Lean Manufacturing w erze IoT
Lean Manufacturing w erze IoT
Poprawianie, ulepszanie, wymyślanie nowych rozwiązań to potrzeba niemalże wpisana w ludzkie DNA i jednocześnie jedno z kół zamachowych rozwoju gospodarki. Jest to szczególnie dobrze widoczne w branży motoryzacyjnej. Wprowadzenie nieco ponad 100 lat temu przez H. Forda produkcji taśmowej było prawdziwą rewolucją w przemyśle. Inny znany przykład skokowej przemiany w przemyśle to wprowadzony przez koncern Toyoty – Toyota Production System, będący z kolei podstawą w opracowaniu koncepcji Lean Manufacturing.
Lean Manufacturing – skokowy wzorzec z Azji
Koncepcja Lean Manufacturing pozwoliła znacząco zredukować koszty, optymalizować zarządzanie zapasami, dostosowując produkcję do faktycznego popytu i, co za tym idzie, nie generować niepotrzebnych i kosztownych zapasów.
Był to niewątpliwie skok jakościowy w przemyśle, gdyż finalnie umożliwiał utrzymanie lub nawet zwiększenie wydajności pracy przy jednoczesnym utrzymaniu lub nawet zmniejszeniu wykorzystywanych zasobów.
Mówiąc o lean manufacturing nasuwa się także skojarzenie z kaizen, który możemy określić jako filozofię ciągłego udoskonalania, drobnych i dobrych zmian. Istotą tej filozofii jest, aby każdy z pracowników na wszystkich szczeblach nieustannie poszukiwał drobnych możliwości usprawnień i udoskonaleń procesu produkcji.
Wyobrażenie niewyobrażalnych rezerw
Optymalizacje poczynione w oparciu o ludzkie doświadczenia, obserwacje są w większości przypadków już wdrożone, a zatem możliwości dalszych usprawnień są ograniczone. Wiąże się to także z niewielką ilością danych jakie możemy w taki sposób zebrać. Dodatkowo ludzkie spostrzeżenia mogą być nieobiektywne. Inny sposób, czyli pomiary czasu danych operacji dają pewne dane, ale nie udzielają odpowiedzi, co naprawdę dzieję się między danymi zadaniami lub etapami produkcji.
Wiedząc o tych ograniczeniach mamy więc świadomość istniejących znacznych obszarów nieefektywności procesów produkcyjnych, których zniwelowanie może przynieść wymierne korzyści w postaci większej marży, płynniejszego zarządzania produkcją czy też większej satysfakcji Klientów.
W obliczu ograniczonych danych i braku możliwości pełnej analizy, wiarygodnej oceny działań i modyfikacji danych procesów, efektywnych porównań i rozwiązań optymalizujących produkcję w sukurs przychodzą nam dane zbierane dzięki digitalizacji obejmującej wszystkie maszyny, ich pracę, procesy oraz zatrudnionych przy produkcji ludzi – Internet of Things (IoT)
IoT w służbie lean manufacturing?
Wprowadzenie czujników i sensorów na każdym etapie produkcji, zmianach czy cyklach produkcyjnych pozwolą nam gromadzić tak potrzebne i ulotne wcześniej dane.
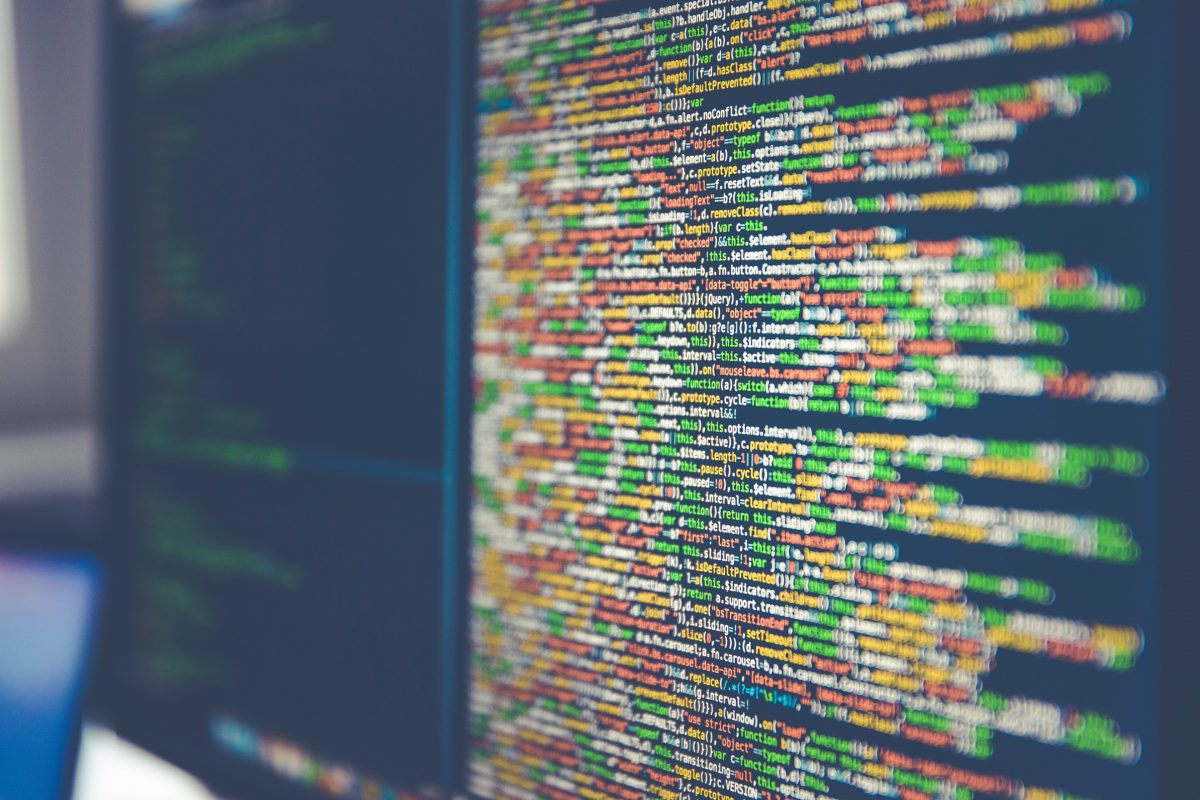
Dzięki ich analizie możemy optymalizować logistykę dostaw i przepływy pracy. Możemy również zmniejszać zużycie zasobów, zwiększać bezpieczeństwo pracy i bezawaryjność, a także analizować jakość półproduktów od różnych dostawców pomagając w optymalizacji ich wyboru.
IoT pozwala też na wydłużenie monitoringu także na okres posprzedażowy poprzez zbieranie danych, jak wydajne są nasze produkty po ich zakupie. Daje to szansę na zwiększenie satysfakcji klientów. Może to prowadzić jednocześnie do generowania wcześniej nie oferowanych usługi posprzedażowych.
Możliwość ciągłej analizy i wprowadzania niemalże nieustannych optymalizacji z wykorzystaniem IoT wydaje się być kolejnym źródłem wykorzystania w produkcji wspomnianej wcześniej filozofii kaizen. Tym razem jednak opartej nie o ludzi, a o technologię.
Lean z IOT wchodzi na kolejny poziom
Wydaje się, że IoT pozwala wprowadzić Lean Manufacturing na kolejny poziom. Wdrożenia IoT powinny przynosić wymierne korzyści. Przykładowo:
– działająca w branży szklarskiej indyjska firma Piramal Glass wdrożyła rozwiązanie IoT w przemyśle szklarskim. Po wdrożeniu wydajność każdej z 5 linii produkcyjnych wzrosła o 1 procent a Total Cost of Ownership (TCO) został zredukowany o 70%.
– wracając do tak zasłużonego przemysłu motoryzacyjnego na podobne zaprzęgniecie IoT zdecydował się Daimler Trucks Asia przy wsparciu Deloitte. Analiza zbieranych z wielu źródeł danych, w tym już podczas użytkowania samochodów przez odbiorców, pozwoliła zwiększyć efektywność monitorowania i zarządzania jakością produkcji co, jak się oczekuje, pozwoli zaoszczędzić Daimler Truck Asia w ciągu pierwszych 2 lat 8 milionów $ na kosztach gwarancji.
Lean z IoT – co dalej?
Kolejny etap Lean Manufacturing w przygodzie z IoT (Intentet od Things, Interner Rzeczy) będzie się wiązał z: – zatrudnieniem sztucznej inteligencji (AI) do analizy coraz większych i bardziej złożonych zbiorów danych, z którymi analitycy zaczną mieć już powoli problemy,
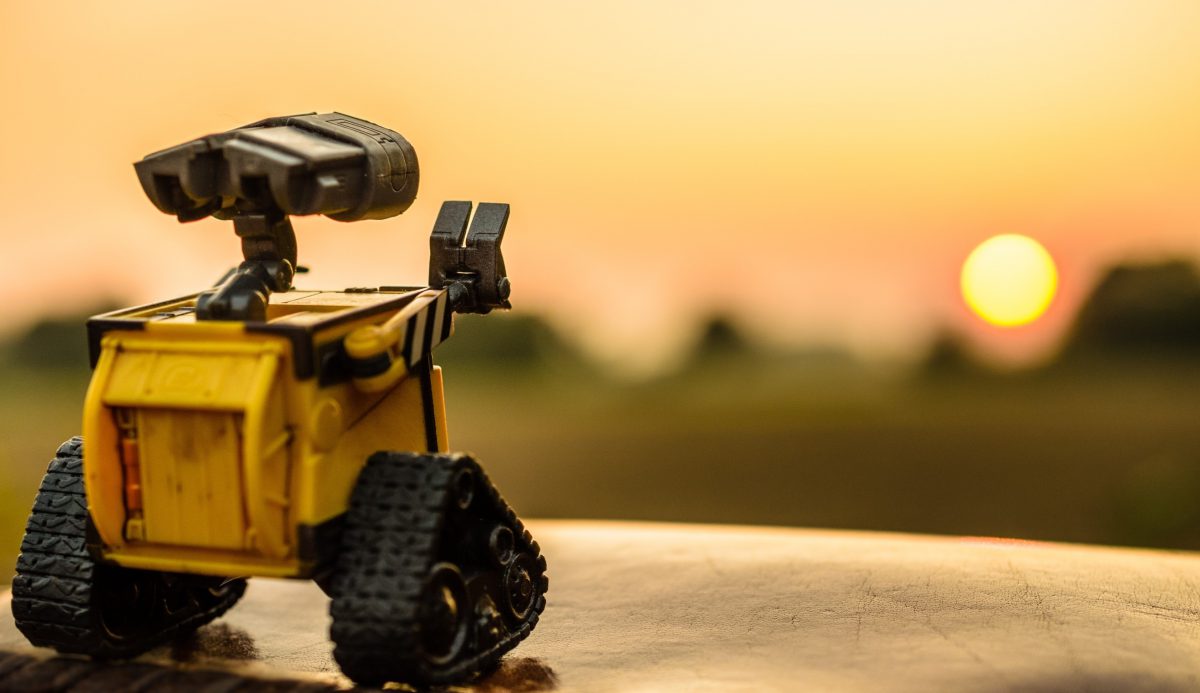
– AI pozwoli systemowi nie tylko uczyć się, ale także wykrywać wzorce, korelacje i anomalie w dużych zestawach danych, które byłyby niezauważalne dla ludzi. Te informacje z kolei mogą prowadzić do zwiększenia przychodów, redukcji kosztów, ochrony środowiska czy też poprawy bezpieczeństwa.
– Produkcja w przyszłości zapewne umożliwi stworzenie dokładnie takiego produktu, jakiego pragnie dany klient. Co więcej, w odpowiednim dla Klienta czasie. To wszystko w oparciu o świetnie zaplanowany, efektywny i oszczędny proces produkcji wykorzystujący IoT i AI – fabryki będą działać z niespotykaną dotąd wydajnością spełniając szybko nasze kaprysy i zachcianki.
O czym będziemy wtedy marzyć? Może już nigdy o niczym materialnym?
Źródło:
“What Lean Manufacturing Means in the Age of IoT” https://kontakt.io/blog/new-whitepaper-lean-manufacturing-means-age-iot/
“Industrial IoT all set to turbocharge lean manufacturing” https://readwrite.com/2017/03/24/industrial-iot-set-turbocharge-lean-manufacturing/