Treści
Gromadzenie i raportowanie danych na miarę Przemysłu 4.0 – big data, IoT i chmura obliczeniowa
Gromadzenie i raportowanie danych na miarę Przemysłu 4.0 – big data, IoT i chmura obliczeniowa
W dobie intensywnej cyfryzacji wkraczającej zarówno do naszych domów, jak i firm produkcyjnych, ilość, jakość oraz sposoby gromadzenia informacji stają się niemałym wyzwaniem dla osób, które w oparciu o te informacje muszą podejmować kluczowe decyzje biznesowe dotyczące przedsiębiorstwa. Dynamiczny rozwój nowych technologii skupionych wokół inicjatywy Przemysłu 4.0 niesie ze sobą szereg sprawdzonych rozwiązań, które skutecznie mogą pomóc w zapanowaniu nad natłokiem informacji oraz znacząco usprawnić procesy ich pozyskiwania i analizowania.
Czasy big data
Ilość gromadzonych danych w firmach produkcyjnych przyrasta z roku na rok lawinowo. Aktualnie gromadzenie dużej ilości informacji na własnych serwerach jest stosunkowo łatwe technicznie. Problematyczne natomiast staje się efektywne wykorzystywanie zgromadzonych informacji i szybki oraz intuicyjny dostęp do tych, które w danym momencie są potrzebne. Kolejnym aspektem, na który trzeba zwracać znacznie większą uwagę niż wcześniej, jest wiarygodność gromadzonych danych. Ze względu na wielką ilość zebranych informacji łatwiej jest popełniać błędy na etapie ich wprowadzania oraz trudniej na etapie analizy odróżnić wiarygodne dane od tych niewiarygodnych.
Ten gwałtowny zwrot możliwości zbierania danych, jaki obserwujemy w ostatnich latach, wynika z dynamicznego rozwoju inteligentnych („smartnych”) urządzeń pomiarowych, które łatwo włączyć do sieci. Takie urządzenia wyposażone w możliwości dokonywania różnych pomiarów i posiadające rozbudowane funkcje komunikacji z innymi urządzeniami i z użytkownikiem tworzą tzw. Internet Rzeczy (ang. IoT, Internet of Things).
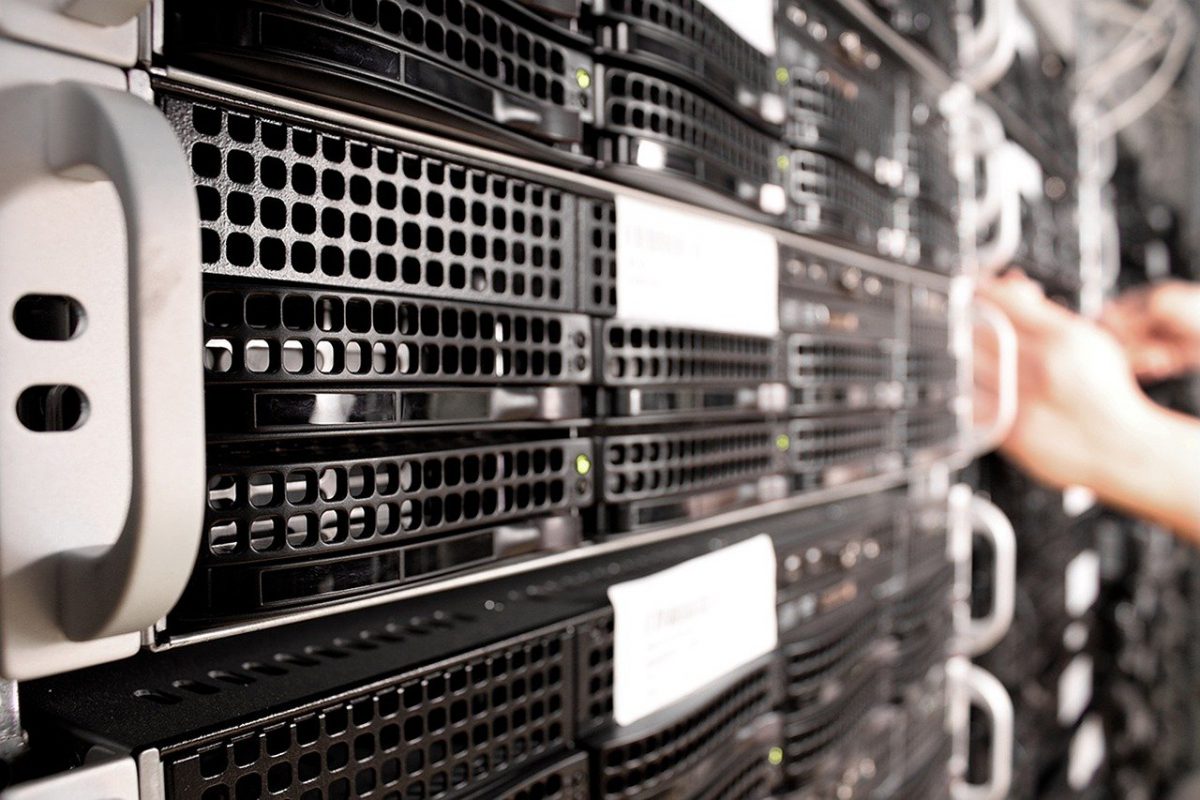
W odniesieniu do realiów produkcyjnych mówimy o Przemysłowym Internecie Rzeczy (ang IIoT, Industrial Internet of Things), na który składają się już nie tylko mierniki, analizatory i czujniki dedykowane wyłącznie dla przemysłu, ale także urządzenia mobilne, jak smartfony i tablety oraz urządzenia noszone jako element garderoby tzw. „wearables”, które mogą monitorować kondycję operatorów podczas pracy i przesyłać te informacje do centralnej bazy danych, która koreluje je z danymi dotyczącymi jakości i wydajności realizowanych czynności produkcyjnych.
Nie ilość, lecz jakość
Łatwość przechowywania dużych ilości danych w dzisiejszych realiach sprawia, że rejestrowanie w bazach danych wszelkich dostępnych informacji jest bardzo dużą pokusą. Okazuje się, że w rzeczywistości spośród wszystkich zgromadzonych danych, po okresie ogólnego entuzjazmu, często wykorzystywane jest poniżej 10% zgromadzonych danych, a do podejmowania właściwych decyzji wystarcza jeszcze mniej. Zagadnieniem, które jest dla nas interesujące, nie jest więc ilość, lecz odpowiednia jakość gromadzonych informacji.
Podniesienie jakości decyzji podejmowanych w oparciu o gromadzone dane wymaga skupienia się na sposobie ich gromadzenia oraz formie prezentacji i łatwości dostępu do przetworzonych danych – to dopiero one stają się wartościową informacją.
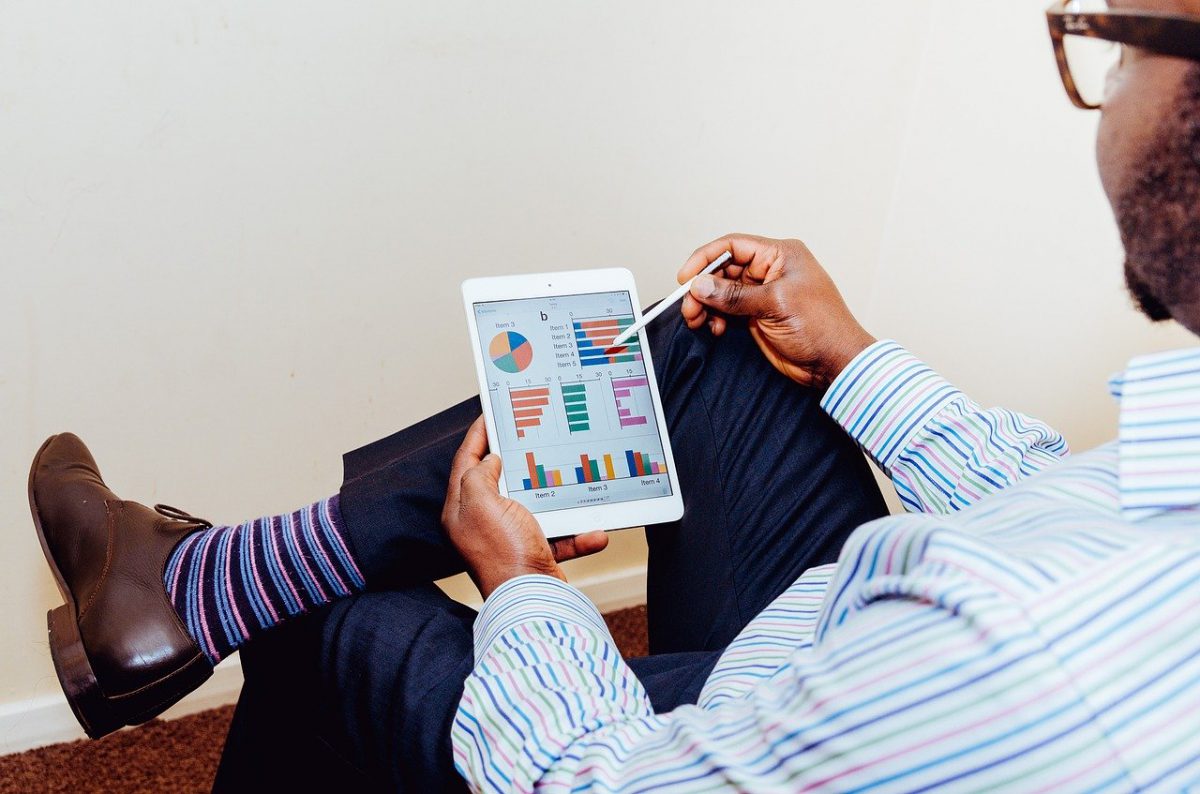
Z punktu widzenia firmy produkcyjnej najbardziej wiarygodne zawsze będą te dane, które zostaną zebrane za pośrednictwem inteligentnych czujników bezpośrednio z maszyn. Używając nazwy „inteligentne czujniki” mamy na myśli urządzenia, które oprócz zebrania danych będą w stanie w czasie rzeczywistym przesłać je do systemu analitycznego. Obecnie takie czujniki często mają już możliwości bezpośredniego cyberbezpiecznego połączenia z Internetem w celu przesłania danych do bazy danych w chmurze obliczeniowej.
W sytuacji, kiedy niestety nie da się w sposób w pełni automatyczny zebrać pomiarów i danych z produkcji (np. ze względu na typowo manualny charakter pracy), możliwe jest zastosowanie urządzeń takich jak panele operatorskie czy czytniki kodów kreskowych. Zastosowanie ich pozwoli przynajmniej na przyspieszenie pomiarów, a wcześniejsze przygotowanie algorytmów umożliwi bieżące prowadzenie operatorów przez proces i zapewni weryfikację danych już na etapie wprowadzania. Następnie sam panel operatorski lub koncentrator danych w postaci sterownika PLC prześle wiarygodne dane na serwer od razu po ich zarejestrowaniu.
Chmura obliczeniowa
Obecnie każdy z nas – korzystając chociażby z konta bankowego lub darmowego konta mailowego – powierza ważne dla siebie dane instytucjom lub firmom przechowującym je w chmurze obliczeniowej. Firmy te, zarządzając naszymi danymi, dbają także o ich bezpieczeństwo, poświęcając wielokrotnie większe środki na ich ochronę przed cyberprzestępcami niż sami bylibyśmy w stanie to zrobić. Dlaczego więc wciąż jeszcze z rezerwą podchodzimy do gromadzenia danych produkcyjnych w chmurze obliczeniowej?
Wiodący dostawcy rozwiązań IT dla przemysłu opierają swoją ofertę wyłącznie na wykorzystaniu centrów danych posiadających odpowiednie certyfikaty bezpieczeństwa. Nad bezpieczeństwem danych i prewencją przed niepowołanym dostępem czuwa sztab ludzi wyposażonych w najnowocześniejsze technologie do obrony przed cyberatakami. Należy wspomnieć także, że dane przechowywane w ten sposób są również zabezpieczane przed innego rodzaju zagrożeniami, jak np. klęski żywiołowe – redundancja danych w centrach obliczeniowych zlokalizowanych w zupełnie różnych lokalizacjach geograficznych jest już standardem.
W dobie Przemysłu 4.0 przekazanie danych produkcyjnych do chmury obliczeniowej jest przedsięwzięciem niezwykle prostym. Zamiast zapisu danych na lokalnym serwerze należy wykorzystać tzw. „IoT Gateway” do zagregowania danych z maszyn i bezpiecznego przesłania ich na serwer w chmurze obliczeniowej. Następnie, korzystając z narzędzi analitycznych, np. Wonderware Online, możliwe jest analizowanie zgromadzonych danych z dowolnego miejsca na świecie z wykorzystaniem dowolnego urządzenia z dostępem do Internetu i przeglądarką internetową obsługującą standard HTML5.
Korzyści wynikające z przeniesienia danych produkcyjnych do chmury obliczeniowej są stosunkowo łatwe do wyliczenia, ponieważ na kwestie finansowe przekłada się bezpośrednio brak konieczności inwestycji we własne kosztowne serwery oraz brak kosztów związanych z ich utrzymywaniem, zarządzaniem i dbaniem o bezpieczeństwo, co często może znacząco przekraczać koszty samej inwestycji. Dodatkowe korzyści to wspomniany już bezpieczny dostęp do danych w dowolnym momencie, z dowolnego miejsca na świecie.
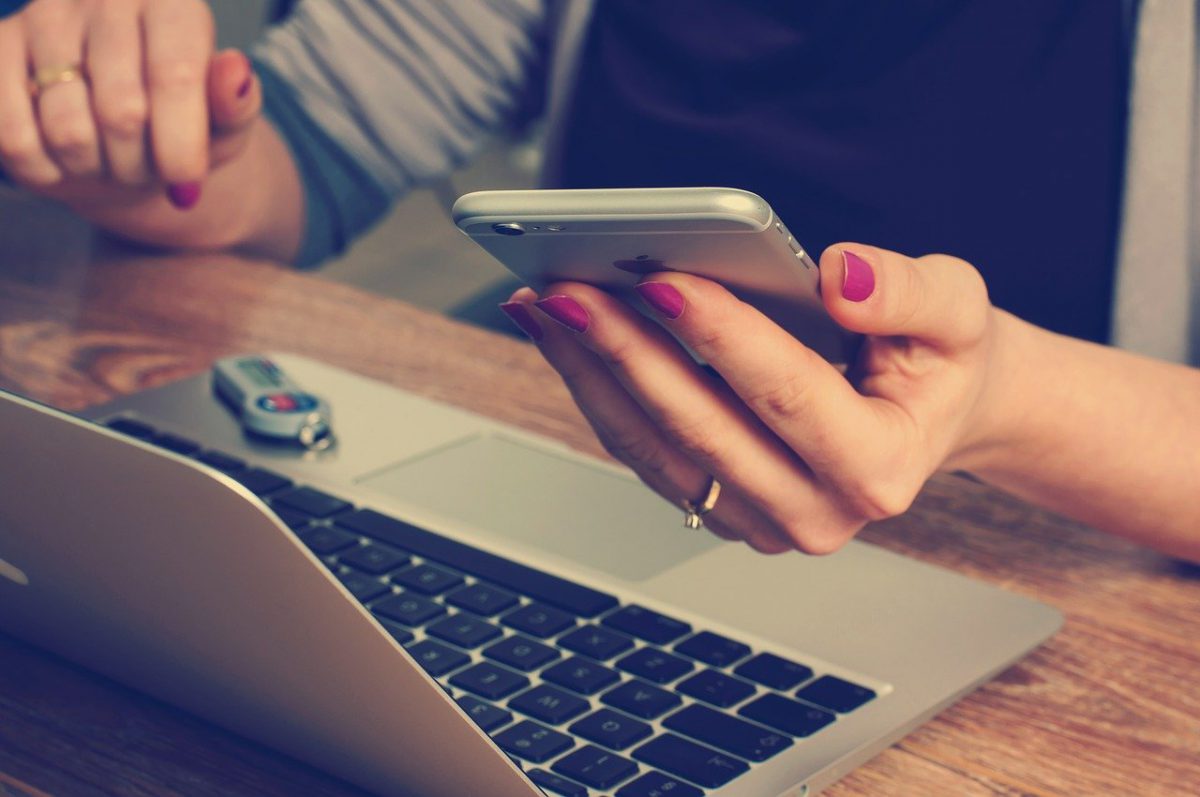
Raportowanie on-line w erze Przemysłu 4.0
W momencie, gdy zdecydujemy się na zautomatyzowanie procesu gromadzenia danych oraz ich archiwizację w chmurze obliczeniowej, możemy rozpocząć korzystanie z narzędzi analitycznych, pozwalających na dostęp do informacji aktualizowanych w czasie rzeczywistym. Rozwiązania takie, jak np. Wonderware Online InSight, dają użytkownikom możliwości tworzenia predefiniowanych dashboardów – bazujących na gromadzonych i aktualizowanych danych – a także definiowania indywidualnych raportów, którymi twórcy mogą dzielić się innymi użytkownikami w firmie lub po prostu osadzić wybrany raport w systemie wizualizacji, andonie lub na wewnętrznej firmowej stronie internetowej.
Ciekawą możliwością, jaką daje system tego typu, jest funkcja alarmowania o anomaliach w ciągu logowanych danych, przez co z łatwością możemy zauważyć nagłą i nieoczekiwaną zmianę w istotnym parametrze produkcyjnym lub wskaźniku KPI.
A zatem, menedżerowie i inżynierowie Przemysłu 4.0 już dziś otrzymują do dyspozycji narzędzia pozwalające na komfortową i wydajną pracę oraz współpracę w zespole. Automatyzacja procesu gromadzenia danych oraz wykorzystanie technologii przetwarzania danych w chmurze obliczeniowej pozwalają na znaczące przyspieszenie procesu podejmowania decyzji i zwiększenie ich trafności. W zakładzie wyposażonym w te technologie rosną szanse, że właściwe decyzje zapadną we właściwym czasie.