Wywiady
Podróż do Fabryk Przyszłości – wywiad z Paulem Peetersem, ekspertem ADMA
Podróż do Fabryk Przyszłości – wywiad z Paulem Peetersem, ekspertem ADMA
Factories of the Future (Fabryki Przyszłości) to temat, o którym ostatnio coraz więcej słyszymy w kontekście Przemysłu Przyszłości. Wiąże się on z poszukiwaniem najlepszej drogi do tego, aby przenieść swoją produkcję/ fabrykę na wyższy, bardziej konkurencyjny, a równocześnie zrównoważony, poziom. Paul Peeters, ekspert w zakresie europejskiej metodologii ADMA, opowiada o tym, jak w Belgii powstają mapy drogowe do Fabryk Przyszłości i co zrobić, aby taką zastosować na gruncie polskim. To propozycja skierowana przede wszystkim do firm z sektora MŚP.
Renata Poreda, ASTOR: Każda podróż zaczyna się od pierwszego kroku. Jak zaczęła się Pańska droga do Fabryk Przyszłości?
Paul Peeters: Moja zawodowa droga od zawsze związana była z przemysłem. 20 lat pracowałem w firmie Philips Electronics, w wielu fabrykach w Belgii i Holandii. Stąd mam wiedzę jak wyglądają procesy w fabrykach od tej praktycznej strony. Obecnie, od ponad pięciu lat pracuję w AGORII, gdzie jestem kierownikiem programu Factories of the Future oraz koordynatorem ogólnoeuropejskiego badania ADMA, które pomaga fabrykom w wyzwaniom w transformacji do Przemysłu Przyszłości.
Jak rozszyfrować skrót ADMA?
ADvanced MAnufacturing, to badanie, którego celem jest pomoc fabrykom z sektora MŚP (ang. SME’s – Small and Medium Enterprises sector) w transformacji do Fabryki Przyszłości. Opracowaliśmy całą metodologię, dzięki realizacji której fabryka osiąga pewien stopień dojrzałości w określonych obszarach. W naszym przypadku siedmiu.
Są one odpowiedzią na pytania o to, jak stworzyć zrównoważoną przyszłość dla firm produkcyjnych, gdzie wyzwaniem są wysokie koszty produkcji i globalna konkurencja? Jakie technologie wprowadzić, aby firmy produkcyjne stały się fabrykami nowej generacji o bardziej konkurencyjnej, zrównoważonej i nowoczesnej produkcji? I jak bardzo potrzebne jest przygotowanie całej strategii innowacji? Nasze badanie pomaga znaleźć odpowiedzi albo przynajmniej pobudzić do ich szukania.
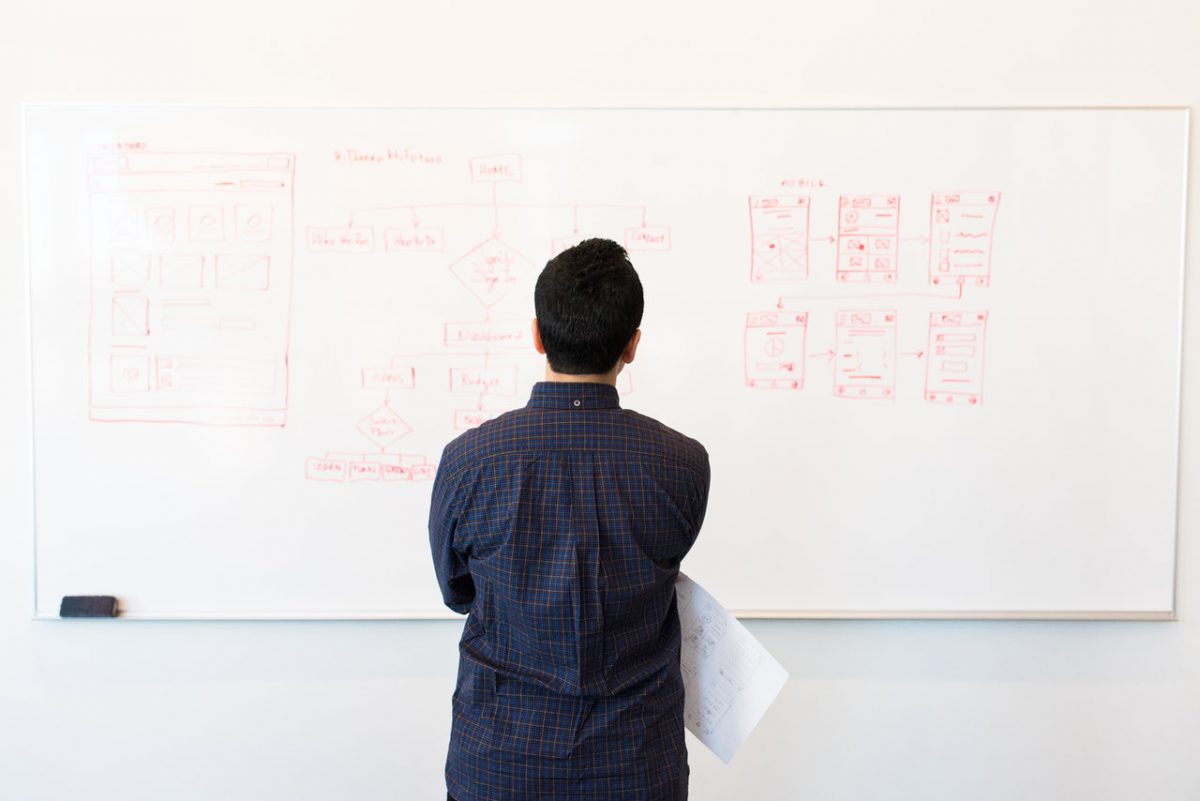
Wróćmy na chwilę do genezy idei Fabryki Przyszłości. Od kiedy funkcjonuje ona w Belgii?
To bardzo dobre pytanie, ponieważ ludzie zawsze pytają mnie, skąd pomysł na opracowanie takiego badania (red. ADMA). Właściwie zaczęliśmy od mapy drogowej (Road Map) Fabryki Przyszłości od EFFRA (The European Factories of the Future Research Association), które jest stowarzyszeniem non-profit nastawionym na wspieranie przemysłu, promującym rozwój nowych i innowacyjnych technologii w zakresie procesów produkcyjnych. Jest oficjalnym przedstawicielem sektora MŚP w programie Factories of the Future.
Myślę, że sam koncept powstał na przełomie 2007 i 2008 roku, kiedy do fabryk na świecie coraz mocniej zaczęła wkraczać technologia i kiedy wiadomo było, że potrzebny będzie jakiś drogowskaz jak sobie radzić tak z (r)ewolucją rynku wytwarzania jak i technologii, które te procesy miałyby wspierać.
To było jeszcze zanim Klaus Schwab powiedział o „czwartej rewolucji przemysłowej” podczas pamiętnego Światowego Forum Ekonomicznego, prawda?
Rzeczywiście. W tym czasie Europa miała już kilka dobrych pomysłów/inicjatyw mówiących o dziejącej się tu i teraz technologicznej rewolucji i potrzebie zmiany. Stąd, kiedy zapoznaliśmy się z koncepcją budowania map drogowych dla Fabryk Przyszłości, zaczęliśmy jako AGORIA adaptować tę mapę do kontekstu belgijskiego.
Co to oznaczało dla belgijskich firm produkcyjnych?
W Belgii, myślę zresztą, że podobnie jest w Polsce, mamy bardzo dużo fabryk z sektora MŚP. Kiedy zaczynaliśmy myśleć o transformacjach i o tym, co zrobić, żeby wszyscy zainteresowani posługiwali się jednym językiem, powołaliśmy kilka zespołów przejściowych reprezentujących kilka różnych obszarów. Dały one początek 7 transformacjom, które obecnie mamy zawarte w badaniu ADMA.
Nasza praca polegała na różnego rodzaju spotkaniach, rozmowach z liderami firm, podczas których zbieraliśmy informację zwrotną, czy takie podejście ma szansę się sprawdzić, czy naprawdę zaspokaja potrzebę. To był okres, kiedy pracowałem jeszcze w małej fabryce Philipsa w Belgii. Dzięki temu brałem czynnie udział w powstawaniu metodologii badania z perspektywy fabryki. I tak stopniowo opracowaliśmy obszary do transformacji, a potem zaczęliśmy angażować fabryki w ten program.
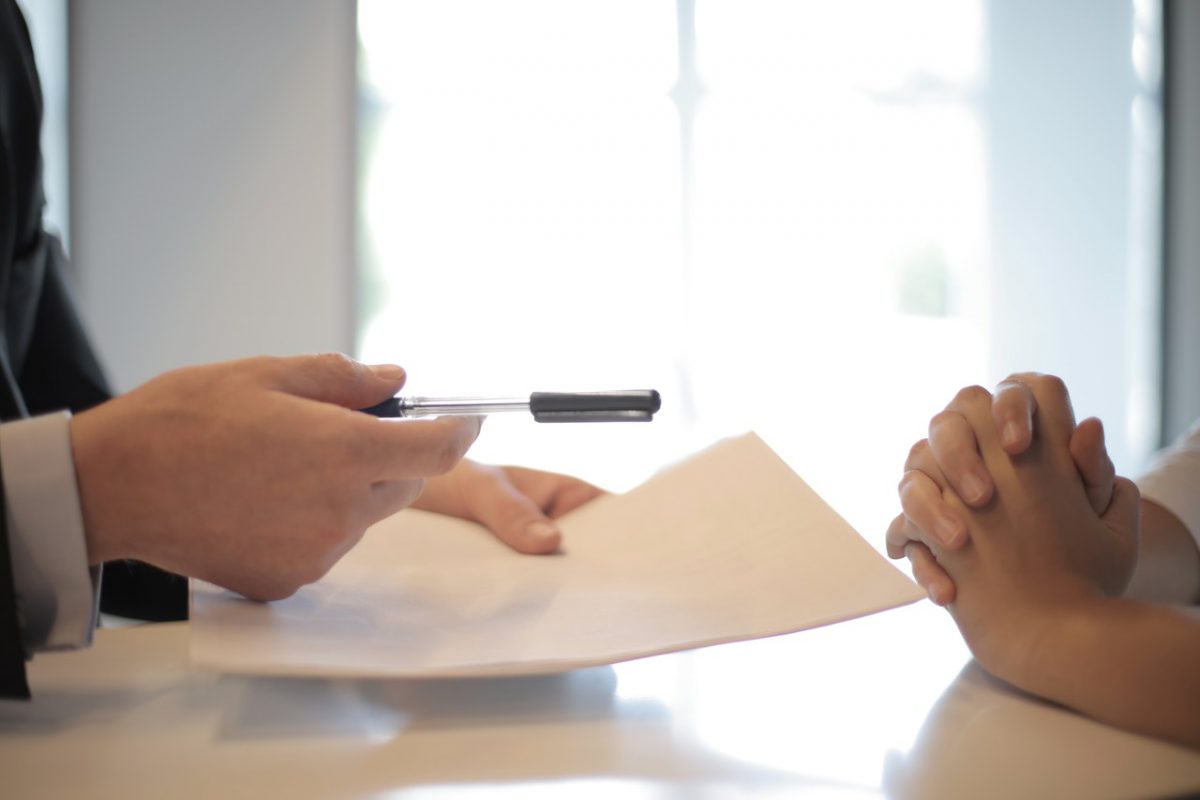
Jakie były największe potrzeby belgijskich fabryk?
Początkowo nasz plan zmiany obejmował same technologie. Tym bardziej, że w tamtym czasie (2008/2009 r.), druk 3D zaczynał już nabierać znaczenia. Coraz więcej mówiło się o robotyzacji. I oczywiście było to bardzo ważne. Coraz częściej jednak, i to z różnych firm, zaczęliśmy dostawać pytania o tzw. czynnik ludzki. Szefowie w fabrykach pytali: „co stanie się z moimi ludźmi”, „jak mam przygotować moich ludzi do tej zmiany”? Zaopiekowaliśmy się tą kwestią. W centrum jednej z transformacji jest człowiek.
Zaproponowaliśmy też, że będziemy łączyć fabryki, aby mogły wymieniać się doświadczeniami między sobą. Ponieważ już w 2008 roku stało się jasne, że innowacje technologiczne niesamowicie szybko wkraczają do przemysłu i że małym i średnim firmom trudno było samodzielnie za nimi nadążyć, zwłaszcza w sytuacji, kiedy liderzy w fabrykach skupiali się na tym, aby zaspokajać rosnące potrzeby klientów NA JUTRO. Nie starczało im już czasu na to, żeby myśleć o tym, gdzie będzie mój biznes POJUTRZE. Stąd nasza propozycja, aby przygotowanie do transformacji powierzyć ekspertom, którzy pomogą w opracowaniu strategii na przyszłość. W latach 2009-2010 pracowaliśmy już metodologią 7 transformacji we Flandrii (północna część Belgii). Nasza praca zaczęła przynosić dobre efekty. Do tego stopnia, że stworzony został rządowy program w oparciu o siedem transformacji.
Ile fabryk w Belgii jest zaangażowanych w transformację do Fabryki Przyszłości?
Obecnie mamy w Belgii 32 Fabryki Przyszłości. Mogą one posługiwać się mianem Factory of the Future. To jest jednoznaczne z tym, że fabryki te zostały poddane audytowi w siedmiu obszarach transformacji. Następnie eksperci z AGORIA udali się na halę produkcyjną i ocenili poziom dojrzałości cyfrowej. Wspomniane 32 fabryki otrzymały nagrodę w ciągu ostatnich pięciu lat, ale ponad 800 MŚP jest w trakcie transformacji przy współpracy z organizacjami wspierającymi, takimi jak ASTOR, Centra Technologiczne, czy Biura Transferu Technologii. To jest długa droga.
Metodologia ADMA jest dostępna także w Polsce. Aktywnie dzieli się Pan wiedzą i doświadczeniem z polskimi organizacjami wspierającymi. Do tego grona należy także ASTOR. Miał Pan już możliwość przyjrzeć się naszemu rynkowi. Z Pana perspektywy – co jest największym wyzwaniem polskich firm produkcyjnych?
Polscy producenci są już w dużym stopniu innowacyjni, choć jeszcze mocno poszukujący. Z całą pewnością inwestycje w technologie przyspieszają wraz z przenoszeniem produkcji globalnych firm do Europy Centralnej i Wschodniej, do Czech, do Rumunii, do Polski. Wiąże się to z ogólnoświatową potrzebą większej elastyczności w produkcji i rozpoczęcia tejże produkcji o wiele bliżej klientów końcowych.
Kiedy patrzę na polską branżę produkcyjną w sektorze MŚP, widzę wiele analogii do Belgii sprzed dobrych kilku lat. Chodzi o wspomnianą lokalną elastyczność oraz potrzebę integrowania jak największej ilości różnych technologii, aby takie działanie było możliwe. Dlaczego? Ponieważ jeśli tego nie zrobisz, w pewnym momencie możesz zakończyć działalność.
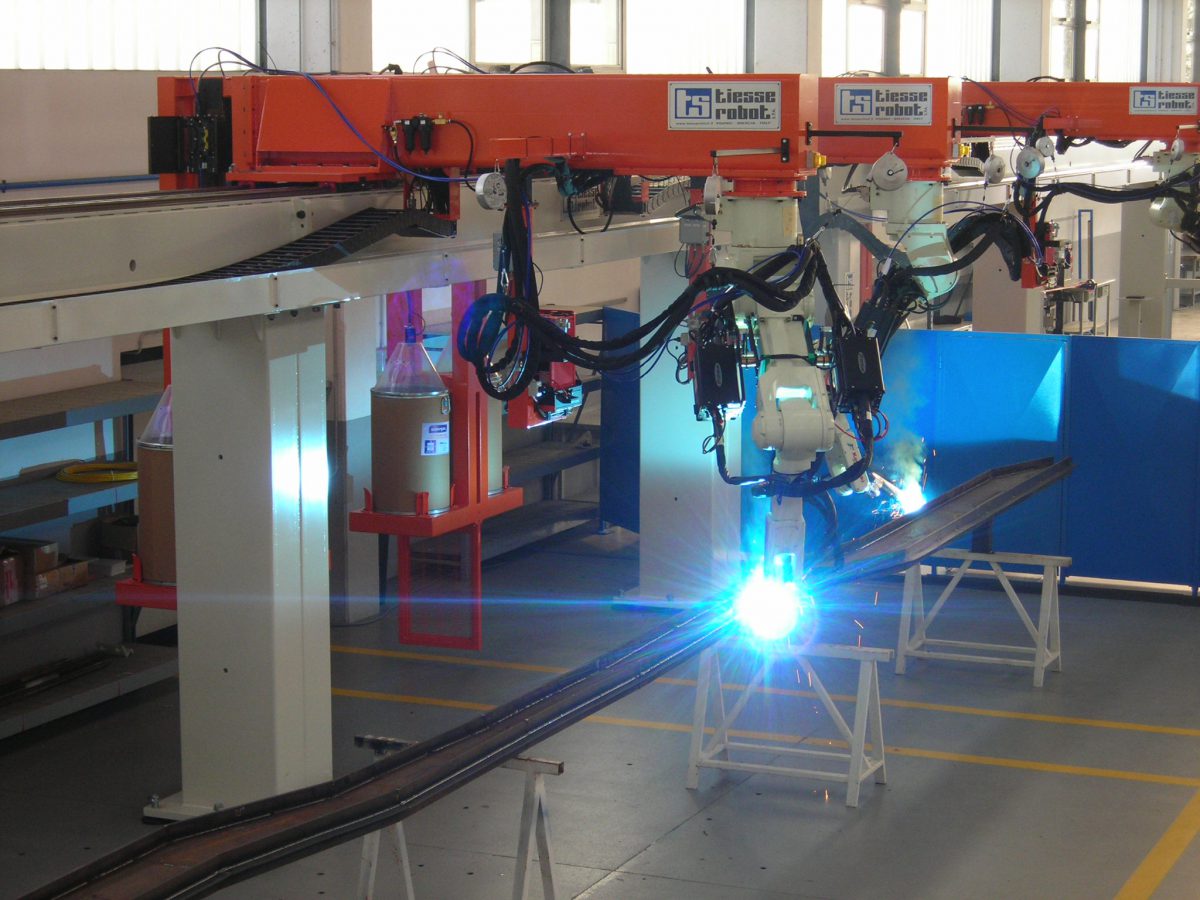
Czy zna Pan przykłady takich fabryk w Polsce?
Nie odwiedziłem osobiście wielu fabryk. Byłem w Vigo (Vigo System SA, producent m.in. detektorów), co zrobiło na mnie ogromne wrażenie poziomem zaimplementowanych technologii. I jest to bardzo dobry kierunek. Jestem przekonany, że dla polskich firm teraz jest czas na program innowacji. Metodyka ADMA może być bardzo pomocna w diagnozie i zbudowaniu strategii. Stąd, z pomocą organizacji wspierających, chcemy pokazać cały program oraz fabryki, które przeszły tę drogę. Drogę do Fabryki Przyszłości.
Słowem, potrzebujemy wdrożyć innowacje, aby być bardziej konkurencyjnym także na globalnym rynku?
Tak. Oczywiście. W pierwszym kroku ważne jest to, co dzieje się lokalnie. Ale wiele firm w momencie, kiedy zaczynają swoją podróż do transformacji w kierunku Fabryk Przyszłości dzięki innowacjom, w pewnym sensie otwiera się na rynek globalny. Widzimy jak wiele naszych belgijskich firm, które otrzymały tytuł Factory of the Future, odnosząc bardzo duże sukcesy w sprzedaży swoich produktów, zaczęły wytwarzać produkty na rynki zagraniczne, te europejskie, a nawet poza Europą.
Świadoma, zaplanowana transformacja przynosi więc wartość dodaną. Nie tylko lokalny wzrost, ale także wzrost na skalę międzynarodową. Tak właśnie było w Belgii. Zaobserwowaliśmy także, że dzięki temu wzrostowi wzrosło zatrudnienie. Wszystkie Fabryki Przyszłości mają obecnie więcej pracowników, chociaż mają wdrożoną robotyzację, digitalizację i automatyzację.
To obala mity, że nowe technologie zabierają pracę. Z drugiej strony zawody, które wcześniej wykonywali ludzie, po prostu przestają istnieć.
Prostym powodem jest to, że dzięki robotyzacji i automatyzacji niektóre zadania wykonawcze na najniższym szczeblu faktycznie zniknęły. W dużym uproszczeniu – pracę tę wykonuje komputer i roboty, które jednak muszą być nadzorowane przez kogoś, kto zna proces. Firmy z wdrożonymi technologiami, odnosząc coraz większe sukcesy na rynku, znacznie poprawiły swoje obroty. Chcąc utrzymać dalszy rozwój biznesu zaczęły zatrudnić więcej osób. Oczywiście to ludzie z nowymi specjalizacjami. Ludzie związani z ICT (z ang. Information and Communication Technologies, Technologie Informacyjno- -Komunikacyjne – TIK) lub inżynierowie procesów.
W Belgii w tym czasie zaszła także duża zmiana już na poziomie kształcenia. Mamy programy, które rzeczywiście wspierają młodzież w podejmowaniu bardziej technologicznych czy związanych z ICT studiów. Dzięki temu już dzisiaj przyszli inżynierowie są bardziej przygotowani do zawodów, które będą potrzebne w przyszłości.
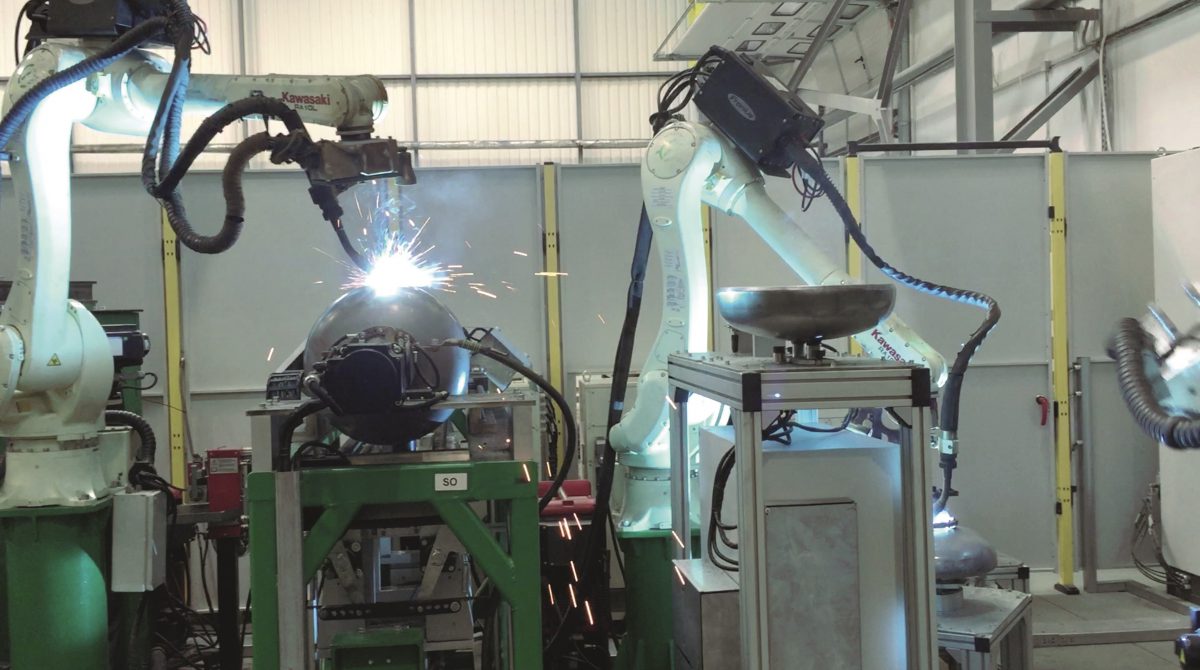
Sprawa nie jest banalna, ponieważ nie chodzi tylko o zmianę zawodu. Nauczenie się nowych rzeczy to także ogromna transformacja mentalna, prawda?
Ma Pani na myśli ludzi w fabryce? Tak. Zawsze podkreślamy: ludzie muszą używać swoich umysłów znacznie bardziej niż rąk. Znam wiele fabryk, w których ludzie musieli wykonywać dużo pracy fizycznej. Niedawno byłem w Bułgarii, gdzie odwiedziłem wiele fabryk o wciąż wysokiej proporcji siły roboczej do zautomatyzowanych procesów. Widziałem jak panie, stojąc cały dzień wykonywały bardzo nużące, ciężkie dla nich prace.
Tymczasem cała idea Fabryk Przyszłości polega na tym, aby operacje, które mogą być wykonywane przez roboty lub automaty, były przez nie realizowane. A twoi ludzie niech pracują umysłem. I każda osoba, to nasze silne przekonanie, każdy operator w fabryce ma swoją unikatową wiedzę, bez której roboty i automaty nie będą dobrze pracować. Musimy więc odkryć talenty wszystkich ludzi w naszych fabrykach. Ktoś, kto w przeszłości obsługiwał tylko maszynę, może mieć talent do robienia czegoś innego w przyszłości.
To było moje następne pytanie. Jak odkryć talenty u ludzi, zwłaszcza tych, którzy mówią: „Nie mogę nic więcej, pracuję kilka lat na tym stanowisku. Jak mogę odkryć coś nowego”. Ludzie po prostu nie wierzą, że mogą robić coś innego, prawda?
To, co pomogło naszym fabrykom, to wiedza o tym, że często w organizacji około 20% pracowników ma taki właśnie sposób myślenia. Około 40% załogi to entuzjaści innowacji, którzy zainicjują program wdrażania innowacji taki jak ADMA. Ta grupa powie: „Tak, działajmy. Wchodzę w to”.
Kolejne 40% to grupa, która początkowo nie będzie chciała się zaangażować. Wyzwaniem będzie zmiana sposobu myślenia, ale w pewnym momencie przekonasz ich do tej zmiany. Zwłaszcza w momencie, kiedy przyjdą pierwsze efekty od 40% przekonanych. Kolejnym krokiem jest przekonanie wspomnianych 20%, z których do zmiany uda ci się przekonać połowę załogi. I zostaje 10% załogi, których nie uda się przekonać do nowego sposobu myślenia, działania. I tak, widzieliśmy firmy żegnające się z tymi ludźmi, niestety.
Czy to jeden z siedmiu etapów transformacji w tworzeniu mapy drogowej do Fabryk Przyszłości?
Tak, nazywamy to „transformacją organizacji zorientowanej na człowieka”, w której ważne jest zbudowanie planu rozwoju dla każdego pracownika. Są tutaj zawarte wskazówki na temat tego, co pracownicy powinni wiedzieć o zmianie, co mogą zrobić dzisiaj, by móc działać w przyszłości i jak zbudujemy program edukacyjny, program szkoleniowy, aby na tę przyszłość być przygotowanym. To rzeczywiście podstawa jednej z transformacji.
Sporo obecnie, także w Polsce mówimy o humanistycznym, skoncentrowanym na człowieku zarządzaniu. Jak zatem pogodzić zarządzanie skoncentrowane na człowieku z transformacją technologiczną? W jaki sposób zaspokoić potrzeby pracowników?
Cieszę się, że także w Polsce jest to ważny temat. W tym sensie zawsze odróżnialiśmy się od fali „The Big Industry 4.0” w Niemczech. Widzieliśmy dwie wady Industry 4.0 w Niemczech. Po pierwsze: to program bardzo zorientowany technologicznie. Słowo „człowiek” w pierwszym opracowaniu dotyczącym Przemysłu 4.0 pojawiło się tylko dwa razy. W 400-stronicowym dokumencie. Tak więc w pierwszym podejściu nie zwracano uwagi na człowieka.
W Belgii robiliśmy to od samego początku, ponieważ nasi liderzy w fabrykach poprosili nas o przyjęcie tego bardziej skoncentrowanego na człowieku podejścia. Drugą rzeczą, której Przemysł 4.0 nie miał, było skupienie się na firmach z sektora MŚP. Przemysł 4.0 w Niemczech zaczął się od dużych fabryk, takich jak Porsche, Audi, Volkswagen. Firm dużych o globalnym zasięgu. W Belgii, podobnie jak w Polsce mamy większość firm MŚP, więc od samego początku musieliśmy budować nasz program, którego celem jest pomoc MŚP. To dwie duże różnice.
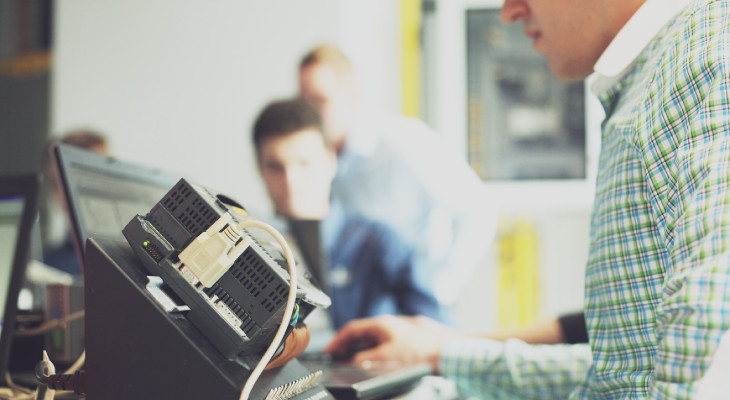
Tak, to ogromna różnica. ASTOR od ponad sześciu lat definiuje, gdzie technologia spotyka człowieka. Mamy przekonanie, że technologia nie istnieje bez ludzi.
Widzę wiele podobieństw między Belgią a Polską. I myślę, że podejście, które proponuje ADMA, jest dokładnie tym, jak chcemy działać. W naszej metodologii mamy 4 z 7 transformacji, które moglibyśmy nazwać raczej technicznymi, technologicznymi: zaawansowane technologie produkcyjne, mamy kompleksową inżynierię, mamy cyfrową fabrykę, mamy inteligentną produkcję. Kolejne 3 zorientowane są na człowieka, jego otoczenie (działania proekologiczne) i zrównoważony rozwój. W tym sensie myślę, że mamy równowagę – połączenie innowacji z ludźmi.
Na zakończenie naszej rozmowy proszę powiedzieć, jak w 4 krokach rozpocząć cyfrową transformację?
Pierwszą rzeczą, którą mówimy przedsiębiorcom, jest: „Najpierw popraw swoje podstawy”. Jeśli zamierzasz zdigitalizować złe procesy, one nadal będą złe. Mówimy więc: najpierw upewnij się, że twoje procesy produkcyjne, procesy inżynieryjne usprawniają. Usiądź z ludźmi i zmapuj swój proces: czy jest on zorientowany na przyszłość, czy będzie w stanie odpowiadać na trendy przez najbliższe 5–10 lat. Jeśli nie, najpierw musisz nad tym popracować.
Następnie mówimy: „określ swoje pola bitew”. To oznacza szybkie wygrane. Na czym to polega? Na znalezieniu słabych punktów, które w miarę łatwo przepracować, zaimplementować, po to, by wzbudzić w ludziach motywację do zmiany, by powiedzieć „Hej, to już się dzieje”. A potem krok trzeci – zbuduj mapę drogową, aby w kroku czwartym, do projektów związanych z transformacją i wynikających z planu działania dobrać właściwych ludzi, którzy będą potrafili ze sobą współpracować. Współpraca bowiem to jeden z determinantów sukcesu.
Czas więc rozpocząć podróż?
Tak. I mam nadzieję, że uda nam się zaprosić do niej coraz więcej liderów MŚP. Przekształcenie firmy nie przychodzi łatwo, ale finalnie nagroda jest dość atrakcyjna. Moją motywacją do działania jest to, aby na poziomie europejskim wdrożyć jednolity sposób pomiaru dojrzałości fabryk. To moja osobista ambicja. Chciałbym, aby przyznany tytuł Fabryka Przyszłości, w całej Europie rozumiany był tak samo i oznaczał fabrykę, która ma za sobą transformację w 7 obszarach.