Treści
Czym zajmuje się nowoczesne Utrzymanie Ruchu i jak wspiera je system CMMS?
Czym zajmuje się nowoczesne Utrzymanie Ruchu i jak wspiera je system CMMS?
Chyba wszyscy dyrektorzy i menedżerowie technicznych firm przemysłowych zdają sobie sprawę, jak duży wpływ na działalność całego przedsiębiorstwa może mieć właściwe zarządzanie utrzymaniem ruchu.
Zarówno odpowiednia kalkulacja zysków i strat, jak i działania profilaktyczne, pomagają maksymalnie wykorzystywać park maszynowy, zmniejszając ryzyko nieplanowanych przestojów. Jak wiadomo, przerwy w produkcji generują wysokie straty, co prowadzi do pogorszenia sytuacji ekonomicznej przedsiębiorstwa oraz utraty jego konkurencyjności.
Wprawdzie działania profilaktyczne, takie jak inspekcje oraz przeglądy prowadzone przez dział Utrzymania Ruchu, również generują koszty, niemniej jednak są one mniejsze od kosztów wynikających ze wstrzymania produkcji. Obecnie działania te wspierane są przez nowoczesne narzędzia, które w znacznym stopniu przyczyniają się do zwiększenia wydajności codziennej pracy działu Utrzymania Ruchu. Właśnie dlatego tak ważny jest bilans zysków i strat, dotyczący wszystkich czynności wykonywanych przez Utrzymanie Ruchu.
Czym jest Utrzymanie Ruchu?
Dział Utrzymania Ruchu (UR) wiąże się bezpośrednio z produkcją, nie oznacza to jednak, że jest podległy działowi produkcji. Łączy je wspólny cel: zapewnienie ciągłości procesów produkcyjnych.
Dział Utrzymania Ruchu, nazywany bywa też działem technicznym. Jego zadaniem jest pełne wykonanie strategii eksploatacji majątku, czyli najprościej mówiąc, dbanie o jak najbardziej efektywną pracę znajdujących się na produkcji maszyn w taki sposób, aby przestoje i awarie zdarzały się jak najrzadziej.
W praktyce dział Utrzymania Ruchu wykonuje ogrom czynności: od sprawowania dozoru technicznego i zarządzania cyklem życia obiektów (maszyn, urządzeń, infrastruktury, instalacji), poprzez nadzorowanie prac zwiększających efektywność działań parku maszynowego, aż po monitorowanie rentowności maszyn czy zgodności prac z obowiązującymi przepisami.
Co jednak najważniejsze, z perspektywy współpracowników z innych działów, prace UR wiążą się z logistyką, a także relokacjami kluczowych maszyn (a nawet całych linii), w celu zapewnienia bezpieczeństwa ludziom i środowisku.
Aby praca służb Utrzymania Ruchu była wydajna, cały dział ma określoną strukturę organizacyjną – płaską lub hierarchiczną. Poniżej zobrazowaliśmy role i poziomy przykładowej struktury. Warto jednak pamiętać, że jest to tylko jedna z możliwych opcji, w każdej firmie taka struktura może wyglądać inaczej.
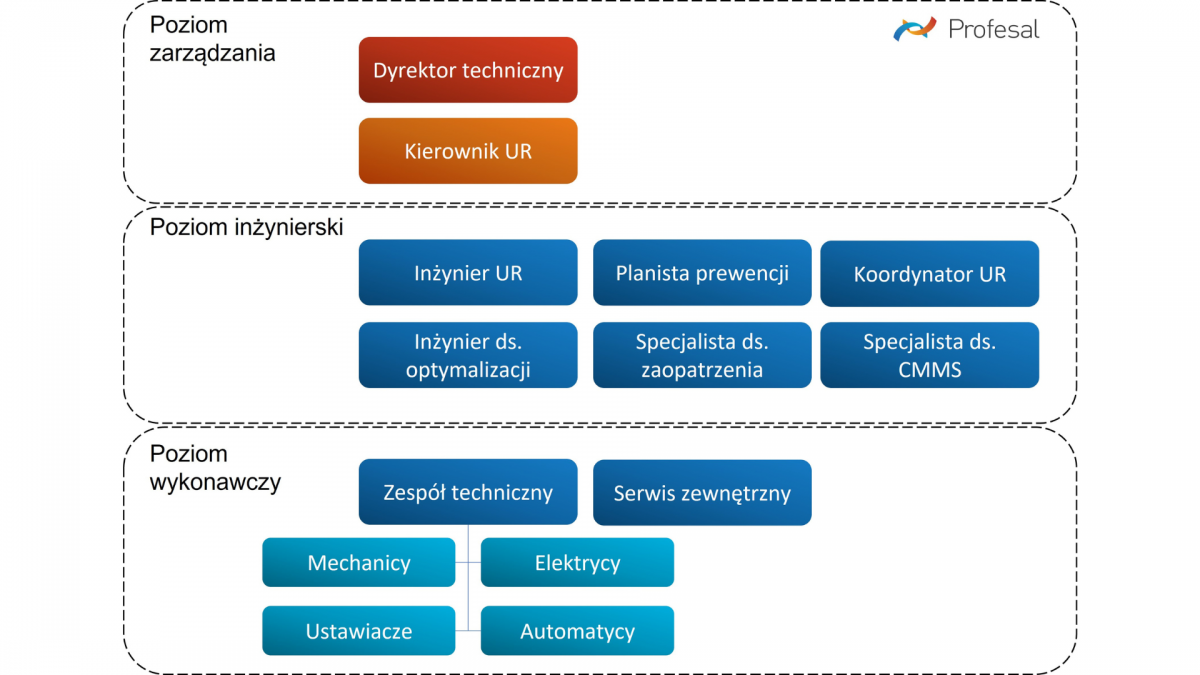
Za co odpowiada Utrzymanie Ruchu?
Główna odpowiedzialność służb Utrzymania Ruchu to realizacja wcześniej ustalonej strategii zarządzania technicznego, w której skład wchodzą misja, wizja, cele i plan zarządzania majątkiem.
Aby zrealizować tę strategię, potrzebny jest szereg codziennych zadań, jakie mają do wykonania służby Utrzymania Ruchu.
Do najważniejszych z nich należy nadzorowanie pracy maszyn i urządzeń, wykorzystywanych aktualnie do produkcji. Pracownicy SUR sprawdzają, czy narzędzia pracy użytkowane są zgodnie z przeznaczeniem, a jeśli zauważą odstępstwa od normy – edukują. Działania te związane są ściśle z zapewnieniem bezpieczeństwa pracownikom i z ochroną samych maszyn.
W realizacji tego zadania znaczącą rolę pełnią dwie kwestie: prowadzenie kompletnej dokumentacji oraz rzetelne zarządzanie informacjami dotyczącymi majątku firmy, które są przekazywane wewnątrz przedsiębiorstwa. Informacje te muszą być zgodne z przyjętymi dyrektywami, standardami oraz normami obowiązującymi w branży. Co ważne, dane powinny być przejrzyste i łatwo zrozumiałe dla wszystkich zainteresowanych.
Jeśli firma posiłkuje się środkami outsourcingowymi w zakresie podtrzymania prawidłowego stanu infrastruktury technicznej, służby Utrzymania Ruchu odpowiedzialne są za stały kontakt z kontrahentami oraz nadzorowanie wykonywanych przez nich prac.
Oprócz kwestii typowo operacyjnych, służby UR skupiają się także na osiąganiu jak najwyższej dostępności technicznej maszyn i urządzeń. W tym celu stosują techniki prowadzące do skrócenia czasu przestojów, zarówno tych planowanych, jak i nieplanowanych.
Aby wypracować właściwe techniki niezbędne jest analizowanie danych historycznych. W związku z tym, dział Utrzymania Ruchu odpowiada też za analizę i zarządzanie ryzykiem technicznym obiektów oraz monitorowanie wskaźników efektywności. Ma to wpływ również na analizę rentowności zasobów technicznych oraz na propozycje optymalizacji procesów.
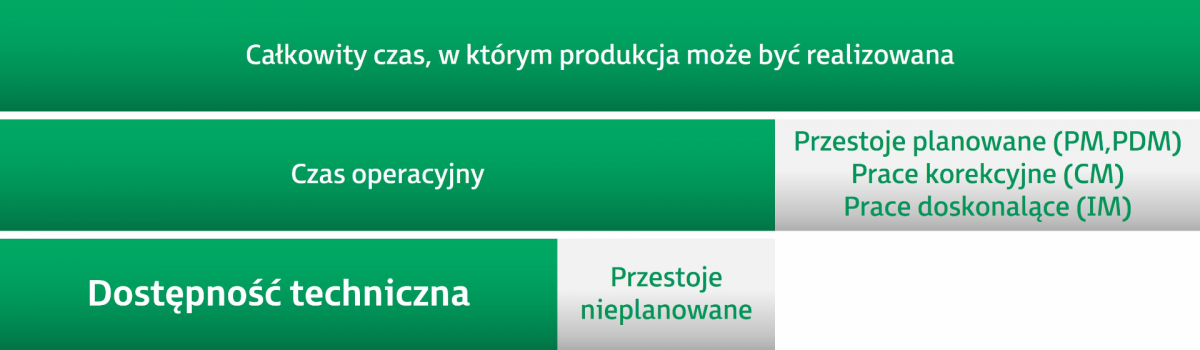
Co jednak w przypadku, gdy pojawiają się nieprawidłowości i zbyt niskie wartości obserwowanych wskaźników? W takiej sytuacji UR odpowiada za projekty inwestycyjne, takie jak: modernizacje maszyn, relokacje całych parków maszynowych oraz remonty obiektów, zarówno techniczne, jak i te o charakterze rozwojowym i optymalizacyjnym, które zwiększają możliwości produkcyjne.
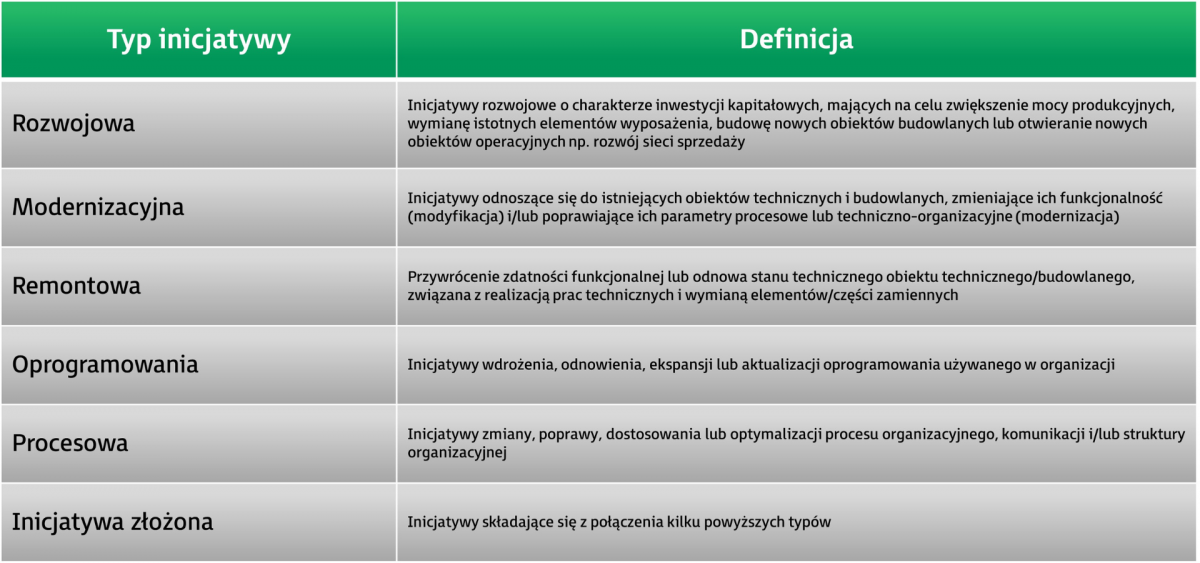
Jakie zadania ma Utrzymanie Ruchu?
Zadania jakie wykonuje dział Utrzymania Ruchu (DUR) możemy podzielić na kilka segmentów:
Planowanie i realizacja działań konserwacyjnych – inspekcje i audyty, a także planowanie wszelkich przestojów mających na celu zapobieganie awariom i przygotowanie do większych prac remontowych oraz naprawczych. Oznacza to również przygotowanie harmonogramów i rejestrowanie wykonywanych prac prewencyjnych (przeglądów kontrolnych, badań diagnostycznych i napraw) oraz ich raportowanie i dostosowywanie do planów produkcji.
Wiąże się z tym:
- Tworzenie i modyfikowanie przypisanych do maszyn list kontrolnych.
- Weryfikacja cyklów przeglądów w zależności od czasu lub przebiegu maszyn i dostępnych środków.
- Raportowanie rezultatów i kosztów działań prewencyjnych.
Reakcja na nieplanowane przestoje i ich eliminacja – przyjmowanie, analiza oraz priorytetyzacja awarii, szybka reakcja na nieplanowane przestoje, a także dokładna rejestracja zdarzenia dla celów dalszej identyfikacji przyczyny źródłowej. Zadania związane z eliminacją nieplanowanych przestojów to również zapisywanie historii napraw oraz opracowywanie procedur awaryjnych dla zachowania ciągłości produkcji.
Wiąże się z tym:
- Spisywanie części lub usług zewnętrznych, związanych z daną awarią.
- Kompleksowe oraz tymczasowe naprawy, wykonywane zależnie od potrzeb.
- Raportowanie wystąpień, tendencji oraz kosztów takich przestojów.
Zarządzanie gospodarką części zamiennych – logistyka części zamiennych oraz środków eksploatacyjnych, monitorowanie rozchodów oraz śledzenie stanów magazynowych. Niejednokrotnie dotyczy również planowania zakupu materiałów potrzebnych do konserwacji sprzętu.
Wiąże się z tym:
- Raportowanie kosztów rozchodów magazynowych z podziałem na obiekty i zdarzenia.
- Optymalizacja kosztów stoków magazynowych, zależnych od zużycia w danym okresie.
Ewidencja, komunikacja oraz zarządzanie informacjami i dokumentacją – zapisywanie i aktywizowanie informacji o obiektach technicznych, ich dokumentacji oraz zgodności z obecnymi normami formalnymi i dyrektywami.
Wiąże się z tym:
- Zarządzanie wiedzą personelu technicznego oraz kompetencjami pracowników.
- Jasne i klarowne przekazywanie wszystkim pracownikom informacji o wszelkich zmianach.
Analizy i monitorowanie KPI utrzymania ruchu – śledzenie krytyczności obiektów i części zamiennych, rentowności maszyn oraz całych kompleksów. Ważna jest też analiza kluczowych wskaźników efektywności Utrzymania Ruchu oraz ogólna dostępność techniczna maszyn.
Wiąże się z tym:
- Analiza kosztów całkowitych Utrzymania Ruchu oraz pozostałych projektów inwestycyjnych.
Współpraca z dostawcami zewnętrznymi – polega na zarządzaniu komunikacją i warunkami współpracy, a także na monitorowaniu zmian rynkowych oraz dostępności asortymentu i usług. Do tych zadań zalicza się też harmonogramowanie działań kontraktorów zewnętrznych oraz weryfikacja i odbiór wykonanych przez nich prac.
Monitoring mediów – śledzenie zużycia energii przez poszczególne obiekty oraz analizy służące optymalizacji w tym zakresie, a także zarządzanie gospodarką odpadową.
Wsparcie BHP – zarządzanie bezpieczeństwem nie tylko maszyn, ale też pracowników, którzy je użytkują. Wiąże się to z zabezpieczaniem miejsc potencjalnie niebezpiecznych oraz z analizą ryzyka przy codziennym użytkowaniu.
Przedstawione powyżej przykłady to najważniejsze, ale nie wszystkie zadania działu Utrzymania Ruchu. Możemy wspomnieć jeszcze o zajmowaniu się naprawami biurowymi, pisaniu instrukcji dla zgodności z normami ISO, wypełnianiu danych w systemach informatycznych, np. CMMS, szkoleniu nowych pracowników, codziennych obchodach czy koordynowaniu autonomicznych prac konserwacyjnych wykonywanych przez wykwalifikowanych operatorów.
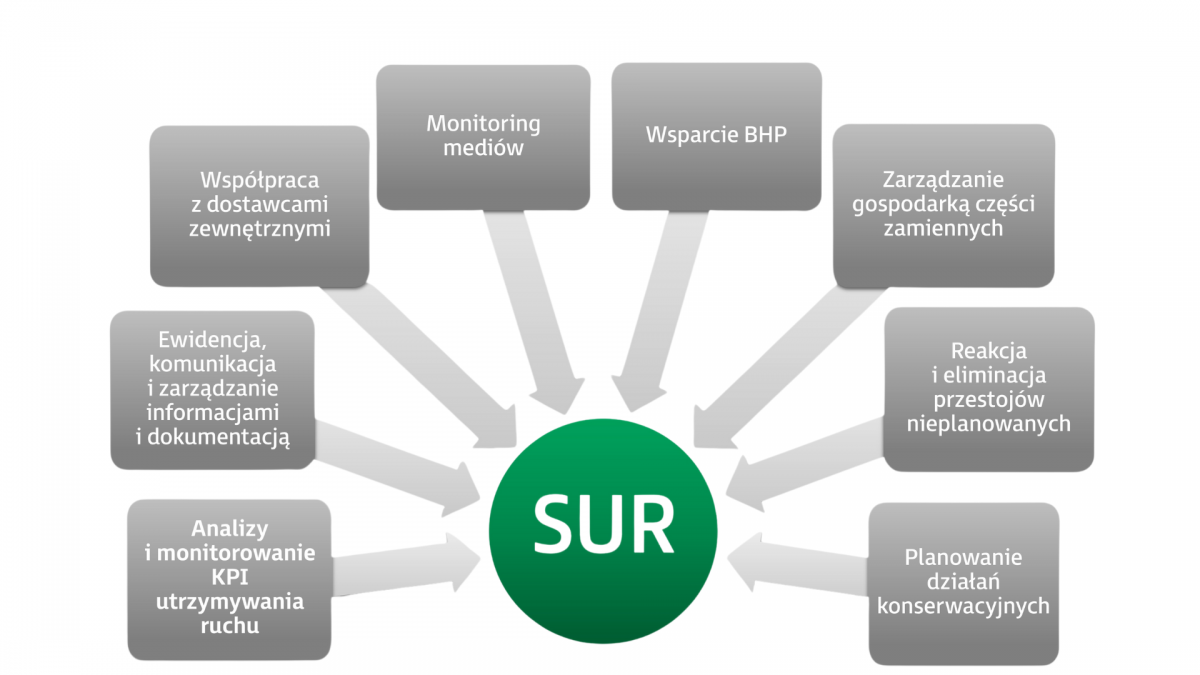
Jakie metody stosuje się w nowoczesnym Utrzymaniu Ruchu?
Nowoczesne Utrzymanie Ruchu coraz częściej jest wspierane przez metodyki, narzędzia i rozwiązania cyfrowe, które pomagają w możliwie najbardziej efektywny sposób wykorzystać zasoby zarówno działu UR, jak i produkcji.
Jedną z metod, która usprawnia działania konserwacyjne jest strategia Total Productive Maintenance (TPM). Jej celem jest osiągnięcie maksymalnej efektywności w zakresie wykorzystania narzędzi oraz zaangażowania pracowników UR i produkcji. TPM wpływa również na poprawę współpracy tych dwóch działów. Pracownicy produkcji zyskują znacznie większą świadomość w kwestii konserwacji, co w efekcie wspiera techniczną dostępność maszyn, a także minimalizuje czasy przestojów. To sprawia, że Utrzymanie Ruchu może skupić swoje działania na bardziej krytycznych czynnościach.
Jeśli interesują Cię narzędzia wspomagające nowoczesne Utrzymanie Ruchu, w tym np. systemy CMMS, zapoznaj się z ofertą polskich producentów takiego oprogramowania.
Nowoczesną i popularną obecnie metodą obsługi technicznej jest predykcyjne utrzymanie ruchu. Polega ono na wykorzystaniu parametrów technicznych maszyn, dostarczanych za pomocą czujników (zintegrowanych lub zewnętrznych) i reagowaniu kiedy pojawia się informacja o pogorszenia pracy maszyny lub procesu. Parametry, które mogą pomóc w szybkim wykryciu problemu to m.in. wibracje, temperatura i wilgotność, poziomy płynów, akustyka, nacisk i obroty czy zużycie energii elektrycznej podczas pracy. Przekazywane dane muszą być dostosowane do procesu, który chcemy monitorować.
Wykorzystanie czujników oraz pozyskiwanie z nich danych możemy uprościć wykorzystując system SCADA (Supervisory Control and Data Acquisition). To oprogramowanie odpowiedzialne za nadzór, pozyskiwanie i katalogowanie danych z procesu. Na podstawie dostarczonych danych, SCADA może wizualizować cały proces produkcyjny wraz ze wszystkimi parametrami, a w przypadkach niezgodności wysyłać alarmy do działów Utrzymania Ruchu oraz produkcji. Co więcej, odpowiednio rozmieszczone czujniki pozwalają odtworzyć w systemie czynniki, od których rozpoczęła się awaria, ułatwiając tym samym wykrycie i eliminację przyczyny źródłowej.
Mówiąc o nowoczesnym utrzymaniu ruchu często wymienia się system CMMS, jako jedno z najpopularniejszych i najbardziej rekomendowanych rozwiązań dla działów technicznych. CMMS pozwala, między innymi na:
- gromadzenie danych i parametrów z maszyn,
- planowanie i harmonogramowanie prac,
- koordynowanie działań reakcyjnych,
- rejestrowanie historii awarii,
- monitorowanie gospodarki części zamiennych,
- dokonywanie automatycznych analiz KPI (dzięki wbudowanym modułom raportowym).
Jak CMMS zwiększa efektywność pracy SUR?
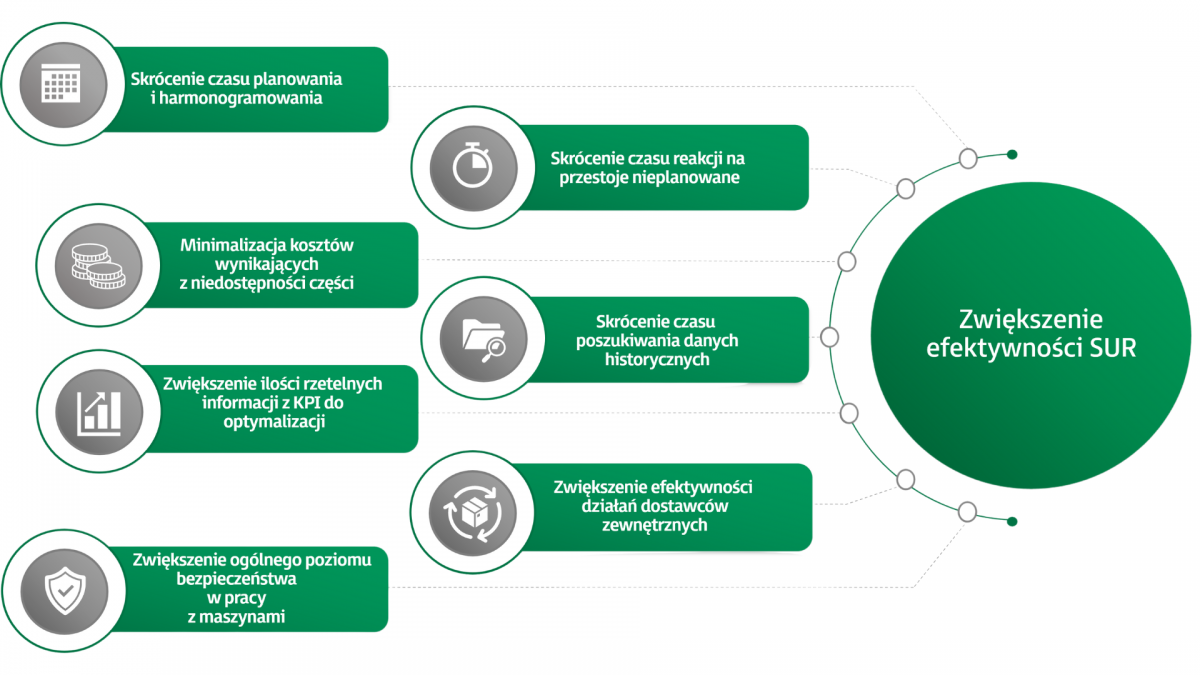
Dzięki automatycznym, cyklicznym przeglądom, realizowanym na przykład po upływie z góry ustalonego czasu lub określonej ilości motogodzin maszyn, CMMS skraca czas planowania i komunikowania działań konserwacyjnych. System wysyła przypomnienia do pracowników czy firm zewnętrznych o zbliżającym się terminie i pozwala koordynować te działania z produkcją.
Dzięki osobnym modułom do generowania zgłoszeń awarii czy usterek przez operatorów lub brygadzistów, CMMS skraca czas przekazywania informacji, a co za tym idzie skróceniu ulega też czas reakcji na awarie. System zapisuje wszystkie niezbędne informacje o zdarzeniach. Odnotowane w ten sposób dane mogą później służyć jako historia awarii dla pozostałych techników lub zostać wykorzystane do wprowadzenia optymalizacji.
Moduły magazynowe w systemie dla Utrzymania Ruchu są dostosowane tak, aby śledzić rozchody oraz rezerwacje części zamiennych (najczęściej za pomocą aplikacji mobilnych), nadzorować stany magazynowe i informować o brakach. Dzięki ciągłej kontroli niwelujemy koszty wynikające z przestoju spowodowanego brakiem części przy awariach czy przeglądach.
Cyfryzacja ewidencji maszyn ułatwia przedstawianie danych podczas audytów, a zdigitalizowana dokumentacja znacząco skraca czas poszukiwania informacji, kart awarii czy list kontrolnych.
Automatyczne raporty i analizy pozwalają na monitorowanie wskaźników efektywności Utrzymania Ruchu w czasie rzeczywistym, na podstawie danych wprowadzanych na bieżąco przez wszystkich użytkowników.
Dodatkowo CMMS jako system dla Utrzymania Ruchu może zostać zintegrowany z wcześniej wspomnianym systemem SCADA, aby automatycznie generować zlecenia awaryjne dla techników o odpowiednich kwalifikacjach. W podobny sposób, przy bezpośredniej integracji z czujnikami, system może generować automatyczne zlecenia przeglądów oparte o motogodziny lub parametry maszyn.
Nowoczesne Utrzymanie Ruchu stale mierzy się z przeciwnościami losu, które wpływają na prawidłowe funkcjonowanie przedsiębiorstwa. Zaburzenie ciągłości realizowanych procesów i potencjalne pogorszenie sytuacji ekonomicznej firmy nie są jedynymi problemami, jakie mogą nastąpić. Mnogość działań, nad jakimi UR sprawuje opiekę wiąże się z koniecznością nie tylko wypracowania odpowiednich technik umożliwiających bieżące zarządzanie kluczowymi zadaniami, ale i szukania rozwiązań, które te prace usprawnią i pozwolą na osiągnięcie maksymalnej efektywności na wielu płaszczyznach.