Analiza predykcyjna: jak skutecznie zapobiegać awariom?
Kontakt w sprawie artykułu: Mateusz Zajchowski - 2023-09-05
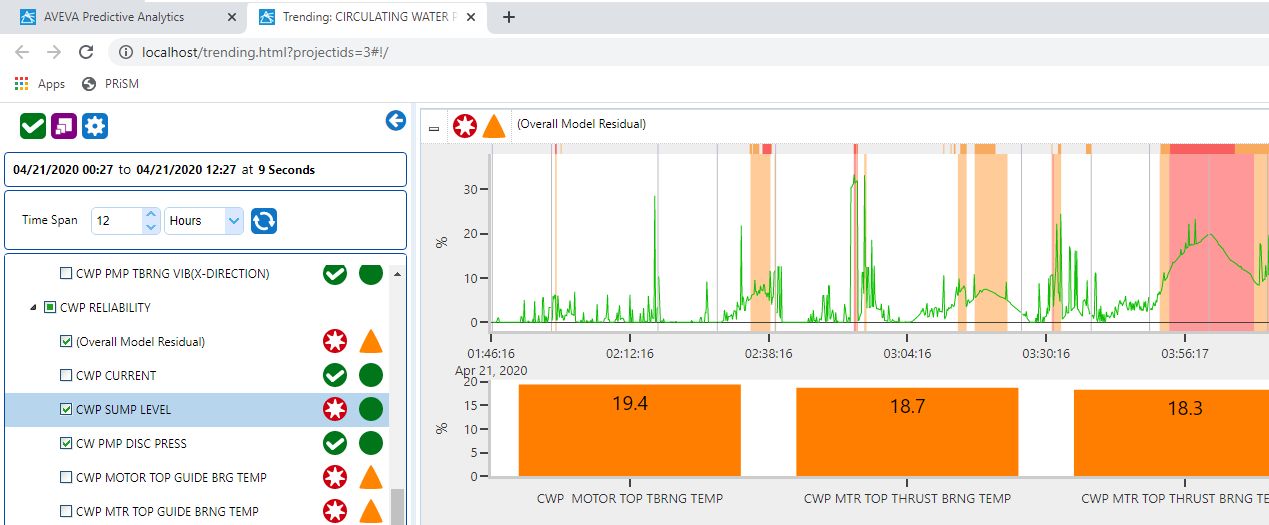
Z tego artykułu dowiesz się:
- czym jest analiza predykcyjna i jak działa,
- jakie korzyści może przynieść,
- jakie możliwości daje AVEVA Predictive Analytics.
Nieplanowane przestoje to jeden z najbardziej dolegliwych problemów, jakie zdarzają się w przemyśle. Z pewnością marzeniem każdego działu utrzymania ruchu jest sytuacja, w której wystarczające jest wykonywanie tylko zaplanowanych przeglądów lub serwisów. Niestety tak nie jest – awarie się zdarzają, a to często wiąże się z dużymi kosztami. Drogie może być samo urządzenie, które uległo awarii, albo też sam przestój generuje poważne straty. Analiza predykcyjna jest odpowiedzią na ten problem.
Na początek przyjrzyjmy się kilku interesującym statystykom związanym z nieplanowanymi przestojami.
Wyzwania związane z nieplanowanymi przestojami
Przede wszystkim z różnych szacunków wynika, że nawet ponad 80% awarii ma charakter losowy. Pozostałe niespełna 20% przypadków awarii jest związane z wiekiem urządzeń. Wiedzę dotyczącą starzenia się urządzeń mogą posiadać np. najbardziej doświadczeni operatorzy i inżynierowie, ale z badań firmy Vanson Bourne wynika, że nawet w dużych i nowoczesnych firmach większość operatorów może nie być świadomych, kiedy wymienić, ulepszyć lub konserwować zasoby.
Jak widać, pracownikom często brakuje wiedzy pozwalającej przewidywać awarie. Kiedy coś się zepsuje, wszyscy koncentrują się na jak najszybszym naprawieniu problemu, a rzadko myślą np. o sporządzeniu właściwej dokumentacji. Inna sprawa, że nawet istnienie takiej dokumentacji nie musi pomagać w zapobieganiu awarii, jeżeli zapowiadające ją symptomy są trudne lub niemożliwe do zauważenia.
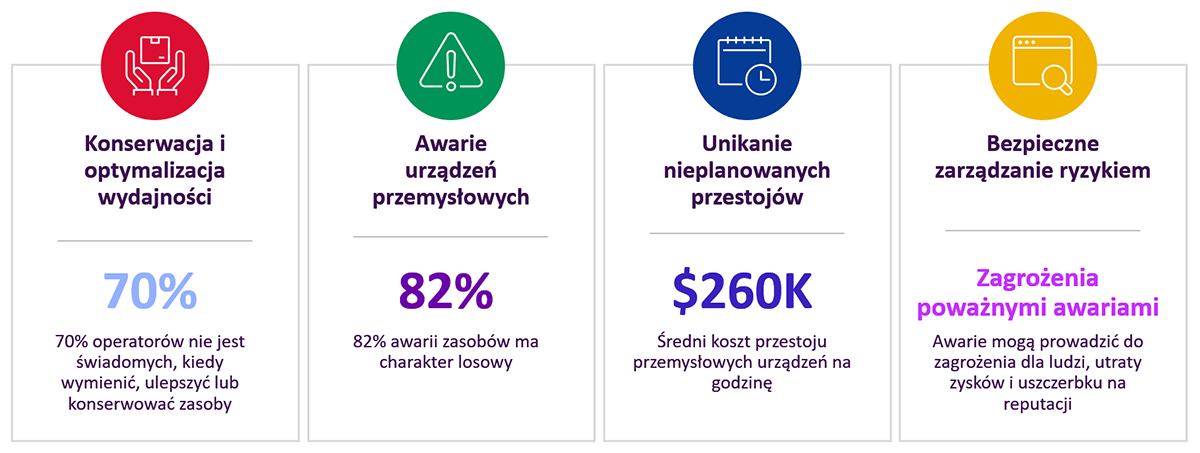
Równie znamienna jest trzecia statystyka ogólnoświatowego przemysłu. Średni koszt jednej godziny nieplanowanego przestoju infrastruktury IT to 260 000 dolarów. Kwota ta robi wrażenie, ale należy pamiętać, że to jest średnia – i dotyczy tylko infrastruktury IT. Zdarza się więc w światowym przemyśle wiele przestojów mniej kosztownych, ale również całkiem sporo takich dużo droższych, gdzie straty mogą sięgać nawet milionów dolarów. To istotne spostrzeżenie, które będzie miało ważny wpływ na planowanie systemu analizy predykcyjnej. Wdrażanie takich systemów warto bowiem zaczynać od tych obszarów, gdzie potencjalne zagrożenie stratami jest najwyższe.
Kończąc przytaczanie statystyk warto wspomnieć też o mniej wymiernych konsekwencjach nieplanowanych przestoju. Poważna awaria może nie tylko skutkować stratami materialnymi, ale być też zagrożeniem bezpieczeństwa dla ludzi lub środowiska. W efekcie może dojść do zdarzeń tragicznych, które dodatkowo będą miały rujnujący wpływ na reputację przedsiębiorstwa i otoczenie.
Predictive maintenance – jak to działa?
Zobaczyliśmy dość jasno, że awarie są nieprzyjemne. Gdyby udało się skutecznie je przewidywać, według różnych szacunków możliwe byłoby ograniczenie kosztów operacyjnych przedsiębiorstw produkcyjnych o 10 do 20%.
W jaki sposób można przewidzieć awarię? Przecież właśnie dowiedzieliśmy się, że jest to zdarzenie, które przytrafia się w sposób losowy. Pozornie właśnie tak jest, ale gdy przyjrzymy się uważniej, dojdziemy do wniosku, że nie do końca. Każda bowiem awaria jest czymś spowodowana, a w praktyce okazuje się, że już wcześniej można dostrzec symptomy, które ją zapowiadają.
Aby dostrzec te symptomy, potrzebujemy właściwych danych, zbieranych z procesu produkcyjnego. Dane takie muszą pochodzić z czujników. Wciąż jeszcze zdarza się, że procesy są słabo opomiarowane, ale najczęściej jednak każda linia produkcyjna wyposażona jest w wiele czujników i sygnałów, które w sposób bezpośredni i pośredni wskazują na to, jak pracuje. Dane zbierane z tych czujników mogą być wyświetlane na stacjach operatorskich, a także trafiać do baz danych, np. AVEVA Historian. W bazie danych zbieramy więc całą historię pomiarów, ze stemplami czasowymi. Tych danych z reguły jest bardzo dużo – zależy to od wielkości systemu, liczby czujników i częstotliwości zbierania danych. Następnie korzystając z odpowiednich narzędzi możemy np. taką historię pomiarów przedstawić na wykresie, takim jak poniżej.
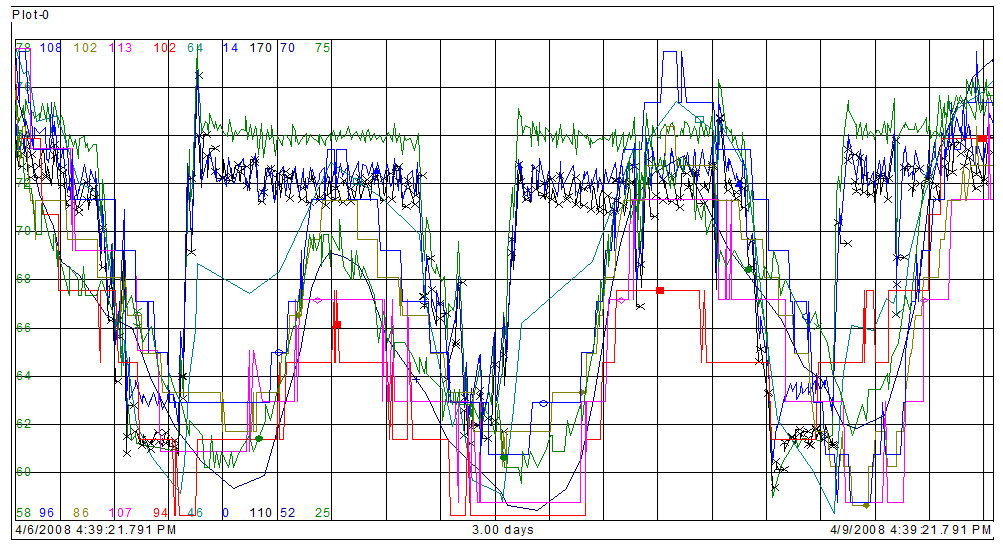
Jak widać… niewiele tu widać, niestety.
Analiza takiego wykresu jest bardzo trudna. Nie sposób zauważyć tu drobnych zmian. Nie da się też „nieuzbrojonym okiem” wykryć jakichkolwiek korelacji między sygnałami – nie widzimy bowiem, czy zmiana jednego z sygnałów wpływa na zmianę drugiego. A pokazany powyżej wykres to przecież i tak stosunkowo mało skomplikowany przykład. Jeżeli mielibyśmy przed sobą wykres jednego lub dwóch pomiarów, to być może – mając odpowiednią wiedzę i doświadczenie – bylibyśmy w stanie coś na nim dostrzec. W większości procesów będziemy mieli zapewne do czynienia z dziesiątkami lub setkami pomiarów.
Monitorowanie sygnałów: podejście tradycyjne
W tradycyjnym podejściu odpowiedzią na ten problem jest system alarmowy. Pozwala on dla każdego pomiaru określić zakres, w którym wartość parametru traktowana jest jako poprawna. W przypadku wyjścia poza ten zakres – zgłaszany jest alarm. Przykładowo, dla czujnika temperatury możemy określić, że prawidłowa wartość temperatury wynosi między 100 a 200 stopni. Gdy wartość pomiaru wyniesie ponad 200 (albo poniżej 100), to generowane będzie najpierw ostrzeżenie, a w przypadku większego przekroczenia – alarm. Z całą pewnością tego rodzaju informacja jest przydatna i może ułatwić reakcję na jakiś problem. Jest to jednak rozwiązanie dalekie od ideału.
Po pierwsze – widzimy tylko, że temperatura jest nieprawidłowa. Nie wiemy, dlaczego. Jeżeli jednocześnie pojawiają się alarmy z innych czujników lub urządzeń, jest dla nas jasne, że rzeczy idą nie najlepiej. Ale nie wiemy, co konkretnie się zepsuło. Co było pierwotną przyczyną, a co skutkiem.
Drugi problem z alarmami jest natomiast taki, że bardzo często… jest już za późno. Jeżeli temperatura TERAZ przekroczyła limit, to prawdopodobnie do awarii doszło już jakiś czas wcześniej – i możemy tylko ratować co się da, np. zatrzymując proces. Innymi słowy, alarm nie pozwala nam uniknąć awarii. Możemy się tylko o niej dowiedzieć.
Dodatkowym problemem przy konfigurowaniu systemu alarmowego może być też samo ustalanie progów dla alarmów, które często są ustalane, kolokwialnie mówiąc, „na oko” – na bazie doświadczenia inżynierów. Nie mogą być ustawione zbyt nisko, bo system byłby zbyt czuły i pojawiałoby się dużo fałszywych alarmów. Ale nie mogą być też ustawione zbyt szeroko, aby nie spowodować realnego zagrożenia.
Dobrym przykładem opisanych wyżej problemów jest wykres przedstawiony poniżej:
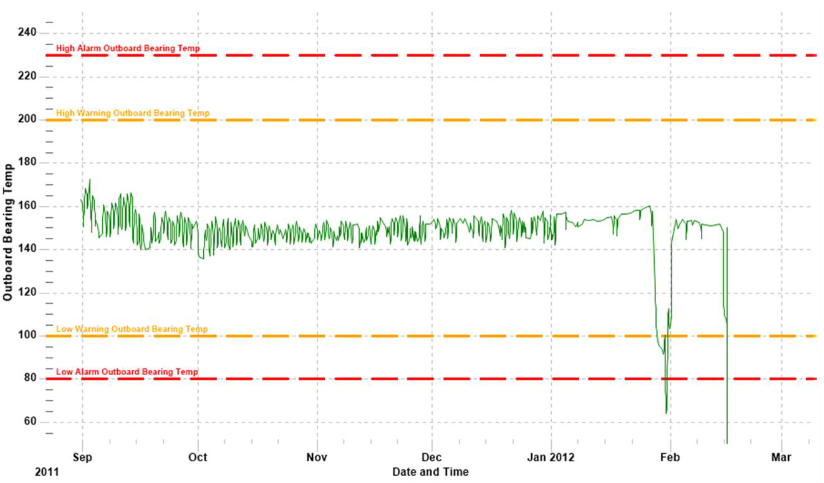
Wykres pokazuje przebieg temperatury z rozdzielczością miesięczną. Widać wyraźnie, że przebieg temperatury wygląda przez wiele miesięcy podobnie. Natomiast na początku stycznia charakter wykresu wyraźnie się zmienia, sygnał zachowuje się zupełnie inaczej. Już tu można się domyślać, że coś jest nie tak – i to przez cały miesiąc. Alarmu jednak nie ma, bo limity nie są przekroczone.
O tym, że z całą pewnością coś jest nie tak, dowiadujemy się dopiero po około miesiącu, gdzie wartość temperatury spada poniżej limitu przyjętego dla alarmów. Wtedy pojawia się alarm, wtedy też – patrząc na wykres – orientujemy się, że przyczyna problemu prawdopodobnie pojawiła się kilka tygodni wcześniej. Nadal jednak nie wiemy, jaka to była konkretnie przyczyna.
Monitorowanie sygnałów: podejście predykcyjne
Podejście predykcyjne różni się radykalnie od tego tradycyjnego, opartego na alarmach. W pewnym uproszczeniu można powiedzieć, że dla każdej maszyny i każdego procesu da się zazwyczaj określić pewien model działania, który moglibyśmy nazwać wzorcowym. To po prostu zapis prawidłowego przebiegu procesu, złożony z szeregu wartości zbieranych pomiarów. Taki model tworzony jest na podstawie zebranych danych historycznych.
Inaczej mówiąc: algorytmy predykcyjne uczą się – na podstawie danych historycznych – przewidywać, jaki powinien być przebieg sygnału. Tym samym zawsze jest wiadome, jaka powinna być wartość tego sygnału w danej chwili – a jaka powinna być w ciągu najbliższych minut, godzin lub dni.
Ten sygnał predykcyjny jest nieustannie porównywany do rzeczywistego przebiegu sygnału. Gdy tylko te dwa przebiegi zaczynają wyglądać inaczej (a więc rzeczywisty sygnał zaczyna odbiegać od modelowego), natychmiast wiemy, że zaczyna się dziać coś złego.
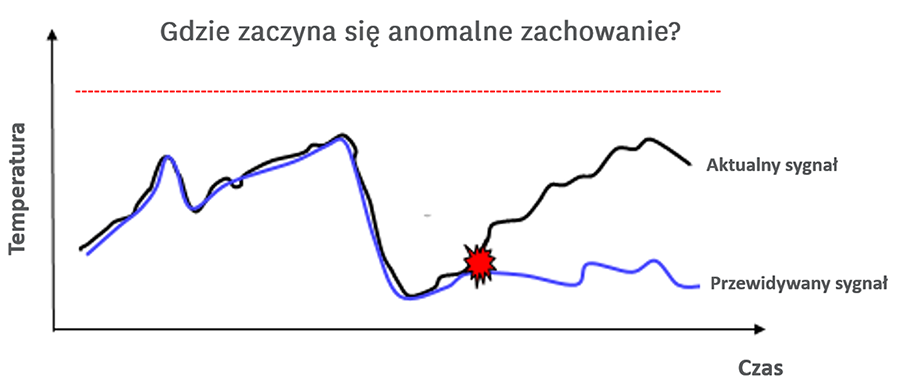
Wracając do naszego przykładowego pomiaru temperatury, algorytm predykcyjny „dostrzegłby” problem już na początku stycznia – bo to właśnie tam przebieg sygnału zaczyna wyglądać zupełnie inaczej. Dzięki temu możemy zareagować natychmiast – tak naprawdę niemal miesiąc przed faktycznym wystąpieniem awarii!
Analiza predykcyjna daje czas na spokojną reakcję
Dzięki analizie predykcyjnej niemal natychmiast wiemy o każdym pojawiającym się problemie. Mamy więc czas, aby zaplanować i przeprowadzić niezbędne działania naprawcze. Możemy np. niezwłocznie wymienić jakieś urządzenie lub część, możemy też podjąć świadomą decyzję o niepodejmowaniu żadnych działań (gdyż np. wiemy, że w krótkim czasie zaplanowany jest przegląd albo serwis maszyny).
Warto tu jeszcze wspomnieć o czułości algorytmu predykcyjnego. Jeżeli badamy odchylenie sygnału rzeczywistego od wzorcowego, możemy zadecydować, jaka będzie dokładność tego badania. Innymi słowy – jak duże odchylenie spowoduje wygenerowanie alarmu. W takim przypadku niewielkie odchylenia nie spowodują alarmu, ale gdy przekroczą określoną skalę – alarm się pojawi.
Mapa kondycji urządzenia
Dzięki algorytmom predykcyjnym możemy zbudować tzw. mapę kondycji urządzenia. Jest to specjalny rodzaj wykresu ilustrujący przebieg monitorowanego sygnału, pokazującego dodatkowo, w których okresach sygnał był nadmiernie odchylony od normy – i jak bardzo. Obszary umiarkowanego odchylenia oznaczane są kolorem żółtym, a tam, gdzie odchylenie było znaczące, pojawia się kolor czerwony.
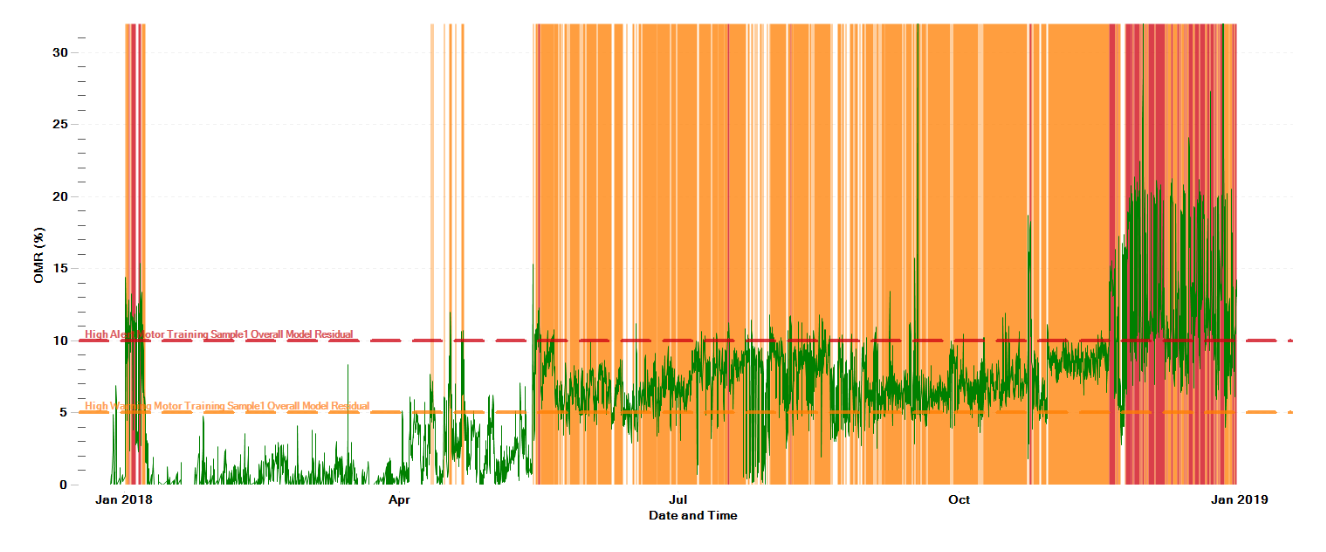
Nie można zapominać, że na całościową kondycję wpływ może mieć np. kilkadziesiąt sygnałów, które opisują pracę danego urządzenia. Nie musimy jednak martwić się tym, jak znaleźć korelacje między tymi sygnałami. Odpowiednie algorytmy zajmą się tym w sposób automatyczny, dzięki czemu otrzymujemy wiodący sygnał, który przyczynił się najbardziej oraz sygnały, które w mniejszym stopniu przyczyniły się do powstania anomalii.
Natomiast w momencie wystąpienia alarmu mamy dostęp do kompletu danych. Algorytm wskazuje nam, które konkretnie sygnały mają największy wpływ na to, że kondycja urządzenia w danej chwili nie jest dobra. Możemy zobaczyć, które parametry i w jakim stopniu wpływały na pojawienie się problemu. Jest to więc narzędzia do tego, aby łatwo odnaleźć główną przyczynę problemów z urządzeniem.
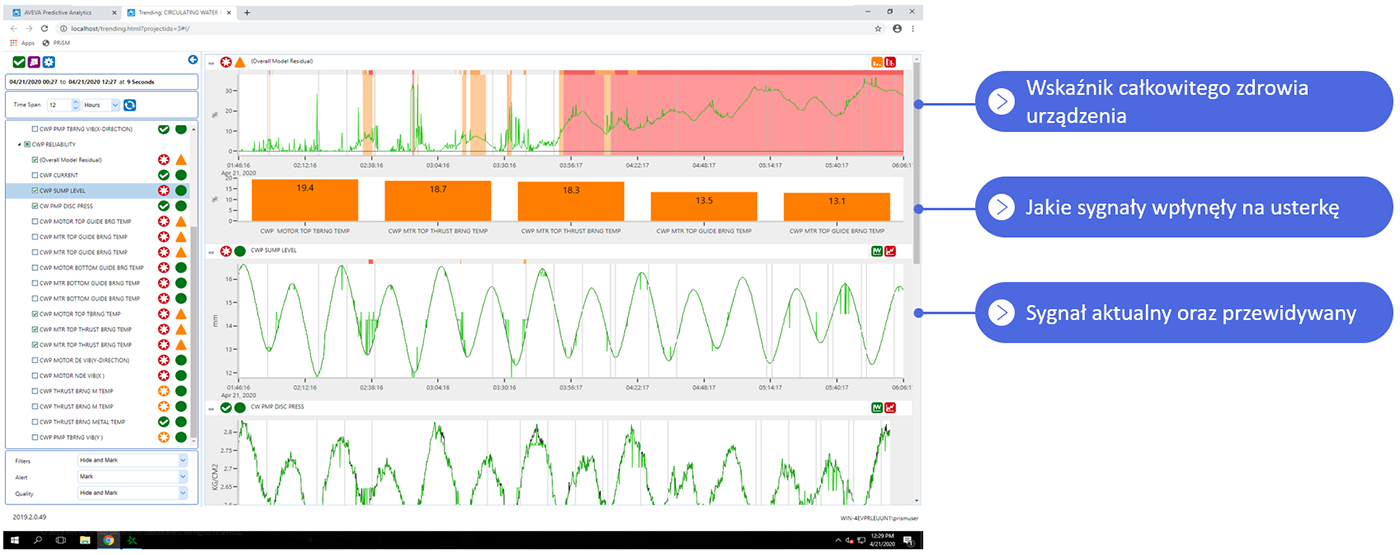
AVEVA Predictive Analytics – analiza predykcyjna w praktyce
Fundamentem wykonywania analiz predykcyjnych jest gromadzenie historycznych pomiarów. Mając dane możemy wykorzystać algorytmy, które pozwalają je analizować i na bieżąco wykrywać pojawiające się anomalie. Aby jednak powstał kompleksowy system pozwalający na zapobieganie awariom, potrzebne jest jeszcze coś. Potrzebujemy narzędzia, które pozwoli przełożyć wiedzę o zagrożeniu awarią na konkretne działania. Potrzebujemy aplikacji, która pomoże rozdystrybuować zadania pomiędzy osobami odpowiedzialnymi za poszczególne obszary, a także ułatwi gromadzenie wiedzy o problemach technicznych i sposobach ich rozwiązywania.
Takim narzędziem jest AVEVA Predictive Analytics, który implementuje cały proces analizy predykcyjnej:
- wykrycie zdarzenia na podstawie analizy odchylenia sygnału rzeczywistego od wzorcowego,
- analiza przyczyn anomalii i wpływu poszczególnych sygnałów na kondycję urządzenia,
- tworzenie zgłoszeń serwisowych,
- rozdysponowanie zadań serwisowych dla pracowników,
- monitorowanie przebiegu akcji serwisowej,
- gromadzenie dokumentacji dokonanych napraw.
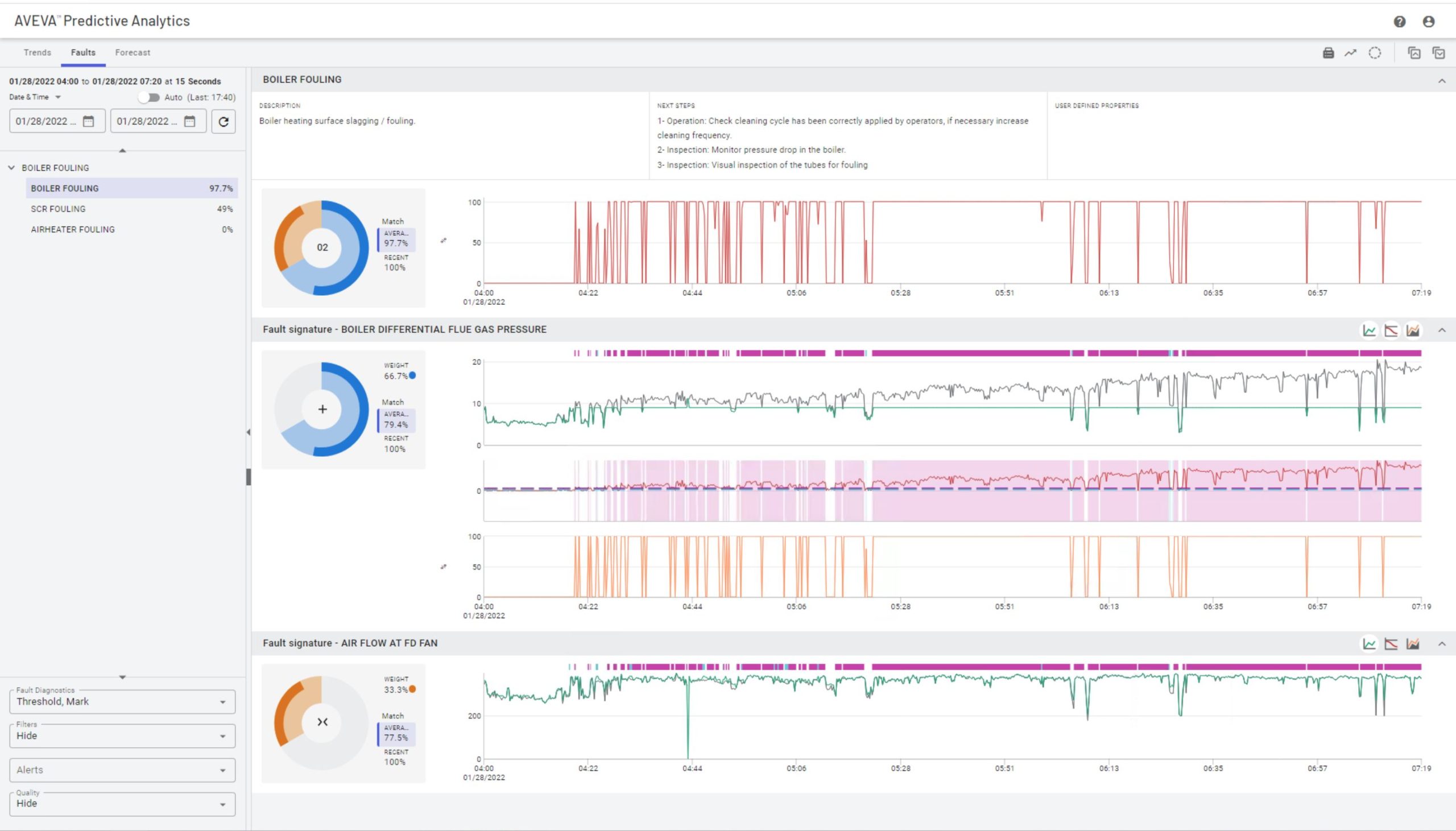
AVEVA Predictive Analytics umożliwia nam śledzenie każdego przypadku krok po kroku, z jednoczesnym budowaniem bazy wiedzy technicznej, zawierającej komplet informacji o awariach, ich przyczynach oraz sposobach ich usunięcia. Taka baza jest bardzo przydatna, jeżeli możliwe jest powtórzenie się podobnych zdarzeń w przyszłości, a także w przypadku, gdy mamy wiele takich samych urządzeń, na których mogą zdarzać się analogiczne awarie.
Dowiedz się więcej o zastosowaniach sztucznej inteligencji w przemyśle.
Autorzy: Bartłomiej Hebda, Mateusz Zajchowski
Redaktor tekstu: Mateusz Pierzchała