Treści
Sens cyfrowych bliźniaków w przemyśle
Sens cyfrowych bliźniaków w przemyśle
Wyobraźmy sobie, że po przeprowadzce do nowo wybudowanego domu potrzebujemy kilkudziesięciu otworów na karnisze. Nie możemy wykluczyć, że tam, gdzie chcemy wiercić, pod tynkiem poprowadzono przewody.
Mamy do dyspozycji cyfrowy projekt instalacji elektrycznej i oczywiście zastanawiamy się, czy kable biegną tak, jak to zostało narysowane przez projektanta. Mamy kilka opcji: możemy uwierzyć projektowi i wiercić, poszukać zdjęć powykonawczych, a jeśli ich nie znajdziemy, sprawdzić wybrane miejsca detektorem kabli.
Wyobraźmy sobie jednak, że po wykonaniu instalacji elektrycznej pomieszczenia zostały zeskanowane i zmiany wprowadzone do projektu cyfrowego. To daje nam dodatkową opcję, znacznie lepszą od pozostałych. Przed wierceniem zakładamy okulary rozszerzonej rzeczywistości i dzięki nim widzimy, czy w wybranym miejscu są kable, czy ich nie ma. To najprostszy scenariusz zastosowania cyfrowego bliźniaka w domu. Jakie daje korzyści? Na pewno pozwala szybciej zrealizować zadanie, zapewniając mniejsze ryzyko uszkodzenia instalacji i większe bezpieczeństwo wykonawcy.
Do tej pory cyfrowe bliźniaki najbardziej upowszechniły się w branży architektonicznej i budowlanej za sprawą standardów BIM (Building Information Management). Wirtualne kopie budynków i ich instalacji pozwalają łączyć procesy cyfrowego projektowania wielobranżowego, planowania i realizacji budowy, przekazywania obiektów do użytkowania, a ostatecznie pozwalają obniżać koszty użytkowania i przebudowy. Kolejnym znaczącym obszarem gospodarki, który wykorzystuje rozwiązania tego typu jest przemysł i sektor produkcyjny.
Gdzie szukać sensu cyfrowych bliźniaków w przemyśle?
Możemy wskazać przynajmniej 4 obszary:
1. Rosnąca złożoność procesów produkcyjnych i logistycznych, czyli jak dostarczać na czas.
Kilka lat temu żyliśmy w rzeczywistości, w której zamówione materiały w 90% przypadków przychodziły na czas, a w niektórych branżach nawet celowo redukowano stany magazynowe surowców w myśl filozofii just-in-time. Pozwalała ona planować produkcję z tygodniowym wyprzedzeniem. Dzisiaj w procesach logistycznych i procesach planowania, kluczowe jest patrzenie na cały, złożony łańcuch wartości, czyli zdolności produkcyjne i przewidywalność dostaw, ścieżki transportowe, realizację produkcji w rozproszonej sieci fabryk oraz dynamikę zamówień klientów. Do tej pory wiele elementów dało się symulować za pomocą Excela i złożonych makr, ale dzisiaj takie narzędzia już nie wystarczą. Co więcej, symulacja wymaga ciągłego dostarczania informacji zwrotnych ze wszystkich wskazanych procesów.
2. Poziom skomplikowania kluczowych linii technologicznych, czyli jak optymalizować zwrot na aktywach operacyjnych.
W miarę wzrostu złożoności procesów rośnie też poziom skomplikowania linii technologicznych. Rynek dąży do masowej personalizacji wyrobów, co przekłada się na konieczność zakupu maszyn i linii technologicznych, które są wielofunkcyjne. To dodatkowo zwiększa stopień skomplikowania i podatność na awarie. Ponadto, w obszarze robotyzacji, programowanie i testowanie realnego obiektu jest czasochłonne i generuje bardzo wysokie koszty związane z zakupem materiałów. Zastosowanie cyfrowych bliźniaków maszyn i linii technologicznych może zdecydowanie wspierać procesy usuwania usterek i awarii przez zespoły autonomicznego utrzymania ruchu, czyli wyspecjalizowanych operatorów. Analogii możemy szukać tutaj w zaawansowanych drukarkach, które podpowiadają, jak usunąć awarię. Dodatkowo dostępność kompleksowych zestawów danych nt. pracy maszyny, daje możliwość stosowania zaawansowanych strategii utrzymania ruchu, np. predictive maintenance albo risk-based maintenance. Dodatkowym wymiarem optymalizacji pracy linii technologicznych może być optymalne zużycie energii i mediów, co wspiera strategie zrównoważonego rozwoju.
3. Eksperci odchodzący na emeryturę, czyli jak zapewnić ciągłość biznesu.
Proces starzenia się ekspertów i technologów w energetyce, branży chemicznej, rafineriach czy innych sektorach przemysłu, jest kolejnym wielkim wyzwaniem. Po pierwsze brakuje następców, ponieważ proces uczenia się w takiej specjalizacji jest bardzo długi. Po drugie, przemysł przestaje być atrakcyjnym miejscem pracy dla młodego pokolenia. Jest to wielkie wyzwanie. Sensowne wydaje się w tej sytuacji „wtłaczanie” wiedzy doświadczonych technologów do cyfrowych narzędzi (np. w formie modeli), a także zaangażowanie ich w procesy nadzorowanego uczenia algorytmów. Z jednej strony gwarantuje to bezpieczeństwo, że wiedza nie odchodzi z firmy w 100% po przejściu eksperta na emeryturę. Z drugiej strony fabryka, która korzysta z nowoczesnych cyfrowych narzędzi, jest atrakcyjniejszym miejscem pracy dla młodego pokolenia.
4. Rozproszenie zespołów inżynierskich, czyli jak budować bazy wiedzy.
Strukturalna zmiana, która dokonała się w latach 2020-2022, to wprowadzenie na masową skalę pracy zdalnej i pracy hybrydowej. Ludzie, którzy dotąd spotykali się często w biurze czy fabryce, teraz przez większość dni w tygodniu pracują z domu. Z jednej strony zwiększa to ich efektywność indywidualną, z drugiej sprawia, że nie mogą rozwiązać problemu w trakcie przysłowiowej rozmowy na korytarzu czy spontanicznej sesji problem-solving na żywo. Cyfrowe narzędzia do projektowania i symulacji, budowy modeli procesów i linii technologicznych, a także komunikacji między zespołami i budowania bazy wiedzy nt. rozwiązywanych problemów, mogą przynieść w takich sytuacjach wiele korzyści. Tym bardziej, że zdecydowana większość inżynierów woli komunikację cyfrową od osobistej.
Jest wiele powodów, dla których zastosowanie cyfrowych bliźniaków ma sens. Ostatnim z nich jest dynamicznie rosnąca dostępność technologii, wyrażona zarównoprzez łatwość jej zastosowania, jak i relację kosztów do korzyści.
Dowiedz się więcej
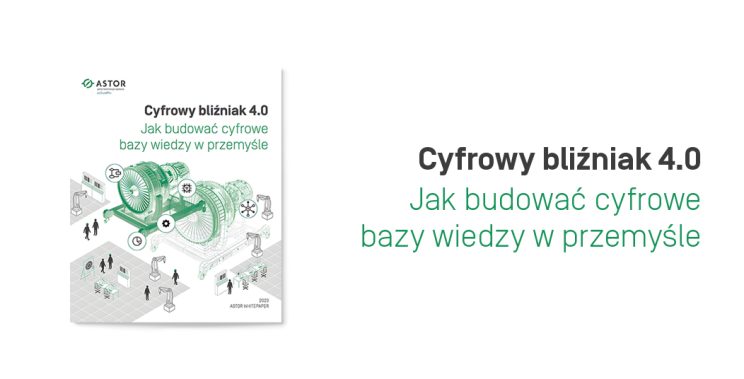
Dowiedz się więcej o cyfrowym bliźniaku w nowej publikacji „Cyfrowy bliźniak 4.0. Jak budować cyfrowe bazy wiedzy w przemyśle„