Dlaczego warto przejść ze sterowników PLC VersaMax na kontrolery Emerson PACSystems RSTi-EP?
Kontakt w sprawie artykułu: Piotr Adamczyk - 2024-05-13
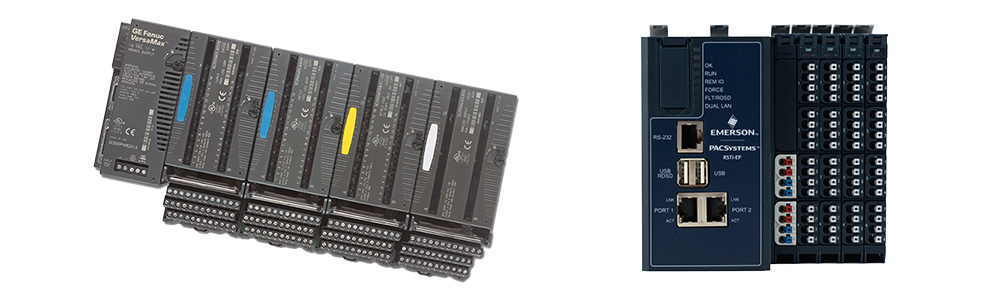
Każdy system sterowania się starzeje. Z jednej strony starzeje się sprzęt, z drugiej – zmieniają się potrzeby użytkowników w zakresie funkcjonalności wymaganej od systemu sterowania. Zakres odpowiedzialności systemów automatyki jest cały czas taki sam: kontrola pracy obiektu. Jednak obecnie standardy w branży automatyki wymuszają stosowania nowoczesnych rozwiązań, które podniosą poziom bezpieczeństwa i pozwolą na łatwą integrację w ramach prowadzonych projektów pełnej cyfryzacji zakładów przemysłowych.
Dopasowanie produkcji do aktualnych potrzeb – poprzez jej lepsze planowanie, optymalizację, kontrolę parametrów produkcyjnych oraz przewidywanie zachowania całego układu – w bezpośredni sposób przekłada się niższe koszty produkcji i lepszą konkurencyjność. Ale cały czas głównym elementem systemu pozostaje układ sterowania, który nie tylko kontroluje proces produkcyjny, ale także dostarcza dane, mające wpływ na jego optymalizację.
Sterownik VersaMax – ponad 20 lat na rynku
VerasMax to sterowniki PLC, które zrewolucjonizowały tysiące obiektów przemysłowych w Polsce i które w dalszym ciągu pracują w wielu instalacjach. Minęło jednak ponad 20 lat od ich premiery, a dziś samo sterowanie przestaje wystarczać. Coraz większe znaczenie ma możliwość zbierania, przetwarzania i udostępniania danych produkcyjnych, serwisowych, statusowych i danych pochodzących spoza obszaru produkcji.
Czego brakuje w VersaMax? Przede wszystkim możliwości komunikacyjnych i większych zasobów programowych, pozwalających obsługiwać bardziej złożone i zaawansowane algorytmy. Co nadal jest bardzo cenione w VersaMax? Na pierwszym miejscu użytkownicy wymieniają bardzo dużą niezawodność, łatwość obsługi i serwisu oraz elastyczną, modułową architekturę. Ale coraz bardziej uciążliwe stają się też inne rzeczy: wolna komunikacja, duże gabaryty, brak redundancji, programowanie wyłącznie w IL i LD czy słaby poziom zabezpieczeń.
PACSystems RSTi-EP następcą linii VersaMax
Sterowniki VersaMax długo jeszcze pozostaną dostępne – producent gwarantuje dostępność i wsparcie do 2035 roku. Jest tak również dlatego, że moduły tej serii są bardzo chętnie wybieranym rozwiązaniem jako układ wejść-wyjść oddalonych podłączany do kontrolerów PACSystems RX3i i systemów redundantnych PACSystems PNSR RX3i. Ale w nowych systemach do kontroli pracy obiektu lepiej skorzystać z nowoczesnych rozwiązań PACSystems i rodziny RSTi-EP, która serię VersaMax powoli zaczyna zastępować. Dlaczego warto przejść na PACSystems?
Cała rodzina urządzeń PACSystems od Emerson wykorzystująca wspólny dla wszystkich urządzeń PAC Engine to odpowiedź na rosnące potrzeby obecnych systemów sterowania. Wprowadzone do oferty w 2005 roku rozwiązanie początkowo w rodzinie PACSystems RX3i i RX7i, jest nieustannie rozwijane i wykorzystywane w każdej kolejnej generacji i rodzinie kontrolerów PAC, jakie Emerson wprowadza do swojej oferty:
- kontrolerach StandAlone PACSystems CPE100/115, przeznaczonych do systemów małej i średniej wielkości,
- kontrolerach StandAlone CPE400/410, przeznaczonych do ekonomicznych układów redundancji i aplikacji wykorzystujących przetwarzanie brzegowe w aplikacjach średniej i dużej wielkości,
- kontrolerach PACSystems RX3i CPE302/305/310 przeznaczonych do średnich i dużych aplikacji automatyki,
- kontrolerach PACSystems RX3i CPE330 w układzie wysokiej dostępnością dla aplikacji oznaczeniu krytycznym,
- kontrolerach PACSystems Micro (nowość zapowiadana na rok 2025), które przeznaczone będą do najprostszych zastosowań.
Element wspólny we wszystkich kontrolerach serii PACSystems – w postaci PAC Engine – jest ich największą zaletą. Aplikacja przygotowana na dowolną rodzinę PACSystems może być przenoszona pomiędzy rodzinami bez potrzeby jej modyfikacji. Języki programowania oraz kod aplikacji są kompatybilne między sobą, dzięki czemu do programowania całego systemu wykorzystujemy jedno narzędzie i ten sam kod programu. Ma to wielkie znaczenie dla służb utrzymania ruchu oraz programistów systemów.
Ale PACSystems to nie tylko kompatybilny program. To cała nowoczesna technologia, która z jednej strony unifikuje system sterowania, a z drugiej sprawia, że jest otwarty na integrację z dowolną inną platformą sprzętową innych dostawców sterowników PLC i producentów oprogramowania SCADA.
Dowiedz się więcej o kontrolerach Emerson PACSystems RSTi-EP.
Możliwości komunikacyjne kontrolerów PACSystems
Bardzo mocną stroną rodziny PACSystems jest komunikacja. Wszystkie urządzenia obsługują komplet protokołów, które obecnie są standardem w nowoczesnych systemach sterowania: Profinet MPR z obsługą komunikacji Simplex i Redundant, OPC-UA Server, Modbus TCP Client/Server, Modbus RTU Master/Slave, Serial ASCII, DNP3 (w wybranych jednostkach) – wykorzystanie tych protokołów nie wymaga żadnych licencji i żadnych dodatkowych opłat.
Możliwość wymiany danych uzupełniają natywne dla Emerson standardy, takie jak SNP, SNP(X), SRTP czy EGD. To wszystko sprawia, że bez względu na to, z jakiej rodziny sterowników PLC i kontrolerów PAC korzystamy, będziemy w stanie połączyć wszystkie urządzenia za sobą w jeden spójny system. Jeśli wbudowana w standardzie komunikacja nie wystarcza, serię RX3i można rozbudować dodatkowo o obsługę Profibus DP Master/Slave oraz IEC65811.
Opisane możliwości komunikacyjne umożliwiają także łatwą integrację z systemami przetwarzania brzegowego oraz systemami IIoT. Trend zapoczątkowany wraz z czwartą rewolucją przemysłową przybiera na sile i w najbliższych latach można spodziewać się, że stanie się takim samym standardem, jak obsługa zmiennych symbolicznych w sterownikach PLC. Możliwości, jakie daje Edge Computing, są odpowiedzią na rosnące zapotrzebowanie na lokalne przetwarzanie brzegowe i analitykę danych mających wpływ na prowadzony proces produkcyjny.
Optymalizacja wykorzystania łączy komunikacyjnych oraz rygorystyczna polityka separacji systemów sterowania od sieci zewnętrznych i komunikacji z chmurą obliczeniową powodują, że na rozwiązania do brzegowego przetwarzania danych decyduje się coraz więcej użytkowników. Obszarem tym interesują się przede wszystkim inżynierowie mający świadomość , że odpowiednio przetworzone dane zgromadzone z produkcji i otoczenia produkcyjnego będę niosły dodatkowe wartościowe informacje. W oparciu o nie proces będzie można prowadzić bardziej optymalnie, a serwis będzie interweniował nie w przypadku wystąpienia awarii, tylko odpowiednio wcześniej – aby awarii zapobiec.
PACSystems nie tylko potrafi dane do systemu przetwarzania brzegowego udostępnić, ale i z nich skorzystać, wprowadzając je jako parametry pracy sterowanego obiektu. Przetwarzanie brzegowe w przypadku PACSystems może być realizowane bezpośrednio na kontrolerze odpowiedzialnym za prowadzenie procesu. Model PACSystems CPL410 powstał właśnie w tym celu: aby dać funkcjonalność zaspokajającą potrzeby wymagających użytkowników, minimalizując jednoczenie liczbę urządzeń w całym systemie.
Kontrolery PACSystems gwarantują najwyższy poziom bezpieczeństwa
Kolejnym istotnym elementem, przemawiającym za wykorzystywaniem serii PACSystems w nowoczesnych systemach automatyki, jest bezpieczeństwo. Otwartość systemu na integrację z innymi platformami to korzyść niosąca niestety za sobą spore ryzyko cyberataków i zagrożeń wynikających z nieuprawnionego dostępu do urządzenia podłączonego do sieci zewnętrznej. Dlatego wszystkie kontrolery PACSystems zostały zaprojektowane i wyposażone w mechanizmy dbające o wysoki poziom bezpieczeństwa.
System bazuje na Root-of-Trust (RoT), który stanowi fundament dla wszystkich konstrukcji zabezpieczeń. Kontrolery PLC/PAC firmy Emerson wyposażone są w technologię, która pozwala na zbudowanie zaufanego źródła w systemie kryptograficznym. Ponieważ bezpieczeństwo kryptograficzne zależy od wykorzystanych kluczy do szyfrowania i deszyfrowania danych oraz wykonywania funkcji, takich jak generowanie podpisów cyfrowych i weryfikacja podpisów, schematy RoT wykorzystują bezpieczny, dedykowany moduł sprzętowy zainstalowany w kontrolerze PACSystems.
Całe oprogramowanie układowe (firmware) w kontrolerach PACSystems jest podpisane przez Emerson za pomocą klucza prywatnego, co gwarantuje, że tylko oprogramowanie podpisane przez Emerson będzie mogło być wgrane i uruchomione na urządzeniu sterującym. Ponadto aktualizacje dostarczane przez Emerson również są podpisywane w celu weryfikacji przed ich załadowaniem. W kontrolerach PACSystems mamy wbudowane standardowo trzy mechanizmy, które na wysoki poziom bezpieczeństwa mają znaczący wpływ: Trusted Platform Module (TPM), Secure Boot (SB) oraz Trusted Boot (TB).
Trusted Platform Module (TPM) to osobny moduł sprzętowy zainstalowany w kontrolerze PACSystems, wyposażony w dedykowany mikrokontroler, który umożliwia generowanie i przechowywanie kluczy kryptograficznych. Każdy chip TPM ma unikalną i poufną parę kluczy RSA (algorytm Rivesta-Shamira-Adlemana), co umożliwia wykonywanie uwierzytelniania platformy i innych urządzeń sprzętowych. Moduł TPM może być wykorzystywany zarówno do szyfrowania, jak i deszyfrowania, a także do generowania liczb losowych, co praktycznie uniemożliwia odgadnięcie innym systemom wygenerowanej sekwencji kluczującej.
Ta funkcjonalność, w połączeniu z publicznym kluczem serwera, pozwala na utworzenie zaszyfrowanego połączenia między dwoma punktami końcowymi: producentem oraz sprzętem który dostarczył. Moduł TPM wymagany jest obecnie przez Departament Obrony Stanów Zjednoczonych w wielu urządzeń codziennego użytku, takich jak telefony i komputery. Jest też bardzo pożądany w systemach automatyki. Gdy TPM jest wykorzystywany jest w połączeniu z BIOS-em, tworzy Root-of-Trust (RoT). TPM umożliwia także bezpieczne przechowywanie i raportowanie statystyk bezpieczeństwa, które mogą być wykorzystane do losowej walidacji konfiguracji systemu w celu weryfikacji, czy nie zostały wprowadzone żadne nieautoryzowane zmiany.
Secure Boot (SB) wykorzystywany w PACSystems odpowiedzialny jest za weryfikację, czy narzędzie do rozruchu systemu jest podpisane kluczem kryptograficznym autoryzowanym przez Emerson i przechowywane w bazie danych zapisanej w oprogramowaniu firmware. Wykorzystywane jest do kontrolowanego uruchomiania urządzenia i zapobiegania uruchamiania programów nieposiadających podpisów dostawcy.
Ostatnim mechanizmem wbudowanym w kontroler PACSystems jest Trusted Boot (TB). Sprawdza on z kolei cyfrowy podpis systemu operacyjnego, weryfikując tym samym komponenty, używane w procesie rozruchu: pliki i sterowniki rozruchowe. Jeśli plik został zmodyfikowany, mechanizm wykrywa nieautoryzowaną zmianę, a następnie blokuje załadowanie i uruchomienie komponentu. Trusted Boot używa wyłącznie zaufanego oprogramowania podpisanego i certyfikowanego przez producenta, co prowadzi do właściwego zarządzania konfiguracją i aktualizacjami urządzenia.
Dowodem na wysoki poziom bezpieczeństwa kontrolerów PACSystem jest certyfikat Achilles. Jest on stosowany w przypadku systemów sterowania na potrzeby oceny poziomu bezpieczeństwa stosowanego w przemyśle. Ma na celu ocenę i potwierdzenie odporności urządzeń przemysłowych na cyberzagrożenia. Certyfikacja przeprowadzana jest przez niezależne laboratoria badawcze, które oceniają produkty pod kątem bezpieczeństwa i odporności na potencjalny cyberatak. Testy obejmują między innymi różnorodne scenariusze ataków, w tym próby włamania, ataki DoS (Denial of Service) oraz próby wykorzystania podatności systemu.
Certyfikat Achilles ma na celu zapewnienie, że urządzenia przemysłowe spełniają określone standardy bezpieczeństwa, co z kolei przyczynia się do zwiększenia bezpieczeństwa całego systemu przemysłowego, wspierając ochronę przed nieautoryzowanym dostępem, atakami hakerskimi, infekcją złośliwym oprogramowaniem oraz innymi formami ataków, mającymi na celu zakłócenie wykonywania operacji przemysłowych. Dla wielu firm i instytucji działających w sektorze przemysłowym posiadanie certyfikatu Achilles jest istotnym czynnikiem branym pod uwagę przy wyborze i zakupie urządzeń przemysłowych.
Dowiedz się więcej o kontrolerach Emerson PACSystems RX3i.
Kontrolery PACSystems umożliwiają budowanie systemów wysokiej dostępności
Na bezpieczeństwo w przemyśle patrzymy też z innej perspektywy – z punktu widzenia dostępności urządzenia i jego odporności na nieplanowane przestoje spowodowane awariami. Krytyczne obiekty technologiczne – z uwagi na bezpieczeństwo prowadzonego procesu – są często zdublowane (na przykład kompresory odpowiedzialne za dostarczania sprężonego powietrzna na produkcję). Ale jest wiele obiektów technologicznych, których z uwagi na swoją specyfikę zdublować się nie da. Wówczas wysoką dostępność uzyskuje się dublując system sterowania. Platforma PACSystems nadaje się do tego idealnie.
Najprostszy i zarazem najbardziej popularny model redundancji dostępnej we wszystkich rodzinach PACSystems to redundancja medium komunikacyjnego. Natywna obsługa Profinet MRP pozwala łączyć wszystkie urządzenia ze sobą w topologii RING, co zabezpiecza nas przed uszkodzeniem kabla sieciowego oraz daje możliwość serwisu na ruchu dowolnego węzła bez wpływu na pozostałe elementy systemu.
Jeśli obiekt wymaga wysokiej dostępność na wyższym poziomie, możemy wybrać rodzinę PACSystems RX3i, która redundancję może realizować w znacznie szerszym zakresie. Podwojenie zasilaczy systemowych, jednostek centralnych, modułów do synchronizacji danych, modułów i magistral komunikacyjnych podnosi w sposób znaczący dostępność całego systemu, czyniąc go odpornym na wiele różnych awarii, jakie mogą potencjalne wystąpić na obiekcie.
Warte podkreślenia jest to, że układ w takim przypadku działa w układzie gorącej rezerwacji (HotStandby Redundancy) i przełączanie z modułu głównego na zapasowy realizowana jest bezuderzeniowo w czasie pojedynczych milisekund, co nie wprowadza żadnego zakłócenia do sterowanego procesu. Jest to możliwe dzięki dwukrotnej synchronizacji danych pomiędzy kontrolerami w każdym cyklu programu.
W przypadku aplikacji mniejszych i wolnozmiennych można wybrać ekonomiczny model redundancji działający w oparciu o PACSystems CPE400/CPL410. Tam mechanizmy synchronizacji i przełączania działają tak samo, jak w przypadku RX3i, ale sama konstrukcja urządzenia gwarantuje wysoką dostępność na nieco mniejszym poziomie. Programowanie systemu o redundantnej architekturze nie różni się niczym od programowania systemu, w którym redundancji nie ma. Wbudowane w oprogramowanie narzędziowe mechanizmy i wizardy dokonują automatycznej konfiguracji systemu za programistę, co eliminuje możliwość popełnienia błędów i znacząco przyspiesza uruchomienie systemu. Zaletą systemu redundancji zbudowanego w oparciu o PACSystems jest także to, że cały układ jest widoczny w systemach HMI i SCADA pod jednym adresem IP, bez względu na to który z kontrolerów w danej chwili prowadzi proces.
Więcej zasobów dla aplikacji sterujących
Ostatnim bardzo istotnym elementem przemawiającym za stosowaniem PACSystems w nowoczesnych systemach automatyki są jego zasoby. Możliwość obsługi kilku języków programowania i wbudowany kompilator języka C powodują, że PACSystems musi być wyposażony w więcej pamięci programu, niż tradycyjny sterownik PLC. W zależności od rodziny urządzenia kontrolery mają od 0,5 MB do 64 MB pamięci przeznaczonej na program sterujący. To ilość wystarczająca nawet dla najbardziej rozbudowanych algorytmów sterujących.
Wykorzystanie w serii RSTi-EP nowoczesnej pamięci MvRAM pozwala wyeliminować baterię do podtrzymania zawartości pamięci. Tam, gdzie pamięci MvRAM jeszcze nie ma, mamy do dyspozycji moduły Energy PACK, które są odpowiedzialne za automatyczne zrzucenie zawartości pamięci RAM do pamięci Flash. Gwarantują one ponowne uruchomienie kontrolera z takimi samymi danymi, jakie były w pamięci podczas ostatniego cyklu programu.
Programowanie symboliczne bez adresowania konkretnych komórek pamięci czy elastyczność przy przydzielaniu pamięci na obsługę konkretnych zmiennych daje programiście pełną dowolność w wykorzystaniu dostępnych w kontrolerze zasobów. Programowanie na ruchu z możliwością testu i szybkiego powrotu do poprzedniej wersji programu to kolejne elementy poprawiające komfort pracy inżynierów odpowiedzialnych za konfigurację systemu.
Czy warto planować migrację systemów sterowania VersaMax do PACSystems?
Przedstawione powyżej cechy kontrolerów PACSystems mogą zostać wykorzystane w systemach, w których do tej pory pracowały lub wciąż pracują sterowniki PLC VersaMax. Ich bezpośrednim następcą jest seria kontrolerów PACSystems RSTi-EP z jednostkami centralnymi CPE205/210/220/240. Wybór wydaje się prosty w przypadku inwestycji w nowy system sterowania – tam naturalnie powinniśmy inwestować w nowoczesne rozwiązania. Można zadać jednak pytanie, co z istniejącymi i wciąż działającymi systemami, które wykorzystują sterowniki VersaMax?
Jeśli system nie wymaga zaawansowanych możliwości, o których pisaliśmy wcześniej, zapewne nie warto planować modernizacji. Takich obiektów z całą pewnością będzie sporo – nie wszystkie inwestycje da się biznesowo uzasadnić. Jeśli jednak zasobów dostępnych w VersaMax zaczyna brakować, to należy pomyśleć o migracji i zmianie serii.
Migracja może być realizowana w kilku etapach i nie ma konieczności eliminacji całego posiadanego sprzętu. Pracujący sterownik VersaMax można niewielkim kosztem przerobić na układ wejść-wyjść poprzez zamianę jednostki centralnej na interfejs komunikacyjny. Taki węzeł bez najmniejszego problemu podłączymy do dowolnego kontrolera PACSystems w oparciu o Profinet (jeśli w VersaMax zamiast CPU zastosujemy interfejs IC200PNS001 lub IC200PNS002) lub EGD (jeśli w VersaMax zamiast CPU zastosujemy interfejs IC200EBI001).
Tak więc inwestując w jednostką centralną PACSystems RSTi-EP oraz interfejs komunikacyjny możemy w łatwy sposób przerobić system VersaMax na PACSystems. Również program sterujący z VersaMax dla się automatycznie przekonwertować na PACSystsms. Pomaga w tym oprogramowanie narzędziowe PAC Machine Edition, które posiada wbudowane konwertery i narzędzia do walidacji projektu sprawdzające kompatybilność kodu pomiędzy seriami.
Jeśli użytkownikowi zależy na mniejszych gabarytach systemu sterowania, szerokim zakresie temperatur pracy czy rozbudowanej diagnostyce modułów rozszerzeń, wówczas migracja z VersaMax do PACSystems RSTi-EP musi być zrealizowana w pełnym zakresie – a więc wszystkie moduły należy zastąpić nowymi urządzeniami.
Decyzja o migracji systemu sterowania nie może być podyktowana wyłącznie trendami panującymi w automatyce. Musi być poprzedzone analizą potrzeb oraz audytem pracującego systemu. Tylko na tej podstawie da się podjęć decyzję, czy migracja jest uzasadniona technicznie i biznesowo. Jeśli tak jest, koniecznie trzeba przeanalizować posiadaną dokumentację techniczną, sprawdzić co w układzie automatyki pracuje, sprawdzić czy dysponujemy backupami aplikacji sterującej i dokonać analizy algorytmu sterującego – czy do nowego kontrolera powinien być zaimportowany w obecnej postaci czy wymaga wprowadzenia dodatkowych poprawek. Więcej na ten temat napiszemy w kolejnych artykułach.
Sprawdź ofertę kontrolerów Emerson PACSystems RSTi-EP w sklepie internetowym ASTOR.