Treści
Historia systemów MES, cz.1 – od planowania zasobów, aż do zarządzania produkcją
Historia systemów MES, cz.1 – od planowania zasobów, aż do zarządzania produkcją
Dostęp do bieżących, rzetelnych informacji o wszelkich procesach produkcyjnych to kluczowy element współczesnej fabryki. Właśnie dlatego systemy MES – Manufacturing Execution Systems, takie jak AVEVA MES cieszą się ogromną popularnością i wspierają coraz większą liczbę firm produkcyjnych w codziennej pracy. Jak jednak rozwiązania MES ewoluowały na przestrzeni lat? Jak zaczęła się ich historia i czy dotarliśmy do jej ostatniego etapu? Odpowiedź znajdziecie w poniższym artykule.
Ludzkie dłonie kluczowym zasobem?
Od wybuchu pierwszej rewolucji przemysłowej, aż do lat 70. XX wieku produkcja bazowała w dużej mierze na sile i sprawności ludzkich rąk. Pracownicy przychodzili do fabryki, obsługiwali rozmaite maszyny i, przy udziale mniejszych lub większych finansowych motywacji (np. pracy akordowej), wspierali fabryki w generowaniu bieżących zysków.
Wielość maszyn, stale rozbudowujące się fabryki, jak również rosnący popyt i możliwości nabywcze klientów powodowały jednak, że o ile skuteczność pracy przedsiębiorstw stale rosła, to ich efektywność – zaczynała stopniowo spadać. Brakowało systemów, które pozwoliłyby odciążyć zapracowanych inżynierów i zautomatyzować najprostsze procesy produkcyjne. Próżno było także szukać rozwiązań, które pozwolą w porę przewidzieć i uniknąć awarii maszyn. Tych zaś, z racji coraz bardziej intensywnej eksploatacji urządzeń, było coraz więcej.
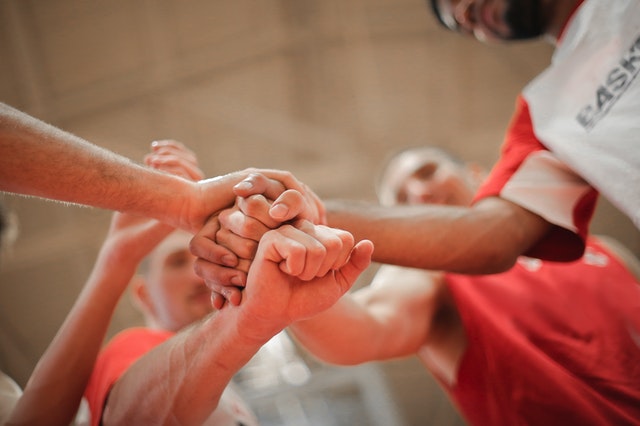
Narodziny systemów MRP – Material Requirements Planning
Jednym z pierwszych systemów, który pozwalał, choćby połowicznie, usprawnić pracę fabryki poprzez bieżące planowanie był MRP, czyli Material Requirements Planning. Tego rodzaju rozwiązanie zapewniało inżynierom wsparcie w trzech obszarach:
- jakich materiałów potrzebujemy?
- jak wiele materiałów potrzebujemy?
- kiedy powinniśmy je otrzymać?
Efektem zastosowania MRP była znacznie większa kontrola nad posiadanymi zasobami i zdolność do planowania produkcji z większym wyprzedzeniem. Ich popularność i użyteczność była tak duża, że wiele przedsiębiorstw do dziś korzysta z nich w bieżącej pracy. Trudno jednak w ich przypadku mówić o automatyzacji procesów produkcyjnych – systemy MRP sprawdzały się raczej jako cyfrowe wsparcie dla specjalistów produkcji. Z czasem były wypierane przez znacznie bardziej rozbudowane rozwiązania, z Enterprise Resource Planning (ERP) i HMI/SCADA na czele.
Drugi etap cyfrowej rewolucji
Zapoczątkowana w latach 70. XX wieku cyfrowa rewolucja objawiała się w fabrykach nie tylko w postaci systemów MRP. Jednym z najważniejszych rozwiązań w obszarze usprawniania procesów produkcyjnych było wdrożenie sterowników PLC, czyli uniwersalnych urządzeń, służących do obsługi prostych, małych i średnich systemów. Ich konstrukcja była wręcz rewolucyjna – zakładała umieszczenie algorytmu obsługującego urządzenie w jego pamięci, a nie w szeregu kabli zamkniętych w szafie sterowniczej.
Takie rozwiązanie umożliwiało wdrażanie zmian w schemacie działania maszyny bez konieczności modyfikowania jej części mechanicznej – wystarczyło przeprogramowanie sterownika. Znacząco przyspieszyło to efektywność funkcjonowania fabryk, pozwalając na dynamiczne dostosowywanie procesów do stanu materiałów (sygnalizowanego przez MRP) czy warunków popytowych. Pracownik nie musiał już obsługiwać maszyny jednego dnia przez 18h, a kolejnego przez 5h z powodu zmian w zapotrzebowaniu – w zamian po prostu modyfikował ustawienia sterownika.
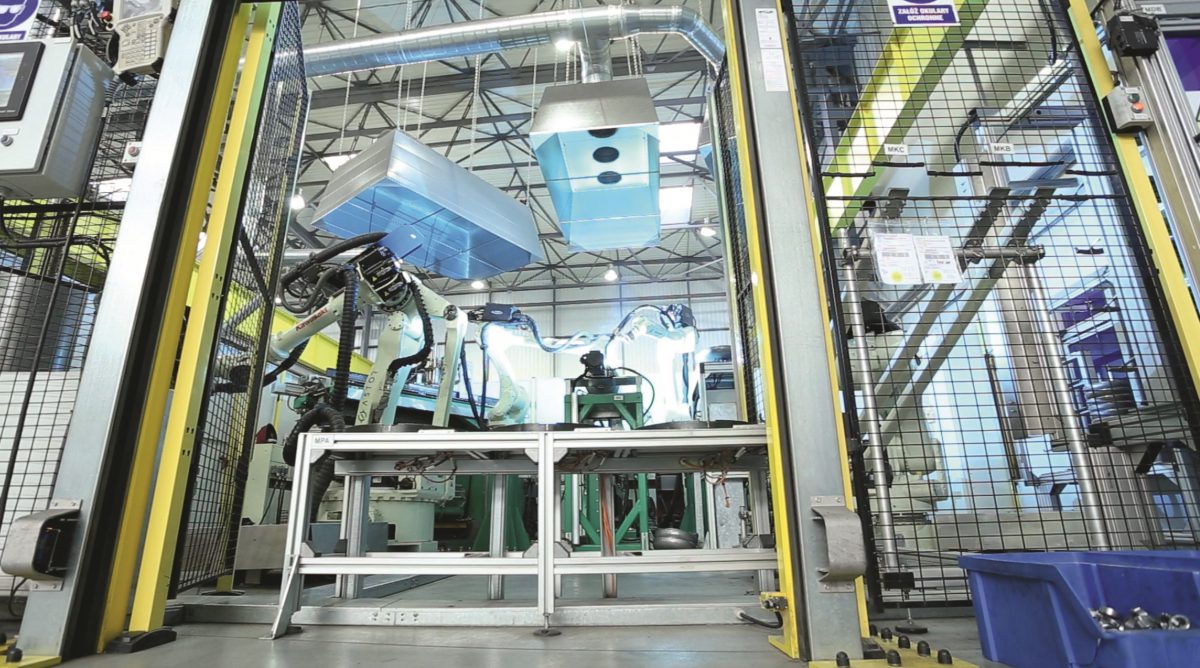
Sterowniki PLC są zresztą do dziś z powodzeniem wykorzystywane w firmach produkcyjnych. Przykładem jest choćby sterownik Astraada One ECC2000, dedykowany rozwiązaniom maszynowym i systemom automatyki budynkowej.
Niezwykle istotnym elementem cyfrowej rewolucji w firmach produkcyjnych było także stworzenie w latach 90. XX wieku systemów ERP, czyli Enterprise Resource Planning. Jak wskazuje ich nazwa, rozszerzały one paletę zadań, wykonywanych do tej pory przez wysłużone systemy MRP. Choć oba rozwiązania skupiały się na zarządzaniu zasobami, ERP pozwalało zintegrować bazową funkcję oprogramowania z takimi elementami jak:
- księgowość
- sprzedaż i marketing
- customer relationship management (CRM)
- zarządzanie dystrybucją
- zarządzanie jakością
Innymi słowy, systemy ERP gwarantowały bardziej holistyczne spojrzenie na bieżącą pracę przedsiębiorstwa. Maszyna i obsługujący ją pracownik nie stanowiły dzięki temu odrębnego bytu, a stały się częścią większej, zintegrowanej całości, połączonej rozmaitymi zależnościami.
Dużym wsparciem dla inżynierów i managerów były także rozwiązania spod szyldu HMI/SCADA, powstające już od wczesnych lat 70. XX wieku. Ich główna zaleta polegała na łączeniu rozmaitych urządzeń sterujących, pomiarowych i wykonawczych oraz operatora maszyn. Systemy te pozwalały także zbierać dane w czasie rzeczywistym, co pozwalało na bieżący nadzór nad procesem. Dzięki temu możliwe było stopniowe minimalizowanie ryzyka wystąpienia zastojów w produkcji czy też potencjalnych awarii.
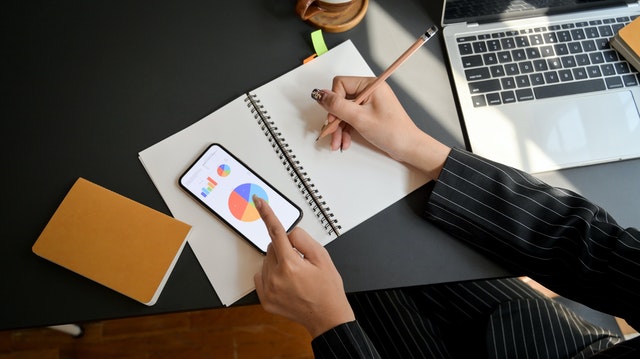
Ich wdrożenie było milowym krokiem na drodze do automatyzacji produkcji. SCADA reaguje bowiem na sygnały urządzeń w sposób zupełnie automatyczny, natychmiast wizualizując i przetwarzając dane. To spora zmiana w stosunku do choćby lat 60. XX wieku, kiedy wszelkie informacje na temat funkcjonowania maszyny były zamknięte w wypełnionej kablami szafie sterowniczej. Rozwojowi SCADA sprzyjały także narodziny sieci LAN, a w kolejnych latach, ogólnodostępnego Internetu. Dzięki tym innowacjom proces przesyłu danych był bowiem szybszy i łatwiejszy niż kiedykolwiek wcześniej.
Manufacturing Execution System (MES) – od zbierania danych po zarządzanie wydajnością produkcji
Na początku lat 90. rynek oprogramowania dla firm produkcyjnych był jednak świadkiem narodzin jeszcze jednego, niezwykle istotnego rozwiązania. Termin „MES”, czyli Manufacturing Execution System został użyty pierwszy raz przez organizację AMR Research w 1992 roku. Definiowała ona systemy klasy MES jako „rozwiązania pozwalające na efektywną i sprawną obsługę procesów produkcyjnych”. Choć początkowo MES powielał w dużej mierze funkcjonalności SCADA i koncentrował się na zbieraniu danych, z czasem wyewoluował w narzędzie, które nie tylko analizuje informacje, ale także na bieżąco zarządza produkcją. Co więcej, systemy MES przekształciły się w rozwiązania modularne, pozwalając ograniczać koszty i zwiększać efektywność procesów.
Jak jednak przebiegał rozwój MES na przestrzeni ostatnich 30 lat? W jaki sposób oprogramowanie do zbierania danych zmieliło się do postaci, którą znamy choćby z rozbudowanych systemów AVEVA MES? To temat na osobną historię – podejmiemy ją w drugiej części naszej MESowej opowieści.