Treści
Wózki AGV czy roboty AMR? Tramwaj i autobus intralogistyki
Wózki AGV czy roboty AMR? Tramwaj i autobus intralogistyki
Przewozić towary po stałej trasie czy może zmienianej dynamicznie, w zależności od zapotrzebowania? To dylemat, przed jakim stają menedżerowie produkcji i osoby zarządzające centrami logistycznymi, które muszą wybrać między automatycznymi wózkami transportowymi typu AGV a robotami AMR. Co warto wiedzieć o obu tych rozwiązaniach? Jakie są zalety i wady każdego z nich?
Współczesne miasta nie mogłyby obejść się bez transportu publicznego. Bardzo często wśród miejskich pojazdów są zarówno te, które poruszają się po stałej trasie (tramwaj, metro czy pociąg) oraz te, które mogą ją zmieniać, elastycznie dostosowując się do sytuacji na drodze, omijając przeszkody, korzystając z objazdów i docierając do dzielnic położonych poza głównymi szlakami komunikacyjnymi (autobus, bus). Podobnie jest w intralogistyce, czyli transporcie towarów wewnątrz hal magazynowych czy fabrycznych. Tu także czasem sprawdzają się wózki, które mają z góry wyznaczoną trasę niczym tramwaje, a z kolei w innych przypadkach skuteczniejsze są roboty transportowe, które w sposób elastyczny wybierają drogę z punktu A do punktu B, dostosowując się do warunków otoczenia, omijając przeszkody i innych uczestników ruchu niczym autobusy na ulicach.
Oba rozwiązania nie potrzebują operatora. W tym miejscu urywa się zatem analogia z tramwajami i autobusami, które wciąż (choć może już niedługo to się zmieni) potrzebują kierowcy czy motorniczego. Oba mobilne rozwiązania intralogistyczne są jednak we współczesnych halach magazynowych i produkcyjnych równie potrzebne i komplementarnie stosowane, co tramwaje i autobusy w warunkach miejskich. Podobieństw jest zresztą więcej.
Czym AGV różni się od AMR?
W miastach krajów uprzemysłowionych pierwsze tramwaje pojawiły się na początku XIX wieku. Pierwsze autobusy dopiero w latach 80. i 90. dziewiętnastego stulecia. Jeśli chodzi o wózki autonomiczne w intralogistyce, również przez długi czas dominowały takie, które jak tramwaje poruszały się po wyznaczonej trasie. Pojazdy te określane są mianem AGV (Automated Guided Vehicle). Ścieżka, po której jeżdżą może być wyznaczana na wiele sposobów: przez szynę, pętlę indukcyjną czy nawet taśmę naklejoną na podłodze.
Pojawienie się miejskich autobusów wymagało czasu i postępu technologicznego. Podobnie było z robotami, które wkroczyły do magazynów i hal produkcyjnych jako uzupełnienie i rozwinięcie technologii AGV. Owe roboty, oznaczane skrótem AMR (Autonomous Mobile Robot), to także wózki transportowe, jednak wyposażone w kamery, lasery, radary, lidary, kamery podczerwieni i wiele innych czujników, które monitorują otoczenie. Inteligentne oprogramowanie pozwala im interpretować sygnały płynące z zewnątrz i na bieżąco dobierać trasę tak, by omijać przeszkody oraz ludzi pracujących w magazynie i bezpiecznie dojechać do punktu docelowego z towarem.
Kiedy sprawdza się wózek AGV, a kiedy robot AMR?
Wybór konkretnego rozwiązania zależy często od tego, w jakim środowisku dany wózek ma pracować oraz jak ma wpisywać się w profil zakładu i ogólną koncepcję intralogistyczną.
Generalnie można jednak przyjąć zasadę, że w sytuacji, gdy mamy do czynienia z powtarzalnym przewozem dużej ilości towaru, czy to w magazynie, czy w centrum logistycznym, czy w hali produkcyjnej, a procesy, w które ten przewóz się wpisuje są generalnie niezmienne lub są modyfikowane w nieznacznym stopniu, wówczas wózki typu AGV, poruszające się po stałej trasie, będą lepszym rozwiązaniem. Trasy ich poruszania są najczęściej dobrze oznakowane, czasem wydzielone, ale też pracownicy dobrze wiedzą, którędy one przebiegają, w związku z tym ryzyko kolizji czy sytuacji, w której wózek przeszkadza pracownikom w wykonywaniu bieżących zadań, albo musi się zatrzymać, jest niskie.
Jednak obecnie, w czasach, gdy coraz więcej mówi się o personalizacji produkcji wysokoseryjnej i nastawieniu firm produkcyjnych na zaspokojenie potrzeb klienta, wiele przedsiębiorstw stawia na elastyczność i zwinność. Częściej zdarza się, że zakład produkcyjny musi szybko przezbroić linię produkcyjną, by dostosować się do zmieniających się potrzeb rynku, a tym samym musi zadbać o to, by półprodukty czy surowce były dostarczane do tej linii równie dynamicznie. Ponadto w czasach pandemii pojawiły się restrykcje epidemiologiczne, a czasy kryzysu przyniosły niedobory pewnych surowców czy półproduktów, co sprawiło, że wiele firm produkcyjnych musiało elastycznie reagować na błyskawicznie zmieniające się okoliczności. W takich warunkach lepszym rozwiązaniem będą roboty AMR. Ich przystosowanie do nowych okoliczności czy nowego zadania wymaga znacznie mniej czasu niż w przypadku klasycznego wózka AGV. Trasy, po których się poruszają, są ustalane na bieżąco, a punkty, do których dojeżdżają, mogą być szybko dodawane, usuwane lub modyfikowane.
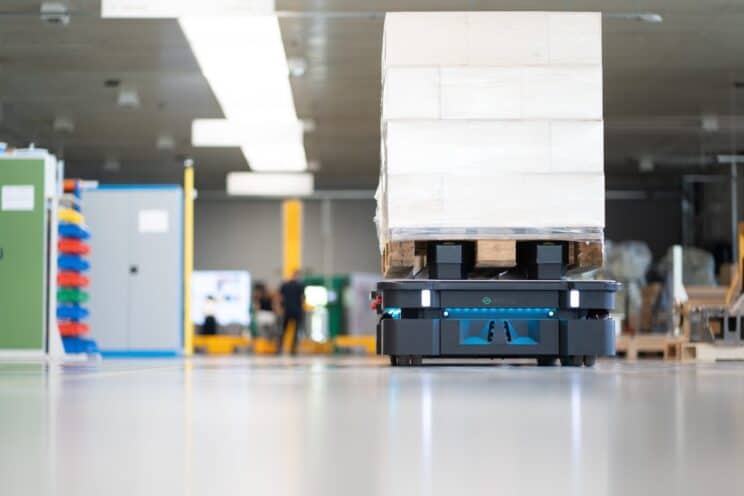
Które urządzenie gwarantuje lepsze parametry pracy?
W przypadku urządzeń transportowych ważną kategorią jest ich udźwig. Im większy ładunek może być przewieziony za jednym razem, tym mniej kursów i większe oszczędności czasu i energii. Historycznie wózki AGV miały większy udźwig niż roboty AMR. Obecnie nowsze wersje tych ostatnich mogą już konkurować z tradycyjnym rozwiązaniem. Jednak, jeśli chodzi o maksymalny udźwig każdego z systemów wciąż pozostaje pewna różnica. Roboty AMR mogą maksymalnie przewozić 2 tys. kg, a wózki AGV do 5 tys. kg.
Drugi ważny parametr to prędkość jazdy. Teoretycznie jest on porównywalny w przypadku obu rozwiązań. Jednak biorąc pod uwagę fakt, że wózki AGV często poruszają się po wyznaczonych, a nawet wygrodzonych torach sprawia, że praktycznie się nie zatrzymują. Roboty AMR przeciwnie – często pracują wśród ludzi i w czasie pracy zwalniają, zatrzymują się lub omijają przeszkody, co może wpływać na czas transportu. Różnice są jednak niewielkie. W zależności od potrzeb można wybrać odpowiedni wariant mobilnego robota AMR o udźwigu od 100 kg do 1350 kg.
Które rozwiązanie jest tańsze?
W przypadku każdej inwestycji w nowe rozwiązania musi pojawić się refleksja na temat kosztów. Jak ta kwestia wygląda w przypadku wózków AGV i robotów AMR? Nie jest tak oczywista, jak mogłoby się wydawać. Pierwsze z omawianych rozwiązań, wózek AGV, jest zdecydowanie mniej technologicznie zaawansowane, co mogłoby sugerować, że jego wdrożenie jest tańsze. I rzeczywiście wózek AGV jest tańszy od robota AMR. Należy jednak pamiętać o tym, że zakup samego wózka AGV to dopiero początek. Trzeba jeszcze zainwestować w zaprojektowanie i poprowadzenie szlaków, którymi ten wózek będzie się poruszał. Czasem oznacza to przebudowę ścian lub wydzielenie specjalnych pasów ruchu w obrębie zakładów produkcyjnych i taką aranżację przestrzeni, by wózek mógł jeździć swobodnie, co generuje dodatkowe koszty i wpływa na czas uruchomienia wózka. W przypadku robotów AMR ta kwestia zupełnie odpada, ponieważ po krótkim programowaniu są one praktycznie gotowe do akcji.
W rezultacie, paradoksalnie, cena technicznie bardziej zaawansowanego rozwiązania może okazać się niższa niż tego prostszego. Jednak sama cena nie może być jedynym kryterium wyboru. Menedżer produkcji przed podjęciem decyzji musi zawsze oszacować, do jakiego zadania potrzebuje wózka lub robota i na tej podstawie oszacować zwrot z inwestycji. Czasem więc droższa opcja może przynieść więcej korzyści.
AGV a AMR – które rozwiązanie jest bezpieczniejsze?
Oba omawiane rozwiązania charakteryzują się wysokim poziomem bezpieczeństwa. Na pierwszy rzut oka AGV wydaje się bezpieczniejszy, ponieważ jeździ po wydzielonej, jasno oznaczonej trasie, a pracownicy dobrze wiedzą, gdzie się ona znajduje i wręcz podświadomie unikają niebezpieczeństwa. Nawet jeśli na trasie wózka znajdzie się przeszkoda czy człowiek, nie ma ryzyka wypadku, ponieważ specjalne czujniki zatrzymają pojazd, gdy wykryją zagrożenie.
Robot AMR przeznaczony jest do poruszania się wśród ludzi pracujących w zakładzie produkcyjnym czy w magazynie. Najczęściej korzysta z tej samej przestrzeni, co oni. Potencjalnie zagrożenie bezpieczeństwa jest więc większe, ale de facto, ryzyko w przypadku robotów AMR jest minimalne. Właśnie dlatego, że robot korzysta z tej samej przestrzeni co ludzie, bezpieczeństwo jest dla producentów tych urządzeń absolutnym priorytetem. Roboty AMR wyposażone są w skanery laserowe, które nieustannie monitorują obszar urządzenia i są podpięte do osobnego sterownika bezpieczeństwa. Takie rozwiązanie gwarantuje natychmiastowe zatrzymanie się robota w sytuacji zagrożenia. Wsparciem dla skanerów są kamery 3D. Te rozwiązania, w połączeniu z odpowiednimi algorytmami, które analizują płynące z nich dane, sprawiają, że roboty są zgodne z normą ISO 3691-4, mają nadane CE oraz spełniają kategorię bezpieczeństwa PLd3, czyli są po prostu bezpieczne.
Podsumowując, we współczesnych zakładach produkcyjnych czy centrach logistycznych wciąż jest miejsce zarówno dla wózków AGV i robotów AMR. Decydując się na zakup konkretnego rozwiązania raczej nie trzeba obawiać się o bezpieczeństwo. Warto natomiast rozważyć szczegółowe cechy wózka czy robota w kontekście konkretnych zadań i konkretnej lokalizacji. Tutaj często diabeł tkwi w szczegółach.
Ciekawostka
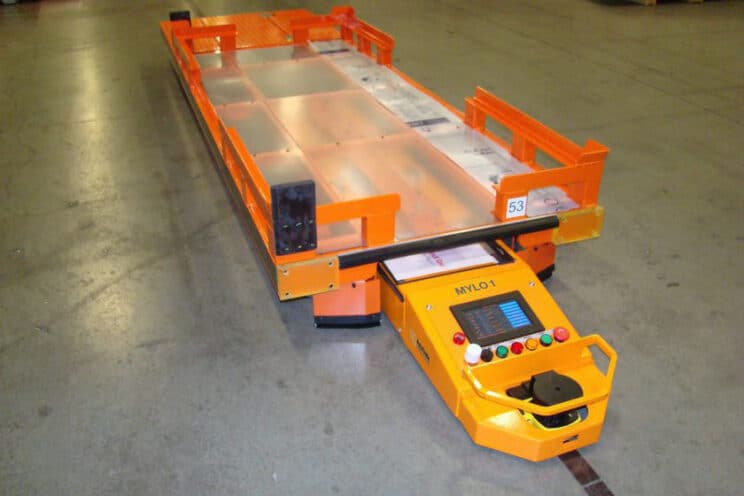
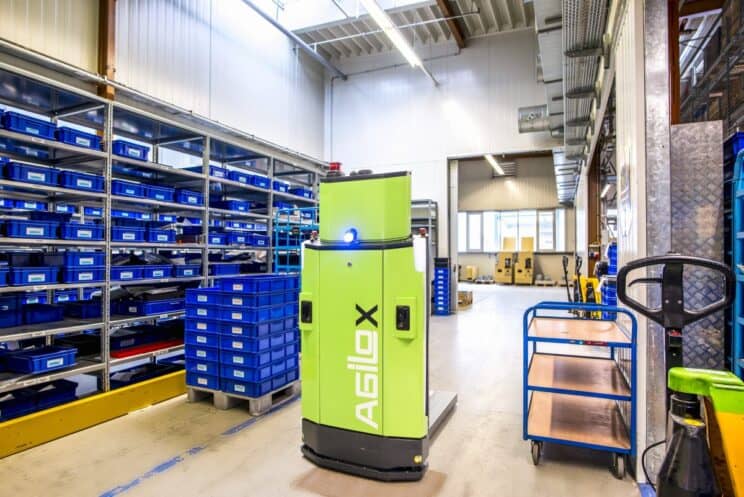
Roboty AMR są rozwinięciem technologii AGV, przez co często i jedne, i drugie pojazdy określa się mianem AGV. Czasem może to ułatwiać komunikację pomiędzy specjalistami w trakcie prac projektowych. Dla laików ta niejednoznaczność pojęciowa może być jednak źródłem konfuzji.
Różne moduły w zależności od potrzeb
Zarówno wózki AGV, jak i roboty AMR mogą funkcjonować jako transportery widłowe bądź platformowe. W pierwszym przypadku wykorzystuje się je do przewozu towaru na paletach. W drugiej opcji dysponują one dodatkowym modułem górnym lub zabudową. Może to być półka, szafka, transporter rolkowy, taśmowy, ramię robota czy dowolny rodzaj zabudowy stworzony na potrzeby konkretnego zadania. Możliwości te dają ogromną elastyczność w realizacji celów zakładu produkcyjnego.