Treści
PackML – poznajmy język maszyn
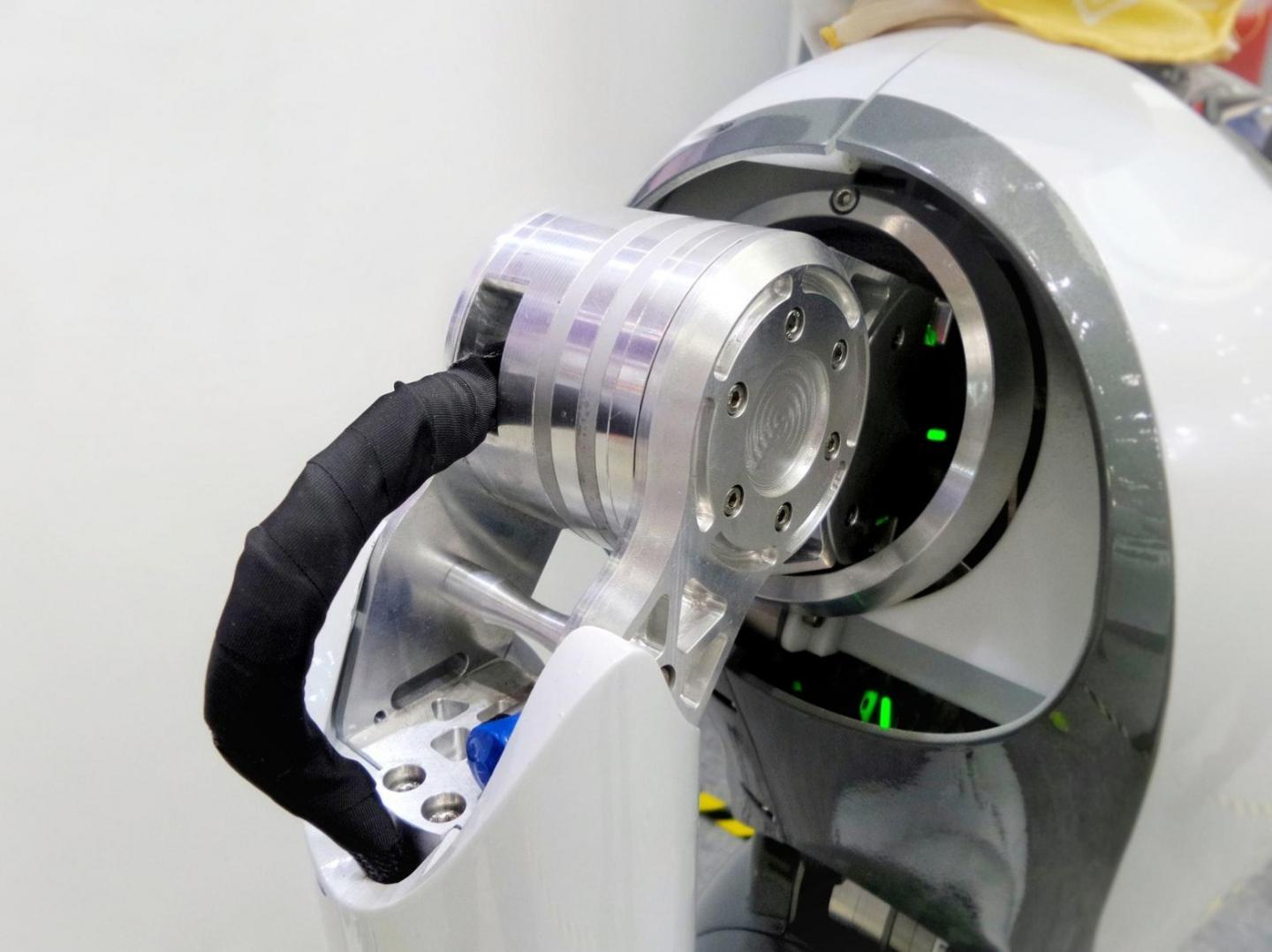
PackML – poznajmy język maszyn
Obserwując nieporozumienia i konflikty powstające między mieszkańcami Białegostoku o różnych narodowościach, Ludwik Zamenhof uznał za ich przyczynę brak wspólnego języka. Dlatego rozpoczął pracę nad stworzeniem, wspólnego, prostego w nauce i neutralnego języka które zaowocowały wydaniem w 1887 roku podręcznika „Język Międzynarodowy”, gdzie zaprezentowany został język dziś znany pod nazwą Esperanto. Podobna idea przyświecała organizacji OMAC podczas opracowywania standardu PackML (Packaging Machine Language).
Problemy komunikacyjne w świecie maszyn, procesów i systemów
Arne Svendsen z Arla Foods, członek organizacji OMAC, porównuje standard PackML do standardu USB w komputerach. Jeżeli wybierzemy się do sklepu i kupimy tam zestaw bezprzewodowy „myszkę wraz z klawiaturą” i podepniemy go do naszego komputera, zadziała ona natychmiastowo i nie będziemy potrzebować żadnej ingerencji czy konfiguracji. Niezależnie jaki to będzie sprzęt: ładowarka, słuchawki, dysk twardy, lampka, jeżeli wyposażone są w złącze USB, biorąc je pierwszy raz do ręki od razu wiemy co z nimi zrobić, jak je podłączyć i nie musimy niczego konfigurować.
Patrząc na nasz zakład produkcyjny z lotu ptaka, możemy wyróżnić kilka poziomów dekompozycji: hale produkcyjnie, w nich linie, składające się z maszyn, które wykorzystuj urządzenia różnych dostawców, kartoniarki dozowniki, paletyzery, drukarki etykiet, dozowniki, zakręcarki. Każda z tych maszyn wykorzystuje komponenty różnych dostawców, silniki, falowniki, komputery przemysłowe, ekrany HMI, każda zaprogramowana jest w inny sposób, posiada inne wizualizacje, inne zmienne itp.
Wiąże się to ze sporymi problemami dla użytkownika końcowego. W pierwszym etapie – przy wdrożeniu i uruchomieniu systemów w zakładzie, które wymaga dodatkowego czasu i zasobów, aby skonfigurować systemy pomiędzy sobą. Następnie w trakcie użytkowania systemu, gdzie utrudnione jest uzyskanie spójnych i przejrzystych danych na temat produkcji, wydłużony zostaje również czas wyszkolenia operatorów oraz utrudnione jest przemieszczanie ich pomiędzy różnymi stanowiskami pracy, na których muszą uczyć się od nowa obsługi danej maszyny.
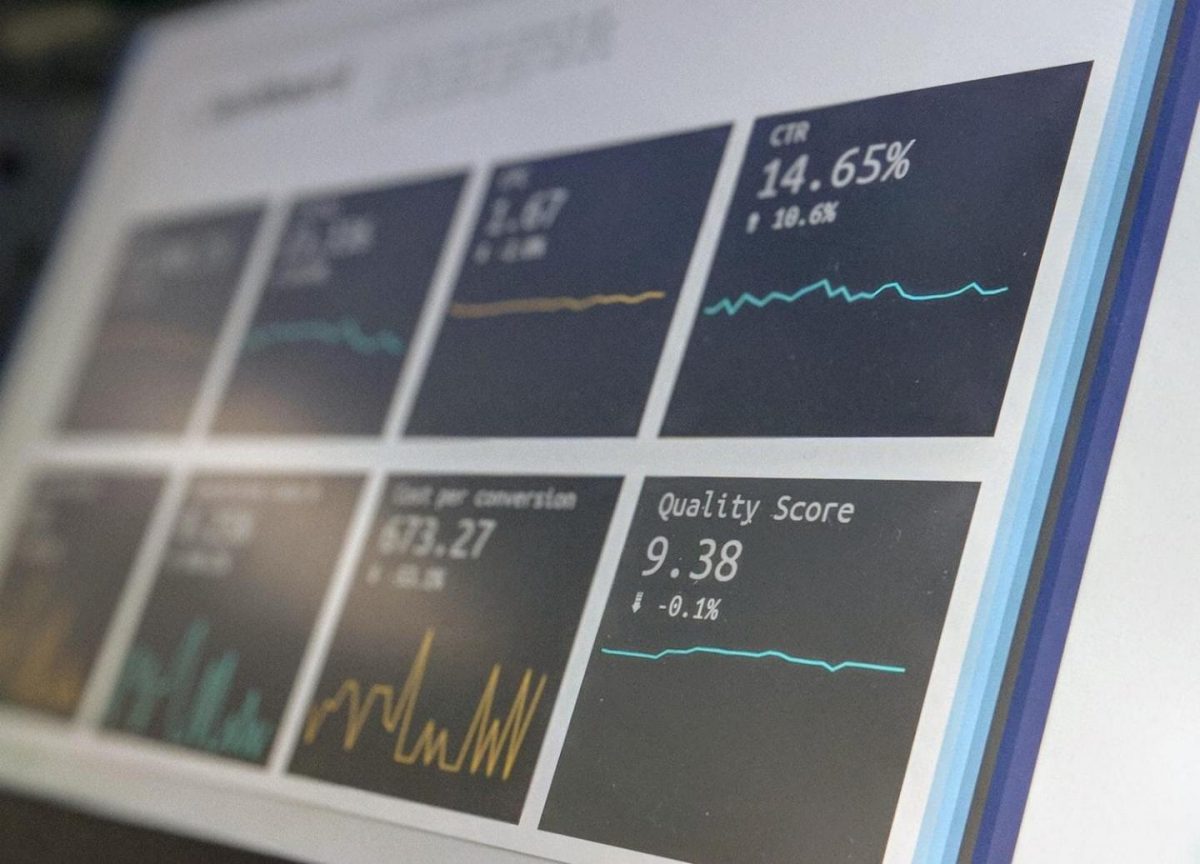
Jeżeli użytkownik posiada kilka zakładów, problem stanowi także wysłanie maszyny z jednego z nich do drugiego. Pomimo, że dana maszyna pracuję już w naszej firmie od kilku lat to w nowym zakładzie musimy wdrożyć ją jak zupełnie nową.
Co więcej, patrząc z perspektywy drugiej strony – producenta maszyn, sytuacja wcale nie jest lepsza. Posiadamy opracowaną maszynę, gotową do implementacji, ale pojawia się u nas End User, który chce, aby była ona wykonana w oparciu o konkretny system sterowania, inny od użytego przez nas, który jest u niego standardem.
Sprawia to, że musimy poświęcić czas, aby na nowo opracować algorytm sterowania i zaimplementować go, zamiast skupić się na poszukiwaniu nowych rozwiązań i innowacji dla rozwoju naszego biznesu i konkurencyjności. Wpływa to również na wydłużenie czasu wdrożenia, generuje większe koszty oraz utrudnia późniejszą diagnostykę przez serwisantów, którzy przyjeżdżając od zakładu, muszą nauczyć się nowego systemu sterowania.
Wyzwania użytkownika końcowego | Wyznania OEM |
– Dynamicznie rozwijające się rynki i coraz większa presja z szybszym prowadzeniem produktu do obrotu – Braki kadrowe, duża rotacja operatorów pomiędzy maszynami – Połączenia w ramach jednej linii produkcyjnej maszyn od różnych dostawców – Zebranie wiarygodnych danych na temat produkcji z maszyn różnych producentów – Brak jasnych informacji o przyczynie awarii | – Poświęcanie czasu na „przeprogramowanie” istniejącej maszyny zamiast budowie innowacji dla konkurencyjności – Długi czas wyszkolenia serwisantów we wszystkich używanych systemach sterowania – Konieczność budowania przewagi konkurencyjnej przez wprowadzanie innowacji |
Czym jest PackML?
W odpowiedzi na te wyzwania, organizacja OMAC, w skład której wchodzą czołowi dostawcy komponentów do budowy maszyn, użytkownicy końcowi oraz OEM, opracowała standard PackML. Jako podstawa pod opracowanie standardu wykorzystana została norma ISA-S88 dla procesów batch’owcyh. Pracę ruszyły w roku 2000, aby w 2008 wydać standard PackML, jako część składową normy ISA-S88 – ISA-TR88.00.02. Na standard PackML składają się trzy główne elementy; tryby pracy, model stanów oraz Packtagi.
Podstawowym celem standardu PackML jest wsparcie spójnego „spojrzenia i odczucia” w zakładzie produkcyjnym oraz zachęcenie i umożliwienie wprowadzenia innowacji w przemyśle. Choć otwarty standard przemysłowy PackML, możemy śmiało określić jako język maszyn pakujących, nie można dać zmylić się jego nazwie. Z powodzeniem może być on bowiem stosowany do wszystkich maszyn i urządzeń wykorzystywanych w procesach dyskretnych, nie tylko do maszyn pakujących.
Co daje używanie PackML?
Jeżeli skorzystamy ze standardu PackML, określimy model stanów, tryby prace oraz informacje wymieniane pomiędzy maszynami, to jakiekolwiek dwie maszyny, w których zastosowane zostaną te definicje mogą się z sobą komunikować, niezależnie od zastosowanego systemu sterującego. Jako otwarty standard, PackML nie jest bowiem przywiązany do żadnej konkretnej technologii.
Dzięki takiemu rozwiązaniu nie potrzebujemy żadnego obszernego systemu do translacji pomiędzy nimi. Znacząco ułatwia to integrację poziomą – maszyna do maszyny w ramach linii produkcyjnej, jak również integrację pionową – linii produkcyjnej z nadrzędnym systemem (MES, SCADA, Historian) w celu obliczenia kluczowych wskaźników produkcyjnych (KPI) np. OEE.
Standard PackML nie jest ponadto protokołem komunikacyjnym, a to, jaki protokół zostanie użyty w danej maszynie zależy od End Usera. PackML określa, w jaki sposób maszyny będą komunikować się pomiędzy sobą przy użyciu któregokolwiek z Ethernetowych protokołów komunikacyjnych. Dzięki temu maszyny mogą udostępniać informacje do sieci w taki sposób, aby każda inna maszyna do niej podłączona również mogła ją zrozumieć.
Korzyści użytkownika końcowego | Korzyści OEM |
– Skrócenie czasu przestojów – Skrócenia czasu wdrożenia – Szybka integracja maszyn różnych dostawców w jedną linię produkcyjną/ pakującą – Redukcja czasu potrzebnego na szkolenia operatorów, przełożonych i utrzymania ruchu – Łatwe wpięcie maszyny zgodnej ze standardem PackML do linii/systemu Scada / MES czy sterownika linii – Wymiana informacji pomiędzy maszynami pakującymi i liniami pakującymi oraz w dobie przemysłu 4.0 z danymi w chmurze – Standaryzacja danych wejściowych i wyjściowych – PackTags | – Ochrona know-how – Krótszy czas wdrożenia serwisantów – Łatwiejszy serwis maszyn – Standaryzacja pozwala na modułowość – Niższe koszty inżynieringu – Koncentracja na rozwoju innowacji |
Czy PackML jest dla mnie?
Czwarta rewolucja przemysłowa jest faktem. Żyjemy w czasach, w których rośnie potrzeba personalizacji produktu i zbierania coraz większej ilości danych dla optymalizacji procesów, a wszystkie urządzenia muszą nawiązywać z sobą komunikację w ramach IoT. Wydaje się zatem, że jednolity język maszyn pakujących może służyć za panaceum na sporą ilość bolączek, które mogą czekać nas w przyszłości. Spróbujmy więc odpowiedzieć sobie na kilka pytań:
- Chcesz wdrożyć założenia 4. rewolucji przemysłowej w swoim zakładzie?
- Przygotowujesz się do wdrożenia nadrzędnego systemu zarządzania przedsiębiorstwem (MES, SCADA ERP)?
- Masz problem z zatrudnieniem pracowników i dużą rotację pomiędzy stanowiskami?
- Budujesz nowy zakład, w którym musisz połączyć w sprawną linię produkcyjną maszyny od wielu dostawców?
- Produkujesz maszyny i potrzebujesz zwolnić zasoby czasowe swoich pracowników dla rozwoju nowych rozwiązań i budowy przewagi konkurencyjnej?
Jeżeli na któreś z tych pytań odpowiedź brzmi TAK, oznacza to, że powinniśmy zainteresować się standardem PackML, i zacząć mówić… w języku swoich maszyn.
Źródła zdjęć:
https://unsplash.com/photos/AUxh4Tccuf8