Wywiady
Z Krakowa w świat – o rozwoju polskiej myśli inżynierskiej i współpracy Control-Service i ASTOR
Z Krakowa w świat – o rozwoju polskiej myśli inżynierskiej i współpracy Control-Service i ASTOR
Control-Service i krótka historia o tym, jak systemy produkcji wsadowej z symulatorami procesów pomagają spełniać najbardziej nietypowe potrzeby.
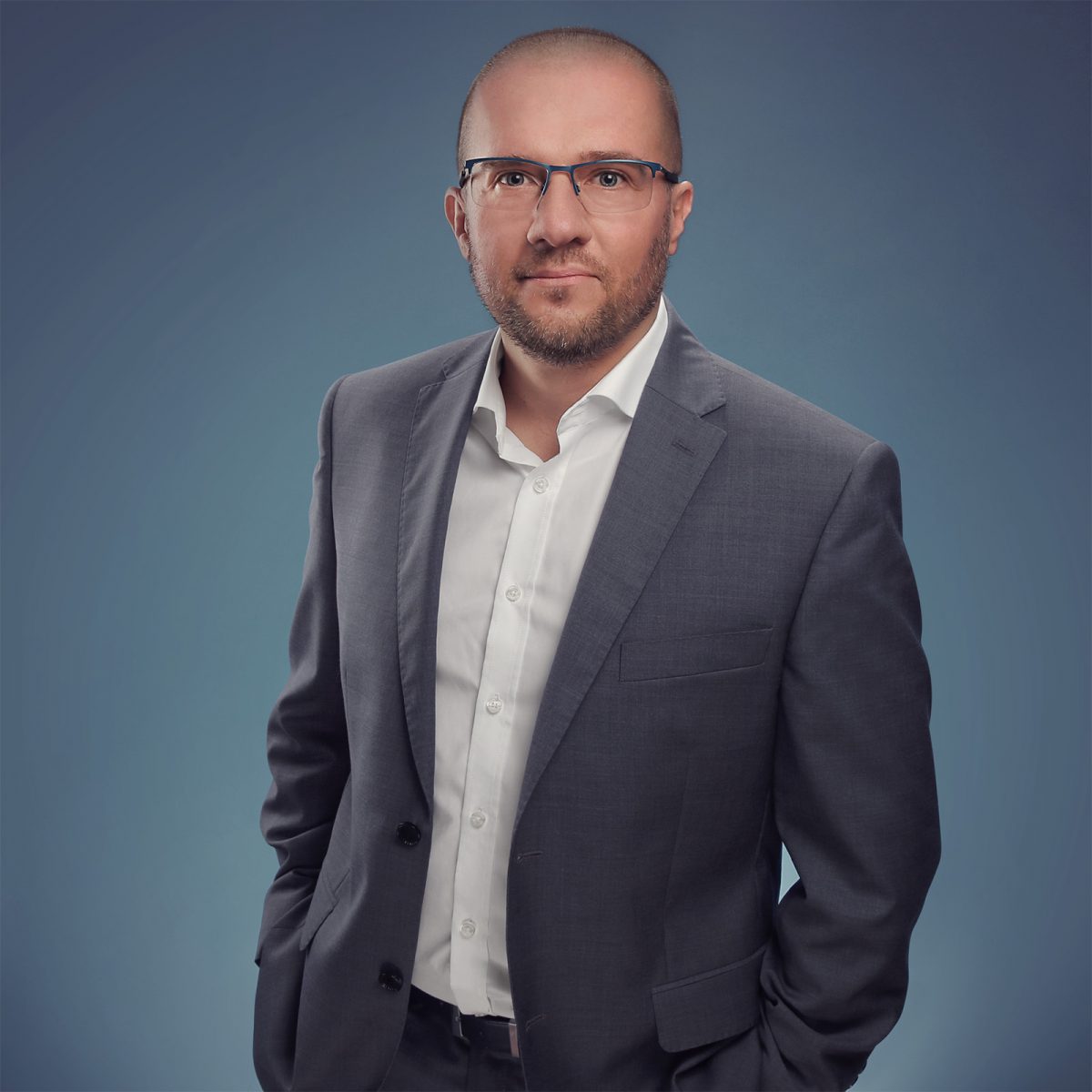
„Wyobraź sobie, że ogarnęła Cię nagła i niecierpiąca zwłoki potrzeba kupienia nowych butów. Bezskutecznie przeglądasz oferty sklepów internetowych w poszukiwaniu takich, które choć trochę byłyby podobne do tych, których obraz w Twojej głowie uporczywie Cię prześladuje. W końcu trafiasz na sklep, który ma możliwość wyboru koloru, kształtu i wysokości obcasa. Konfigurujesz idealne buty i wysyłasz zamówienie. Ze sklepu internetowego trafia ono do nadrzędnego systemu zarządzania zakładem produkcyjnym, a następnie…”
o tym, jak dalej przebiega proces i innych możliwościach, jakie dają symulatory procesów (coraz częściej znane także jako Digital Twin), Renata Poreda rozmawia z Jaromirem Turlejem, prezesem i właścicielem krakowskiej firmy integratorskiej Control-Service.
Polska myśl inżynierska idzie w świat!
Renata Poreda, ASTOR: Polska myśl inżynierska w dobie globalnej rewolucji przemysłowej. To brzmi dumnie?
Jaromir Turlej, Control-Service: Biorąc pod uwagę działania naszej firmy i wiedzę ekspercką naszych inżynierów integratorów, to zdecydowanie tak. Realizujemy projekty w międzynarodowych zespołach, których członkami są ludzie z USA, Meksyku, Wielkiej Brytanii i Polski oczywiście. Dostarczamy rozwiązania dla dużych korporacji. Mamy za sobą zakończony sukcesem projekt w USA, prowadzimy negocjacje w sprawie dostawy dwóch dużych systemów sterowania w Rosji.
Ogromną satysfakcję dają nam również wszystkie te projekty, które realizujemy lokalnie w małych i średnich firmach. Coraz częściej widzimy, że nasze rodzime firmy chcą się automatyzować, bo dzięki temu mogą odpowiadać na szybko zmieniające się potrzeby konsumentów. Produkcja to dzisiaj duże wyzwanie. Porównam to do perspektywy natychmiastowej korekty palety barw farb w zależności od szybko zmieniających się trendów w wykańczaniu mieszkań i domów. Podobnie atrakcyjna wydaje się możliwość szybkiej zmiany smaku napojów lub ketchupu, błyskawiczne tworzenie nowych sosów, jogurtów, szamponów itp.
RP: Brzmi niewiarygodnie?
JT: Prawda? Ale tylko dla nie-specjalistów. Dzięki tzw. systemom produkcji wsadowej zmiana smaku, czy koloru całej serii produkcyjnej możliwa jest niemal natychmiast. Możliwe jest szybkie tworzenie produktów oraz ich łatwe modyfikowanie przez wprowadzanie korekt w recepturach. Co ważne, zmiany w nich wprowadza technolog bez udziału programistów.
Systemy produkcji wsadowej sprawdzają się wszędzie tam, gdzie mamy do czynienia z mieszaniem i obróbką termiczną, ciśnieniową czy chemiczną wielu składników, celem uzyskania gotowego produktu. Idealnie nadają się do przemysłu chemicznego, farmaceutycznego, spożywczego. Zaletą produkcji wsadowej jest to, że system sam dba o zasoby, czyli dostępność urządzeń i surowców potrzebnych do produkcji.
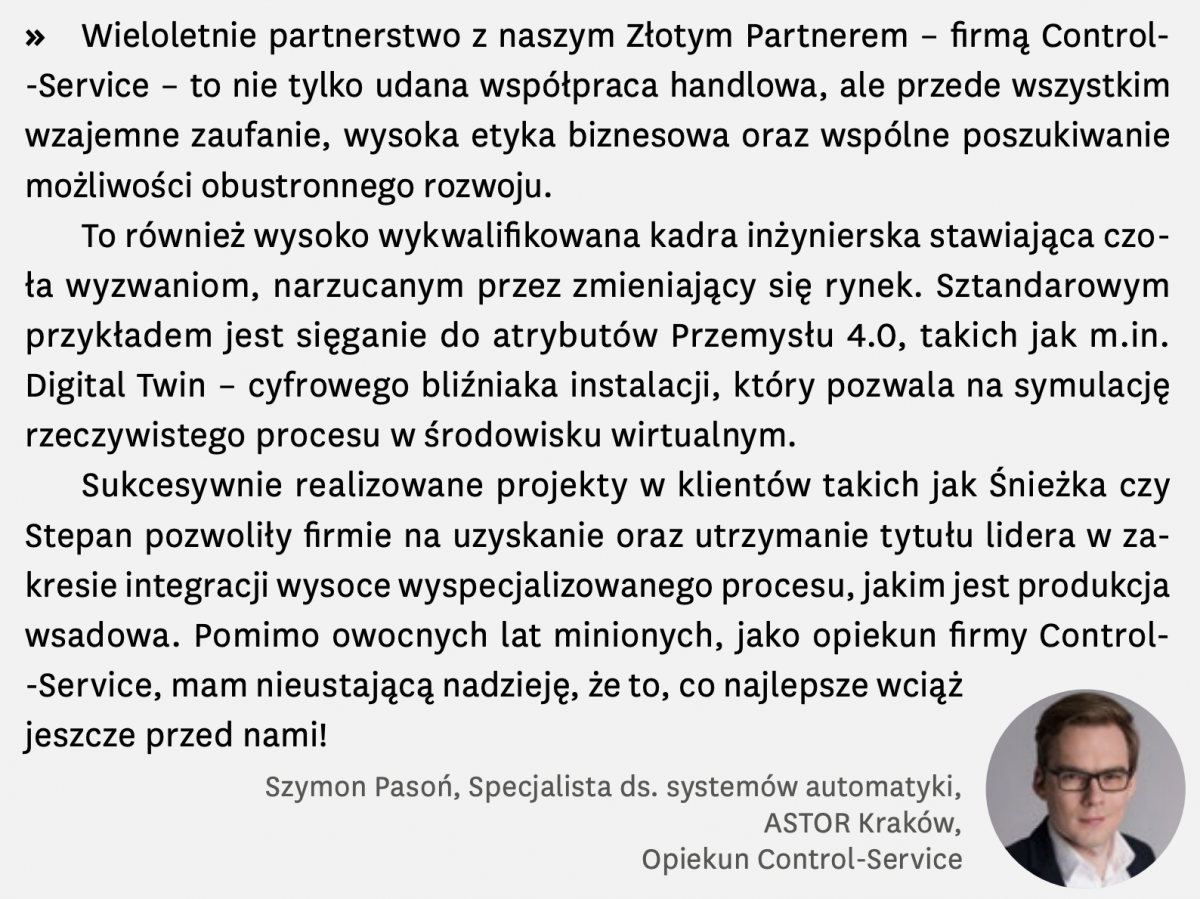
Jak działają systemy produkcji wsadowej?
RP: A jak to wygląda w szczególe? Jak taki proces może przebiegać od A do Z?
JT: Wyobraź sobie, że ogarnęła Cię nagła i niecierpiąca zwłoki potrzeba kupienia nowych butów. Bezskutecznie przeglądasz oferty sklepów internetowych w poszukiwaniu takich, które choć trochę byłyby podobne do tych, których obraz w Twojej głowie uporczywie Cię prześladuje.
W końcu trafiasz na sklep, który posiada możliwość wyboru koloru, kształtu i wysokości obcasa. Konfigurujesz idealne buty i wysyłasz zamówienie. Ze sklepu internetowego trafia ono do nadrzędnego systemu zarządzania zakładu produkcyjnego, a potem do systemu zarządzania procesem produkcyjnym, który bada dostępność potrzebnych składników, a jeśli ich brak, generuje zamówienie do dostawcy np. nietypowego koloru farby, którego akurat nie ma w magazynie czy oryginalnego kształtu obcasa.
System dostaje informację zwrotną od dostawców, kiedy wyślą potrzebne komponenty. Wylicza na podstawie tych informacji i ilości zamówień, kiedy będzie w stanie wyprodukować buty, a Ty dostajesz informację mailem lub sms-em o terminie spodziewanej dostawy towaru. Podczas produkcji poszczególne maszyny odpowiedzialne za wyprodukowanie butów komunikują się z systemem sterowania produkcją, informując o ewentualnych stanach awaryjnych, a system bierze to pod uwagę przy kierowaniu do nich zleceń produkcyjnych, pomijając te wymagające naprawy lub przeglądu.
Oczywiście w sytuacji poważnej awarii i przestoju, skutkującego zmianami w planach produkcyjnych, automatycznie generowana jest informacja na Twojego maila o wydłużeniu terminów dostaw wraz z przeprosinami. Gdy już otrzymasz upragnioną paczkę z butami, informacja od firmy kurierskiej dociera do producenta i automatycznie po 3 dniach otrzymujesz ankietę z badaniem satysfakcji klienta z jakości obsługi i produktu oraz podziękowaniem za dokonany zakup. Twoja odpowiedź dotrze do działów kontroli jakości, marketingu, sprzedaży. Po analizie danych z tysięcy takich ankiet, algorytm oparty na AI wygeneruje raporty, z których parametry posłużą do doskonalenia produktów i usług.

W świecie Industry 4.0 (Przemysłu 4.0) dopiero tu pojawia się człowiek. Oczywiście wszystkie dane są dostępne i zintegrowane we wspólnej dla wszystkich systemów danego zakładu bazie danych. Dzięki temu możemy w łatwy sposób generować dopasowane do naszych aktualnych potrzeb raporty. Wszystkie istotne dane posiadają tworzącą się automatycznie kopię bezpieczeństwa w chmurze, a lokalne serwery są zwirtualizowane celem ich szybkiego ożywienia w przypadku awarii.
Cały proces produkcyjny Twoich butów można wcześniej przetestować w środowisku wirtualnym, ponieważ system oczywiście ma cyfrowego bliźniaka.
RP: Istna rewolucja! W moim odczuciu to idealny proces wpisujący się w ideę Przemysłu 4.0.
JT: Tak. Mamy poczucie, że realizowane przez nas projekty jak najbardziej wpisują się w założenia Przemysłu 4.0. Rozwiązania z zakresu sterowania procesami produkcyjnymi, które dostarczamy, integrujemy z systemami nadrzędnymi, np. SAP. Dzięki temu zlecenia produkcyjne do naszego systemu wędrują często wprost z działów realizacji zamówień.
Dostępność składników potrzebnych do produkcji jest kontrolowana automatycznie, a w przypadku ich braku lub niedostarczonej ilości, rozpoczęcie produkcji jest niemożliwe i generowana jest informacja o konieczności zamówienia składników. Każdy dostarczany przez nas system produkcji wsadowej posiada symulator procesu produkcyjnego, dzięki któremu można w środowisku wirtualnym sprawdzać poprawność jego działania przed wdrożeniem na obiekcie, testować nowe rozwiązania czy szkolić operatorów.
Przemysł 4.0 w służbie rozwoju firmy produkcyjnej
RP: Tutaj dochodzi kolejny ważny aspekt. Technologie 4.0 dają rozwój. Czy tak jest także w Waszym przypadku?
JT: Każdy taki projekt to możliwość rozwoju. Dla Control-Service najbardziej rozwojowym projektem był system sterowania recepturowego reaktorami chemicznymi wraz z symulatorem procesu technologicznego zrealizowany dla firmy Stepan z USA. To korporacja posiadająca wiele fabryk na całym świecie, zajmująca się między innymi tworzeniem ekstraktu dla Coca-Coli, substancji czynnych dla producentów proszków czy składników do produkcji pianek dla sektora automotive.
Wspólnie z inżynierami procesowymi i technologami z firmy Stepan tworzyliśmy przez ponad rok system, który miał być wzorcowy dla innych oddziałów firmy. W projekcie brali udział specjaliści z USA, Meksyku, Wielkiej Brytanii i polskiego oddziału firmy Stepan. Pozwoliło nam to nabrać doświadczenia w pracy w międzynarodowym zespole, a przede wszystkim zdobyć wiedzę technologiczną, potrzebną do tworzenia tego typu systemów.

Efektem owocnej współpracy na lokalnym rynku był realizowany przez nas projekt w USA, gdzie zostaliśmy zatrudnieni przez firmę Stepan w roli superwizora dla lokalnego integratora systemów. Ta współpraca trwa nieprzerwanie od 2015 roku.
RP: To chyba nie jedyny projekt wykraczający poza granice nie tylko Krakowa, Małopolski, ale i naszego kraju?
JT: To prawda, bo kolejnym projektem, który rozpoczął owocną współpracę z międzynarodową korporacją, był projekt systemu sterowania produkcją wsadową wyposażony w symulator procesów technologicznych, wykonany dla korporacji produkującej materiały wykończeniowe wnętrz, m.in. panele podłogowe.
Dzięki posiadanej wiedzy i doświadczeniu z zakresu sterowania reaktorami chemicznymi, wykonaliśmy system sterowania, przekonując inwestora do wprowadzenia szeregu naszych autorskich rozwiązań. Ten system okazał się być lepszy od dotychczas posiadanych przez korporację, na których pierwotnie mieliśmy się wzorować. Znalazło to uznanie inwestora i zaowocowało kolejnym projektem. W tej chwili trwają rozmowy dotyczące realizacji dwóch projektów sterowania fabrykami tego inwestora w Rosji.
RP: A Śnieżka SA?
JT: Podobnie. Tylko nasza współpraca trwa jeszcze dłużej, bo już od ośmiu lat działamy w zakresie automatyzacji recepturowych procesów produkcyjnych z naszym rodzimym producentem farb i lakierów, dzielnie zdobywającym zagraniczne rynki. W ciągu ostatnich kilku lat, dzięki m.in. automatyzacji produkcji, a co za tym idzie – poprawie jakości wytwarzanych produktów, z lokalnego dostawcy Śnieżka S.A. stała się jednym z poważniejszych graczy na arenie międzynarodowej. W tej chwili jest 22 dostawcą farb i lakierów w Europie.
Pierwszy system recepturowy zbudowaliśmy dla tej firmy w 2013 roku w fabryce w Brzeźnicy. Od tego czasu stworzyliśmy kilka tego typu systemów w dwóch kolejnych fabrykach w Polsce. Zaczynamy współpracę także za granicą. Zrealizowaliśmy wspólnie już pierwsze projekty na Węgrzech w lokalnym zakładzie produkcyjnym Śnieżka S.A.
Sekrety udanych wdrożeń w przemyśle 4.0
RP: Co według Ciebie jest wyznacznikiem tego, że wdrożenie będzie udane?
JT: Niezwykle istotne jest staranne opracowanie koncepcji rozwiązania. Do tego potrzebny jest bardzo dobry kontakt z Klientem. Zrozumienie i chęć wyjścia naprzeciw potrzebom inwestora oraz otwartość na zmiany i nowe rozwiązania to moim zdaniem podstawa każdego projektu zakończonego sukcesem.
Forsowane przez nas zmiany w dotychczasowych rozwiązaniach naszych klientów później stawały się u niego standardem w budowie następnych systemów. Ciekawe rozwiązania spotykane na obiektach u Klientów, zmieniały niejednokrotnie nasz punkt widzenia i przyczyniały się do rozwoju umiejętności programistycznych czy projektowych.
No i wreszcie na koniec – najważniejsze. Po obydwu stronach (inwestora i dostawcy rozwiązań) muszą znaleźć się dobrze zmotywowani, otwarci na współpracę ludzie, dla których praca to pasja – robią dokładnie to, co chcą robić, a dążenie do doskonałości w tym, co robią, to ich codzienność.
RP: Sporo już powiedziałeś o projektach zewnętrznych, dla innych. A Twój własny projekt? Czy zawsze marzyłeś o swojej firmie?

JT: Zacząłem myśleć o tym na praktykach po trzecim roku studiów. W trakcie rozmów z pracownikami działu UR dowiedziałem się, że mają problem z serwisowaniem przetwornic częstotliwości. Miałem wtedy pomysł, żeby w porozumieniu z producentem otworzyć lokalny serwis. Skończyłem studia, poszedłem do pracy, gdzie nawet wdrożyłem ten pomysł w życie i po pół roku już wiedziałem, czego chcę
Chciałem stworzyć firmę zajmującą się, zgodnie z moim wykształceniem, automatyzacją procesów technologicznych, będącą przyjaznym środowiskiem pracy dla ludzi, którzy chcą się rozwijać, lubią to, co robią i dlatego są w tym dobrzy, mają wysoki poziom motywacji, najwyższej klasy narzędzia, a odbiorcami produktów i usług są klienci, dla których istotny jest stosunek jakości do ceny, użyteczność i innowacyjność rozwiązań, a nie sama cena. Szczęśliwie udało mi się przyciągnąć do siebie ludzi, z którymi budowanie i rozwijanie firmy to czysta przyjemność.
RP: Skąd nazwa Control-Service?
JT: Tworząc nazwę zależało mi na tym, żeby kojarzyła się z usługami dotyczącymi systemów sterowania, a równocześnie, zgodnie z polskimi skojarzeniami dotyczącymi słowa „service”, zwracała szczególną uwagę na rolę posprzedażowej obsługi klienta w misji firmy. Dodatkowo, zakładając w przyszłości możliwość ewentualnego eksportu, dobrze żeby nazwa była zrozumiała również za granicą. I tak powstał Control-Service.
Współpraca Control-Service i ASTOR
RP: Pytanie, które zostawiłam na koniec dotyczy historii współpracy z ASTOR. Od czego się zaczęła, jaki był pierwszy wspólny projekt, co daje Ci ta współpraca i tytuł Złotego Partnera ASTOR?
JT: Intensywną współpracę zaczęliśmy w 2013 roku przy okazji realizacji projektu dla wspomnianej wyżej Śnieżki SA. Stawialiśmy wtedy pierwsze kroki w zakresie budowy systemów produkcji wsadowej. Wasze kompleksowe wsparcie techniczne, wysoki poziom wiedzy w zakresie oferowanych produktów, gotowość do pomocy i cierpliwość są nie do przecenienia.
Jeżeli zaczynasz pracę z tak złożonym produktem jak Platforma Systemowa AVEVA (dawniej Wonderware), użytym do wykonania oprogramowania sterującego procesem produkcyjnym całego zakładu, niezwykle istotne jest kompetentne wsparcie techniczne oferowane przez dostawcę.
Oczywiście nasza współpraca ciągle ewoluuje. Po ośmiu latach ciągłej pracy z Platformą Systemową AVEVA (dawniej Wonderware), zdanych międzynarodowych egzaminach, potwierdzających nasze kompetencje, kilkudziesięciu zrealizowanych projektach, posiadamy już wiedzę i doświadczenie, dzięki czemu już rzadziej potrzebujemy wsparcia technicznego.
Dlatego też ostatnio nasza współpraca koncentruje się bardziej na wspólnych działaniach marketingowych i sprzedażowych. Wspólne wizyty u klientów, organizacja konferencji, eventów, współpraca przy tworzeniu koncepcji, wymiana referencji, sprawiają, że synergia wynikająca z tego typu działań jest coraz bardziej widoczna w ilości nowych projektów do realizacji. Dlatego też w tej chwili to ten rodzaj współpracy z ASTOR jest dla nas najbardziej cenny.
Z dostawcy produktów i narzędzi programistycznych, oferującego świetne wsparcie techniczne, staliście się dla nas niezwykle istotnym partnerem biznesowym, wspólnie z którym chcemy kontynuować owocną współpracę, przyczyniającą się do rozwoju naszych firm.
RP: Dziękuję za rozmowę.
Rozmawiała Renata Poreda
Menedżer ds. komunikacji i PR, ASTOR
