EtE®flow: skalowalne rozwiązania dla nowoczesnego transportu palet
Kontakt w sprawie artykułu: Kinga Tarsa - 2024-11-13
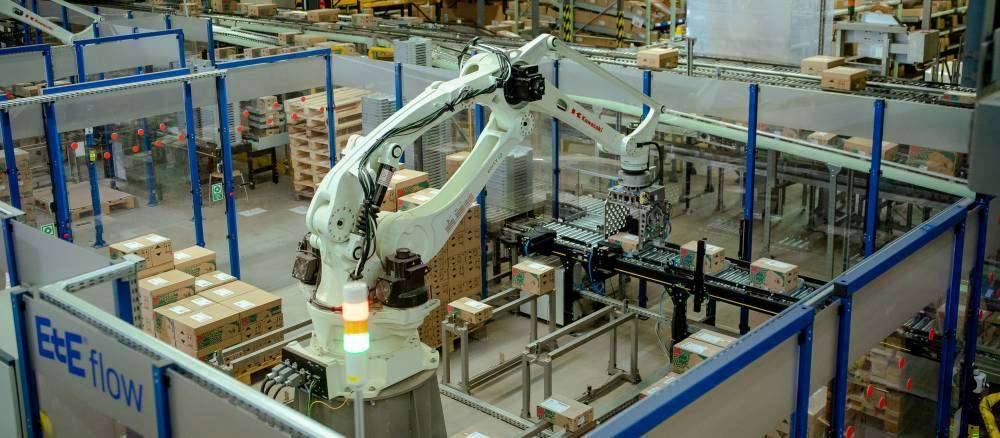
O inteligentnej intralogistyce i marce EtE®flow rozmawiamy z Adamem Pajdą, dyrektorem Linii Biznesowej Intralogistyka w firmie ASTOR.
Jak najkrócej zdefiniowałbyś zakres działalności Linii Biznesowej Intralogistyka w ASTOR?
Adam Pajda: Specjalizujemy się w kilku obszarach należących do szeroko rozumianej intralogistyki. Są to wszelkie systemy transportu wewnątrzzakładowego: zyskujące coraz większą popularność autonomiczne roboty mobilne oraz całość konwencjonalnych rozwiązań, przeznaczonych do transportowania wszelakich surowców, materiałów oraz gotowych produktów – między operacjami lub z produkcji do magazynu, bez względu na nośnik, w którym się znajdują. Drugim elementem są systemy obsługujące proces kompletacji zleceń, łącznie z oprogramowaniem nadzorującym ich pracę i wspierającym optymalizację. Trzeci obszar to zrobotyzowana paletyzacja produktów, działająca na końcówkach linii produkcyjnych. Intralogistyka jest najmłodszą linią biznesową w ASTOR. Specjalizacja właśnie w tym kierunku wynikła na przestrzeni lat z naszych szerokich doświadczeń w tym zakresie. Jest to obszar ponadbranżowy, bo rozwiązania intralogistyki potrzebne są w każdym niemal rodzaju produkcji, gdzie tylko mamy do czynienia z potrzebą transportowania jakichkolwiek towarów. W znakomitej większości przypadków naszą pracę możemy sprowadzić do dwóch słów: transportujemy palety. Jesteśmy dostawcą inteligentnych technologii i producentem systemów intralogistyki.
Między innymi dlatego powstała nowa marka EtE®flow.
Wszystkie systemy intralogistyki, które produkujemy, będą dostarczane pod brandem EtE®flow. Chcemy mieć silną markę, rozpoznawalną na rynku, taki jest strategiczny cel. Pod tą marką powstają rozwiązania intralogistyki w pełni dostosowywane pod oczekiwania klienta, które rozwijamy wspólnie z naszymi Partnerami, jak również portfolio gotowych produktów, spełniających określone zadania.
Dowiedz się więcej o skalowalnych systemach inteligentnej intralogistyki EtE®flow.
Zacznijmy od transportu wewnątrzzakładowego. To dość szerokie pojęcie.
Traktujemy intralogistykę jako transport wewnątrzzakładowy, ale faktycznie w ramach tego pojęcia możliwych jest wiele różnych scenariuszy. Może być transport z punktu do punktu, czyli transport międzyoperacyjny, zwinny, mobilny. Wtedy wykorzystujemy autonomiczne roboty mobilne AGILOX. Drugi scenariusz to rozwiązania konwencjonalne. Chodzi o sytuacje, gdy obejmujemy transportem część zakładu, na przykład z końcówek linii produkcyjnych na magazyn, bądź sam proces produkcji. Stosujemy do tego wtedy transport standardowy z wykorzystaniem na przykład transporterów rolkowych do przenoszenia palet albo półfabrykatów. Wreszcie trzeci scenariusz, optymalny dla coraz większej liczby zadań, czyli hybryda obu poprzednich. Wtedy łączymy tradycyjną, klasyczną intralogistykę, związaną z transportem stacjonarnym, z rozwiązaniami inteligentnej robotyki mobilnej.
Domyślam się, że wybór scenariusza zależy przede wszystkim od konkretnej potrzeby klienta?
Tak jest – i zaczynamy zawsze od tego, żeby właśnie tę potrzebę dobrze zdefiniować. Ściśle współpracujemy z firmami produkcyjnymi, które są zainteresowane dostarczeniem systemu intralogistycznego. Rozmawiamy oczywiście z kadrą zarządzającą, menedżerami i kierownikami obszarów, żeby dobrze zrozumieć potrzeby biznesowe, ale również z osobami pracującymi bezpośrednio na produkcji, zwłaszcza z liderami obecnych gniazd czy też linii produkcyjnych – żeby uchwycić codzienne wyzwania. Takie wielowymiarowe podejście jest bardzo potrzebne, dlatego że każde takie zadanie można rozwiązać na wiele sposobów. Opieramy się ściśle na faktach, nie „zgadujemy” żadnych parametrów, wszystkie dane i informacje uzyskujemy bezpośrednio od klienta.
Jak wykorzystujecie zebrane informacje?
Staramy się stworzyć mapę takiego procesu, poprzez symulacje i tworzone przez nas na ich bazie raporty, które dają klientowi dokładny obraz tego, jak może wyglądać jego nowy system, ale też jakie korzyści odniesie po jego uruchomieniu. Wszystkie procesy zbieramy w jedną całość, tak żebyśmy możliwie holistycznie mogli ujrzeć całe zadanie, nie tylko dzisiaj, ale też z możliwością rozbudowy w przyszłości. Staramy się przy tym, aby projektowany przez nas system był – jak to nazywamy – transparentny. Chodzi o to, że on powinien być po jakimś czasie praktycznie niezauważalny dla pracownika, powinien być naturalną pomocą i realnym uzupełnieniem jego codziennej pracy.
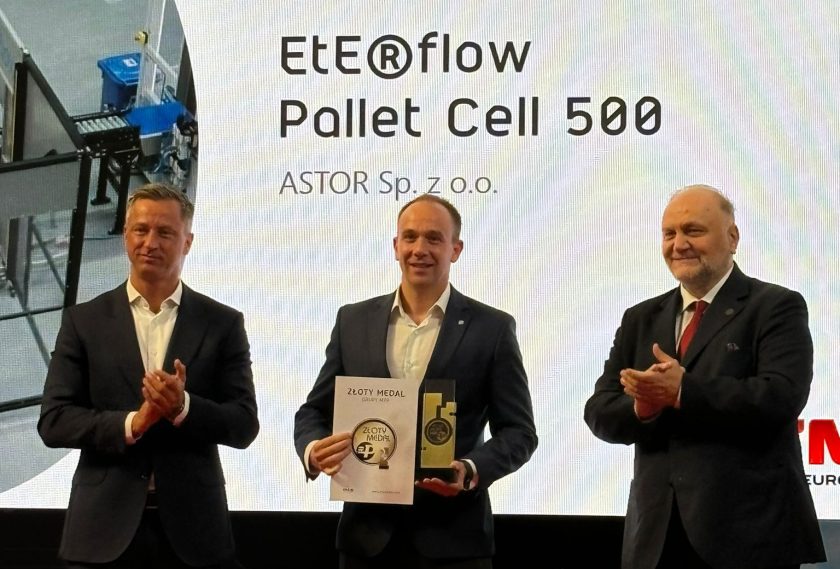
Wspomniałeś o rozbudowie systemów. Rozwiązania EtE®flow są skalowalne?
Dbamy o to, aby projektowane przez nas systemy można było w łatwy sposób przeskalować, żeby one były rozwiązaniami modułowymi. Dobrze obrazuje to obszar robotów mobilnych, który często w pierwszej fazie ogranicza się do jednostki, aby z czasem zamienić się we współpracującą ze sobą flotę. Albo jest to jakaś część linii transportowej, która później może być w łatwy sposób rozbudowana o kolejnej nitki produkcyjne. Jednocześnie wszystkie techniczne i wydajnościowe aspekty tych systemów zawsze konfrontujemy z ich opłacalnością. Zawsze szukamy odpowiedzi na pytanie: czy to się klientowi opłaci – i w jakim zakresie.
W tym miejscu oprócz doradztwa ściśle technicznego pojawia się też aspekt biznesowy.
Tak, konieczne jest dokładne sprawdzenie, czy to się po prostu opłaca, oraz co warto, a czego nie warto robić. Natomiast intralogistyka generalnie powinna być skalowalna, to jest zupełnie naturalne. Często zachęcamy wręcz do podejścia etapowego. Jeżeli na przykład widzimy, że u klienta do realizacji procesów wewnątrzzakładowych potrzebnych jest 10 robotów mobilnych, to często sugerujemy, aby zrobić wdrożenie „proof of concept”.
Zacznijmy od jednego robota?
Tak. Ma to też dodatkową – oprócz minimalizacji ryzyka finansowego – zaletę. Trzeba pamiętać, że dostarczenie systemów intralogistyki, zwłaszcza jeżeli mówimy o nowoczesnych technologiach lub pierwszym robocie mobilnym, to jest duża zmiana w kulturze i organizacji pracy u klienta. Może się więc to wiązać z różnymi emocjami, zamieszaniem organizacyjnym. Dlatego jeśli zauważamy takie ryzyko dla inwestora, żeby zmniejszyć próg wejścia często sugerujemy podejście etapowe. Po prostu realizujemy taki projekt w kilku krokach, wspieramy technicznie, dbamy o coraz większą samodzielność załogi i w momencie kiedy już widzimy, że to się sprawdza, a organizacja jest gotowa, po prostu skalujemy system, dodając kolejne jednostki. Z punktu widzenia klienta początkowo jest to rodzaj „Proof of Value”, co pozwala odpowiedzialnie i bezpiecznie skalować system w przyszłości.
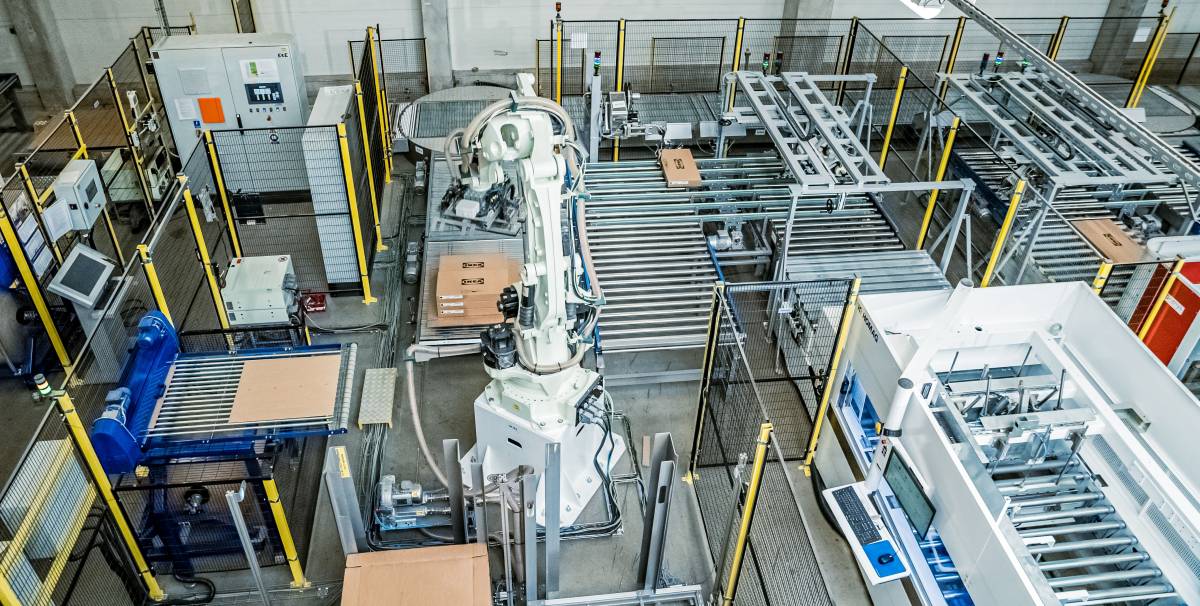
Intralogistyka to nie tylko sprzęt, ale również oprogramowanie.
Zgadza się. Aby w pełni wykorzystać potencjał nowoczesnej intralogistyki łączymy nie tylko systemy transportowe czy roboty mobilne, ale też zaawansowane systemy informatyczne, które nadzorują urządzenia, czuwają nad procesami, czuwają nad tym, żeby optymalnie wykorzystać zasoby czy wspierają człowieka w podejmowaniu decyzji, często strategicznych, związanych z rozwojem przedsiębiorstwa. Takie połączenie intralogistyki z oprogramowaniem daje po prostu dodatkowe korzyści, a czasami jest warunkiem koniecznym, żeby stworzyć możliwości rozwoju przedsiębiorstwa. Dlatego bardzo ważna jest szeroka wiedza z tego zakresu, żeby odpowiednio przeprowadzić proces inwestycji, właśnie ze względu na te wspomniane przeze mnie wcześniej zmiany organizacyjne w przedsiębiorstwie. Intralogistyka w takim ujęciu łączy kilka linii biznesowych w ASTOR – systemy budujemy w oparciu o sterowniki PLC, roboty i oprogramowanie przemysłowe z szerokiej oferty naszej firmy, co gwarantuje wysokie kompetencje techniczne w każdym kluczowym obszarze nowopowstałego systemu. To znacząco obniża ryzyko inwestycji i pozwala skrócić czas trwania projektu.
Co dzieje się, gdy przechodzimy od projektu do realizacji?
Jeszcze zanim rozpoczniemy realizację projektu, kiedy jesteśmy na końcowym etapie przygotowywania koncepcji, do zespołu dołącza osoba, która będzie koordynowała projekt na etapie realizacji. Zapewnia to bezproblemowe przejście pomiędzy etapami inwestycji i odpowiednio wcześnie wprowadza project managera, zwłaszcza w najbardziej newralgiczne obszary projektu. Na pierwszym takim „realizacyjnym” spotkaniu podsumowujemy harmonogram, dokładnie omawiamy, w jaki sposób będziemy pracować, a następnie przekładamy opracowane wcześniej koncepcje na realny projekt wykonawczy całego systemu i poszczególnych maszyn. Oczywiście wykorzystujemy sprzęt i oprogramowanie naszych dostawców: Kawasaki Robotics, AGILOX, Astraada, Emerson i AVEVA. Na tym etapie w projekt zostają również zaangażowani nasi Partnerzy.
Właśnie, to bardzo istotne: ASTOR nie realizuje takiej inwestycji sam.
Zaangażowanie Partnerów ma kluczowe znaczenie. Współpracujemy z wieloma firmami inżynierskimi, integratorskimi, które są wyspecjalizowane w określonych zadaniach, na przykład w produkcji jakiejś maszyny albo w końcówkach linii, albo w produkcji komponentów lub tworzeniu aplikacji dla sterowników. Powstaje zatem zespół firm, któremu przewodzi ASTOR, realizując generalne wykonawstwo, dbając o harmonogram czy jakość. Odpowiadamy za zgodność powstającego systemu z wcześniej przygotowaną analizą techniczno-funkcjonalną, czyli dokumentem, który dokładnie opisuje to, w jaki sposób system działa. Razem z Partnerami de facto produkujemy gotowy system u klienta, dostarczając go wraz ze szkoleniami, serwisem. Wszystko pod klucz.
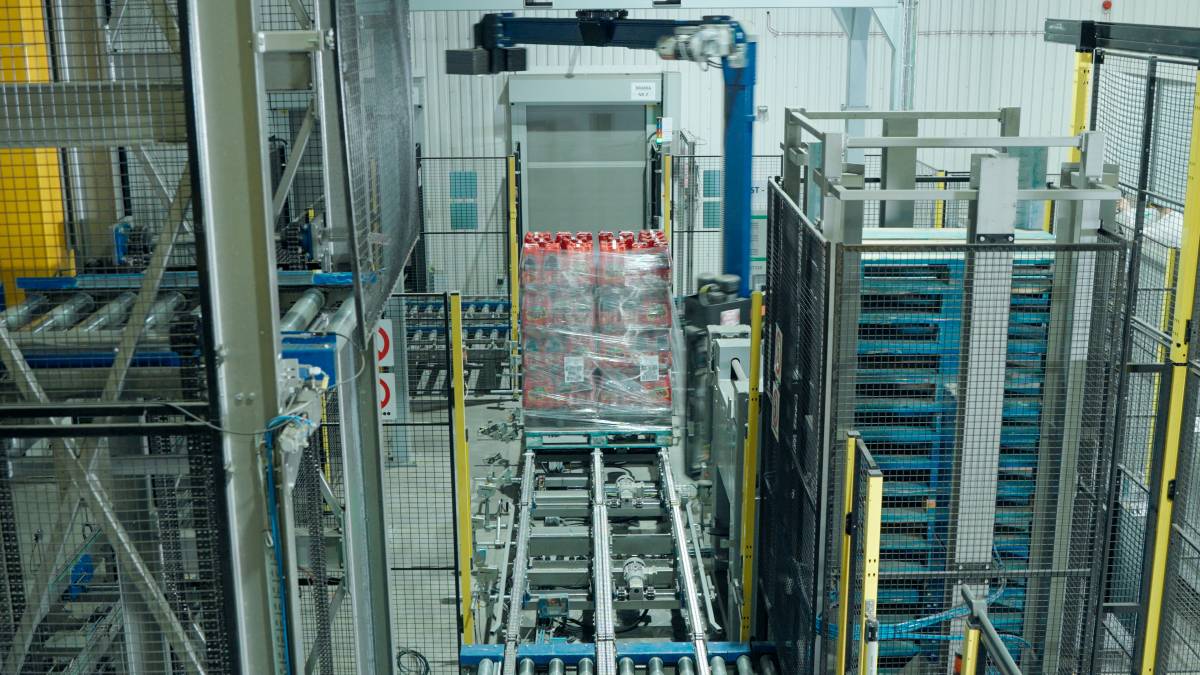
Wspomniałeś wcześniej, że EtE®flow to także gotowe produkty. O jakie produkty może chodzić, gdy mówimy o intralogistyce.
Mamy już w ofercie pierwsze takie produkty, to cele paletyzujące EtE®flow PallettCell. To faktycznie gotowe rozwiązania, realizujące określone zadanie – w tym wypadku zrobotyzowaną paletyzację – dla konkretnych produktów i z wyznaczoną wydajnością. Ponieważ są to projekty zbudowane ze standaryzowanych komponentów, możemy zapewnić je szybko, a tym samym bardzo przyspieszyć dostarczenie i uruchomienie systemu. Warto tu podkreślić, że takim gotowym produktem jest też autonomiczny robot mobilny AGILOX. Może on oczywiście wchodzić w skład dużego, zaawansowanego systemu, ale klient może również wykorzystać takiego robota „solo” – i bez dodatkowej infrastruktury czy reorganizacji na hali zacząć go używać. Zawsze sporym zaskoczeniem dla klienta jest czas uruchomienia takiego robota. Przy podstawowych założeniach po kliku dniach Agilox już porusza się po alejkach, wykonując zadane mu misje, a użytkownik ma wiedzę i narzędzia, aby umieć modyfikować jego pracę lub wyciągać wnioski z oprogramowania analitycznego
Bardzo szybko.
Jeżeli mówimy o kompleksowym systemie, który trzeba zaprojektować i zbudować, to wiadomo, że to musi trwać dłużej, podobnie jak wybudowanie hali też trwa. Nie da się hali wybudować w tydzień i takiego systemu też się nie da zrobić w tydzień. Natomiast jeżeli mówimy o robocie, to robot jest praktycznie gotowy do pracy po rozpakowaniu. Tak naprawdę ten robot jest jednocześnie produktem i rozwiązaniem dla klienta, bo realizuje zadania transportowe, a nie potrzebuje budowania żadnej dodatkowej infrastruktury. W dużym skrócie, logika jego pracy polega na dynamicznym porównywaniu mapy zapisanej w pamięci do rzeczywistych warunków na hali i na tej podstawie wyznacza sobie ścieżki przejazdów na obszarach, do których damy mu dostęp.
Można więc powiedzieć, że marka EtE®flow oznacza ofertę bardzo szeroką. Z jednej strony gotowe produkty „z półki”, a z drugiej – duże systemy, projektowane i – dostarczane zgodnie z indywidualnymi potrzebami klientów.
Tak jest, EtE®flow to gotowe, szybko dostarczane i sprawdzone produkty oraz rozbudowane, ale modułowe i skalowalne rozwiązania. Wszystko to w trzech obszarach: systemy transportu wewnatrzzakładowego, kompletacja zleceń i końcówki linii produkcyjnych ze zrobotyzowaną paletyzacją.
Rozmawiał: Mateusz Pierzchała