Treści
Tożsamość maszyny – jak przekształcić inżynierię w cyfrowego partnera?
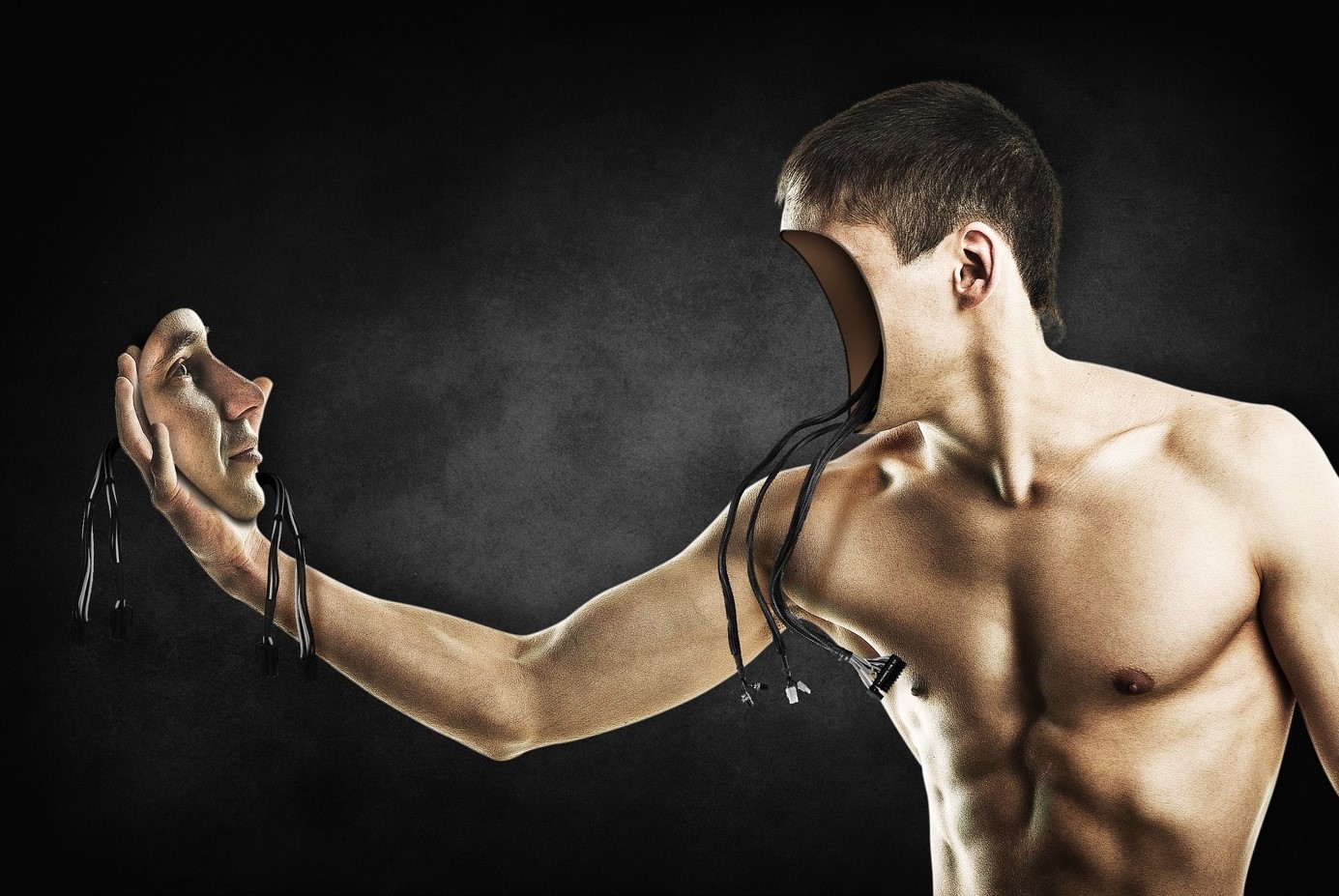
Tożsamość maszyny – jak przekształcić inżynierię w cyfrowego partnera?
Tożsamość maszyny zależy od środowiska w jakim działa. Jest tak inteligentna, jak inteligentny jest jej twórca. Jak zatem zdefiniować taką inteligencję i czy możemy odnieść ją do tego, co znamy z ludzkich zachowań? Daniel Sonntag z German Research Center for Artificial Intelligence przekonuje, że objawia się ona w “tożsamości” maszyn, robotów czy systemów. Innymi słowy, w przemyśle 4.0 przekształcamy inżynierię w cyfrowego, zautomatyzowanego partnera.
Narodziny cyfrowych bliźniaków
„Digital Twin” to pojęcie doskonale znane każdemu inżynierowi przemysłu 4.0. Są to wirtualne, niemal identyczne kopie obiektów fizycznych, które pozwalają symulować i optymalizować zarówno urządzenia, jak i procesy zachodzące wewnątrz fabryki. Dzięki temu inżynierowie unikają ryzyka i swobodnie testują rozmaite rozwiązania, poprawiają działanie maszynerii i przeprowadzają analizy w czasie rzeczywistym.
Sonntag zwraca jednak uwagę, że cyfrowy bliźniak to ostatni etap „ewolucji”, jaką przechodzą urządzenia i systemy funkcjonujące w firmach z Industry 4.0. Wdrożenie tego rodzaju innowacji w pracę fabryk wymaga jednak zapoznania się z innymi stadiami procesu, jakim jest tworzenie inteligentnego, zautomatyzowanego środowiska. Niemiecki badacz przedstawił cztery fazy, przez które warto przeprowadzić organizację zanim podejmie ona współpracę z „digital twins” i, co za tym idzie, dołoży niezwykle istotną „cegiełkę” do procesu transformacji cyfrowej.
1. Cyfrowa tożsamość
Pierwszym z etapów jest wykorzystanie innowacji, która od dłuższego czasu jest elementem funkcjonowania naszych smartfonów. Cyfrowy odcisk palca, bo o nim właśnie mówimy, to niezwykle prosty i powszechnie stosowany wariant budowania naszej wirtualnej tożsamości. To pigułka informacji na temat każdego z nas, która pozwala zidentyfikować nas w cyfrowym świecie.
Co więcej, taką wirtualną tożsamością mogą się poszczycić również produkty. Kody QR, z powodzeniem wykorzystywane choćby w marketingu, pozwalają błyskawicznie zidentyfikować dany zasób i uzyskać niezbędne informacje na jego temat.
Jak cyfrowa tożsamość może zostać wykorzystana w fabryce?
Dla przykładu, inżynierowie mogą dysponować czytnikami kodów QR w smartfonie, którymi skanują kody na rozmaitych urządzeniach. Pozwala im to w mgnieniu oka odwiedzić stronę producenta urządzenia i znaleźć tam niezbędne informacje na temat maszyny i problemów, z którymi aktualnie się boryka. Dzięki temu mogą oszczędzić nie tylko czas, ale również pokaźną liczbę fizycznych dokumentów, do których musieliby zajrzeć w przypadku braku dostępu do wirtualnego opisu produktu.
2. Cyfrowa migawka
Również zdjęcie może być nośnikiem pokaźnej ilości informacji. Każda fotografia zrobiona aparatem czy też smartfonem może bowiem przekazywać niezwykle istotne dane na temat stanu urządzenia w danym momencie.
Dzięki temu inżynierowie mogą z łatwością budować historię eksploatacji i serwisu danej konstrukcji. Opisanie zdjęcia danymi z liczników, informacjami na temat użytych części zamiennych czy też zidentyfikowanych problemów pozwala „drugiej stronie” – serwisantowi urządzenia błyskawicznie zapoznać się z problemem i zaproponować rozwiązanie bez konieczności fizycznej obecności w fabryce.
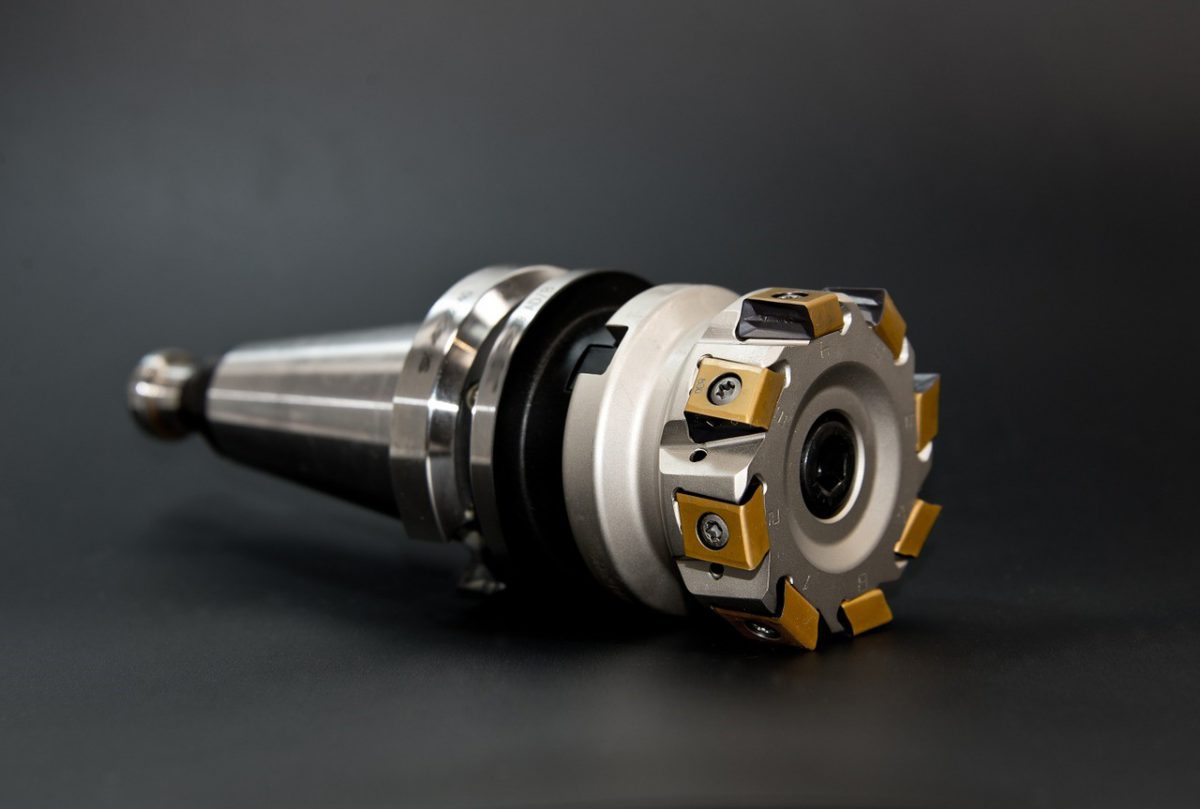
Choć „cyfrowa migawka” zdaje się być daleka od tematyki „cyfrowej transformacji” jest ona wciąż bardzo rzadko stosowana w fabrykach. Biorąc pod uwagę prostotę i efektywność czasową tej metody trzeba jednak przyznać, że jest to duży błąd!
3. Cyfrowy cień
To bardziej zaawansowana koncepcja niż wspomniana „migawka”. Cyfrowy cień stanowi dwuwymiarowa projekcja dowolnego obiektu. O ile pierwszy wymiar stanowi jego faktyczna, fizyczna reprezentacja, o tyle drugi jest jej wirtualnym odzwierciedleniem.
Pozwala to na automatyczne zbieranie danych w czasie rzeczywistym, bez jakiegokolwiek udziału operatora. Te zaś zostają poddane obróbce, która umożliwia wyciąganie wniosków i doskonalenie narzędzia. Z tego etapu został już tylko krok do rozwiązania, dzięki któremu inżynier może symulować również dowolne zmiany w funkcjonowaniu maszyny i warunkach otoczenia – cyfrowego bliźniaka.
4. Cyfrowy bliźniak
Finalny etap stanowi wdrożenie „digital twin” w prace przemysłu. Łącząc cechy cyfrowej tożsamości, cyfrowej migawki i cyfrowego cienia mamy możliwość stworzenia wirtualnej kopii dowolnego obiektu i, jak zaznaczyliśmy we wstępie, dowolnego symulowania rozmaitych aktywności.
Jak technologię cyfrowych bliźniaków wykorzystują rozmaite biznesy? Dla przykładu, NASA stosuje tę technologię niemal od samego początku historii eksploracji kosmosu. Dzięki niej ma bowiem możliwość zarządzania i naprawiania systemów, do których nie ma fizycznego dostępu. Efektem „treningów” z cyfrowymi bliźniakami była np. pomyślna akcja ratowania misji Apollo 13.
Innym zastosowaniem digital twin jest praca z przemysłowymi robotami. Zdalny operator ma dzięki niemu możliwość operowania urządzeniem na dużą odległość. Cyfrowe bliźniaki sprawdzają się także w medycynie (dzięki możliwości wizualizowania operacji), jak również energetyce (np. poprzez symulowanie warunków atmosferycznych i sprawdzanie efektywności działania farm wiatrowych w różnych lokalizacjach).
Cyfrowe bliźniaki powoli wchodzą do głównego nurtu w realizacji procesów produkcyjnych. Według analityków Gartnera, do 2021 roku połowa dużych przedsiębiorstw przemysłowych będzie wykorzystywać rozwiązania digital twins, co pozwoli na wzrost ich wydajności o 10 proc. A do 2022 roku ponad dwie trzecie firm, które mają zaimplementowane technologie z zakresu Internetu Rzeczy, wdroży co najmniej jednego cyfrowego bliźniaka.
Już dzisiaj istnieje nawet cyfrowy bliźniak całego miasta! Dzięki takiemu rozwiązaniu, władze Singapuru mają możliwość nie tylko planowania kolejnych inwestycji, ale także analizowania zużycia energii czy też symulowania zmian w ruchu ulicznym.