Treści
Planowanie produkcji – do sukcesu pierwszy krok

Planowanie produkcji – do sukcesu pierwszy krok
Brian Tracy mówił, że „Korzyści płynące z dobrego planowania są ogromne. Szacuje się, że każda minuta poświęcona na planowanie pozwala zaoszczędzić dziesięć minut pracy”. Sfera produkcyjna nie jest wyjątkiem – tak jak w każdym procesie, tutaj również potrzebny jest plan, który wprowadzi do istniejącego chaosu odrobinę porządku i pozwoli ułożyć go w logiczny ciąg zdarzeń.
Co się dzieje, gdy przedsiębiorstwo nie ma planów produkcyjnych?
Jedna z definicji planowania wspomina, że „gdy nie ma systemu planowania, poszczególne czynności są wzajemnie izolowane i podejmowane w sposób spontaniczny, co może być ryzykowne dla przedsiębiorstwa”. Najczęściej odbywa się to w ten sposób, że w wyniku działań sprzedaży występuje potrzeba szybkiego wytworzenia produktów. Jeśli przedsiębiorstwo ma bardzo ograniczony asortyment, to zapewne „da radę”.
W przypadku większego zróżnicowania oferty zaczynają się schody. Czy mamy surowiec do wyprodukowania? Kiedy mamy to zrobić? Kto to ma zrobić? Jak to mamy zrobić? Nie możemy zrobić takiej małej ilości, bo to jest technologicznie niemożliwe? Co zrobić z pozostała częścią? To tylko część pytań, które pojawiają się w otoczeniu produkcji.
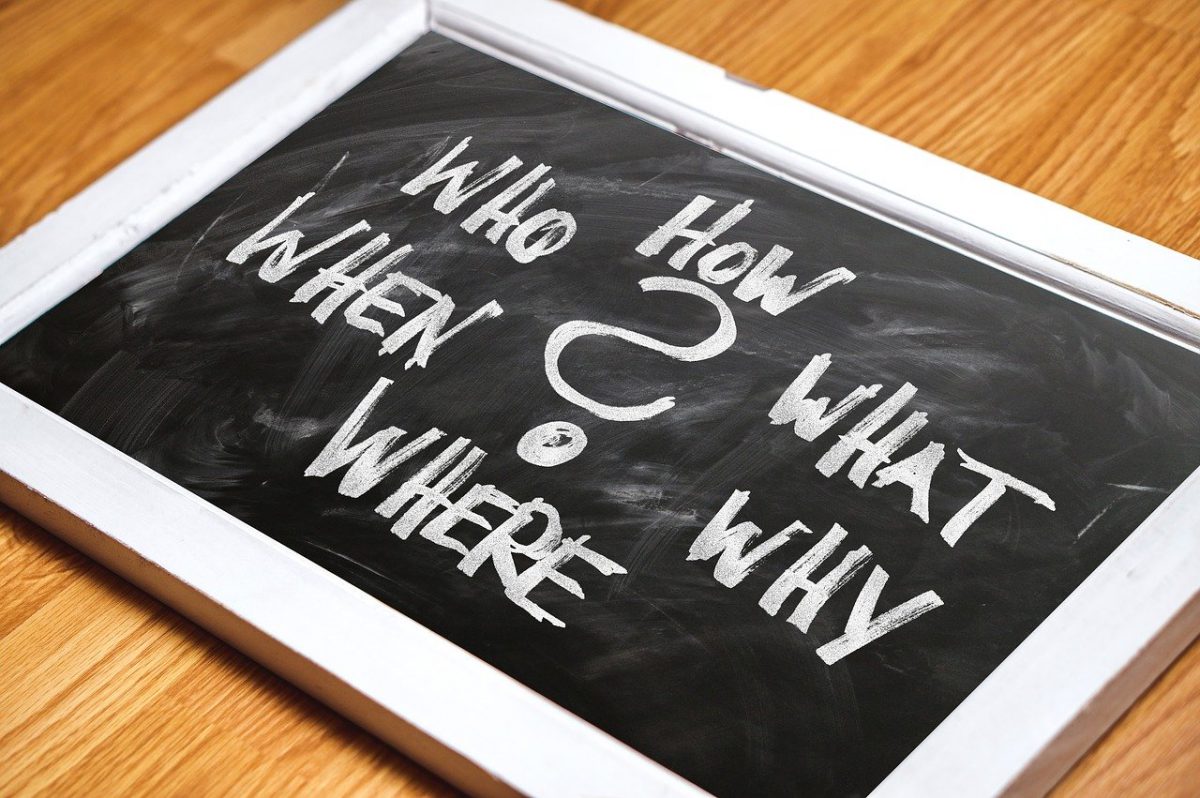
Aby zaplanować, trzeba wiedzieć
Wbrew swojej nazwie planowanie produkcji w zdecydowanej mierze zakotwiczone jest poza obszarem hali produkcyjnej. Jest ono związane ze strategią działań całego przedsiębiorstwa i jest powiązane z szeregiem innych procesów, a przede wszystkim celów organizacji.
Nie jest możliwe przygotowanie planu produkcyjnego bez uwzględnienia trendów sprzedażowych czy planów marketingowych. Im dłuższy horyzont planowania, tym bardziej istotne jest ich uwzględnienie. W tej formie planowanie produkcji to złożony proces podporządkowany strategii biznesowej. A to już bezpośrednio prowadzi do chyba najmniej docenianego, a zarazem do najbardziej istotnego elementu – prognozy popytu. Z prognozy popytu powstają szczegółowe plany sprzedaży, które są bezpośrednim wsadem dla procesu planowania produkcji.
Zanim pochylimy się nad stworzeniem planu, kilka definicji:
Dane indeksowe – zawierają najważniejsze informacje o produkcie, takie jak:
- numer towarowy (item number)
- opis
- jednostkę miary
- kategorie produktowe, sprzedażowe, marketingowe
- czas realizacji (Lead Time)
- wytwarzany / kupowany
- zapas bezpieczeństwa (Safety Stock)
- koszt
- indeksy nadrzędne, agregujące
- klasyfikacje np. ABC, XYZ
- preferowany dostawca / wytwórca
Dodatkowo powinny zawierać informacje:
- Co to jest?
- Skąd pochodzi? Gdzie jest zlokalizowane?
- Jak to kontrolujemy / zarządzamy?
- Ile kosztuje?
- Czy to kupujemy, czy produkujemy?
- W jakich ilościach zamawiamy?
- Jak długo musimy na to czekać?
- Czy jest to materiał, surowiec, półprodukt, wyrób gotowy, towary czy część zamienna?
BOM – struktura wyrobu (Bill of Materials) – definiowana jest jako:
- lista wszystkich komponentów (półprodukty, części, materiały) potrzebnych dla złożenia finalnego wyrobu wraz ze wskazaniem ilości każdego komponentu na wyrób finalny,
- w produkcji procesowej określany jako lista składników potrzebnych do rozpoczęcia procesu produkcyjnego; czasami nazywana także potocznie recepturą lub formułą.
BOM może być jedno- lub wielopoziomowy
Marszruta – definiowana jest jako:
- kolejka operacji niezbędnych do wykonania, aby wyprodukować finalny produkt, wraz z ich prawidłową sekwencją, przypisaniem zasobów do zużycia (maszyna, człowiek, materiał – BOM) oraz czasami realizacji.
LT – czas realizacji (lead time) definiowany jest jako:
- okres czasu niezbędny do realizacji operacji lub listy operacji w celu zaspokojenia zdefiniowanej potrzeby.
Matryca przezbrojeń – jest to zdefiniowana tablica określająca, jakie produkty są możliwe do wykonania na danej maszynie oraz zawiera czasy niezbędne do przestawienia produkcji z jednego wyrobu na inny. Przykładowo w przypadku lakierowania czas przezbrojenia z wyrobów jasnych na ciemne zwykle jest krótszy niż w przypadku produkcji wyrobów jasnych po ciemnych.
Horyzont planowania – to okres czasu, na jaki plan produkcji wykracza w przyszłość:
• zazwyczaj określany jako całkowity czas realizacji powiększony o czas wykonania partii produkcyjnych komponentów, a w przypadku planowania wykraczającego daleko w przyszłość także czas niezbędny dla zmiany zdolności wytwórczych kluczowego stanowiska pracy.
Aby zaplanować, trzeba mieć wspólnie określony cel
Klasyczna definicja planowania produkcji wprowadza konkretnych uczestników procesu:
W procesie uczestniczą trzy osoby:
- Dyrektor ds. planowania produkcji – wykształcenie wyższe z zakresu logistyki lub dziedzin pokrewnych, umiejętności z zakresu obsługi komputera, przynajmniej 3-letnie doświadczenie w zawodzie, praca na podobnym stanowisku.
- Analityk ds. planowania produkcji – wykształcenie wyższe z zakresu logistyki lub dziedzin pokrewnych, umiejętność biegłej obsługi komputera, 2-3-letnie doświadczenie w zawodzie.
- Pracownik ds. planowania produkcji – wykształcenie wyższe z zakresu logistyki lub dziedzin pokrewnych, umiejętność obsługi komputera, praca na podobnym stanowisku wcześniej przynajmniej przez rok.
W przypadku nowoczesnych przedsiębiorstw planowanie produkcji przestaje być sportem indywidualnym, a staje się konkurencją drużynową z wymierną rolą trenera, którym jest przedstawiciel Senior Managementu (dyr. handlowy, dyr. marketingu, dyr. operacyjny, dyr. finansowy, dyr. produkcji).
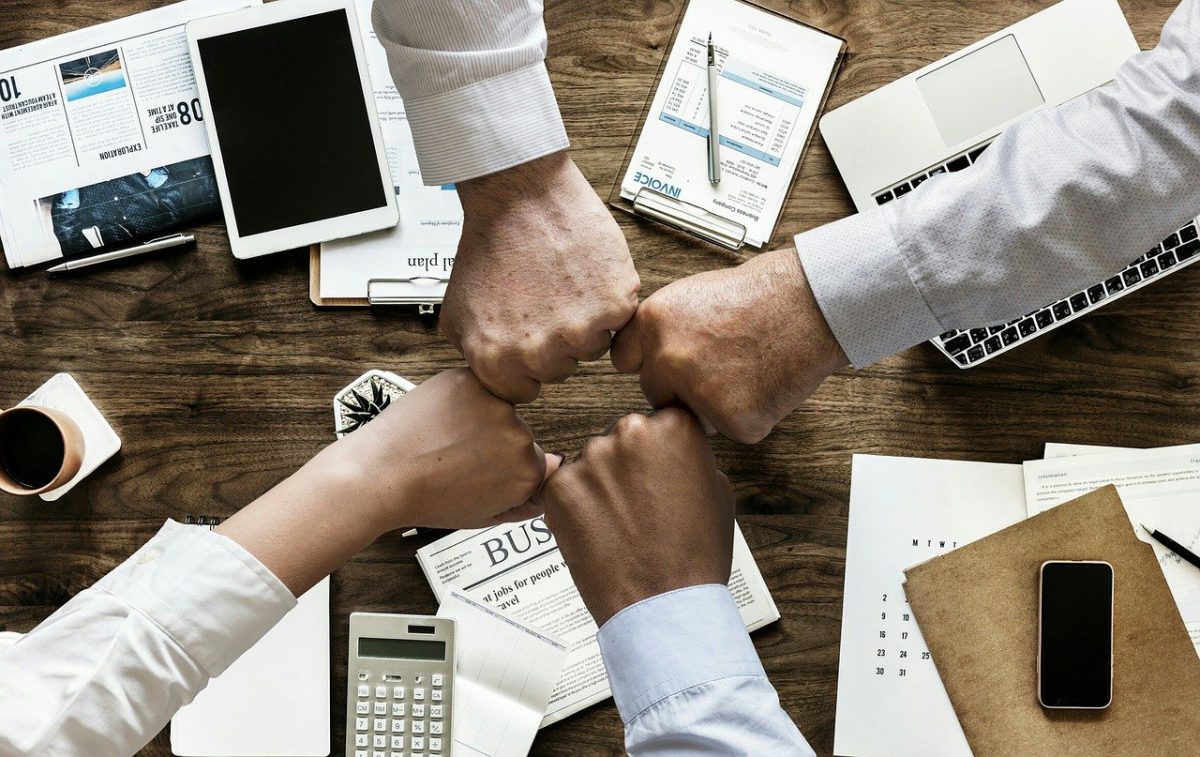
W skład tej drużyny wchodzą przedstawiciele wszystkich działów związanych z Łańcuchem Dostaw: Sprzedaż, Finanse, Zakupy, Planowanie, Transport, Magazyny i Produkcja.
Bardzo ściśle są też zdefiniowane reguły, według których poszczególne działy firmy na kolejnych etapach procesu planowania dokładają swój wkład w jego powstanie. Reguły te tworzą jedną z idei procesu planowania, zwaną planowaniem zintegrowanym. Polega ona właśnie na zaangażowaniu poszczególnych działów przedsiębiorstwa w tworzenie i wdrażanie wspólnych, powiązanych ze sobą planów. Działanie to ma na celu realizację strategii całej firmy, nie zaś pomniejszych interesów poszczególnych komórek firmy.
Kluczową rolę w tym procesie pełni komunikacja. Bardzo dobrym narzędziem udrażniającym kanały komunikacji jest S&OP (Sales & Operations Planning). Jest to proces polegający na zbilansowaniu potrzeb rynkowych przedstawionych w postaci planu sprzedaży oraz możliwości operacyjnych, które dla odmiany określa plan operacyjny. Plan, który powstaje w wyniku S&OP jest planem najczęściej długookresowym (1-3 lata) w podziale na duże okresy czasu, np. miesiąc, i jest on tworzony dla grup produktów bez podziału na poszczególne wyroby – indeksy.
Strategia dobrze dobrana
Mając już wszystkich uczestników procesu oraz wprowadzone istotne pojęcia, możemy przystąpić do opracowania planu produkcji. Nie ma jednej uniwersalnej metody, a to, jak ten plan będzie wyglądał, w dużym stopniu zależy od tego, jaką strategię produkcji ma dany zakład.
W dużym uproszczeniu możemy wyznaczyć cztery podstawowe strategie produkcyjne:
1. ETO (Engineer-to-Order) – projektowanie na zamówienie (czasami określane jako Project/Design-to-Order):
- produkt jest niepowtarzalny,
- projekt wykonywany jest dopiero po otrzymaniu zamówienia, co powoduje długie czasy realizacji.
2. MTO (Make-to-Order) – wykonywanie na zamówienie:
- duża różnorodność produktów, uzależniona od zamówień klienta,
- wyroby gotowe w dużej mierze dedykowane są konkretnemu klientowi,
- zakup materiałów w zależności od specyfiki następuje po wpłynięciu zamówienia lub podlega zasadom zarządzania zapasami (w oparciu o zużycia historyczne),
- wymaga dużej tolerancji na czas realizacji zamówienia przez klienta.
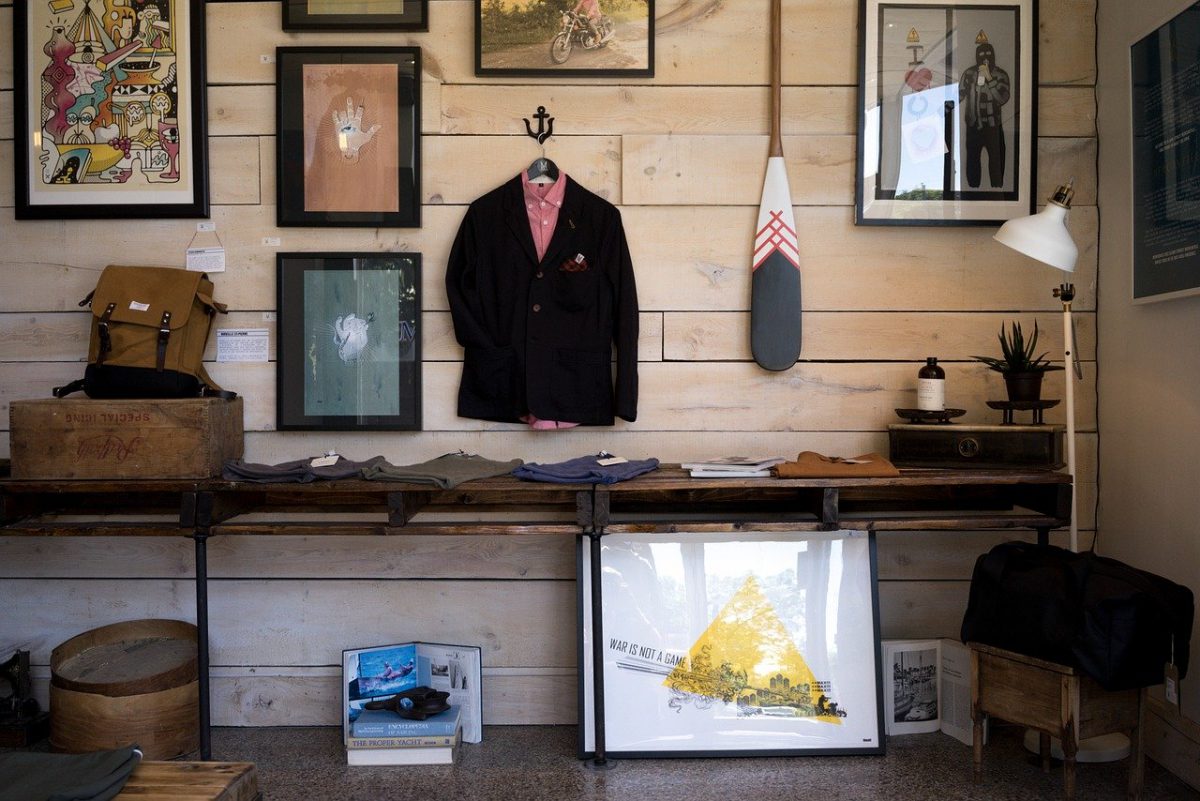
3. ATO (Assemble-to-Order) – montaż na zamówienie:
- opiera się na produkcji najważniejszych podzespołów na zapas i składania finalnego wyrobu dopiero po wpłynięciu zamówienia,
- możliwa przy dużej standaryzacji komponentów,
- względnie szybki czas realizacji zamówień,
- pojawia się ryzyko komponentów niskorotujących lub zbędnych.
4. MTS (Make-to-Stock) – produkcja na zapas:
- wymagany pewny, stały popyt, a przestawienia produkcji są bardzo drogie lub trudne technologicznie,
- klient wymaga natychmiastowej dostawy i standardowego produktu prosto z półki,
- wymagane jest utrzymanie zapasu wyrobów gotowych, głównie z powodu przechowywania wszystkich wariantów wyrobów gotowych,
- konieczność prognozowania wyrobów gotowych,
- pojawia się ryzyko pozycji niskorotujących lub zbędnych.
Najpierw plan, potem harmonogram
Na podstawie zdefiniowanego w procesie S&OP powstają Plany Sprzedaży i Plan Operacyjny, a docelowo zdefiniowane na poziomie poszczególnych wyrobów powstaje zapotrzebowanie, które zostaje dodatkowo określone w zdefiniowanym terminie dostępności zapotrzebowanie pozwalające na zaspokojenie potrzeb.
Zapotrzebowanie, które otrzymamy zweryfikowane o wyroby dostępne, pozwalają stworzyć Główny Plan Produkcji – MPS (Master Production Schedule). Horyzont planistyczny MPS obejmuje zazwyczaj okres 2 do 3 miesięcy. Plan tworzony jest dla konkretnych wyrobów, zwykle w układzie tygodniowym. Jego główną funkcją jest przygotowanie realnego planu produkcji, uwzględniającego zarówno zapotrzebowanie, jak i zdolności wytwórcze.
Przykładowo:
W kolejnych tygodniach zapotrzebowanie wynosi:
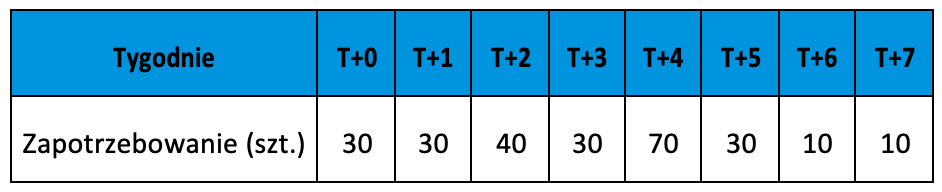
Jeśli w przedsiębiorstwie jest jakiś zapas wyrobu gotowego, to dokonujemy porównania, jaki byłby stan magazynu po zrealizowaniu sprzedaży wg wyznaczonego zapotrzebowania.
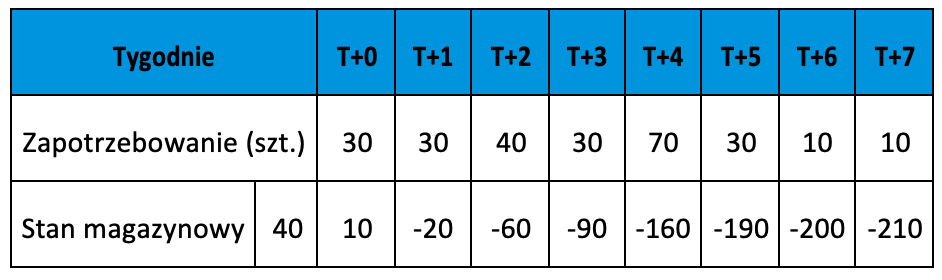
Ustalamy wstępny harmonogram produkcji w taki sposób, aby w żadnym momencie stan magazynowy nie był ujemny. W przypadku zlecenia produkcji mającego wynosić 50 lub wielokrotność 50 sztuk będzie on wyglądał w ten sposób:
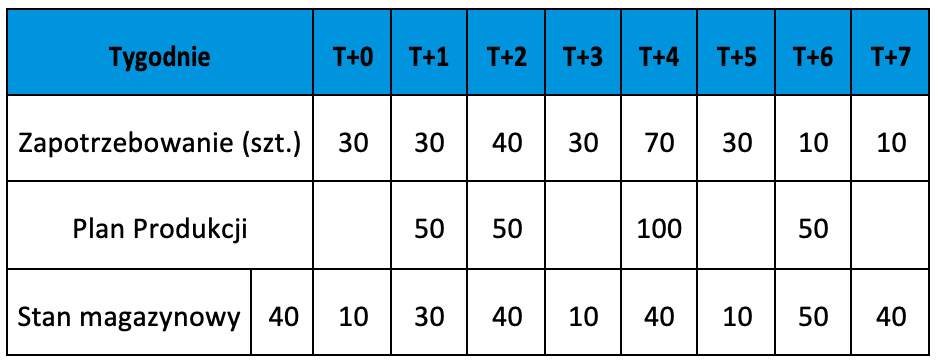
W każdym przedsiębiorstwie istnieją ograniczenia produkcyjne wyznaczające maksymalne zdolności produkcyjne dla danych produktów. Proces porównania wstępnego harmonogramu z ograniczeniami nazywamy zgrubnym planowaniem zdolności – RCCP (Rough-Cut Capacity Planning).
W naszym przykładzie określimy maksymalną zdolność na 50 sztuk i zaplanowana w tygodniu T+4 produkcja wymaga zmiany – produkcja zostaje rozłożona na tygodnie T+3 i T+4.
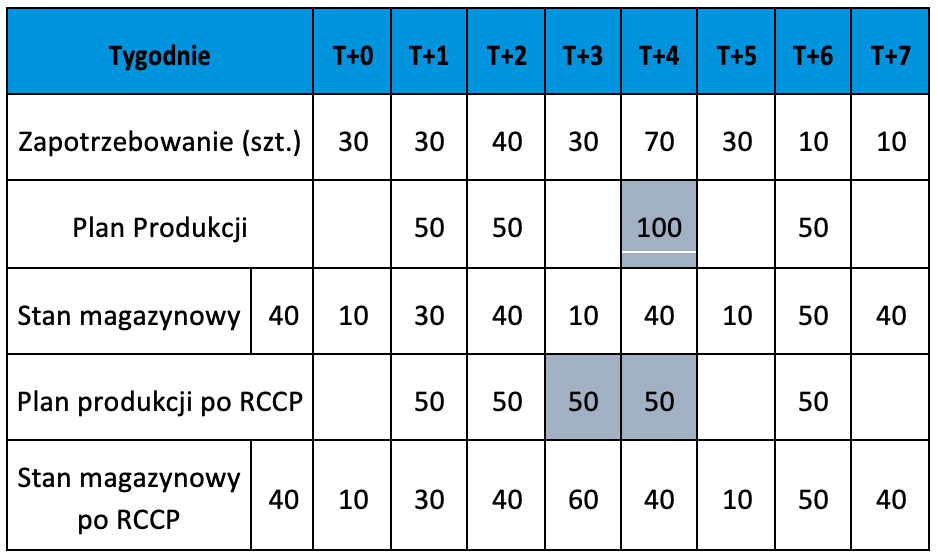
Plan produkcji po RCCP daje nam plan MPS
MPS stanowi w pewien sposób barierę, która pozwala zminimalizować zmiany na kolejnych poziomach BOM.
Plan MPS powinien nam pozwolić na:
- bilansowanie produkcji gotowych wyrobów oraz krytycznych półproduktów i komponentów,
- stabilizowanie zmian i ograniczanie korekt potrzeb materiałowych,
- efektywne planowanie buforów wyrobów gotowych,
- sprawne kierowanie biznesem na poziomie operacji,
- transparentność realizacji zleceń – monitoring „backlog’u”,
- weryfikację planów w oparciu o krytyczne zasoby (RCCP).
Nie można planować produkcji nie mając zapewnionych surowców potrzebnych do produkcji. Następnym etapem jest więc przejście z planu produkcji na zapotrzebowanie materiałowe MRP (Material Requirements Planning) – podobnie jak w przypadku MPS, horyzont planistyczny obejmuje zazwyczaj okres 2-3 miesięcy, ale im dłuższe są czasy realizacji poszczególnych surowców, tym bardziej ten okres jest wydłużany.
Plan tworzony jest dla materiałów i półproduktów, zarówno zakupionych, jak i wytwarzanych. MRP uszczegóławia analizę RCCP, wykonaną na poziomie MPS. Głównym celem MRP jest więc skonkretyzowanie zapotrzebowania na zasoby. Źródłem obliczeń dla ustalania potrzeb materiałowych jest MPS — planowanie odbywa się na jego podstawie.
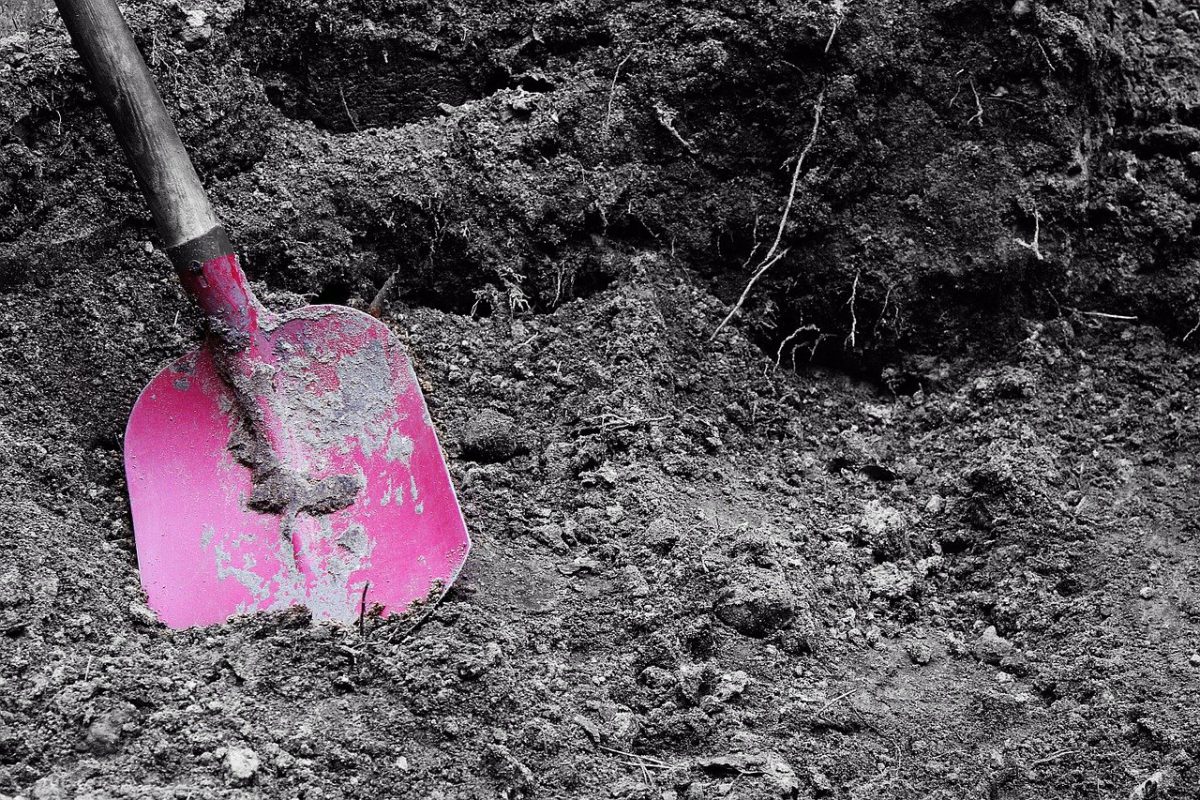
Ostatni etap – stworzenie harmonogramu produkcji
Harmonogram produkcji uszczegóławia powstały plan produkcyjny. Zostaje on rozpisany na poszczególne zmiany, maszyny i zasoby. W harmonogramie uwzględnia się zarówno matryce przezbrojeń, jak i kompetencji. Ustala się kolejność realizacji poszczególnych operacji na poszczególnych maszynach z uwzględnieniem marszrut. Dodatkowo harmonogram produkcji jest wzbogacony o działania kontrolne i monitoring w obszarze produkcji.
Narzędzia wspierające planowanie
Czym bardziej szczegółowy etap powstawania planów produkcji, tym liczba elementów składowych i uwarunkowań staje się większa. Powoduje to, że niezbędne staje się wsparcie narzędziowe tych procesów.
Większość nowoczesnych systemów ERP ma dziś wbudowane moduły Planowania, ERP czy nawet harmonogramowania. W zdecydowanej większości są one jednak ukierunkowane na finansowy aspekt tych procesów.
Szczególnej uwagi wymaga dziś jednak proces harmonogramowania, najlepiej z uwzględnieniem aspektów MRP i MES. W dzisiejszych przedsiębiorstwach jest to najbardziej zindywidualizowane narzędzie. Każdy zakład wygląda inaczej i ma inny park maszynowy.
Wdrożenie systemu harmonogramowania zintegrowanego ze sterowaniem produkcją i zbieraniem informacji kontrolnej z poszczególnych maszyn przy wykorzystaniu ich interfejsów komunikacyjnych na dzień dzisiejszy wydaje się poza zasięgiem zintegrowanych systemów ERP.

Planowanie
- Analiza informacji rynkowych (w tym prognoz)
- Zbilansowanie potrzeb sprzedażowych oraz możliwości operacyjnych firmy – plan produkcji
- Monitoring realizacji zamówień sprzedaży
- Przygotowanie informacji wejściowej dla planowania materiałowego – zaopatrzenie
- Działanie na styku części handlowej oraz operacyjnej
- Zarządzania zapasami wyrobów gotowych
Harmonogramowanie
- Realizacja planu produkcji poprzez zdefiniowanie odrębnych operacji wynikających z marszrut
- Monitoring realizacji operacji produkcyjnych w zakładanych terminach
- Optymalizacja wykorzystania zasobów produkcyjnych – maszyny, ludzie
- Kontrola informacji powstających w obszarze produkcyjnym
- Bieżący monitoring parametrów efektywności jak WIP, czasy realizacji, bufory produkcyjne