Treści
Mierz techniczny koszt wytworzenia, by generować oszczędności
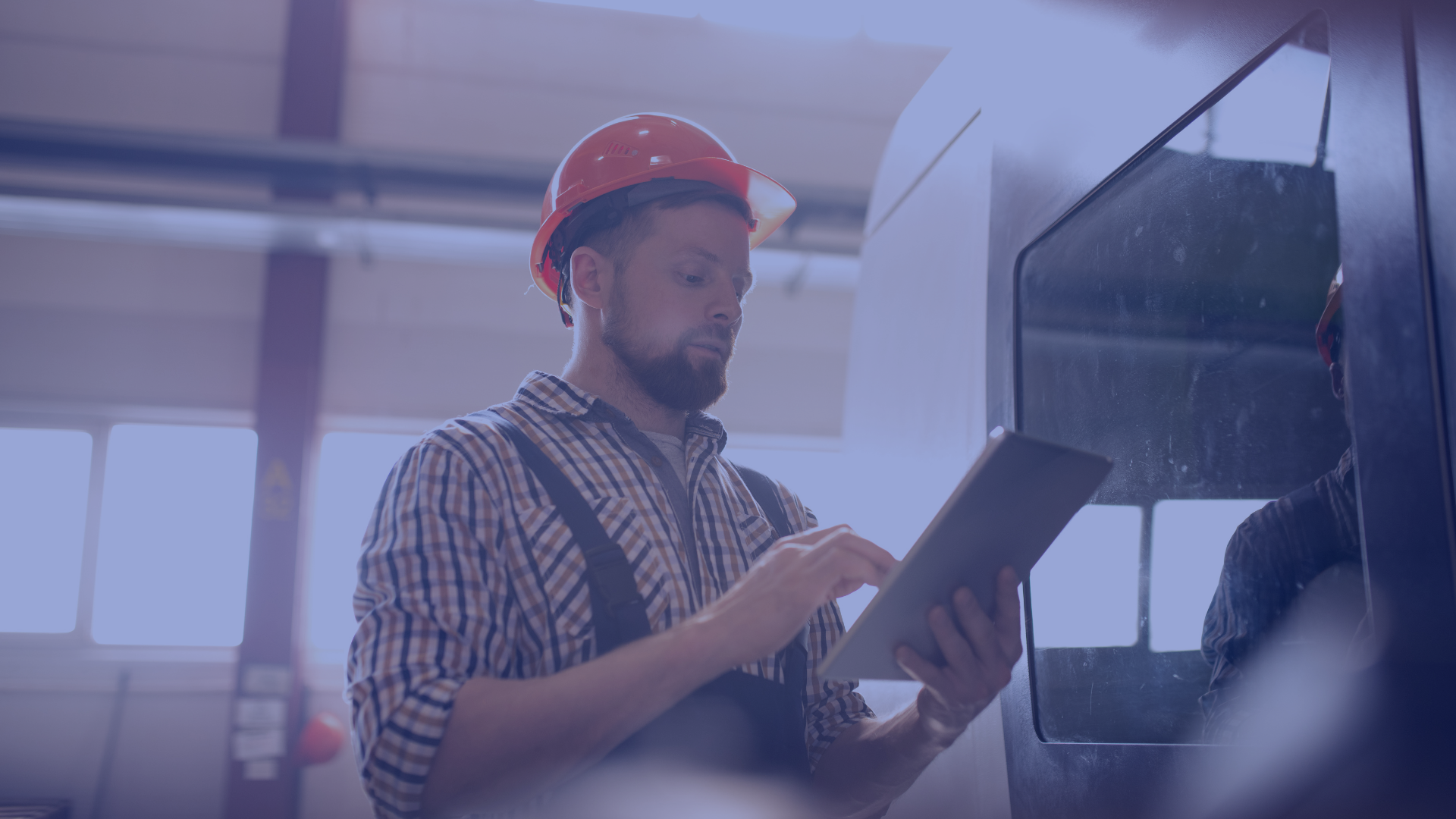
Mierz techniczny koszt wytworzenia, by generować oszczędności
Poznanie złożonej struktury kosztowej twojego biznesu produkcyjnego pozwoli ściąć nieoczywiste wydatki.
Z prowadzeniem każdego rodzaju działalności – także produkcyjnej – związane są koszty, które należy ponosić, aby móc uzyskać przychód. Istnieją dwie zasadnicze grupy kosztów: bezpośrednie i pośrednie. Te pierwsze związane są z procesem wytwarzania produktu. Są ponoszone, by kupić materiały i surowce, opłacić pracowników obsługujących proces produkcji, nabyć opakowania, opłacić zużycie energii potrzebnej w procesie produkcji.
Koszty pośrednie również trzeba ponieść, by wygenerować przychód, ale ich związek z procesem produkcji jest mniej oczywisty. Trudno je też powiązać z wytworzeniem konkretnego produktu. Można je podzielić na trzy grupy: koszty wydziałowe, koszty ogólnozakładowe i koszty sprzedaży.
Koszty wydziałowe dotyczą:
- zużycia materiałów i wyposażenia pomocniczego
- zużycia paliwa i energii
- wynagrodzeń pracowniczych
- prac remontowych
- podróży i zakwaterowania pracowników
- licencji i abonamentów
- amortyzacji środków trwałych sekcji produkcyjnych
Koszty ogólnozakładowe dotyczą:
- wydatków administracyjnych
- wynagrodzeń zarządu
- utrzymania biur, magazynów i terenu
- ochrony mienia
- podatków i opłat lokalnych
- itd.
Koszty sprzedaży – zgodnie z nazwą – dotyczą samego procesu sprzedaży.
Te dwie ostatnie grupy kosztów (ogólnozakładowe i sprzedaży) są ważne dla całego przedsiębiorstwa, jednak z punktu widzenia menedżera produkcji najważniejsze są koszty bezpośrednie i koszty wydziałowe (należące do grupy kosztów pośrednich). Zbiorczo koszty z obu grup określane są mianem technicznego kosztu wytworzenia (TKW). Umiejętne obliczenie tego wskaźnika pozwala dostrzec te miejsca, gdzie w procesie produkcji uciekają pieniądze i dokonać oszczędności.
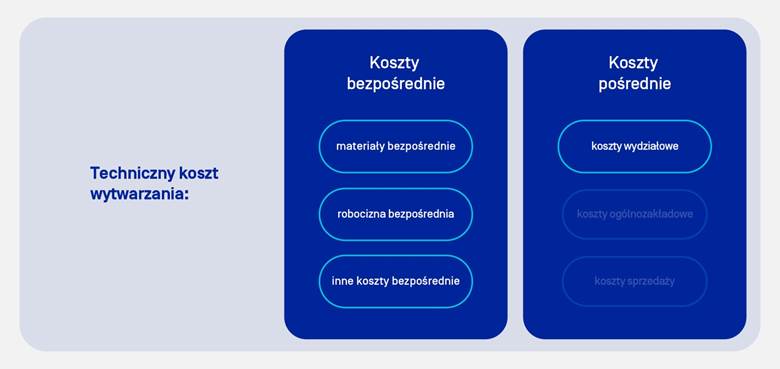
Gdzie szukać oszczędności?
Relatywnie łatwo zakwalifikować takie koszty bezpośrednie jak wydatki materiałowe czy te związane z wynagrodzeniem pracowników. Inne koszty bezpośrednie to np. koszty pozyskiwania i przemieszczania materiałów, energia i media produkcyjne, zużycie narzędzi, koszty obróbki obcej (zlecenia zewnętrzne) czy koszty przygotowania i wdrożenia nowej produkcji. Choć nie myślimy o nich w pierwszej kolejności, to właśnie one dają duże pole do szukania oszczędności poprzez odpowiednie opomiarowanie, analizy, planowanie czy optymalizację.
Dużo możliwości dają też koszty wydziałowe. Patrząc na globalny rachunek kosztów przedsiębiorstwa okazuje się, że wcale nie są tak niewielkie, jak mogłoby się wydawać. Każdy dyrektor finansowy średniej i dużej firmy byłby zainteresowany obcięciem ich o 20%. Jak się okazuje, nie jest to wcale takie trudne. Wystarczy tylko powiązać te koszty z procesem produkcji.
Koszty bezpośrednie są alokowane wprost do konkretnych wyrobów w bardzo oczywisty sposób, czyli relacją liniową. Zakwalifikowanie kosztów wydziałowych jest większym wyzwaniem. Potrzebujemy do tego „narzędzia” w postaci kluczy podziałowych, określających w jakim stosunku do danego wyrobu mogą zostać przypisane koszty wydziałowe.
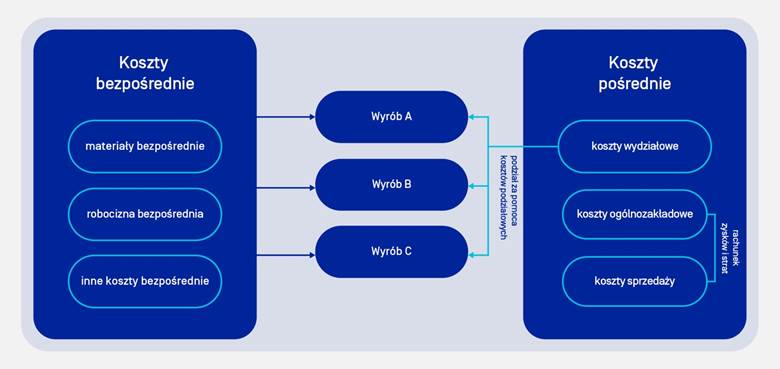
Wiedza o tym, jak kwalifikować poszczególne koszty zapewnia kontrolę nad wszystkimi wydatkami, jakie ponosi firma. Dzięki niej mamy pewność, że pieniądze wydawane są w sposób uzasadniony. Podział na poszczególne grupy oraz powiązanie wydatków z konkretnymi produktami, znacznie ułatwia znalezienie oszczędności, nawet w obszarach, w których na pierwszy rzut oka ich nie widać.
Gdzie z produkcji uciekają pieniądze?
W publikacjach przeznaczonych dla menedżerów można znaleźć wiele pomysłów na redukcję kosztów w przedsiębiorstwie. Materiały te często jednak dotyczą kosztów dość oczywistych – jak choćby tych związanych z zakupem materiałów czy wpłatą wynagrodzeń dla pracowników. Większym wyzwaniem jest redukcja kosztów, z których istnienia początkowo nie zdajemy sobie sprawy. Właśnie nimi chcemy się tu zająć.
Gdzie można ich szukać?
Przykładowo w wydatkach na transport. Gdy w dostawie jest kilka rodzajów produktów, skupiamy się na tym, co należy z nimi zrobić. Nie myślimy, by głębiej przeanalizować jaka część kosztów transportu przypada na poszczególne produkty.
Innym dobrym przykładem takich nieoczywistych kosztów są wydatki na energię. Wiele firm stara się je ograniczyć inwestując w nowoczesne rozwiązania. Zapominają natomiast o tak prostych kwestiach jak wyłączanie klimatyzacji po wyjściu pracowników z biura czy przykręcanie kaloryfera, kiedy temperatura na to pozwala. Wystarczy zadbać o wyrobienie odpowiednich nawyków wśród pracowników, by pojawiły się oszczędności. Być może nie są to działania, które przyniosą od razu spektakularne efekty, jednak powinny być one elementem analizy. Warto wiedzieć, jaki w ich przypadku jest współczynnik korzyści do kosztów.
Jak optymalnie wykorzystać dostępne zasoby?
Czasem, zamiast poszukiwać kolejnych inwestycji, które w dłuższej perspektywie mają przynieść oszczędności, warto najpierw zastanowić się nad optymalizacją zużycia dostępnych zasobów. Nawet jeśli z pozoru wydaje się, że niewiele można zrobić, dobrze jest zadać sobie pytanie, czy aby na pewno.
Świetnym przykładem, który to obrazuje jest podejście pewnej firmy do kwestii zużycia narzędzi specjalistycznych. W organizacji tej narzędzia były współdzielone przy wytwarzaniu różnych produktów. Pojawił się pomysł, aby wprowadzić współczynnik określający ile można wydać na każde wykorzystanie narzędzi mierzone w godzinach, a także ile można wydać na każdą godzinę. Osoby odpowiedzialne za ten projekt, opracowały plan produkcji na 2-3 tygodnie w przód i ustaliły widełki i limity wydatków narzędziowych. Początkowo wydawało się, że wykorzystania niektórych narzędzi nie da się już zoptymalizować. Stopniowo zaczęły pojawiać się jednak ciekawe inicjatywy.
Zaangażowani w projekt pracownicy zaczęli wspólnie optymalizować użycie narzędzi oraz egzekwować sposoby efektywniejszego ich użytkowania od operatorów. Początkowo ustalone poziomy wydatków na narzędzia były dość wysokie, jednak z czasem dział narzędziowy konsekwentnie schodził z tego kosztu. Po trzech kwartałach okazało się, że projekt wygenerował milionowe oszczędności, choć początkowo nikt się tego nie spodziewał.
W tym miejscu warto podkreślić, że bardzo ważną kwestią przesądzającą o powodzeniu tego typu inicjatyw jest powiązanie kosztów z konkretnymi etapami procesu produkcji. To produkcja jest funkcją, która determinuje koszt. Chodzi więc nie o to, aby koszty były jak najniższe, ale by były uzasadnione wymogami produkcji.
Niektóre wydatki łączą się z produkcją w sposób liniowy, jednak nie zawsze tak jest. W przypadku tych mniej oczywistych kosztów, powinniśmy przeanalizować w jaki sposób możemy powiązać je z produkcją i jaki jest ich udział w procesie powstawania poszczególnych produktów. Jeśli tego nie zrobimy i pozwolimy się tym kosztom rozwodnić, nigdy ich nie odzyskamy.
Trudnym zagadnieniem bywają koszty związane z przygotowaniem nowej produkcji. Mamy tu do czynienia z bardzo dużą losowością i początkowo często nie wiemy, które działania są optymalne. Warto jednak zastanawiać się nad każdym kosztem, który został poniesiony. Można choćby próbować ustalić jego związek ze spodziewanym przychodem. Tylko takie podejście daje nam pełny obraz sytuacji.
Jak automatyzacja redukuje koszty?
Czy automatyzacja produkcji może w jakiś sposób pomóc w wychwyceniu tych mniej oczywistych kosztów i umożliwić ich zredukowanie? Zdecydowanie tak. Aby pokazać, jak może się to dziać, posłużmy się przykładem jednej z firm, gdzie produkcja była dobrze opomiarowana i oprzyrządowana. Jednostką pomiarową produkcji w tej organizacji była kilowatogodzina na tonę produktu. W pewnym momencie jeden z produktów zaczął wykazywać niespotykany wcześniej, chwilowy wzrost kosztów.
Co się okazało?
Na jednej z linii spory silnik, pobierający dość dużą ilość energii, został przez dział utrzymania ruchu wprowadzony w tryb manualny, czyli włączony z pominięciem sterownika. Silnik ten pracował przez cały czas. Nikomu z pracowników to nie przeszkadzało, bo był to stan obojętny dla procesu produkcji. System MES przypisał koszty działania silnika do konkretnego produktu. Automatyzacja linii pozwoliła szybko zlokalizować miejsce, gdzie pieniądze uciekały w bezsensowny sposób. Przykład ten jasno pokazuje, że automatyzacja pozwala bardzo szybko wychwycić niestandardowe wzrosty kosztów i znaleźć ich źródła.
Dlaczego warto słuchać pracowników?
Aby jednak dotrzeć do najbardziej ukrytych i niepotrzebnych kosztów, a następnie móc je zredukować, warto wsłuchać się w głos załogi i zaangażować pracowników w generowanie oszczędności. Tak właśnie zrobiono w pewnym amerykańskim koncernie. Okazało się, że drzemiący w zespole potencjał był tak duży, że osoby, których nikt o to nie podejrzewał, zgłaszały najciekawsze pomysły optymalizacyjne. Wdrażanie inicjatyw wiązało się z nagrodami dla pomysłodawców, ale nie była to jedyna motywacja. Pracownikom zaczęło zależeć. Spontanicznie zaczęli budować kulturę oszczędzania.
Nawet jeśli w takich programach wiele propozycji jest nietrafionych, wdrażanie pomysłów pracowniczych ma duży sens. Dzięki temu ludzie czują się odpowiedzialni za to, co dzieje się w firmie, a wśród zaproponowanych inicjatyw prędzej czy później trafi się perełka.
Podsumowanie: Koszty uzasadnione wymogami produkcji
Jak widać oszczędności mogą kryć się w nieoczywistych obszarach. Optymalizacja, dobre nawyki, automatyzacja i poszukiwanie nowych pomysłów mogą bardzo pomóc w redukcji kosztów bezpośrednich i wydziałowych, tak by zwiększyć efektywność biznesową. Najważniejsza jest jednak szczegółowa wiedza o ich powiązaniu z produkcją. Nie należy bagatelizować nawet tych najdrobniejszych wydatków, ponieważ ich analiza w kontekście wolumenu produkcji, może przynieść niespodziewane korzyści.
Jeśli chcecie Państwo dowiedzieć się więcej o możliwych oszczędnościach i sposobach redukcji kosztów pośrednich i bezpośrednich oraz o roli systemów MES i ERP w zarządzaniu tymi kosztami zachęcamy do lektury trzech oryginalnych tekstów na podstawie, których powstał ten materiał:
- TKW a podział kosztów w przedsiębiorstwie. Pierwszy krok do poszukiwania oszczędności
- TKW a podział kosztów w przedsiębiorstwie. Gdzie szukać oszczędności na produkcji? Nieoczywiste koszty
- Rola systemów MES i ERP w zarządzaniu kosztami firmy
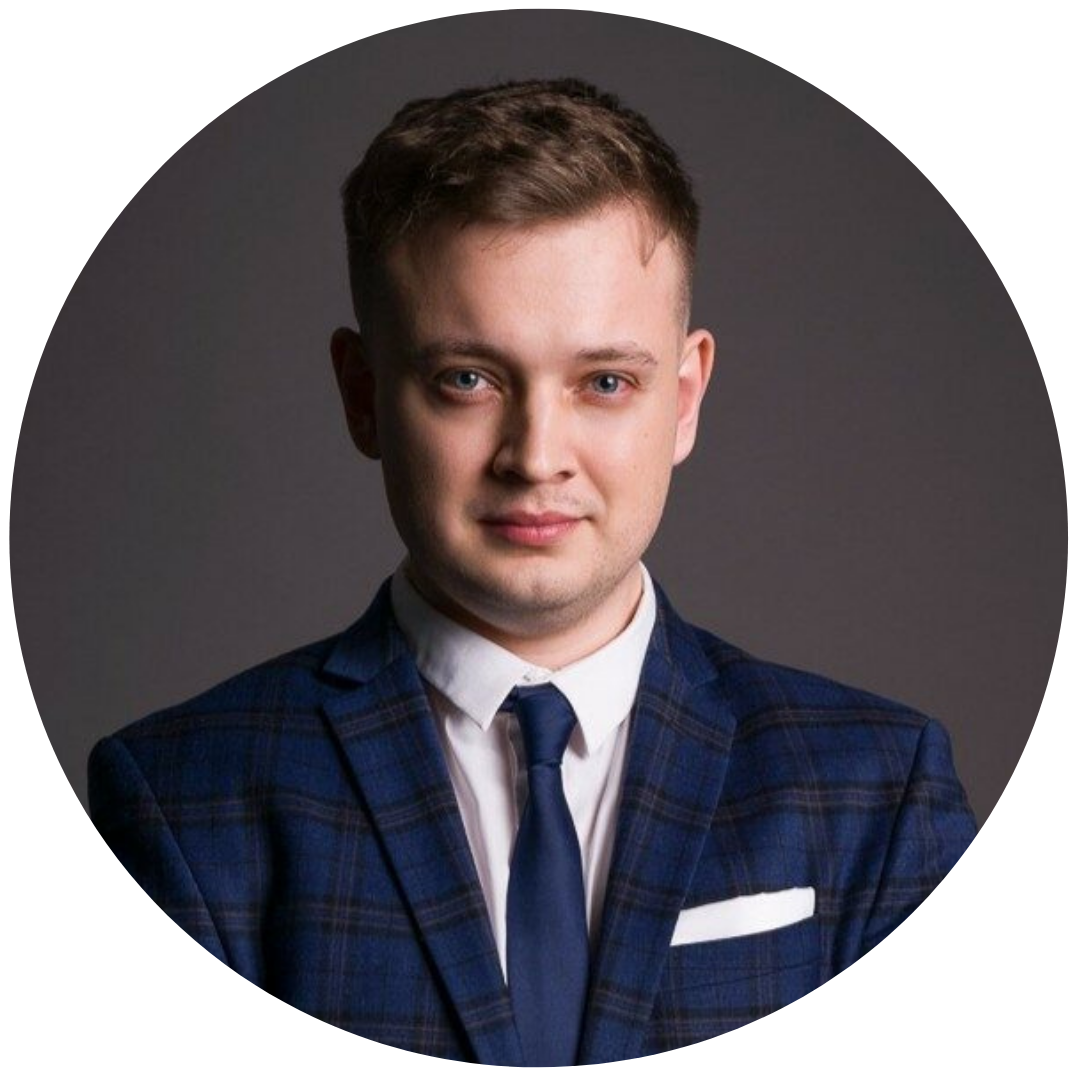
Michał Zieliński
Head of Product and Digital Consulting | Członek Zarządu ImFactory
Kontakt: Michal.Zielinski@imfactory.com.pl
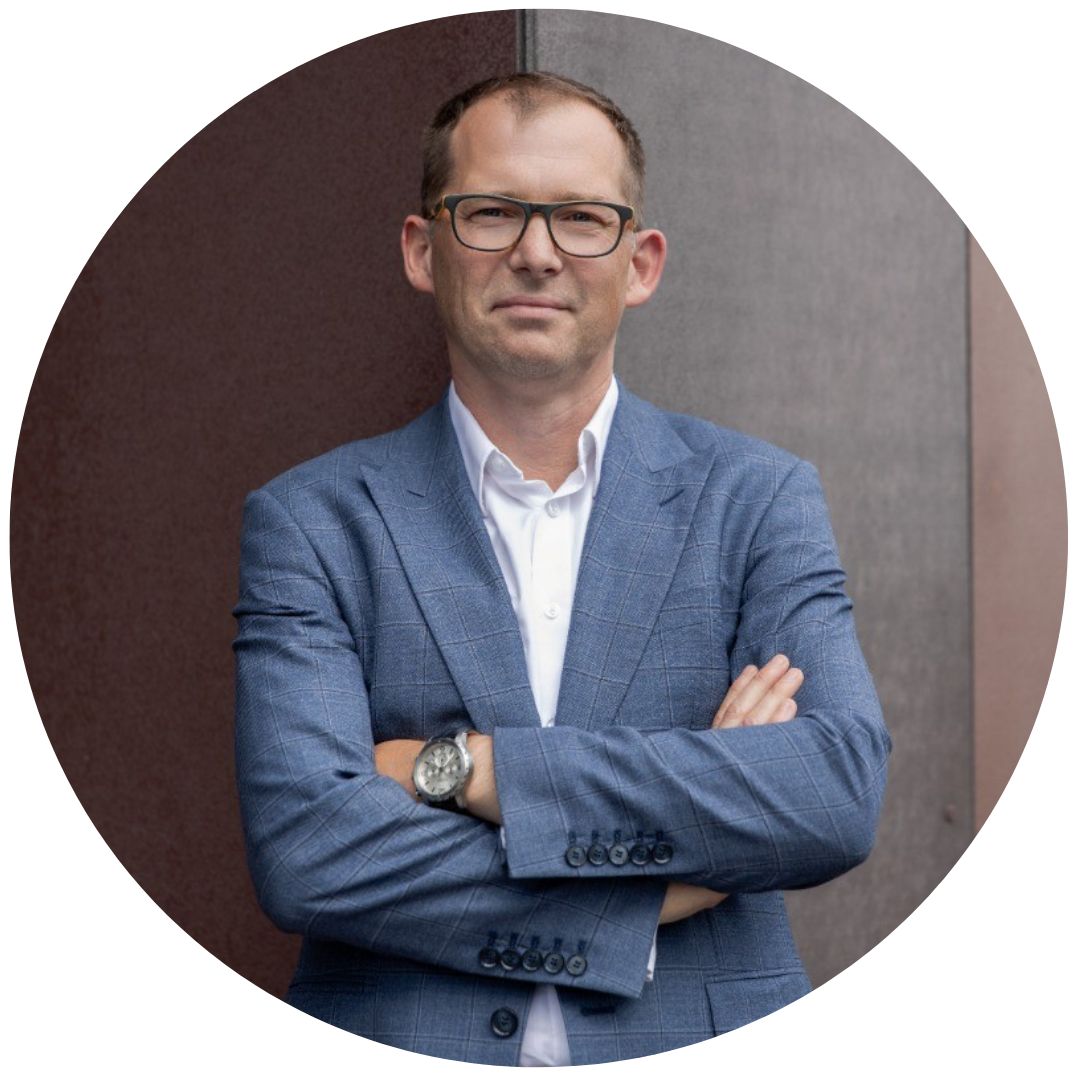
Tomasz Kubach
Konsultant ImFactory | PM-TK
Kontakt: Linkedin