Treści
Poznaj Total Productive Maintenance (TPM), czyli sposób na bezpieczne i efektywne Utrzymanie Ruchu
Poznaj Total Productive Maintenance (TPM), czyli sposób na bezpieczne i efektywne Utrzymanie Ruchu
Podczas planowania projektów cyfryzacji Utrzymania Ruchu, często pojawiają się inicjatywy optymalizacji działania, oparte na koncepcji Lean czy wprowadzeniu takich filozofii jak WCM (ang. World Class Manufacturing) i TQM (ang. Total Quality Management). Niejednokrotnie dobrym rozwiązaniem na początek okazuje się wdrożenie TPM, które pomaga w usprawnieniu działania całego zakładu.
Czym jest TPM?
TPM (ang. Total Productive Maintenance) jest jedną ze strategii Lean manufacturingu, zgodną z filozofią ciągłej optymalizacji procesów i odnoszącą się bezpośrednio do działów Utrzymania Ruchu.
TPM to zestaw procesów, technik i strategii, skupionych na zwiększeniu efektywności produkcji, a także na podniesieniu jakości i bezpieczeństwa poprzez pracę ludzi, konserwację maszyn, wykorzystanie odpowiednich narzędzi oraz procesy optymalizacji, które dodają wartości organizacji.
Celem TPM jest osiągnięcie maksymalnej efektywności w zakresie wykorzystania narzędzi oraz zaangażowania pracowników. Aby to osiągnąć, konieczne jest wyeliminowanie wypadków, błędów jakościowych w wyrobach końcowych lub cząstkowych, a także wykluczenie nieplanowanych przestojów oraz skrócenie czasów tych zaplanowanych.
TPM ma również na celu poprawę współpracy działu produkcji (w dużej mierze operatorów) ze służbami Utrzymania Ruchu. Pracownicy produkcji zyskują znacznie większą świadomość w kwestii konserwacji, co w efekcie wspiera techniczną dostępność maszyn, a także minimalizuje czasy przestojów oraz sprawia, że Utrzymanie Ruchu może skupić swoje działania na bardziej krytycznych czynnościach. To wszystko przekłada się na oszczędności.
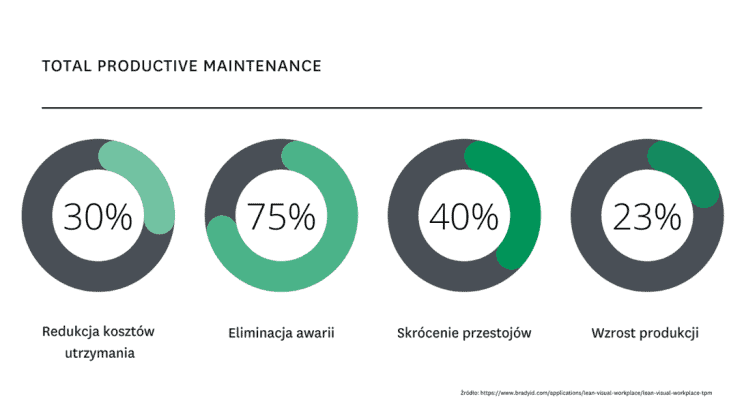
5S – fundament wdrożenia TPM
Fundamentem wdrożenia TPM jest metoda 5S. Skupia się ona na organizacji stanowiska pracy oraz codziennego utrzymania go w czystości, wedle określonych standardów.
Kolejne kroki metody 5S to:
- selekcja znajdujących się na stanowisko pracy elementów i usunięcie zbędnych przedmiotów,
- systematyka w rozmieszczeniu i uporządkowaniu pozostawionych przedmiotów,
- sprzątanie stanowiska pracy według określonego wcześniej wzorca,
- standaryzacja wcześniejszych kroków w celu utrwalenia u pracowników poczucia odpowiedzialności za stanowisko,
- samodyscyplina pracownika w dalszej optymalizacji pracy na swoim stanowisku.
Dzięki tej metodzie pracownik zyskuje większą świadomość i przejmuje odpowiedzialności za swoje stanowisko pracy oraz dąży do jego doskonałości. Filary TPM nie będą miały solidnej podstawy i nie osiągną zamierzonych celów bez poprawnej implementacji procedury 5S.
Filary systemu TPM
Elementy składowe poprawnego wdrożenia TPM ilustruje tzw. świątynia TPM. Istnieje wiele jej przykładów, różniących się nazewnictwem poszczególnych filarów, jednak ich przesłanie zawsze jest podobne: zbudujmy solidne przedsiębiorstwa, eliminując wypadki, usterki i awarie!
Poszczególne filary systemu TPM to:
Autonomiczne Utrzymanie Ruchu – polega nie tylko na samodzielności w zakresie utrzymania ruchu, ale i na zwiększeniu znajomości maszyn u operatorów, którzy przejmują odpowiedzialność za regulacje i drobne konserwacje obsługiwanego przez siebie sprzętu. Dzięki temu pracownicy są bardziej zmotywowani, a ich kwalifikacje rosną. Dodatkowo można znacznie szybciej wychwycić wszelkie niebezpieczne symptomy w działaniu maszyn.
Ciągłe doskonalenie – opiera się na stałej współpracy produkcji i Utrzymania Ruchu. Celem jest eliminowanie marnotrawstwa w procesie produkcji, udoskonalanie codziennej pracy czy znajdowanie przyczyn źródłowych awarii (RCA).
Planowanie UR – polega naplanowaniu działań konserwacyjnych, opartych nie tylko na wykonaniu obowiązkowych wymian zgodnie z dokumentacją, ale i na monitorowaniu zużycia zasobów.
Wczesne planowanie konserwacji – odnosi się do wczesnego planowania działań konserwacyjnych na maszynach. Zarówno podczas ich modernizacji, napraw czy nowych zakupów, weryfikowana jest opłacalność każdej z tych opcji.
Zapewnienie i utrzymanie jakości – bazuje na możliwości ciągłego monitorowania jakości wyrobów końcowych, dzięki wykrywaniu nieprawidłowych elementów procesu w trakcie produkcji. Narzędzia takie jak Andon czy Jidoka pozwalają maszynom informować pracowników o wszelkich nieprawidłowościach za pomocą sygnałów świetlnych lub dźwiękowych.
Komunikacja międzydziałowa – filar ten dotyczy stosowania zasad TPM w administracji. Ma na celu poprawę procedur związanych z przetwarzaniem zamówień, standardów dokumentacji czy harmonogramowania. Wpływa on na doskonalenie komunikacji między poszczególnymi działami przedsiębiorstwa.
Rozwój i szkolenie personelu – opiera się nie tylko na szkoleniu operatorów tak, aby byli w stanie samodzielnie dokonywać drobnych napraw, ale i na udostępnieniu im potrzebnych do tego narzędzi. Utrzymanie Ruchu uczy się zmiany działania z reaktywnego na prewencyjne, a później na predykcyjne. Menadżerowie natomiast uczą się zmian w strategii doskonalenia czy standardów WCM.
Bezpieczeństwo i środowisko – odnosi się do bezpieczeństwa pracowników, poprzez eliminację potencjalnych zagrożeń dla zdrowia, a także wpływu zaplecza technologicznego na środowisko pracy.
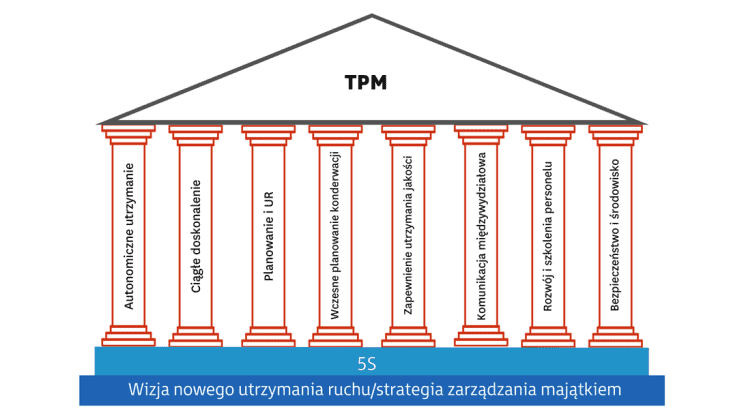
Cele TPM
Główne cele TPM, realizowane nie tylko w sferze maszyn, ale i ludzi, to zwiększenie wskaźnika OEE (na które składa się możliwie jak największa dostępność maszyn, najwyższej jakości produkty, ograniczenie do minimum nieplanowanych konserwacji i przestojów) oraz zapewnienie maksymalnego bezpieczeństwa pracowników.
Najprościej cele te określane są jako:
- ZERO awarii,
- ZERO defektów,
- ZERO wypadków.
W każdym projekcie związanym z TPM najpierw wypracowujemy proces, a potem narzędzia. Jeśli potrzebujesz pomocy w którymś z tych etapów, zgłoś się do naszych ekspertów.
Na wskaźnik OEE wpływa 6 głównych strat:
Nieplanowane przestoje – awarie oprzyrządowania, nieprzewidziane konserwacje, przegrzania czy problemy ze smarami.
Przezbrojenia i regulacje – konieczność przezbrojenia, niedobór materiału, wydłużone czasy zmian operatorów, uruchomienia czy dostrojenia do procesu.
Krótkie przestoje – mikroprzestoje, drobne regulacje, braki w dostawach surowca, problemy z czujnikami.
Bieg jałowy – nieprawidłowe ustawienie, blokady, zacięcia.
Wady produkcyjne – odrzuty podczas produkcji spowodowane złą kalibracją lub brak monitorowania wyrobów, którego efektem jest zła jakość wymagająca poprawek.
Zmniejszona wydajność – odrzuty podczas rozgrzewania, uruchamiania lub inne problemy na wczesnym etapie produkcji.
Jak wdrażać TPM?
Wdrożenie TPM dobrze jest rozpocząć od rozpisania poszczególnych etapów tak, aby system został jak najlepiej przyjęty przez pracowników.
ETAP I: Przygotowanie do wdrożenia – określenie celów, jakie mają być zrealizowane, zaangażowanie kierownictwa, przeprowadzenie szkoleń wstępnych i poinformowanie pracowników o idei, a także określenie wskaźników oraz stworzenie planu wdrożenia.
ETAP II: Oficjalne rozpoczęcie wdrożenia TPM – na tym etapie warto przeprowadzić wydarzenie związane z oficjalnym wdrożeniem TPM. Pomoże to przekonać osoby niezainteresowane, że projekt jest ważny dla organizacji.
ETAP III: Proces wdrożenia TPM – wdrażanie Autonomicznego Utrzymania Ruchu i optymalizacji procesów, zwiększanie kompetencji pracowników, zwielokrotnianie nakładów na prewencje i predykcje, wprowadzanie metod pomagających zapobiegać wadom jakościowym na etapie planowania, zapewnienie lepszego środowiska komunikacji, zwiększanie poziomu bezpieczeństwa pracowników.
ETAP IV: Ciągłe doskonalenie – systematyczne wdrażanie i rozwijanie zasad TPM w innych działach oraz stałe doskonalenie procesów w przedsiębiorstwie.
Jak CMMS wspiera wdrożenie TPM?
Systemy klasy CMMS (ang. Computerised Maintenance Management Systems) posiadają funkcjonalności pozwalające koordynować pracę działów Utrzymania Ruchu, a także prowadzić ewidencję danych o parku maszynowym. Przede wszystkim jednak wspierają produkcję, poprzez zapewnienie narzędzi umożliwiajacych ciagłą edukację operatorów w zakresie serwisowania maszyn. Wszystkie te cechy sprawiają, że CMMS są systemami sprzyjającymi wdrażaniu metody TPM.
Rozróżnienie na poszczególne platformy, w zależności od tego, kto z nich korzysta, pozwala dostosować narzędzia wpierające działania w systemie TPM do potrzeb organizacji.
Wyróżniamy takie platformy jak:
- Aplikacje dla produkcji z wbudowanymi elementami Autonomous Maintenance (Autonomicznego Utrzymania Ruchu). Można w nich znaleźć historię napraw, listy kontrolne, dokumentację, zgłoszenia sugestii KAIZEN oraz system powiadomień o zmianach w planach serwisowych
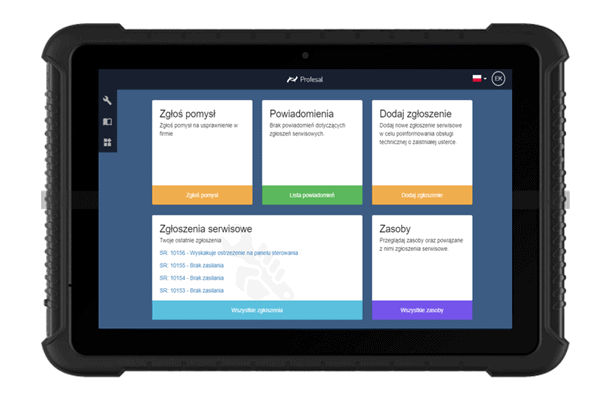
- Aplikacje dla techników Utrzymania Ruchu pozwalające na dostęp do dokumentacji technicznej maszyn, podgląd dostępnej historii awarii i ostatnich przeglądów. Zapewniają one ciągły kontakt z działem produkcji i umożliwiają wykonywanie przeglądów w oparciu o listy kontrolne z wizualizacją pokazującą co, gdzie i jak należy wykonać.
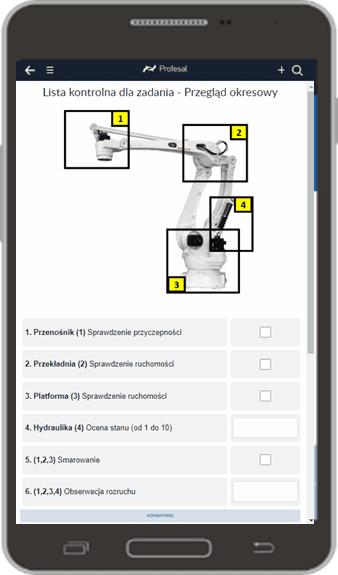
- Programy kierownicze pozwalające na generowanie raportów zależnych od wskaźników UR, analiz porównawczych i matryc kompetencji pracowników. Umożliwiają one weryfikację szkoleń dla działów Utrzymania Ruchu i śledzenie wskaźników KPI.
Możliwość integracji systemów CMMS z innym oprogramowaniem pozwala na rozszerzenie działania systemu poza standardowe działy Utrzymania Ruchu i Infrastruktury. W tym kontekście zadaniem takiego systemu jest nie tylko codzienne wspieranie pracy działu Utrzymania Ruchu, ale i dostosowanie się do zachodzących w nim procesów oraz ich ciągłe ulepszanie, zgodnie z metodologią Lean.
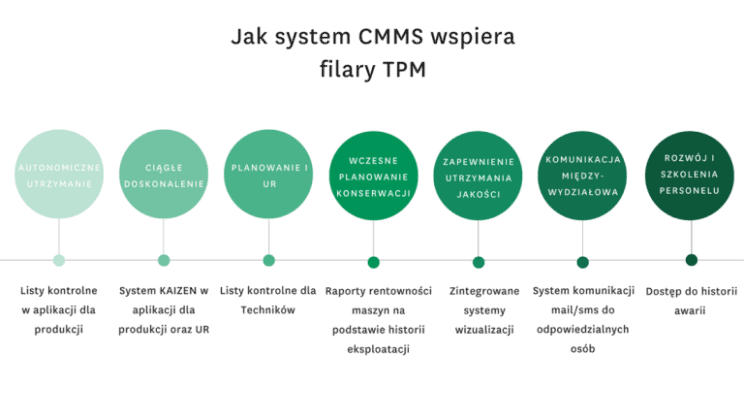
TPM wspierany przez CMMS – korzyści
Główne korzyści wynikające z wdrożenia systemu CMMS wspierającego strategię TPM to:
- sprawność komunikacji na linii produkcji UR,
- wzrost dostępności technicznej maszyn,
- wzrost wskaźnika OEE,
- szybkie analizy przyczyn źródłowych awarii,
- mniejszy poziom nadmiernych zapasów,
- redukcja jednostkowych kosztów wyrobu,
- poprawa stabilności procesów produkcji,
- wzrost efektywności przeglądów prewencyjnych,
- spadek ilości wypadków,
- szybkość i dokładność planowania harmonogramów przeglądów,
- wzrost kompetencji personelu Produkcji i Utrzymania Ruchu,
- automatyzacja procesów zarządzania serwisem,
- nowoczesne utrzymanie ruchu, mające czas na optymalizację procesów i działania maszyn.
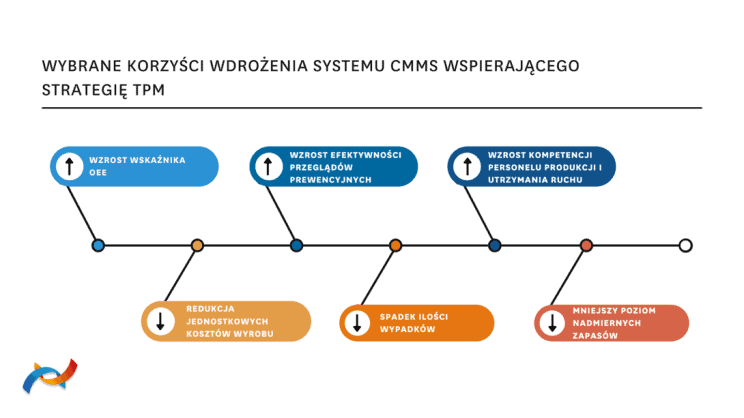
FAQ – najczęściej zadawane pytania
Jakie wskaźniki mierzyć podczas wdrożenia TPM?
W zależności od stopnia zaawansowania wdrożenia, cele mogą się zmieniać. Najczęściej jednak mierzone są wskaźniki OEE, MTTR i MTBF, a także dostępność techniczna oraz ogólna jakość wyrobów końcowych.
Czy mogę na początku wdrożenia nie angażować produkcji?
Aby TPM został poprawnie wdrożony, niezbędne jest zaangażowanie działu produkcji. Ważne, aby odpowiednio wcześnie informować osoby, których wdrożenia będzie dotyczyć w znaczącym stopniu.
Od czego zacząć wdrożenie TPM?
Najlepiej zacząć od wizji. Warto zadać sobie pytanie: jak nasz zakład ma wyglądać po wdrożeniu systemu TPM? Następnym krokiem jest zastosowanie metody 5S. Ważne, żeby zrobić to całościowo, samo uporządkowanie nie wystarczy. W późniejszych etapach można rozpocząć pracę na poszczególnych filarach, aż do osiągnięcia pożądanego celu.
Jak radzić sobie z oporem pracowników związanym z TPM?
Ważne jest jasne i czytelne komunikowanie idei wdrożenia zarządzającym wszystkich szczebli. Założenia TPM, które chcemy wprowadzić muszą być wyjaśnione w sposób zrozumiały. Wszelkie niedomówienia lub niedokładnie przedstawione kwestie mogą wywoływać opór. Warto przeprowadzić wstępne szkolenia przekazujące idee TPM wszystkim pracownikom.
Czy mogę wdrożyć TPM bez systemu CMMS?
System CMMS pomaga w wielu aspektach wdrożenia TPM, ale nie jest jego obowiązkowym punktem.