Historie sukcesu
Transformacja cyfrowa sposobem na ratowanie planety – historia sukcesu DOVISTA Polska
Transformacja cyfrowa sposobem na ratowanie planety – historia sukcesu DOVISTA Polska
Zwykle technologię cyfrową i sam Przemysł 4.0 kojarzy się z takimi inwestycjami, jak robotyzacja czy automatyzacja. Jednakże warto na tę kwestię spojrzeć także z innego, czysto humanistycznego punktu widzenia. Mianowicie, jak owa „rewolucja” może wpłynąć na to, co bliskie człowiekowi. Środowisko naturalne, w którym żyje, a którego jest nieodłączną częścią. Na które ma wpływ.
Na czym polega dobry klimat do automatyzacji?
Kwestie klimatu i ochrony środowiska zaczynają na równych zasadach konkurować z tymi twardymi – finansowymi czynnikami oceny wartości inwestycyjnej. Mimo, iż pozornie nie generują oszczędności, ba, potrafią nawet kosztować extra, to jednak warto się nimi zainteresować. W dłuższej perspektywie prowadzą bowiem do wielu skwantyfikowanych korzyści. Jakich?
Kluczowym dylematem, jaki mieliśmy w DOVISTA Polska na początku naszej drogi do „cyfrowości” było, po pierwsze, dostarczenie na stanowiska robocze szczegółowej informacji o produkcie oraz po drugie, jakie operacje obróbcze bądź montażowe potrzeba będzie podjąć, aby uzyskać zamierzony efekt. W wielu firmach mówi się na to „technologia”.
W naszym biznesie, z uwagi na różnorodność produktu oraz skalę przedsięwzięcia, klasyczne podejście do tworzenia technologii nie ma szans się sprawdzić. Dzisiejsze trendy w budownictwie to dążenie do indywidualizmu. Rosnące możliwości produkcyjne oraz poprawa parametrów izolacyjności cieplnej stolarki powodują, iż z dnia na dzień zlecenia klientów są coraz bardziej wymagające.
I co więcej, coraz bardziej zróżnicowane. Przy produkcji około 6000 okien tygodniowo, gdzie wielkość partii produkcyjnej równa się jedna sztuka i każda może być inna, sprawa się komplikuje. Co ważne, nie produkujemy niczego na tak zwany magazyn, więc każde okno ma określonego klienta.
Okno na świat, drzwi do przyszłości
Dla zbudowania pełni obrazu należy poznać także produkt. Okno lub drzwi, w potocznym rozumieniu, nie jest zbyt skomplikowanym produktem. Każdy z nas na co dzień obcuje ze stolarką okienną, zwykle nie zdając sobie sprawy, jak skomplikowanym produktem może ono być. W naszym fabrycznym systemie „okno” opisujemy do 12 000 charakterystyk. Oczywiście, to wszystko ma początek po stronie świadomego klienta i to on w głównej mierze decyduje o kilkuset z nich, takich jak wymiar, kolor, funkcja otwierania etc.
Jednakowoż, aby produkt finalny powstał, potrzebne jest, aby te bazowe informacje, wygenerowane na etapie składania zamówienia sprzedażowego, uzupełnić o dodatkowe parametry, zarówno dla dostawców, jak i produkcji. Ważnym generatorem danych w wielu krajach Europy są także wymagania legislacyjne i środowiskowe, jakie należy dostarczyć w procesie inwestycyjnym. Etapy przerostu danych na poszczególnych etapach tworzenia zlecenia produkcyjnego pokazuje schemat przedstawiony na rys. 1. Na każdym z etapów ilość danych przyrasta w postępie geometrycznym.
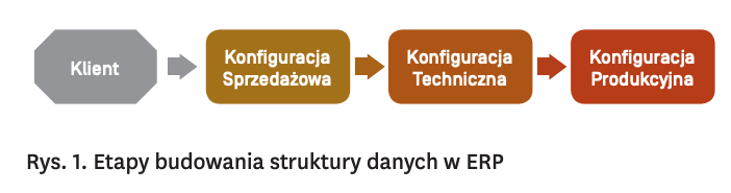
Moje okno na świat – takie, a nie inne
Wyobraźmy sobie wizytę w salonie dealera samochodów. I przyjemny moment wybrania takiego auta, jakiego potrzebuję. Jakiś silnik determinuje odpowiednie skrzynie biegów, a wersje tapicerki są dostępne tylko w określonych wersjach nadwozia. Analogicznie jest w przypadku okien. Konfiguracja sprzedażowa to wspomniane wcześniej dane, jakie „widzi” klient lub jakie wyspecyfikował architekt danej nieruchomości.
W dalszej części tworzona jest konfiguracja techniczna. To także miejsce na eliminację kolizji elementów okna. Ostatni etap to tworzenie detalicznych list komponentów (BOM) oraz dane maszynowe dla urządzeń CNC w celu zrealizowania życzenia klienta. Cały proces na tym etapie odbywa się w pełni automatycznie, bez udziału człowieka.
Okno zbudowane z danych, dzięki umiejętnej analizie inżynierów
Konfigurator na bazie przygotowanych reguł konfiguracyjnych oraz walidacyjnych generuje oraz weryfikuje dane. Tak przygotowana paczka informacji zostaje wyeksportowana do sytemu MES i od tej pory zadanie jest w rękach zespołu, który jest centrum kompetencji dla łańcucha dostaw DOVISTA.
W ramach kompetencji, jakie dostarczamy do organizacji, znajduje się zarządzanie systemami SAP (ERP) oraz AVEVA (MES). Naszym zadaniem jest wsparcie zakładów w Polsce, Litwie oraz Danii. Zajmujemy się procesami planistycznymi, logistycznymi (zarówno zakupowymi, jak i dystrybucji wyrobów gotowych do centrów logistycznych) oraz produkcyjnymi po stronie zarówno MES jak i ERP. Tak przygotowane dane są hurtownią dla procesu produkcyjnego.
Dwoma kluczowymi zadaniami, jakie stawiane są przed MES w naszej organizacji, są dostarczenie aktualnej informacji w zakresie planu produkcyjnego, jak i dokładnych danych o technologii każdego elementu okna w miejscu jego wytwarzania bądź obróbki. W ramach dostarczania technologii w tym zakresie jest także tworzenie plików z programami dla maszyn CNC. To jednak nie koniec przygotowania danych do produkcji. Na tym etapie dane zgromadzone w bazie danych MES wciąż są „nieużyteczne” dla operatorów. Aby nadać im znaczenie i określoną rolę, połączonymi siłami, DOVISTA i ASTOR, stworzyliśmy zestaw aplikacji WEB-owych wspierających założone cele.
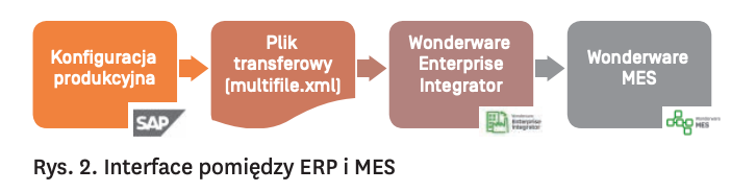
1. DOVISTA Sequence Plan (DSP)
Nadrzędnym zadaniem tej aplikacji jest nadzór nad terminową realizacją planu produkcyjnego. W produkcji na zlecenie, terminowość to klucz do sukcesu. Ten parametr jest szczególnie istotny na rynku renowacji stolarki. Dostępne są dwa widoki: planisty (moduł logistyczny) oraz produkcji (moduł operacja). Każdy z nich wizualizuje dane do potrzeb każdej grupy odbiorców. Widok planisty – perspektywa całego procesu (ang. routing) to graficzna prezentacja przebiegu procesu produkcji w relacji do planu.
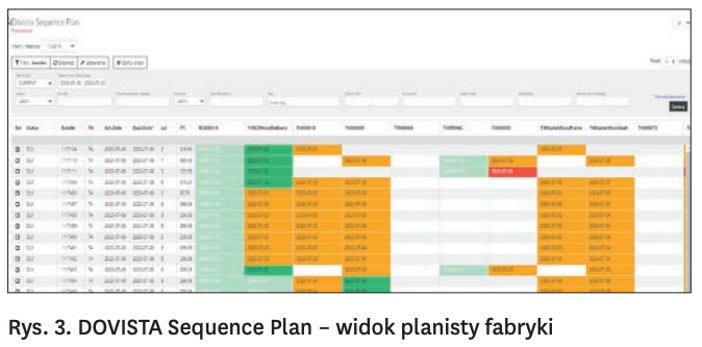
Każda zrealizowana operacja jest monitorowana przez sieć skanerów pracujących w sieci zakładowej Wifi. Po skanie, termin faktycznej realizacji jest odnoszony do planu dla tejże operacji oraz prezentowany w postaci kolorowej komórki. Zielona (ciemno) – zrobione na czas, zielone (jasno) – przed planowanym czasem, żółte – zrobione, ale później niż zakładano, czerwone – opóźnione.
Taka forma, wzbogacona o dodatkowe dane dotyczące każdego zlecenia, daje planiście / logistykowi ciągłą i aktualną informację o stopniu zaawansowania produkcji. To pozwoliło znacząco zredukować konieczną liczbę telefonów, maili oraz spotkań w celu określenia realizacji zlecenia. Narzędzie to zyskuje na znaczeniu w przypadku, gdy są problemy z jakimś zleceniem – przykładowo, gdy dojdzie do uszkodzenia produktu (np. zbicie szyby). Informacja taka uruchamia natychmiast procedury awaryjne, włącznie z poinformowaniem centrum dystrybucyjnego, a w krytycznych sytuacjach, klienta docelowego, o sytuacji.
Proces inwestycyjny na budowie może wówczas zostać zmodyfikowany. Takie podejście umożliwiło zakładowi objętemu tym systemem osiągnięcie poziomu +95% terminowości do centrum dystrybucyjnego.
Drugim dostępnym widokiem DSP jest widok operatora. Jest to ujęcie tych samych danych, tym razem z punktu widzenia pracownika (brygadzisty) konkretnego stanowiska roboczego. Taki układ agreguje zadania dla wybranego obszaru produkcji wraz z podstawowym danymi o planowanym terminie wykonania zadania oraz pozwala dokonać kilku podstawowych akcji z poziomu stanowiska, takich jak potwierdzenie zlecenia, wprowadzenie komentarza do zlecenia (notatki istotnej dla innych uczestników procesu), zarejestrowanie wady czy generowanie plików CNC na maszynę.
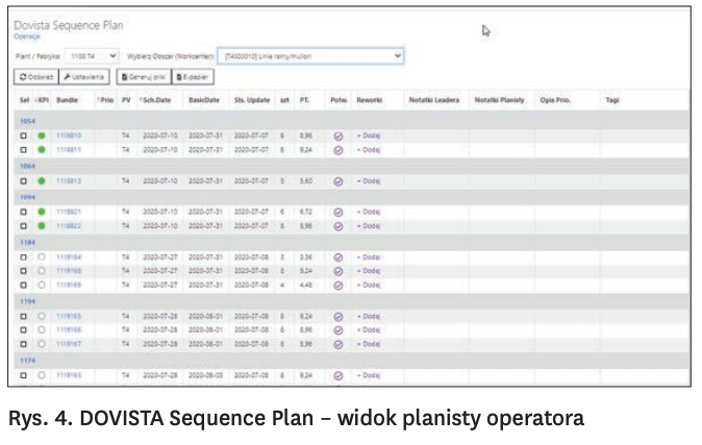
Dodatkową korzyścią dla operatora jest informacja o tym, czy poprzednia operacja już się zakończyła. Oszczędza to czas operatora na szukanie zleceń, których nie ma w jego buforze.
2. E-papiery produkcyjne – znak firmowy DOVISTA
Kluczowym osiągnięciem w ramach tego projektu, będącym swoistym znakiem firmowym, to E-papiery produkcyjne. Mierząc osiągnięcia wpływem na środowisko, to właśnie ten element jest kluczowy. O skali oddziaływania na środowisko niech świadczą liczby, jakie stoją za tym projektem.
Otóż w skali tygodnia w całej wiosce okiennej drukowane jest ok. 200 000 kartek A4. Jest to ekwiwalent 400 ryz papieru. W naszych realiach koszt uwzględniający tylko papier oraz tonery drukarek w skali roku to kwota mocno ponad 100 000 PLN. Do tego należy doliczyć koszty utylizacji zużytego papieru.
Po wdrożeniu projektu na wszystkie zakłady, szacujemy redukcję tego kosztu o 85%. Rozwiązanie to dostarcza aktualnych informacji dla operatorów w zakresie danych szczegółowych dla wybranego zlecenia produkcyjnego. Oprogramowanie jest zaprojektowane i wykonane do pracy na tablecie, dając tym samym pełną mobilność i ogranicza koszty. Jedyne wymagania sprzętowe to obsługa przeglądarki. Wśród funkcjonalności, jakie dostarcza E-papier, to zestawienie detali, jakie należy wyprodukować w ramach zlecenia, wraz z detaliczną informacją dotyczącą danych danego detalu.
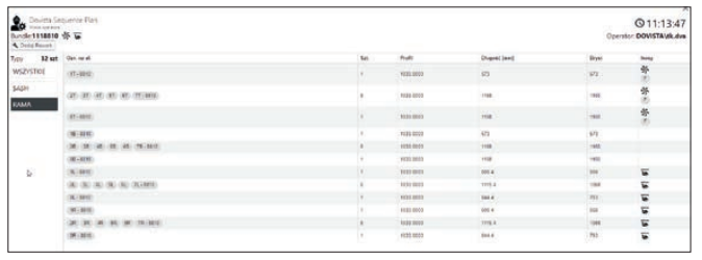
Co istotne, każda operacja wspomniana w dokumentacji jest osobnym linkiem do dokumentu i instrukcji. Ta cecha powoduje, że każdy pracownik w dowolnym momencie ma dostęp do najaktualniejszej dokumentacji bez konieczności przechowywania papierowej wersji. Eliminuje to także konieczność nadzoru aktualności kolejnych dokumentów. Każde podniesienie rewizji dokumentu powoduje, że jest ona natychmiast dostępna dla pracowników.
Rozwiązania E-papier, oprócz wymagań technicznych i merytorycznych, poddawane są również analizie UX (User Experience) poprawiającej ergonomię pracy z dokumentem oraz powodują przyjazność użytkowania dla pracowników. W trakcie szkoleń załogi na bieżąco zbieramy opinie pracowników i wprowadzamy korekty do wyglądu dokumentów. Zespół pracuje w oparciu o metodę Agile (zwinne zarządzanie projektami), stąd częste zmiany to coś, co lubimy najbardziej.
3. Generator plików maszynowych
Przy produkcji produktów konfigurowanych na masową skalę, wyzwaniem staje się dostarczanie dedykowanych programów dla maszyn CNC. W ramach wdrożenia wykonaliśmy rozwiązanie, które, bazując na danych zgromadzonych w bazie danych MES, „na życzenie” operatora generuje plik (program) do konkretnej maszyny. W zakładach DOVISTA pracuje kilkadziesiąt gniazd cyfrowych różnych producentów i wiele języków programowania.
Stąd konieczne było stworzenie translatorów (xslt) kojarzących zadania i maszynę. W wyniku działania tego mechanizmu po kilku sekundach program jest dostępny w lokacji sieciowej i operator przystępuje do pracy. Ten proces całkowicie wyeliminował potrzebę angażowania w proces służb technologicznych. Operatorzy „piszą” sobie programy samodzielnie.
4. Blokady jakościowe
Kolejną funkcjonalnością, jaką wdrożyliśmy, jest możliwość blokowania konkretnych produktów na wybranych etapach produkcji celem szczegółowej weryfikacji jakościowej lub produktowej. Zlecenia, które wymagają takiego nadzoru (na przykład elementy targowe lub zlecenia VIP) w momencie próby potwierdzania postępu produkcji wchodzą w stan blokady, co jest sygnalizowane na skanerze operatorskim (skanerze Wifi) odpowiednim monitem. Aby zlecenie mogło być kontynuowanie, konieczne jest „zdjęcie blokady”, którego może dokonać autoryzowany personel (zwykle inspektor jakości lub inżynier procesu), poświadczając tym samym, iż produkt spełnia wymagania specyfikacji.
Rozwiązanie to jest szczególnie przydatne w procesie wdrożenia nowego produktu / technologii, gdyż pozwala w pełni walidować proces, nawet jeśli nowy przepływ stanowi ułamek całości wolumenu i nie jest jeszcze standardem.
5. Rework APP – monitor zleceń wadliwych
W każdym, nawet bliskim ideałowi, procesie produkcyjnym, zdarzają się „wpadki”. Jak to bywa w produkcji, czasami wydarzy się jakiś „wypadek”, który sprawia, że założony plan nie może być w pełni zrealizowany. Takie zdarzenie bywa dodatkowo kłopotliwe z uwagi na fakt, iż o ile właściwy przepływ jest dość dobrze monitorowany, to już ten „alternatywny” niekoniecznie.
Celem naszych prac było także umożliwienie monitorowania i wsparcie procesu wadliwego. Kiedy produkcja stwierdza taki fakt, zakładany jest tzw „Rework”. Zarejestrowany brak od tej pory podlega specjalnemu nadzorowi. Zaistnienie takiego faktu jest odnotowane kreskowaniem komórki na DSP (patrz poniższy rysunek), co samo z siebie nasuwa planiście wniosek, że zlecenie jest zagrożone. Jednocześnie z poziomu DSP mamy możliwość prześledzenia historii zlecenia.
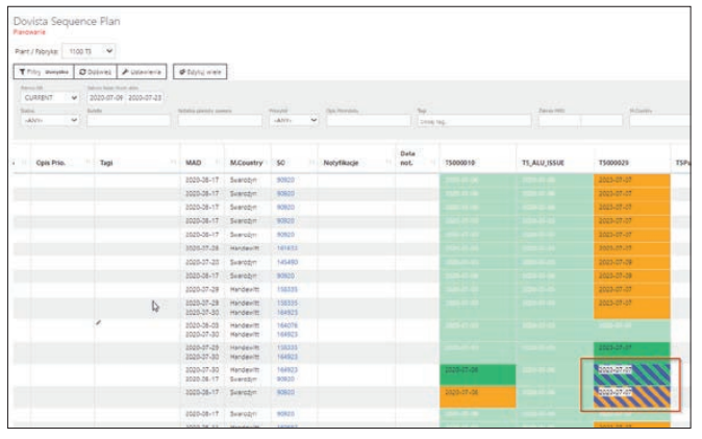
Tutaj, wzorem historii przesyłki kurierskiej, mamy zarejestrowane wszystkie istotne sekwencje dla takiego „Reworka”. Na jego karcie, poza historią, mamy do dyspozycji także informacje statystyczne (kodowanie błędu) dla lepszej analizy źródeł powstania braku oraz pracy nad eliminacją w przyszłości.
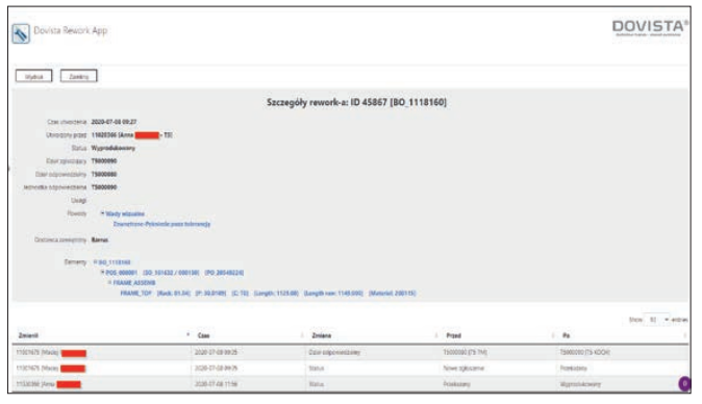
Ślad cyfrowy zamiast węglowego?
Każdy proces produkcyjny w dobie digitalizacji ma swój cyfrowy ślad w postaci niezliczonej ilości danych, które ostatecznie, po odpowiedniej analizie, przy zastosowaniu określonych technologii, materializują się w postaci konkretnego produktu czy usługi. Ten cyfrowy ślad to także dowód na odpowiedzialne podejście do kwestii środowiska naturalnego. Digitalizacja bowiem istotnie pomaga ograniczyć nie tylko zużycie papieru, ale ma wpływ na zostawiane ślady węglowe w całym łańcuchu dostaw. Warto więc podjąć każde, nawet najmniejsze działanie, które może pomóc ratować planetę.
Tomasz Kubach