Wywiady
Valeo – Innowacyjna intralogistyka w branży automotive
Valeo – Innowacyjna intralogistyka w branży automotive
Michał Odyniec, dyrektor zakładu produkcji wycieraczek Valeo w Skawinie, dostarczającego swoje produkty największym producentom aut na świecie, opowiada o szampańskich inspiracjach, digitalizacji, automatyzacji i robotyzacji transportu wewnątrzzakłądowego. Rozmawia Renata Poreda.
Renata Poreda, Biznes i Produkcja: Zanim porozmawiamy o innowacjach w kierowanym przez Pana zakładzie w Skawinie, proszę powiedzieć kilka słów o swojej ścieżce kariery i ewolucji Valeo, której był Pan świadkiem.
Michał Odyniec, Valeo: Zawodowo, od początku jestem związany z Valeo. 23 lata temu po studiach na Politechnice właśnie w Skawinie podjąłem swoją pierwszą pracę. Wtedy jeszcze nie było tu fabryki wycieraczek, a zakład produkcji chłodnic. Od razu zostałem wysłany na szkolenie do Francji. Przez kilka miesięcy miałem okazję pracować i uczyć się w zakładach Valeo zlokalizowanych 150 kilometrów na wschód od Paryża w okolicach Reims, stolicy Szampanii, regionu słynącego z produkcji win musujących znanych na całym świecie jako szampany. To była okazja, by nie tylko poznać nową kulturę pracy, której w Polsce jeszcze wówczas nie było, zobaczyć fabrykę na najwyższym poziomie zaawansowania technologicznego i organizacji, ale też zwiedzić niezwykle ciekawy region, z licznymi winnicami i zabytkami oraz zakosztować francuskiego stylu życia, z poranną kawą, croissantami, winem i doskonałą kuchnią. To było nie tylko ciekawe doświadczenie, ale też źródło inspiracji w całej późniejszej karierze.
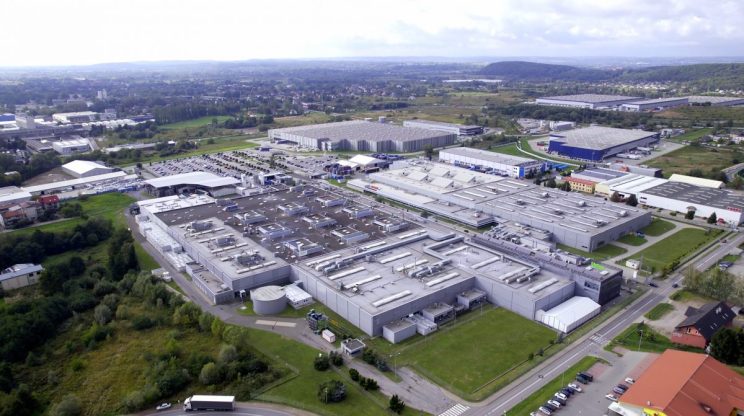
Po powrocie z Francji zacząłem pracować jako technolog w zakładzie chłodnic i od początku byłem zaangażowany w duże projekty rozwojowe, choć o automatyzacji czy robotyzacji wówczas jeszcze się nie mówiło. Koszty pracy w Polsce były niewielkie w porównaniu z tymi we Francji, więc nikt nie myślał o dodatkowej optymalizacji. Sam fakt, że fabryka działała w warunkach niskich kosztów był dla firmy źródłem dużych oszczędności. Ten zakład produkcji chłodnic bardzo dobrze funkcjonował zasilając większość klientów OEM (Original Equimpment Manufacturer) w Niemczech.
A jak to się stało, że w Skawinie powstał drugi zakład, którym obecnie Pan zarządza?
W naszej centrali w Paryżu powstał pomysł zdublowania mocy produkcyjnych w kierunku produkcji wycieraczek. W Europie mieliśmy kilka zakładów wytwarzających ich komponenty zlokalizowanych w Niemczech, we Francji, w Hiszpanii, ale brakowało jednego, dużego zakładu, który by zasilał głównie rynki niemieckie, przy niższych kosztach pracy. Zlokalizowanie takiego zakładu w Skawinie miałoby tę dodatkową zaletę, że klienci OEM z Niemiec, wysyłając transport po chłodnice, mogliby jednocześnie zabierać wycieraczki, co obniżałoby koszty.
Zakład produkcji wycieraczek powstał w Skawinie w 2003 roku, początkowo jako mała fabryka nastawiona głównie na tzw. produkcję aftermarketową, czyli wytwarzanie piór wycieraczek, które można kupić oddzielnie w supermarketach czy na stacjach benzynowych. Pierwszym projektem realizowanym dla klienta OEM, była produkcja wycieraczek dla Opli Corsa. Ich fabryka była zlokalizowana w Niemczech, relatywnie blisko. Potem przyszli kolejni, duzi odbiorcy.
Początkowo zlecaliśmy malowanie metalowych części wycieraczek na zewnątrz, ale w pewnym momencie, uznaliśmy, że możemy to robić sami. W końcu wycieraczki, zupełnie jak pierwsze Fordy T dostępne są w dowolnym kolorze, pod warunkiem, że jest to kolor czarny. Stworzyliśmy więc własną linię malowania, która była uruchamiana na przełomie lat 2006-2007. Malowanie odbywa się metodą kataforetyczną, a więc przez zanurzenie elementu w farbie rozcieńczonej wodą, przez którą przepływa prąd elektryczny. W następnym etapie nakłada się tzw. top coat – warstwę wierzchnią. Tak samo maluje się karoserie samochodowe, ponieważ wycieraczki tak jak reszta samochodu muszą spełniać ścisłe wymagania antykorozyjne.
W Skawinie obecnie powstają nie tylko wycieraczki, ale też elektryczne silniki, które je napędzają. Kiedy i w jakich okolicznościach ruszyła ich produkcja?
To kolejny kamień milowy w rozwoju naszego zakładu, w dodatku taki, z którego jestem niezwykle dumny. W latach 2008-2009 w związku z globalnym kryzysem nastąpił zastój inwestycyjny, ale już w latach 2012-2013, w Paryżu, w centrali grupy Valeo zaczęło się mówić o stworzeniu nowej fabryki silników do wycieraczek zasilanych prądem o napięciu 12V, zlokalizowanej w jednym z regionów o niskich kosztach pracy. Po serii rozmów i analiz, w grze zostały dwie lokalizacje: Skawina i Timisoara w Rumunii. W tamtym czasie, koszty pracy w Rumunii były znacznie niższe niż w Polsce, więc rachunek ekonomiczny przemawiał za wyborem Timisoary. Mi i poprzedniemu dyrektorowi fabryki, bardzo zależało jednak na tym, aby przekonać naszych francuskich szefów do polskiej lokalizacji tego zakładu. Przyjęliśmy następującą linię argumentacji: poza samymi kosztami pracy warto wziąć pod uwagę także inny czynnik, wydajność każdej z fabryk (efficiency). Wskaźnik wydajności podaje się w procentach. W idealnym świecie sięga on 100% ale to nigdy się nie zdarza. Po uwzględnieniu tego czynnika i przeliczeniu kosztów, wartość wyprodukowania jednej sztuki towaru w Polsce i w Rumunii była podobna. Tym argumentem udało nam się przekonać naszych francuskich szefów by produkcję silników do wycieraczek jednak uruchomić w Skawinie.
Gdy to się stało, nasz zakład doświadczył dynamicznego wzrostu. W latach 2013-2016 dwukrotnie zwiększyliśmy powierzchnię fabryki z 12,5 tys. do 25 tys. metrów kwadratowych. W sumie obecnie mamy 8 linii produkcyjnych, działających tak sprawnie, że w skali zakładu gotowy silnik zjeżdża z produkcji co 2 sekundy.
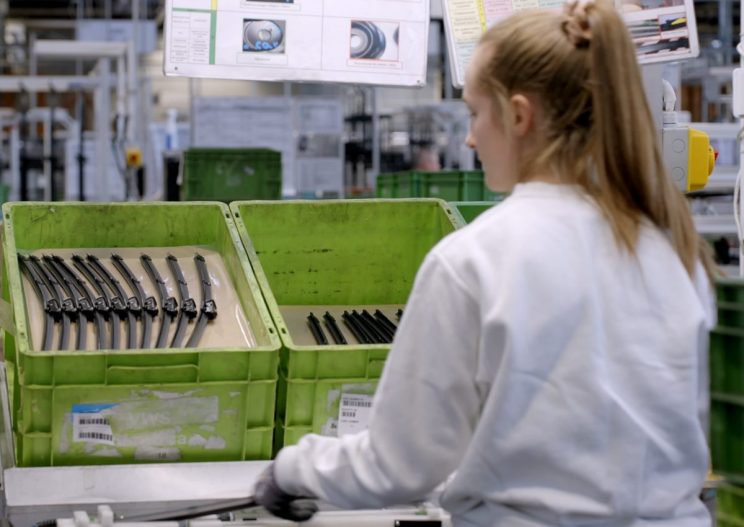
A jak na przestrzeni tych lat i w świetle doświadczeń związanych z rozwojem zakładu zmieniło się Pana postrzeganie innowacyjności?
Już od początku miałem pewien kontakt z innowacyjnością. Maszyny, które 23 lata temu przyjechały do Skawiny były naprawdę najwyższej klasy, ze sterowaniem PLC, kurtynami, barierami. Patrzyliśmy na nie z podziwem. Jednak od tamtego czasu moje postrzeganie innowacyjności nieco ewoluowało. Dziś wzorem innowacyjności jest dla mnie firma Apple, która w 2007 roku wprowadzając na rynek iPhone’a całkowicie zmieniła branżę. Później Steve Jobs powiedział, że kto trzyma w dłoniach iPada, trzyma cały internet. I rzeczywiście iPad czy szerzej tablet dzięki dostępowi do sieci może być niezrównanym źródłem informacji i wiedzy, także w kontekście przemysłowym. Dzisiaj tablety pomagają nam w codziennym zarządzaniu fabryką. Operatorzy w Skawinie mają dostęp do czegoś co nazywamy electronic work station. To cyfrowe repozytorium, w którym dostępne są wszelkie instrukcje i dokumentacje w wersji elektronicznej dostępne z poziomu tabletu. Dzięki temu rozwiązaniu nasza organizacja jest paperless, a więc scyfryzowana do tego stopnia, że papier nie jest potrzebny.
I jak rozumiem, nie chodzi tylko o ochronę klimatu i oszczędności, ale też o dostęp do danych.
Tak, chodzi o nieograniczony dostęp do danych w dowolnej chwili. Jeżeli maszyna czy linia produkcyjna pracuje 24 godziny na dobę, to wszystkie rekordy z tego procesu, czyli ilość wyprodukowanych sztuk towaru, braki czy przestoje są zapisywane w bazach danych. Później w każdym momencie można do tych zapisów wrócić by dokonać analizy. Kiedyś operator robił raporty produkcyjnie na papierze. Później dopiero były one skanowane do plików PDF albo nie. Trzeba było wynajmować dodatkowe magazyny by składować papierową dokumentację. Teraz mamy podpisaną umowę z firmą zewnętrzną, która zajmuje się archiwizacją danych w formie cyfrowej. Nie tylko zbierane są przez nią raporty, ale też surowe dane, które następnie po wpisaniu pewnych zapytań można przeszukiwać i analizować. Jeśli klient pyta nas, dlaczego w produkcie, który zjechał z linii montażowej półtora roku temu wystąpił defekt, możemy sprawdzić, kiedy wadliwy element był produkowany, kto był osobą odpowiedzialną, czy była przerwa w procesie, czy nastąpiła awaria. To pozwala zawęzić pole poszukiwań i szybko wyjaśnić sprawę.
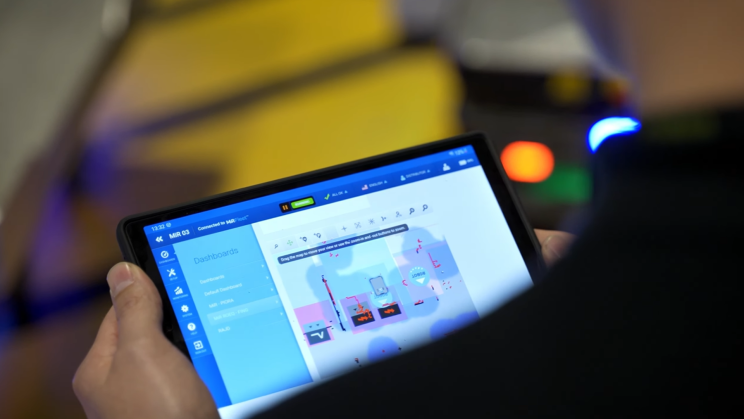
Sam koszt archiwizacji cyfrowej nie jest duży i spada. Dysk o pojemności kilku terabajtów można kupić za kilkaset euro i zapisać na nim bardzo dużo informacji. Pojemność dysku nie jest ograniczeniem, do tego stopnia, że my dublujemy dane na naszych macierzach dyskowych dla bezpieczeństwa, żeby były zapisane w różnych miejscach. Nawet w takim układzie koszt archiwizacji jest relatywnie niewielki.
Czy kolejny krok to sieci neuronowe i sztuczna inteligencja?
Dzisiaj problemem nie jest brak danych a ich nadmiar. Dane cyfrowe z raportów produkcyjnych, sterowników PLC maszyny, z serwonapędów, z robotów, to są miliony pozycji. Problem polega na tym jak wyciągnąć dane, których potrzebujemy. Właśnie o to toczy się gra by stworzyć systemy, które w sposób autonomiczny mogłyby przeszukiwać bazy danych i dzięki zastosowaniu odpowiednich zapytań wyłuskiwać cenne informacje. To jest właśnie zadanie dla sztucznej inteligencji. Ważne jest też by systemy te nie tylko umiały analizować przeszłość, ale też przewidywały przyszłość. Jak powiedział słynny kanadyjski hokeista, Wayne Gretzki, trzeba kierować się tam, gdzie krążek będzie, a nie tam, gdzie jest teraz. W takim paradygmacie muszą działać systemy obdarzone sztuczną inteligencją.
Zaawansowane systemy współczesnego przemysłu 4.0 to jednak nie tylko analiza danych, czy szeroko pojęta cyfryzacja, ale też automatyzacja i robotyzacja. Jak podchodzicie państwo do nich w Skawinie?
Zaczęliśmy od małych robotów MiR. W naszym zakładzie działają dwa „Mirki”– bo tak zaczęliśmy je nazywać. Transportują półprodukty między liniami technologicznymi. W dalszej kolejności dzięki współpracy z firmą ASTOR wprowadziliśmy na hale produkcyjne roboty Agilox, które są znacznie większe i przy udźwigu 1 tony są w stanie zastępować tradycyjne wózki widłowe. Przewożą towary gotowe do magazynu. Roboty obu typów poruszają się autonomicznie po wyznaczonych trasach i nie potrzebują operatora, taśm magnetycznych ani specjalnej infrastruktury.
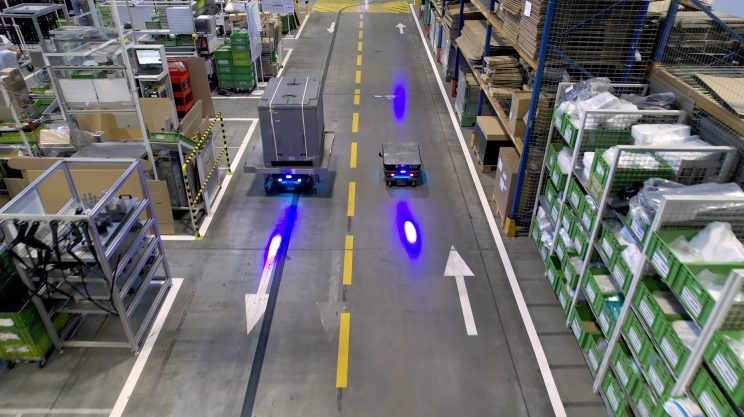
Roboty, z których jesteśmy bardzo zadowoleni, pozwalają nam pracować 24 godziny na dobę, nie chorują, nie biorą urlopów, zastępują ludzi w pracach monotonnych, powtarzalnych, uciążliwych i czasem niebezpiecznych. Jednocześnie ludzie potrzebni są do ich obsługi i programowania tras, ale też mogą zajmować się innymi zadaniami.
Wprawdzie początkowo potrzebowaliśmy instruktarzu ze strony firmy ASTOR – dostawcy technologii, ale obecnie w 99% przypadków możemy sami przeprogramować robota w zależności od tego jakie zadanie chcemy mu zlecić.
Wiele osób wręcz zgłasza się do tych zadań, dlatego, że praca z robotami jest dla nich przyjemnością, czy wręcz sposobem na samorealizację. To jest właśnie cecha czwartej rewolucji przemysłowej, że nie tylko nie zabiera ludziom pracy, ale wręcz pozwala im poszerzać kompetencje, dawać motywację do rozwoju. Osoby, które wcześniej jeździły na wózkach widłowych teraz programują roboty.
W wyniku automatyzacji część osób odchodzi, ale z drugiej strony branża wciąż zmaga się z niedoborami rąk do prac, wynikającymi z nieubłaganych trendów demograficznych. Dlatego właśnie korzyści z wykorzystania robotów wciąż przeważają nad zagrożeniami.
Co ciekawe swoistym produktem ubocznym zastosowania robotów intralogistycznych w naszym zakładzie był porządek. Wprawdzie Agiloxy są w stanie omijać przeszkody, ale wydają przy tym dźwięki i robią trochę zamieszania. Wszyscy wiedzą już, gdzie są trasy ich kursowania i pamiętają, żeby nie zastawiać ich zbędnymi przedmiotami, kartonami czy narzędziami. W efekcie podłoga na szlakach komunikacyjnych robotów lśni czystością.
Proszę powiedzieć, kiedy podjęliście państwo decyzję o zakupie robotów. Jakie były przesłanki do tego, żeby je zaimplementować?
W Polsce czas, w którym następuje zwrot z inwestycji nie jest aż tak spektakularnie krótki jak w krajach Europy Zachodniej, więc decyzje podjęliśmy około dwóch może trzech lat temu, licząc na oszczędności w dłuższym okresie. Naszą motywacją była jednak także chęć wpisania się w idee przemysłu 4.0, bo wierzymy, że takie podejście prędzej czy później przełoży się na realne korzyści. Dodatkowo był też aspekt wizerunkowy. Nasze zakłady są często odwiedzane przez klientów np. z firm Mercedes-Benz czy BMW. Pokazanie im nowoczesnej zrobotyzowanej fabryki owocuje wzrostem zaufania co z kolei przekłada się na nowe linie biznesowe.
Cała branża automotive jest na bardzo wysokim poziomie technologicznym, jeśli również dostawca ma zautomatyzowany i scyfryzowany zakład, jest o czym rozmawiać.
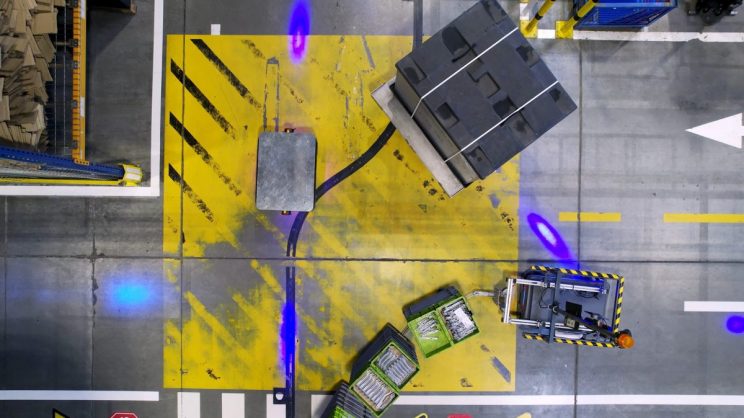
A jak widzi Pan przyszłość Valeo zakładu, którym Pan zarządza?
Wiele kierunków naszych działań wyznaczyły pandemia i wojna. Chcielibyśmy uniknąć sytuacji ponownego zerwania łańcuchów dostaw, dlatego jeśli to możliwe przenosimy produkcję bliżej. Dodatkowo ograniczając transport z Azji, zmniejszamy nasz ślad węglowy. Chcąc zabezpieczyć się na przyszłość dbamy o zróżnicowane źródła komponentów i półproduktów. Cała grupa Valeo coraz częściej stawia też na rozwiązania do aut elektrycznych. Fabryka Valeo w Czechowicach produkuje np. silniki elektryczne dla dużego niemieckiego dostawcy z branży automotive. Wycieraczki są wprawdzie podobne w samochodach spalinowych i elektrycznych, ale tu też stawiamy na innowacje. np. na integrację czujnika deszczu z silnikiem elektrycznym wycieraczki, systemy odmrażania wycieraczek, czy takie, które pozwalają równomiernie rozprowadzać płyn do spryskiwania po całej szybie.
Kończąc, czy mógłby Pan dać kilka rad zakładom przemysłowym, które zmierzają w stronę przemysłu 4.0?
Oczywiście.
- Należy dbać o optymalizację i automatyzację produkcji wdrażając je w taki sposób by produkować na poziomie wydajności właściwym dla danej technologii.
- Trzeba określić właściwy poziom robotyzacji i automatyzacji z punktu widzenia pracowników. Znaleźć właściwą równowagę pomiędzy zadaniami, które można zautomatyzować i tymi, do których realizacji potrzebni są ludzie.
- Nie można zapominać o digitalizacji, zbieraniu cyfrowych danych i pozbywaniu się papieru, zachowując otwartość na nowe rozwiązania.
Jeśli nie będziemy innowacyjni skończymy jak Nokia czy Kodak. Ta pierwsza firma nie wyobrażała sobie telefonu bez klawiatury. Ta druga nie wzięła pod uwagę potęgi cyfrowej fotografii, a dziś nie ma śladów ich potęgi. Lepiej uczyć się na cudzych błędach niż na własnych.
Valeo to globalna firma, która na całym świecie posiada niemal 200 zakładów produkcyjnych, 20 ośrodków badawczych, 39 centów rozwojowych i 15 platform dystrybucyjnych zatrudnia około 115 000 osób w 33 krajach i notowana jest na Paryskiej giełdzie. Fabryka wycieraczek w Skawinie jest największym zakładem produkującym tego rodzaju części w grupie Valeo i mieści się w pierwszej piątce zakładów tego typu na świecie.
Wywiad przygotowany na podstawie 10. odcinka Biznes i Produkcja Podcast „Inteligentne technologie, które wspierają intralogistykę w Valeo.”
Treść zredagowana i skrócona celem zwiększenia klarowności przekazu i przystosowania do formatu tekstowego.
Opracowanie: Paweł Górecki