Treści
Lean a CMMS – jak na 7 sposobów wesprzeć pracę działu Utrzymania Ruchu?
Lean a CMMS – jak na 7 sposobów wesprzeć pracę działu Utrzymania Ruchu?
Bezawaryjne procesy, ciągłe doskonalenie, szybki przepływ informacji, efektywna praca zespołów – to niektóre czynniki, które odpowiadają za ciągłość produkcji. Jak je zoptymalizować, aby wesprzeć pracę działu UR i zwiększyć efektywność produkcji, nie zwiększając nakładu kosztów? Odpowiedź to dwa słowa: Lean i CMMS.
„Lean” to koncepcja szczupłego zarządzania, powstała w oparciu o system produkcyjny Toyoty. Stosowanie tej właśnie metodyki uznaje się za jedną z przyczyn wielkiego sukcesu tej firmy. Co w kontekście metodologii Lean oznacza „szczupłe”? Przede wszystkim pozbawione zbędnych nakładów pracy i finansów, które są związane z marnotrawstwem, takim jak: nadmierne wytwarzanie, nadmierne zapasy, wady jakościowe, nadmierny czas oczekiwania, nadmierne przetwarzanie, zbędny ruch i transport, niewykorzystany potencjał pracowników. W skrócie – Lean to ciągłe doskonalenie procesów i rozwój potencjału pracowników wszystkich szczebli.
Cyfryzacja w firmach produkcyjnych opiera się przede wszystkim o systemy klasy HMI/SCADA, ERP, WMS, ale także o systemy CMMS (z ang. Computerised Maintenance Management Systems, co można tłumaczyć jako: komputerowy system zarządzania utrzymaniem ruchu). Systemy te mają na celu wsparcie działań służb technicznych, co przekłada się na niezawodność parku maszynowego i utrzymanie ciągłości produkcji.
Poniżej 7 sposobów wsparcia pracy działu UR, które są jednocześnie siedmioma zasadami jego efektywnego działania
7 zasad działania efektywnego działu UR ze wsparciem Lean & CMMS
1. Szybko reaguj na awarie, znając ich priorytet
Awarie i usterki to zmora działu utrzymania ruchu – ich pojawienie się dezorganizuje pracę działu i przyczynia się do powstawania marnotrawstwa definiowanego w idei Lean: pojawia się nadmierny czas oczekiwania, mogą powstawać wady jakościowe w produktach. Ważne, żeby osoba odpowiedzialna za dział utrzymania ruchu była niezwłocznie informowana o wszelkich nieprawidłowościach – dzięki temu może interweniować najszybciej jak to możliwe.
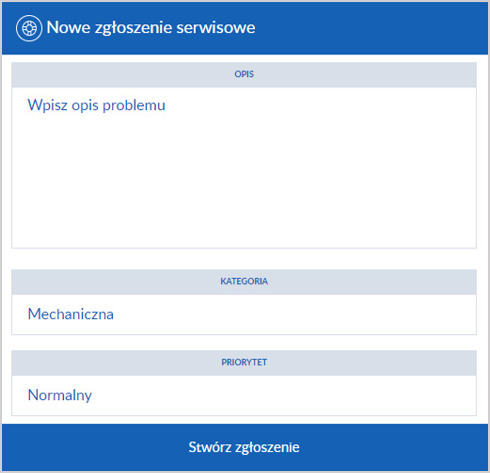
2. Zyskaj szybki dostęp do zgłoszeń serwisowych, danych i raportów
Zautomatyzowany przepływ informacji na linii produkcja – utrzymanie ruchu pozwala na bieżący dostęp do zgłoszeń serwisowych, ale również do zgromadzonych informacji i danych historycznych, a także tworzonych na ich podstawie raportów.
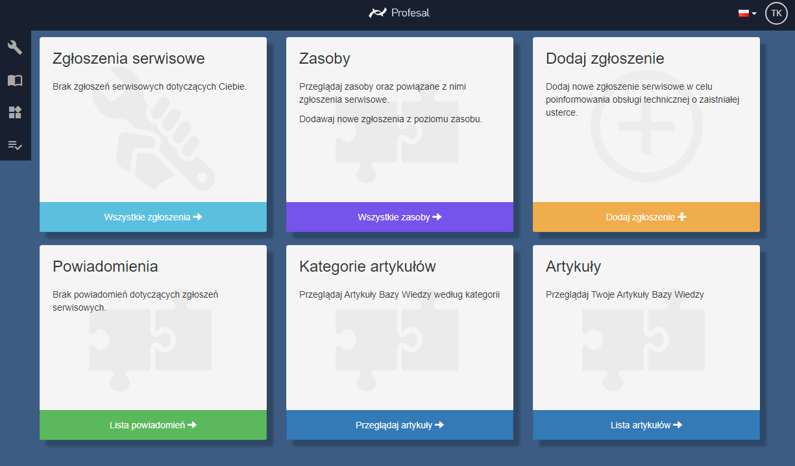
Na podstawie takiej bazy wiedzy możesz racjonalnie planować działania prewencyjne w oparciu o fakty i twarde dane.
3. Otrzymuj na bieżąco e-mail i/lub SMS o awariach
Dzięki funkcjonalnościom systemu CMMS, osoba odpowiedzialna za naprawę danej maszyny może otrzymywać natychmiast powiadomienie e-mail lub SMS o awarii zgłoszonej przez pracownika produkcji.
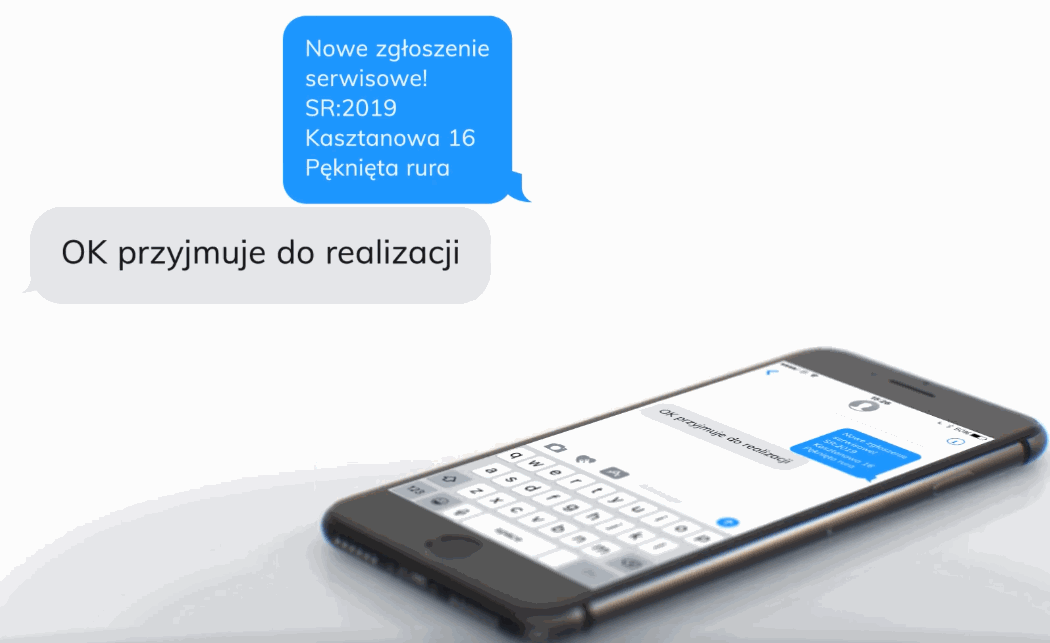
W formularzu zgłoszeniowym system podpowiada pracownikowi, jakie najważniejsze informacje musi zawierać takie zgłoszenie (m.in. rodzaj maszyny, przyczyna, priorytet awarii). Wszystkie zainteresowane osoby mają wgląd w postępy prac naprawczych.
Czy można generować zgłoszenia jeszcze szybciej? Jak najbardziej! Możliwość integracji systemu CMMS z systemami typu SCADA zapewnia automatyczną wymianę informacji o pojawiających się awariach, niwelując czas poświęcony przez pracownika na wypełnianie formularza zgłoszeniowego.
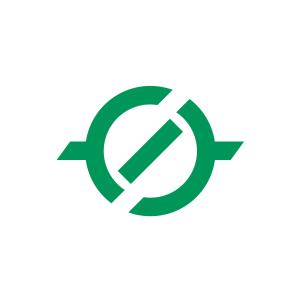
Zastosuj sprawdzony system CMMS
W ten sposób możesz dokonać cyfryzacji działu UR oraz zwiększyć produktywność nawet o 50%.
4. Zaplanuj cykliczne działania preventive maintenance
Prewencja to przede wszystkim regularne przeglądy maszyn, kontrolowanie liczby części zamiennych w magazynie, planowanie zadań służb utrzymania ruchu. Wprowadzenie zasad Lean w ten obszar pozwoli na zniwelowanie zbędnych zapasów i przestojów.
Cenna w systemie CMMS jest możliwość planowania czynności konserwacyjnych jako zadań cyklicznych (powtarzających się w określonych interwałach), dzięki czemu pracownik nie musi pamiętać o terminach przeglądów – robi to za niego system. I możesz mieć pewność, że w natłoku zadań nie umkną te z serii „niezbyt pilne, ale bardzo ważne”.
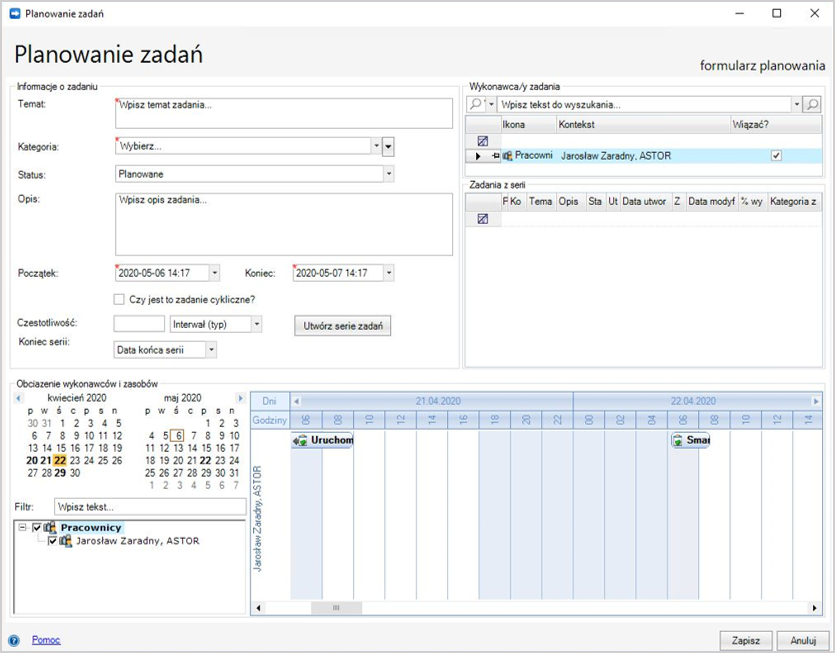
System CMMS ma na celu wspieranie pracownika w planowaniu zadań naprawczych. Na czym polega to wsparcie? System przypomina o zadaniach cyklicznych, zapewnia szybki dostęp do niezbędnych informacji: instrukcji, procedur, historii awarii – masz wszystko w zasięgu ręki. I to dosłownie, bo system może być dostępny również na telefonach czy tabletach.
Dodatkowo do zlecenia konkretnego działania prewencyjnego może zostać dodana lista kontrolna, dzięki której masz pewność, że pracownik obsługujący zlecenie wykona wszystkie niezbędne czynności.
5. Upraszczaj realizację procedur
Sporządzenie protokołu, wydrukowanie raportu, otrzymanie potwierdzenia zrealizowanej naprawy, przekazanie informacji do zwierzchnika, sprawdzenie dokąd się zanosi protokoły, zaniesienie dokumentów… Nawet taka prosta czynność, jak zatwierdzenie zrealizowania zgłoszenia serwisowego, może generować spore zamieszanie i marnotrawstwo czasu, co oczywiście zgodnie z kulturą Lean, powinno zostać zminimalizowane.
Jak taka realizacja procedury może wyglądać w wersji 2.0? W systemie informatycznym klasy CMMS generujesz formularz protokołu według wymaganego przez firmę wzoru, w którym można zawrzeć informacje takie jak: rodzaj wykonanego działania, czas trwania naprawy, przyczyna wystąpienia zdarzenia.

W tym samym systemie dokument jest od razu zatwierdzany przez zgłaszającego, a raport zostaje natychmiast przesłany do kierownika działu utrzymania ruchu, który ma dostęp do wszystkich informacji umożliwiających mu przeanalizowanie zdarzenia i podjęcie działań prewencyjnych w celu uniknięcia podobnych w przyszłości. Niwelujesz w ten sposób wszelkie opóźnienia, które mogłyby być wynikiem oczekiwania na przekazywanie protokołu papierowego do odpowiednich osób w firmie, a sam proces jego tworzenia staje się przyjaźniejszy.
6. Niweluj nadmierne zapasy
Dwa największe wyzwania, jakie Lean stawia zarządzaniu zasobami to: zachowanie ciągłości produkcji i brak nadmiernych zapasów. Zachowanie balansu między nimi nie jest prostym zagadnieniem i wymaga ciągłego nadzoru. Tutaj z pomocą znowu przychodzi system CMMS.
Rozwiązaniem może być oznakowanie zasobów w magazynie kodami QR lub NFC, co pozwoli w szybki sposób ewidencjonować stany magazynowe, za pomocą zwykłego czytnika kodów. Odczytywane dane są zapisywane w systemie jako lista zasobów, która jest punktem odniesienia do składania zamówień, przyjmowania dostaw, wydawania asortymentu z magazynu.
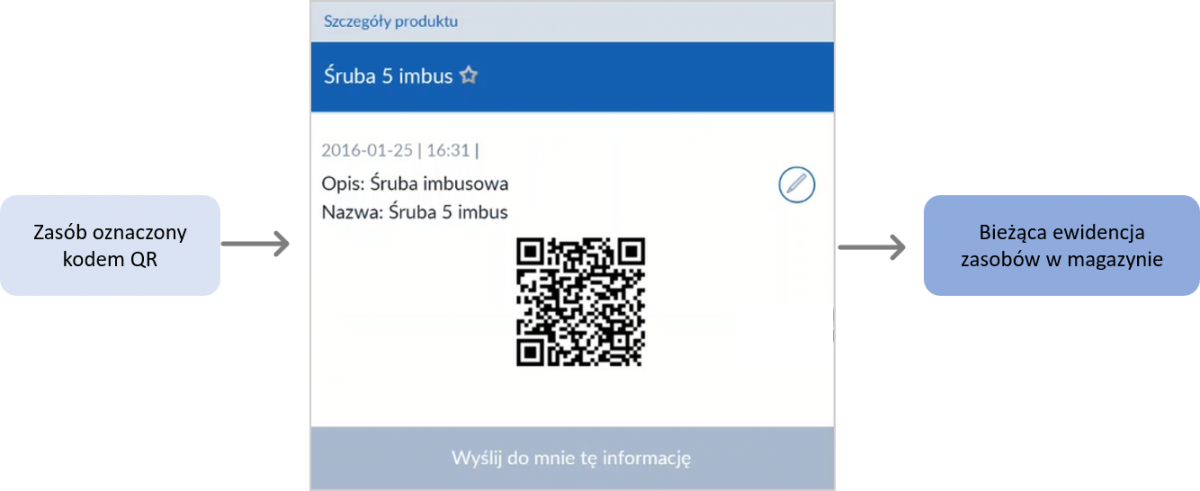
W momencie przekroczenia stanu minimalnego konkretnego zapasu, system generuje powiadomienie o konieczności jego uzupełnienia. Nadmiar zasobów, zgodnie z ideologią Lean, jest marnotrawstwem, a jego ograniczenie to zysk. Dzięki ciągłej kontroli zapasów nie zamrażasz gotówki w dodatkowych, niepotrzebnych towarach, ograniczasz czas przeznaczony na zarządzanie nimi i ograniczasz powierzchnię magazynową.
7. Wdrażaj ciągłe doskonalenie jako proces
Lean w technologiach produkcyjnych to ciągłe doskonalenie z jeszcze skuteczniejszą optymalizacją procesów i cyfryzacją narzędzi, upraszczającą wdrażanie tej metodologii. System CMMS może być solidnym wsparciem dla Ciebie w całym procesie.
Źródło: Wikipedia