Treści
Najczęstsze problemy działów utrzymania ruchu. Jak sobie z nimi radzić?
Najczęstsze problemy działów utrzymania ruchu. Jak sobie z nimi radzić?
Głównym celem działów utrzymania ruchu jest zapewnienie ciągłości procesów produkcyjnych. W miarę rozwoju technologii i w związku ze zmianami rynkowymi, zadanie to wymaga mierzenia się z coraz nowymi wyzwaniami czy problemami. Jak sobie z nimi radzić?
Główny cel istnienia działu utrzymania ruchu można opisać też jako ciągłe zapewnianie zadowalającego poziomu dostępności technicznej maszyn dla celów produkcyjnych. Aby go osiągnąć działy utrzymania ruchu realizują wiele pracochłonnych działań:
- Interweniują w przypadku, gdy maszyny w wyniku awarii nagle przestają działać.
- Prewencyjnie prowadzą cykliczną weryfikację stanu maszyn i usuwają drobne usterki, gdy te się pojawią.
- Zarządzają dostępnością części zamiennych niezbędnych do napraw i wprowadzania usprawnień;
- Zarządzają ciągłą ewidencją danych technicznych dotyczących maszyn;
- Monitorują wskaźniki KPI związane z efektywnością utrzymania ruchu.
Dodatkowo, na przestrzeni lat można było obserwować systematyczne rozszerzanie zakresu podstawowych działań utrzymania ruchu między innymi o:
- zarządzanie infrastrukturą, a więc budynkami oraz pozostałymi obiektami technicznymi;
- monitorowanie i optymalizacja zużycia mediów;
- zarządzanie i usprawnienie współpracy z dostawcami zewnętrznymi;
- wspieranie działów BHP pod kątem dostępności i komunikacji w zakresie informacji dotyczących parku maszynowego;
- wdrażanie nowych metodologii opartych na współpracy produkcji i utrzymania ruchu (np. TPM);
- planowanie działań predykcyjnych w oparciu o ciągłe monitorowane parametrów maszyn.
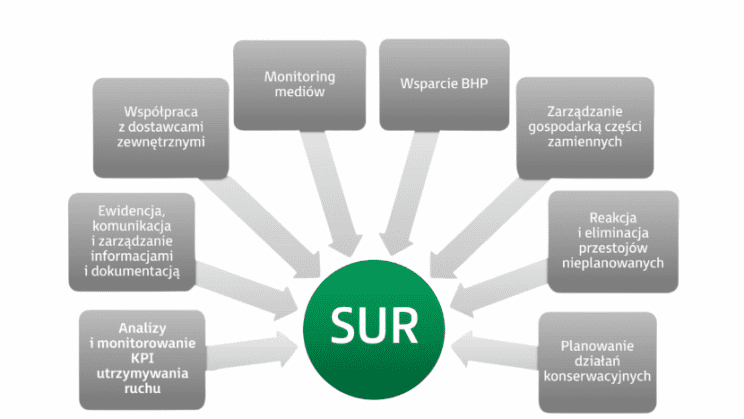
Obecne trendy widoczne w obszarze cyfryzacji przedsiębiorstw sprawiają, że ten zakres obowiązków jest w dalszym ciągu rozbudowywany, między innymi o:
- monitorowanie danych dotyczących pracy maszyn zbieranych za pomocą czujników;
- monitorowanie procesów technologicznych z wykorzystaniem systemów SCADA;
- wdrażanie i nadzorowanie procesów automatyzacji i robotyzacji.
Przykładowe wyzwania i problemy działu utrzymania ruchu
Zwiększająca się ilość działań, planowanych przeglądów, obchodów, inspekcji oraz działań zakontraktowanych firm zewnętrznych, przy ograniczonych zasobach, nierzadko prowadzi do pojawienia się problemów z terminowością. Zazwyczaj planowanie i pilnowanie by zadania prewencyjne były realizowane w terminie spoczywa na barkach jednej osoby. Bez dodatkowych przypomnień, nie tylko dla planisty, ale i samych wykonawców, narastają zaległości, które zwiększają ryzyko awarii.
Często można spotkać się też z sytuacją, w której dział produkcji przesyła niekompletne opisy awarii. Zdarza się, że brakuje wstępnej analizy, zdjęć miejsca awarii czy dokładnego opisu sytuacji. Niekiedy problemem jest komunikacja. Zdarza się bowiem, że informacje nie trafiają bezpośrednio do działu utrzymania ruchu, tylko przechodzą przez kilka kolejnych instancji. W rezultacie wydłuża się czas reakcji na potencjalne zagrożenia.
Utrudnieniem dla działu technicznego jest bez wątpienia sytuacja, w której dokumentacja przechowywana jest w formie papierowej. Archiwa zazwyczaj nie są wówczas „po drodze”, a same dokumenty czasem bywają nieczytelne. Dodatkowo, gdy w krótkim czasie podejmuje się wiele działań naprawczych, ich historia nie jest nawet zapisywana. Skutkuje to sytuacją, w której pracownicy „wywarzają otwarte drzwi”, bo brakuje informacji na temat wcześniejszych udanych i nieudanych prób rozwiązania podobnego problemu.
W wielu przypadkach źródłem kłopotów jest mocno niedoskonały nadzór nad magazynem części zamiennych (a czasem nawet jego brak). Części są stale pobierane, a osoba odpowiedzialna za zamówienia dowiaduje się o brakach w magazynie w ostatniej chwili, gdy już półki są prawie puste.
Wiele działań optymalizacyjnych opiera się na przeczuciach budowanych na podstawie bieżących obserwacji. Przez to, że dane często nie są przez nikogo gromadzone, nie ma czego analizować. W rezultacie bardzo często nie można wykazać rzeczywistej rentowności maszyn, a zbadanie, dlaczego doszło do awarii wymaga dużego nakładu prac.
Przyczyny źródłowe problemów utrzymania ruchu
Jedną z przyczyn źródłowych powyższych problemów jest brak procedur działania nie tylko w obrębie utrzymania ruchu, ale też innych działów, co uniemożliwia skuteczną komunikację. Problem ten uwidacznia się, gdy brakuje standardów przekazywania informacji o zdarzeniach nieplanowanych, brakuje procedur planowania i powiadomień o działaniach, szablonów rejestrowania pobrań części na poczet działań. Gdy nie ma ustalonych odgórnie zasad pracownicy pozbawieni są dostępu do danych. Pojawiają się przeoczenia i dezinformacja.
„Klątwa wiedzy” to kolejne źródło problemów. Zagrożenie pojawia się, gdy doświadczeni pracownicy, są przekonani, że „wiedzą najlepiej” co trzeba zrobić, ponieważ brali już udział w wielu naprawach maszyn. Często ich wiedza, rzeczywiście jest bezcenna, ale w momencie, gdy pojawiają się nowe wyzwania, nie zawsze da się polegać wyłącznie na rutynie. Dodatkowo im więcej podejmuje się działań, tym trudniejszy jest próg wejścia dla nowych pracowników. Kadra o bardzo dużej wiedzy przestaje zapisywać „oczywiste” informacje, jak przyczyna awarii czy sposób jej rozwiązania. Przestaje aktualizować dokumentację po drobnych zmianach i modernizacjach.
W wielu przypadkach przyczyną problemów jest po prostu brak odpowiednich, specjalistycznych narzędzi wspierających planowanie, komunikację oraz monitorowanie i nadzorowanie realizowanych działań. Przechowując wszystkie dane w kilku plikach Excel, mamy poczucie pozornej kontroli. Taka strategia wymaga jednak stałej czujności, najczęściej ze strony jednej osoby, której pamięć może z czasem okazać się zawodna.
Jak można przeciwdziałać problemom pojawiającym się w Utrzymaniu ruchu?
W celu przeciwdziałania problemom pojawiającym się w utrzymaniu ruchu przydatne okazuje się wyznaczenie standardów i wzorów podejmowania działań przez pracowników.
Dodatkowo dobrze jest precyzyjnie określić działania związane z analizą krytyczności maszyn, określenie minimalnych i maksymalnych stanów magazynowych oraz reguł codziennych działań (zapisu danych, rejestracji wykonanych prac naprawczych, rejestru pobrań części potrzebnych do serwisowania maszyn), jak również wzorów przepływu informacji. Dodatkowym poziom zabezpieczenia może przynieść nadanie pracownikom odpowiedzialności za konkretne obiekty techniczne.
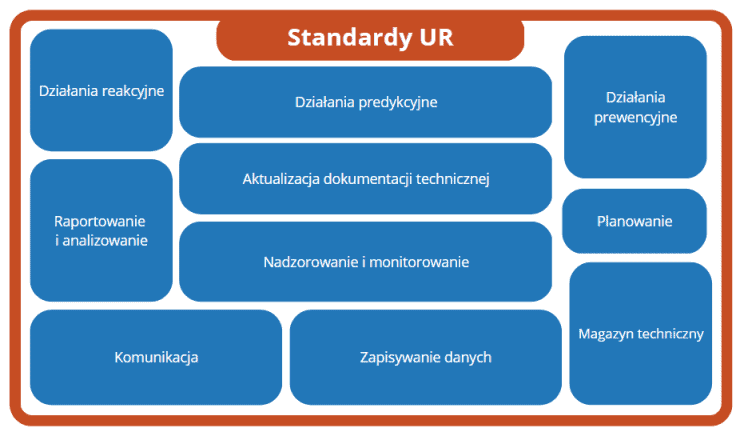
Innym sposobem zaangażowania zespołu i poprawienia efektywności działu technicznego jest przypisanie do pracowników, zależnie od pełnionego stanowiska, wskaźników efektywności, dotyczących takich obszarów jak zaległości w zaplanowanych przeglądach czy czas usuwania awarii. Takie podejście można połączyć z systemem premiowania za podejmowanie wyzwań usprawniających pracę działu. Szansa na premię za bezawaryjność pracy lub szybką reakcję może na przykład sprawić, że pracownicy będą zwracać większą uwagę na stan maszyn oraz przekonywać produkcję do szybszego kontaktu, gdy tylko pojawią się wczesne symptomy awarii (hałas, drgania oraz inne odstępstwa od normy).
Najpopularniejszym rozwiązaniem jest wdrożenie systemu CMMS dostosowanego do potrzeb organizacji. Systemy te wspierają nie tylko planowanie, ale i komunikację, archiwizację, dostępność danych, jak i samo wykonanie prac, nie wspominając o automatycznym raportowaniu.
Jak systemy CMMS rozwiązują problemy utrzymania ruchu?
Systemy CMMS nakładają standardy na organizację. Proces tworzenia procedur jest efektem współpracy klienta i dostawcy rozwiązania CMMS.
System ma specjalne procedury dla większości obszarów aktywności działów utrzymania ruchu:
- Komunikacji z liniami produkcyjnymi
- Działania w przypadku akcji prewencyjnych
- Działania w przypadku akcji reakcyjnych
- Zapisywania historii oraz wykorzystania historycznych danych
- Monitorowania stanów magazynowych
- Raportowania
- Postępowania w procesie tworzenia analiz i optymalizacji
Systemy CMMS oferują również specjalne platformy dla różnych użytkowników dostosowane do ich wymagań. Wszystkie są ze sobą połączone, dzięki czemu możliwe jest automatyczne aktualizowanie niezbędnych danych. Niektóre systemy oferują spersonalizowane platformy z dostępem do dokumentacji, historii zdarzeń, podglądem stanów magazynowych czy nawet dodatkowymi materiałami szkoleniowymi dla operatorów oraz techników.
Dane dostępne są z poziomu różnych urządzeń, takich jak komputer, tablet, telefon czy nawet panele dostępne przy maszynach. Równie ważne jest też to, że dane w systemie są ze sobą bezpośrednio powiązane, dzięki czemu w łatwy sposób mamy dostęp do wszystkich interesujących nas informacji dzięki kilku kliknięciom.
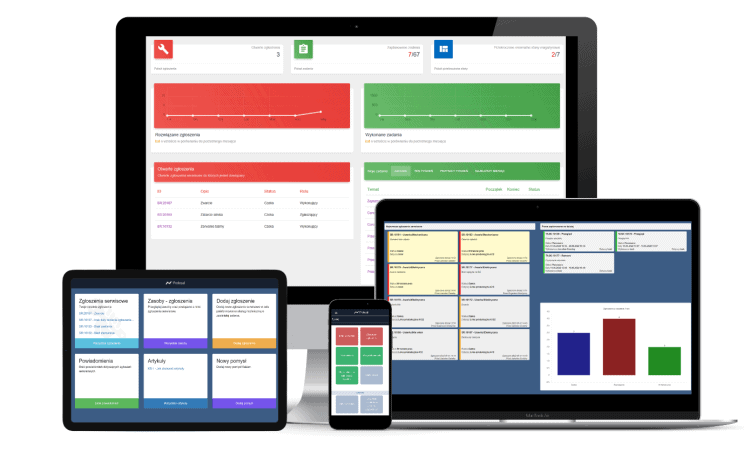
Systemy CMMS oferują również nadzór i monitorowanie danych. Wszelkie działania produkcji oraz techników mogą być odzwierciedlane w systemie, a ich efekty automatycznie zapisywane. Dzięki temu CMMS może generować powiadomienia a w nagłych sytuacjach raporty stanów. Niekiedy może nawet podpowiadać działania mające na celu optymalizację pracy. Wszystko to sprawia, że choć problemy działu utrzymania ruchu nie znikają, ich lista jest zdecydowanie krótsza.