolejnych elementów projektowania wizualizacji.
Jeśli przeczytasz wszystkie artykuły, będziesz świetnie przygotowany/a do końcowego quizu, po którym otrzymasz certyfikat ukończenia.
„Kurs projektowania systemów HMI/SCADA” obejmuje następujące artykuły w formie poradników:
1. Jak efektywnie projektować wizualizacje?
2. Tradycyjne i nowoczesne praktyki tworzenia wizualizacji HMI/SCADA.
3. Jak dopasować specyfikę wizualizacji HMI/SCADA do celu procesu i oceny wydajności procesu?
4. Jak przedstawiać elementy dynamiczne oraz alarmy na wizualizacjach HMI/SCADA?
5. Jak zacząć projektowanie i tworzenie wydajnej wizualizacji zgodnie z dobrymi praktykami?
6. Jak przeprowadzić testy, kontrolę i utrzymanie nowej wizualizacji HMI/SCADA?
7. Jak dbać o rozwój i przyszłość systemów HMI/SCADA w przedsiębiorstwach?
Praca projektanta systemów HMI/SCADA nie kończy się na samej znajomości technik projektowania wizualizacji. Dla każdego projektanta systemów SCADA ważna jest świadomość, że wygląd i grafika wizualizacji nie jest jedynym wyróżnikiem jej wydajności – wizualizacja, którą zaprojektuje projektant, ma działać niezawodnie i spełniać wszystkie kryteria niezbędne do efektywnego zarządzania i monitorowania produkcji.
Krok 1. Zaplanuj i przeprowadź testy z operatorami przed wdrożeniem wizualizacji
Testy wizualizacji pozwolą sprawdzić, czy wizualizacja spełnia wszystkie kryteria, wymogi, założenia i oczekiwania. Do testów zaangażuj operatorów, którzy będą pracowali na zaprojektowanej przez Ciebie wizualizacji. Pamiętaj, że wizualizacja HMI/SCADA powinna być czytelna i zrozumiała dla wszystkich operatorów.
Bez wcześniejszego sprawdzenia wizualizacji nie możesz przystąpić do jej wdrożenia – celem takiego podejścia jest upewnienie się, że wszystko działa poprawnie i że nowa wizualizacja jest bardziej funkcjonalna i daje lepszy komfort pracy dla operatora niż poprzednia.
Operator powinien wykonać testy wizualizacji przygotowanej przez projektanta systemów HMI/SCADA w zakresie:
- zastosowania obowiązujących procedur dotyczących monitorowania i zarządzania,
- aspektów dotyczących efektywnego korzystania z wizualizacji HMI/SCADA dopasowanego do danej operacji i zadania (czy operator może intuicyjnie, bez problemów wykonywać swoje zadania)
- powodów, dla których wizualizacja HMI została zmieniona oraz tego, czy błędy zostały poprawione, a oczekiwane korzyści osiągnięte,
- weryfikacji, czy grafiki spełniają odpowiednie zadania oraz reprezentacji alarmów i zarządzania nimi; w tym punkcie operator powinien sprawdzić, czy wszystkie elementy wizualizacji są dla niego jasne i czy w czasie normalnego zarządzania procesem oraz w sytuacjach alarmowych jest w stanie bez problemu zinterpretować wszystkie elementy,
- sprawnej nawigacji pomiędzy ekranami wizualizacji HMI/SCADA,
- odpowiedniego wykorzystania wykresów – czy na wykresach zostały przedstawione wszystkie wskaźniki kluczowe dla operatora i procesu,
- zastosowania hierarchii w wizualizacji – czy wszystkie najważniejsze informacje są widoczne na głównym ekranie, a dotarcie do szczegółowych informacji jest intuicyjne,
- weryfikacji działania elementów graficznych przeznaczonych do kluczowych zmian w procesie, takich jak zmiana wytwarzanego produktu, przejście do innej zmiany lub zatrzymania – czy operator jest w stanie z łatwością dokonać kluczowej zmiany w procesie,
- porównania poprzednich grafik z nowymi grafikami – czy nowa wizualizacja rozwiązuje problemy, które pojawiały się w poprzedniej wizualizacji oraz czy nowo wprowadzone grafiki są wprowadzone w taki sposób, że nie generują dodatkowych problemów?
Operator powinien przeglądnąć całą wizualizację, przekazać Tobie jako projektantowi opinię zwrotną i zaplanować ciągłe doskonalenie wizualizacji w czasie jej działania.
Wskazówka: W trakcie testów najlepszym rozwiązaniem jest wyłączenie z aktywnego działania starej grafiki. Nie jest dobrze, aby obydwie wersje pracowały równocześnie, ponieważ elementy starej wizualizacji mogą wpływać na działanie nowej i powodować błędy. Poprzednia, stara wersja wizualizacji powinna zostać zapisana i przechowywana jako backup na wypadek, gdyby zdarzyła się nieprzewidziana sytuacja i byłby potrzebny powrót do starej wizualizacji.
Krok 2 – Rób zmiany w wizualizacji po przetestowaniu jej działania w rzeczywistych warunkach
Po testach i pierwszych poprawkach wdrażasz wizualizację do aktywnego użycia w warunkach rzeczywistych, gdzie przechodzi przez kolejny (najważniejszy 🙂 ) test sprawdzający jej efektywność.
Po kilku tygodniach użycia nowej wizualizacji HMI/SCADA w warunkach rzeczywistych jest duże prawdopodobieństwo, że operatorzy napotkali już na błędy w zaprojektowanej wizualizacji lub zauważyli elementy, które można poprawić – tak, żeby ich praca była bardziej wydajna. Po takim czasie warto zapytać operatorów o zmiany w wizualizacji, które według nich należy koniecznie przeprowadzić.
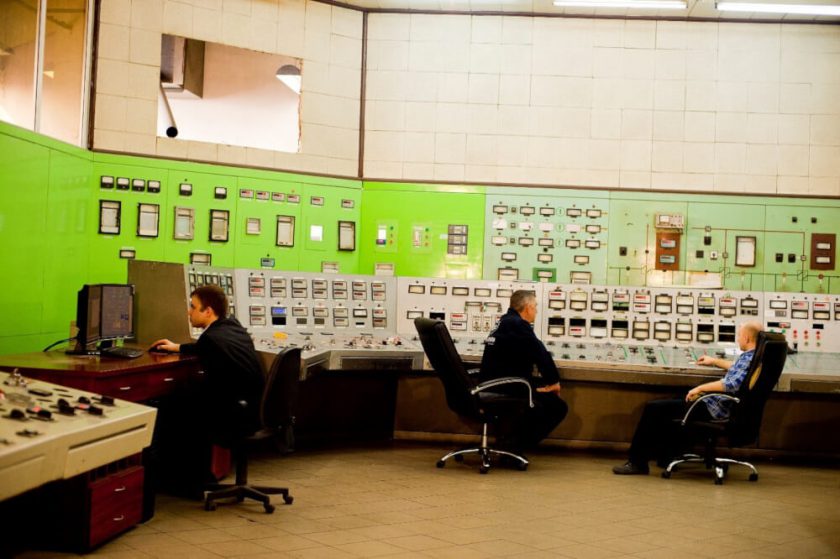
Utrzymuj ciągły kontakt z operatorami, by być na bieżąco z informacjami zwrotnymi, czy nowa grafika wzmacnia efektywność działania i jaką ma skuteczność. Dobrze jest poprosić o zrzut ekranu (tzw. print screen) wraz z notatkami dotyczącymi sugerowanych zmian i ulepszeń.
W większości zakładów produkcyjnych sytuacje alarmowe, wypadki i błędy są gromadzone w wewnętrznych raportach. Część z tych raportów może być przydatna również dla projektanta – wgląd w raporty umożliwi Ci dostęp do wiedzy na temat błędów wynikających z wizualizacji.
Wskazówka: Aby uzyskać jak najbardziej efektywną wizualizację, utrzymuj stały kontakt z operatorami, aby przesyłali komentarze dotyczące błędów wizualizacji.
Krok 3 – Jak dobrać sprzęt do efektywnej wizualizacji?
Do właściwego działania control room’u, oprócz zaprojektowania wizualizacji potrzebny jest odpowiedni sprzęt konieczny do monitorowania i zarządzania procesem. Dobór sprzętu nie należy do projektanta, ale jest bardzo ważny w kontekście systemów HMI/SCADA wykorzystywanych w przemyśle.
Które urządzenia będą potrzebne operatorowi? Lepiej wybrać komputer przemysłowy, czy panel HMI? Jaki sprzęt powinien się znaleźć w centralnej dyspozytorni? Aby odpowiedzieć sobie na te pytania, trzeba mieć świadomość tego, do jakiego zastosowania ten sprzęt zostanie wykorzystany – liczy się nie tylko to, co zostanie uruchomione na urządzeniu, ale też to, w jakich warunkach będzie pracować.
Dobierając panele operatorskie dla małych aplikacji i komputery przemysłowe dla systemów SCADA, warto mieć na uwadze, że takie urządzenia powinny mieć wysoką moc obliczeniową i podzespoły, które pozwolą na wieloletnią, bezawaryjną pracę. Dlaczego Ty – jako projektant/projektantka systemów HMI/SCADA powinieneś przeczytać tę część kursu?
Na tym etapie część graficzna zostaje przeniesiona na rzeczywiste ekrany do control room’u. To, na jakich ekranach zostanie wdrożona, ma wpływ na jej efektywne wykorzystanie.
1.Komputery przemysłowe do systemów SCADA oraz panele operatorskie dla mniejszych zastosowań
Wydaje się, że im większa liczba ekranów w centralnej dyspozytorni, tym większe możliwości i większa kontrola nad procesem. Aby umożliwić operatorowi efektywne zarządzanie i monitorowanie procesu podczas normalnego działania systemu, potrzebne jest nie więcej niż 6 ekranów, natomiast w czasie sytuacji awaryjnej – nie więcej niż 3 ekrany.
Dodatkowe ekrany wprowadzane do control roomu zazwyczaj są nieużywane i przedstawiają dodatkowe informacje nieistotne dla działania bieżącego procesu, a co za tym idzie niepotrzebnie rozpraszają. Ilość fizycznych ekranów w control room wprost zależy od tego, ile zostało zaprojektowanych ekranów wizualizacji.
Wprowadzenie dodatkowych ekranów, najczęściej jest wynikiem błędnie zaprojektowanej wizualizacji ekranu pierwszego (poziom 1 hierarchii projektowania), który powinien pokazywać wszystkie istotne informacje dla procesu produkcyjnego. Brak wiedzy projektanta na temat projektowania hierarchicznego skutkuje brakiem odpowiedniej ilości informacji na ekranie głównym, a tym samym wprowadzaniem dodatkowych ekranów z informacjami, które powinny znaleźć się na ekranie głównym.
Operator, który nadzoruje większość procesów sam, potrzebuje 4 ekrany wizualizacji oraz dodatkowy, piąty ekran główny – przedstawiający wszystkie informacje niezbędne dla prawidłowego działania procesu. Jeżeli wynikiem procesu jest więcej niż jeden produkt lub proces przechodzi różne etapy i stany działania, potrzebne mogą być jeden lub dwa dodatkowe ekrany.
Operator potrzebuje też komputera ogólnego przeznaczenia do innych zadań nie związanych z zarządzaniem i monitorowaniem procesu produkcyjnego, np. wysyłania maili, dlatego przy planowaniu centralnej dyspozytorni warto zaplanować miejsce na dodatkowy komputer. Warto zastanowić się, jaki sprzęt dobrać: monitor, panel HMI, czy komputer przemysłowy.
2. Sprzęt do komunikacji
Zazwyczaj każdy operator do komunikacji potrzebuje telefon, system nagłośnienia oraz dostęp do interkomu. Urządzania radiowe i telefony używane powszechnie w zakładach produkcyjnych zazwyczaj są jeszcze przewodowe. W przypadku projektowania control room’u i dobierania nowego sprzętu, wchodząc w kolejny etap unowocześniania systemów SCADA, warto rozważyć wprowadzenie urządzeń bezprzewodowych, takich jak słuchawki z mikrofonem. Da to większą mobilność operatorowi.
Działanie sprzętu do komunikacji oraz naładowanie baterii poszczególnych urządzeń powinno być sprawdzone przed każdą zmianą. Osoba, która dobiera sprzęt do komunikacji, musi zapewnić operatorom niezawodną i łatwą komunikację z inżynierami oraz menadżerami.
3. Konsole i klawiatury
Liczba konsoli do sterowania zależy od tego, jak skomplikowany jest proces oraz jaki jest jego aktualny stan. Wielość stanowisk z konsolą umożliwiającą wykonywanie zadań zarządzania jest potrzebna w przypadku trudnych uruchomień lub zatrzymań procesu. W takiej sytuacji do stanowiska kontroli potrzebny jest więcej niż jeden operator, dlatego trzeba pamiętać o przewidzeniu większej ilości stanowisk przed konsolą.
Dzięki temu możliwe jest podzielenie zakresu nadzoru na większą liczbę operatorów. Oczywiście możliwe jest kontrolowanie różnych ekranów z jednego stanowiska, ale zazwyczaj prowadzi to do chaosu i utraty całkowitej kontroli.
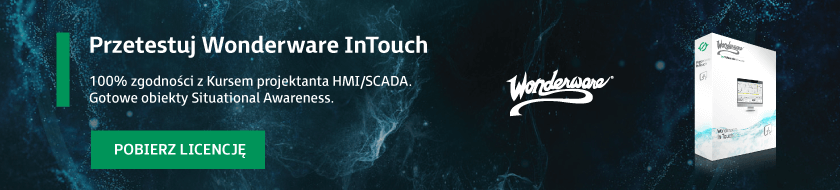
4. Przełączniki przewodowe
W pewnych szczególnych instalacjach w control room’ach potrzebne są fizyczne przełączniki przewodowe, żeby zapewnić natychmiastowy dostęp operatora lub redundancję w sterowaniu. Ich położenie musi zostać szczegółowo zaplanowane, żeby wzmocnić efektywność zarządzania w sytuacjach alarmowych ze stanowiska operatora.
Jak właściwie zaplanować położenie przycisków? Fizyczne przełączniki muszą zostać umiejscowione w taki sposób, aby tworzyły logiczny i spójny wzór przestrzenny (łatwy do zinterpretowania). Dodatkowo trzeba pamiętać o odpowiednim oznaczeniu lub opisaniu każdego z nich.
Przewodowe przełączniki najczęściej używane są przy aktywacji i zazwyczaj są połączone z graficznymi przyciskami wizualizacji. Przełączniki awaryjne umieszczone w wizualizacji w sposób graficzny muszą być odpowiednio opisane, tak żeby wskazywać na ich stan – gdy są włączone operator musi zostać o tym poinformowany w odpowiedni, łatwy do interpretacji sposób.
Umieszczenie przełączników w wizualizacji jest mniej kosztowne niż fizyczna implementacja ich na konsoli operatora, a konsola operatora jest mniej skomplikowana. W przypadku, gdy decydujemy się na umieszczenie przełączników i przycisków w wizualizacji, musimy zapewnić operatorowi szybki i łatwy dostęp oraz ich aktywację – dostęp do nich nie powinien wymagać przejścia do innych ekranów wizualizacji.
5. Lampki sygnalizacyjne
Lampki sygnalizacyjne mogą być alternatywą do systemu alarmowania w wizualizacji, ale są znacznie droższe w wprowadzeniu, utrzymaniu i modyfikacji. Zaletą lampek sygnalizacyjnych jest to, że są widoczne i dostępne cały czas, jednak nie powoduje to wzrostu wydajności w sytuacjach alarmowych. System alarmowania zaprojektowany w wizualizacji daje dużo większe możliwości zarządzania i przekazywania informacji.
Który system alarmowania jest lepszy – zaimplementowany w wizualizacji, czy w postaci lampek sygnalizacyjnych? Lepszym rozwiązaniem jest to, które dostarcza operatorowi więcej informacji i ułatwia mu zarządzanie alarmami.
W przypadku alarmu sygnalizowanego przez panel lampek sygnalizacyjnych operator dostaje tylko informację o zaistnieniu alarmu, natomiast wprowadzenie sygnalizowania alarmu za pomocą wizualizacji pozwala na umieszczenie dodatkowych informacji, takich jak np. w jakim czasie wartość graniczna została przekroczona i o ile.
Pamiętaj! Ilość lampek sygnalizacyjnych jest ograniczona do pewnej liczby alarmów, a zaprojektowanie panelu z lampkami musi być wykonane zgodnie z pewnymi kryteriami.
Jak właściwie zaprojektować panel z lampkami sygnalizacyjnymi?
- Każdy alarm umieszczony na panelu z lampkami sygnalizacyjnymi musi spełniać kryteria priorytetyzacji alarmów.
- Grupa alarmów musi być podzielona na podzbiory zgodnie z priorytetem i określonym wypracowanym podejściem. Nie powinno się wprowadzać wszystkich alarmów na panel z lampkami sygnalizacyjnymi.
- Alarmy umieszczone w postaci lampek sygnalizacyjnych muszą być odpowiednio opisane i umieszczone w spójny, logiczny sposób. Ich kolor oraz ułożenie powinny pomagać operatorowi w diagnozowaniu i działaniu operatora w konkretnych sytuacjach.
- Alarmy z lampek kontrolnych powinny być powiązane z wizualizacją, tak żeby możliwe było stworzenie i podgląd historii wystąpienia alarmów.
- System alarmowy powinny mieć jeden interfejs, a ich zatwierdzanie powinno być możliwe w jednym miejscu. Nie powinno się wprowadzać alarmów jednocześnie w wizualizacji i na panelu z lampkami kontrolnymi.
Sposób zamontowania i ułożenia ekranów w control room’ie
Ułożenie ekranów w control room’ie wpływa na komfort pracy operatora, na to jak szybko się on męczy oraz na szybkość jego reakcji. Standardowo ekrany z wizualizacji układane są poziomo w jednej płaszczyźnie. Takie ułożenie nie jest komfortowe dla operatora, bo wtedy nie jest w stanie objąć wszystkich ekranów zasięgiem wzroku nie przemieszczając się.
Aby to ulepszyć, stosuje się takie ułożenie ekranów, że jedna warstwa ekranów umieszczona jest niżej, na specjalnej wysuniętej półce, w taki sposób, że dolne ekrany są bliżej operatora i skierowane pod takim kątem, że operator jest w stanie – zachowując wyprostowaną postawę – swobodnie objąć wzrokiem ich zawartość. Niezależnie od postawy operatora (stojącej lub siedzącej), może on objąć wzrokiem zarówno górne, jak i dolne ekrany z wizualizacją. Dla stanowisk bez konsol takie ułożenie jest najlepsze.
Co powinno znaleźć się na stanowisku kontroli?
Aby zapewnić wszystkie elementy składowe stanowiska niezbędne do wydajnego monitorowania i zarządzania, należy pamiętać o umieszczeniu:
- dużego ekranu z wizualizacją dotyczącą całego procesu,
- 5 lub 6 ekranów wizualizacji,
- komputera ogólnego przeznaczenia,
- pozostałych monitorów przeznaczonych do innych celów,
- opcjonalnych lampek sygnalizacyjnych do alarmów,
- opcjonalnych przełączników umieszczonych na konsolach,
- sprzęt do komunikacji.
4 przykłady ułożenia stanowiska kontroli
Możliwe są różne opcje ułożenia ekranów i dodatkowego sprzętu na stanowisku operatora, który zarządza i monitoruje proces produkcyjny przy pomocy oprogramowania SCADA. Każda z nich ma swoje plusy i minusy, a wybór odpowiedniego ułożenia powinien zależeć od konkretnego zastosowania.
1.Ułożenie pionowe ekranów w jednym rzędzie.
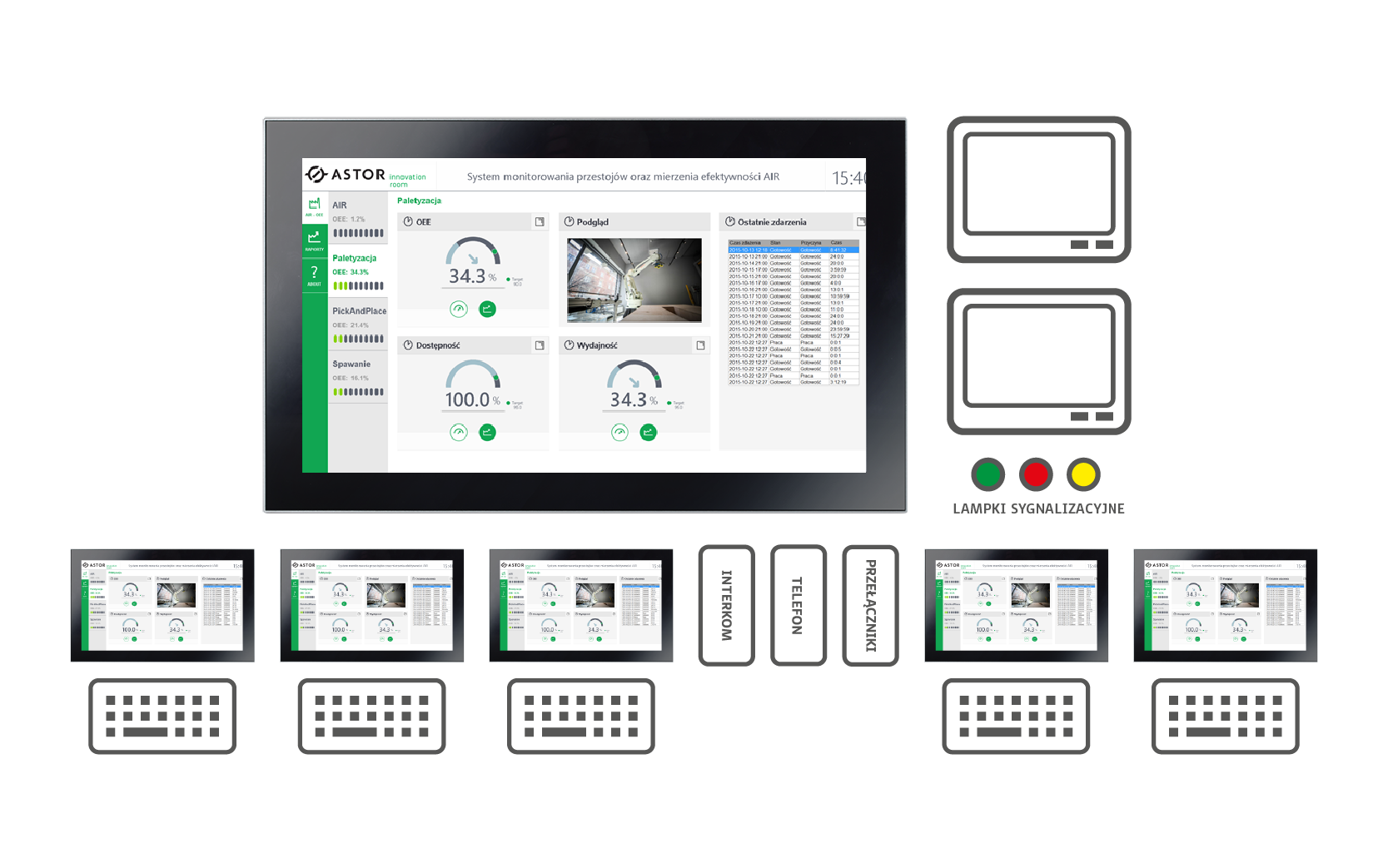
W takim ułożeniu ekran z główną wizualizacją poziomu 1 jest umieszczony nad operatorem, który siedzi na stanowisku. Cztery ekrany wizualizacji umieszczone są poziomo pod ekranem głównym, na jednej konsoli z klawiaturami i przedstawiają wizualizacje poziomu 2, 3 i 4 oraz ogólne zestawienie alarmów.
Oprócz ekranów z wizualizacją, na stanowisku, umieszczony jest komputer ogólnego przeznaczenia do użytku operatora w innych pracach nie związanych z nadzorowaniem. Dodatkowo, pomiędzy ekranami zostały umieszczone fizyczne przełączniki oraz urządzenia do komunikacji – takie jak telefon oraz radio, w takim miejscu, żeby operator miał do nich swobodny dostęp.
Na wysokości ekranu głównego jest opcjonalna możliwość umieszczenia panelu z lampkami sygnalizacyjnymi do alarmów oraz umieszczenia dodatkowych monitorów. W takim ułożeniu istnieje możliwość, żeby kolejny operator mógł pracować na tym stanowisku. Takie ułożenie ma też swoje wady, ponieważ zajmuje dużo miejsca, które w niektórych pomieszczeniach może być bardzo ograniczone. Dodatkowo ekrany są umieszczone w taki sposób, że zajmują dużo miejsca na szerokość, co powoduje, że nie wszystkie są w zasięgu wzroku operatora. Ten problem będzie szczególnie uciążliwy przy zastosowaniu większej ilości ekranów.
2. Ułożenie poziome ekranów z jednym ekranem w drugim rzędzie.
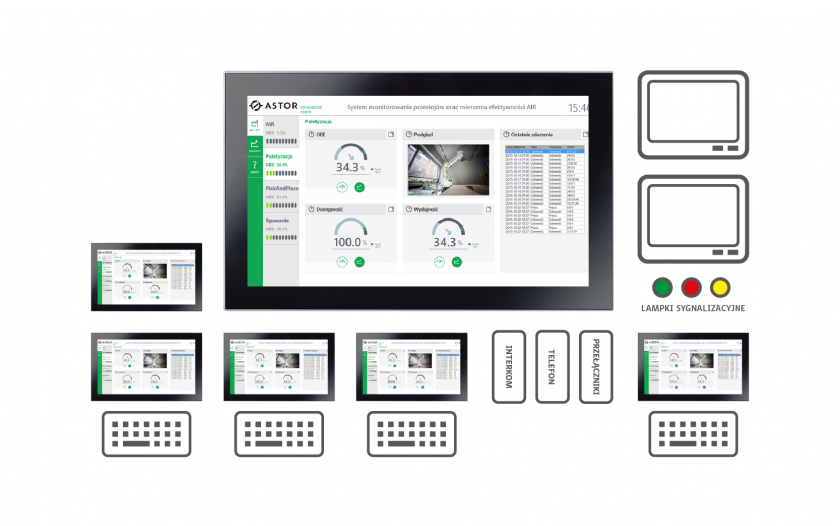
Takie ułożenie prowadzi do zredukowania szerokości stanowiska operatora. Ekran komputera ogólnego przeznaczenia zostaje umieszczony nad ekranem z podsumowaniem alarmów. Lepszym rozwiązaniem w ułożeniu ekranów w dwóch rzędach jest umieszczenie jednego rzędu bliżej operatora z kątem pochylenia w kierunku operatora.
3. Ułożenie 6 ekranów w dwóch rzędach
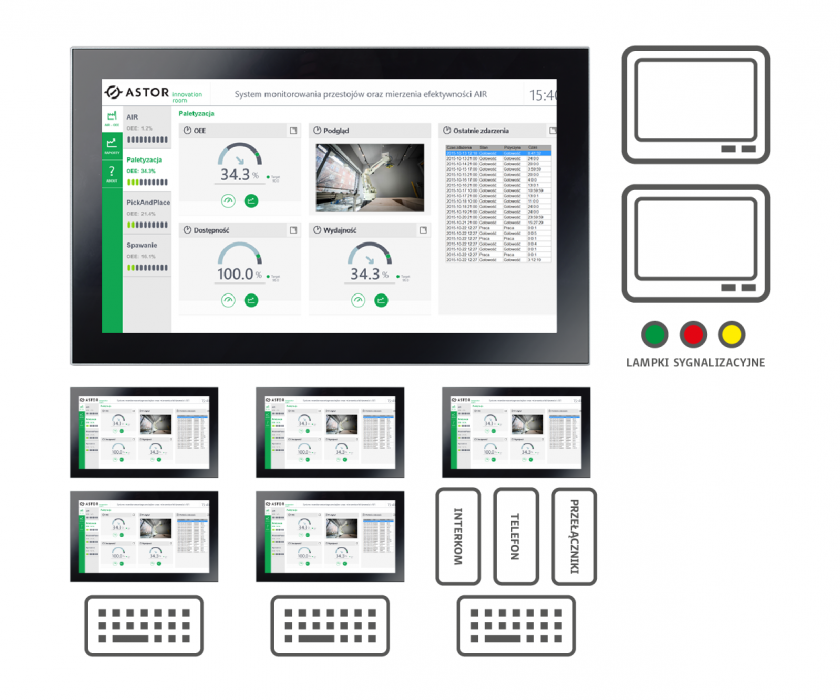
W takim ułożeniu należy zastosować półkę, na której zostają umieszczone ekrany dolnego poziomu. To umożliwi bardziej komfortową i efektywną pracę operatora. Takie rozwiązanie redukuje wykorzystanie szerokości stanowiska i może zostać wykorzystane, gdy przestrzeń na stanowisku jest ograniczona.
4. Ułożenie 8 ekranów w dwóch rzędach
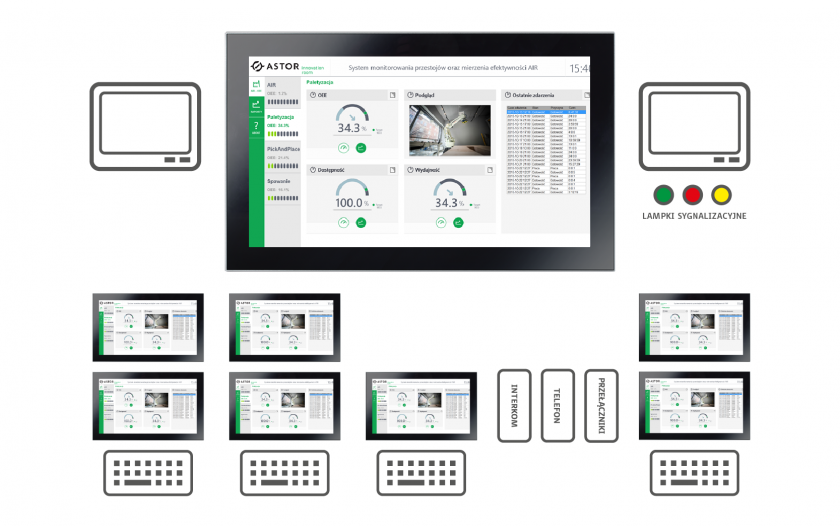
W szczególnych przypadkach, gdy zakres kontroli jest szczególnie duży, zawiera dużo podsystemów lub dotyczy wytwarzania wielu różnych produktów, mogą być potrzebne dodatkowe 2 ekrany. Aby zapewnić możliwość złapania zasięgiem wzroku wszystkich ekranów, zastosowano ułożenie analogiczne dla poprzedniej konfiguracji – w dwóch rzędach, gdzie dolny rząd zamontowany jest na półce, bliżej operatora. Oczywiście w przypadku tak dużej ilości ekranów odczuwalna będzie ograniczona możliwość skupienia się przez operatora.
Projektowanie control room’u
Właściwie zaprojektowana centralna dyspozytornia zapewnia komfort pracy operatora, jego czujność i efektywność. Ważna jest świadomość tego, jakie skutki, korzyści i wady mają elementy, czynniki i parametry centralnej dyspozytorni.
Co powoduje, że pomieszczenia centralnej dyspozytorni są nieefektywne dla operatora?
- słabe oświetlenie,
- nadmiernie błyszczące ekrany, na których zostają wyświetlone wizualizacje,
- zbyt mała czcionka na ekranach,
- niewłaściwa wysokość i kąt pochylenia ekranów,
- ograniczony dostęp do elementów wizualizacji, których potrzebuje operator,
- niewłaściwa lokalizacja konsoli z klawiaturą,
- źle zintegrowane urządzenia komunikacyjne,
- brak ekranu z główną wizualizacją dotyczącą działania procesu,
- zbyt duża ilość ekranów, która zajmuje zbyt dużo miejsca, przez co nie może być efektywnie monitorowana i nadzorowana,
- obecność w pomieszczeniu osób, których obecność nie jest konieczna,
- błędne rozmieszczenie w pomieszczeniu elementów służących do pracy operatora,
- prace serwisowe przeprowadzane w control room’ie,
- duże zakresy hałasu,
- duże zanieczyszczenie pyłem,
- nieodpowiednia wentylacja.
Jak właściwie zaprojektować control room?
Aby control room spełniał swoją rolę przy projektowaniu i planowaniu, należy trzymać się pewnych zasad i wziąć pod uwagę główne czynniki, takie jak:
- lokalizacja,
- rozmieszczenie wewnętrznych i zewnętrznych okien,
- liczba stanowisk operatorów,
- liczba stanowisk bez konsoli,
- fizyczne przyciski i przełączniki umieszczone na konsoli,
- wymagania dla serwerowni,
- detekcja gazu i ognia,
- integralność / redundancja mocy,
- dostęp do pomieszczenia dla innych użytkowników (inżynierowie procesu, technicy wizualizacji, nadzoru),
- strategie operacyjne i zespół dla każdego stanu operacyjnego,
- informacje na temat mebli do konsoli,
- liczba konsoli (klawiatur) i ich lokalizacji,
- rozmieszczenie gniazdek elektrycznych,
- pozostały sprzęt (anteny, komputery, stoliki, drukarki…),
- wymagania bezpieczeństwa,
- wentylacja budynku,
- barierki,
- dokumentacja,
- wymagania do testów i symulacji,
- zasilanie awaryjne,
- wymagania dotyczące telefonów i wideo,
- wymagania przechowywania sprzętu,
- wymagania dotyczące ochrony przed przepięciami,
- waga sprzętu,
- dodatkowe sąsiadujące pokoje,
- zdalne lub lokalne montowanie komputerów.
Przy projektowaniu centralnej dyspozytorni pamiętaj o standardach ergonomii pracy przed komputerem, a więc wysokości umieszczenia monitora, kątów i pola widzenia oraz wielkości ekranów.
Dodatkowo uwzględnij: oświetlenie, nagłośnienie, przepływ pracowników oraz planowanie przestrzeni do zapewnienia odpowiedniej odległości od drzwi do stanowisk operatorów.
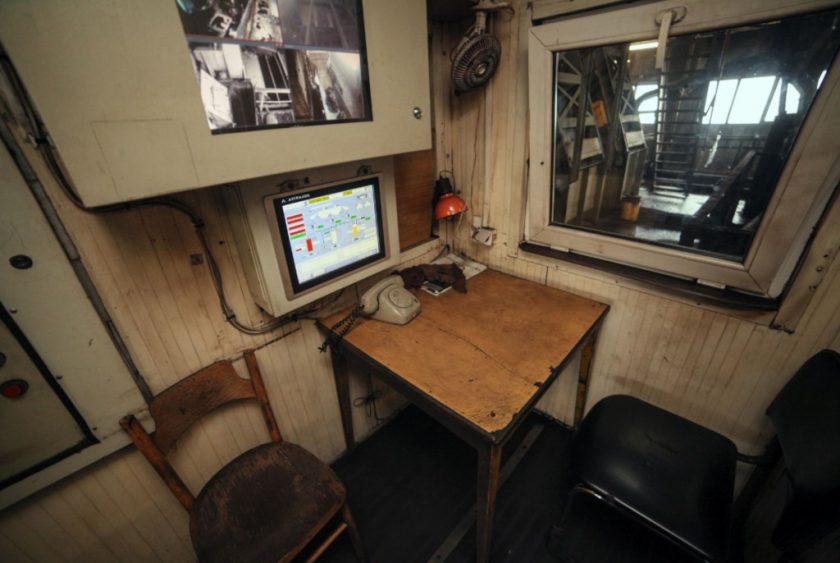
Poziom oświetlenia
Poziomy oświetlenia preferowane w centralnej dyspozytorni są dostosowywane do konkretnego stanowiska pracy, jednak warunki zazwyczaj nie są idealne – należy tak doświetlać stanowisko, żeby spełniło oczekiwania opeartorów.
Dobór oświetlenia zależy od tła wybranego w wizualizacji HMI – przy dobraniu odpowiedniego tła można uniknąć efektów błyszczenia ekranów i odbijania światła. Dodatkowym czynnikiem, który wpływa na dobór oświetlenia jest kolor ścian, rodzaj podłogi, czy nawet białych tablic zamontowanych w pomieszczeniu. W wizualizacjach SCADA kolor tła powinien być szary – to spowoduje zmniejszenie efektu odblasku na ekranie.
Poziom oświetlenia w control room’ie powinien być stabilny. Zmiany poziomów oświetlenia mogą m.in. powodować zmęczenie, nieuwagę oraz bóle oczu.
Akustyka i nagłośnienie
Na niewłaściwą akustykę pomieszczenia control room mają wpływ zarówno hałas maszyn, innego sprzętu z produkcji, ale też np. telefonów. Aby zapewnić odpowiednią akustykę, stosuje się warstwy lub ścianki wygłuszające. Dla nowych pomieszczeń control room warto przemyśleć zastosowanie takiego rozwiązania, aby znacząco zmniejszyć słyszalny poziom hałasu.
Rozmieszczenie stanowisk operatorów
Stanowiska operatorów w control room’ach powinny być ułożone w taki sposób, żeby możliwa była komunikacja pomiędzy nimi, a relacje pomiędzy nimi powinny odpowiadać relacjom w procesie produkcji pomiędzy poszczególnymi elementami składowymi i produktami. Jeżeli stanowiska zostaną logicznie rozmieszczone, z łatwością będzie można wnioskować, kto odpowiada za jaką część procesu, przez co łatwiej będzie zachować spójność kontroli odpowiadającej spójności procesu.
Ściana wideo
W niektórych przypadkach, gdy wszyscy operatorzy powinni widzieć dany ekran wizualizacji, dobrą praktyką jest wprowadzenie ściany wideo dla całego pomieszczenia, z wieloma ekranami. W zastosowaniu ściany wideo wszyscy operatorzy mają łatwy i szybki dostęp do wizualizacji na niej wyświetlanej. Ważne jest jednak, żeby stosowanie takiego rozwiązania nie było nadużywane – zawartość wyświetlana na tych ekranach musi dotyczyć i być potrzebna każdemu operatorowi, w innym przypadku będzie tylko rozpraszać.
W tym miejscu warto przeprowadzić kwestionariusz „Kryteria oceny wydajnej wizualizacji HMI / SCADA cz.2”, który znajdziesz na swojej skrzynce pocztowej. Formularz znajdziesz także wyżej w tym artykule.
Masz doświadczenie w projektowaniu pomieszczeń centralnej dyspozytorni lub dobierałaś/dobierałeś sprzęt? Co jeszcze według Ciebie powinno się w nim znaleźć? Napisz w komentarzu.
Jeśli masz jakieś pytania, napisz do autora artykułu: ewelina.niziolek@astor.com.pl
W kolejnym artykule z cyklu „Kurs projektanta systemów HMI/SCADA”: Jak dbać o rozwój i przyszłość systemów HMI/SCADA:
- Jaka jest przyszłość systemów HMI/SCADA w przedsiębiorstwach?
- Jak dbać o rozwój takich systemów?
- Czego nauczyłeś/nauczyłaś się w kursie, czyli wiedza projektanta w pigułce
Inspiracją i źródłem do powstania „Kursu projektanta systemów HMI/SCADA” są:
- „The High Performance HMI Handbook” – Bill Hollifield, Dana Oliver, Ian Nimmo, Eddie Habibi.
- „Wonderware design guidelines” – materiały Wonderware
- „InTouch Demo conception document” – materiały Wonderware
- Situational Awareness – materiały AVEVA https://sw.aveva.com/monitor-and-control/industrial-information-management/situational-awareness
Czytanie tego bloga to dla mnie zawsze miłe chwile spędzone w towarzystwie ciekawych treści! Autorzy potrafią zainteresować nawet najbardziej wymagających czytelników.