Treści
Cyfrowy bliźniak — metawersum dla Twojej fabryki
Cyfrowy bliźniak — metawersum dla Twojej fabryki
Wirtualna symulacja poszczególnych maszyn, linii produkcyjnych czy całego biznesu pozwala z wyprzedzeniem wykrywać nieprawidłowości, lepiej gospodarować zasobami, testować bez ryzyka. W branży produkcyjnej i nie tylko, znaczenie tzw. cyfrowych bliźniaków stale rośnie.
Posiedzenie zarządu, spotkanie biznesowe, konferencja albo spotkanie o charakterze towarzyskim, tak jak w rzeczywistości, ale inaczej, bo wszyscy uczestnicy są obecni w postaci awatarów. Mogą dyskutować, gestykulować, prowadzić negocjacje czy rozmowy handlowe, niezależnie od tego, w której części świata się znajdują. To metawersum, nowy wymiar internetu, który pozwala spotykać się w świecie cyfrowym, będącym kopią rzeczywistego. Koncepcji tej na razie często towarzyszy szum medialny, ale idea wiernego odwzorowywania realnego świata w przestrzeni cyfrowej jest już rzeczywistością. Tzw. cyfrowe bliźniaki ułatwiają obsługę linii produkcyjnych, projektowanie, prace inżynierskie oraz zarządzanie łańcuchem dostaw. Jak działa to przemysłowe metawersum i jakie jeszcze korzyści może zaoferować menedżerom produkcji i kierowanym przez nich fabrykom?
Cyfrowy bliźniak – definicja
Według definicji Gartnera cyfrowy bliźniak (digital twin) to wirtualna reprezentacja realnego obiektu, stworzona po to, by optymalizować wykorzystanie zasobów lub podejmowanie dotyczących go decyzji biznesowych, w takich obszarach jak utrzymanie ruchu, rozbudowa, naprawy serwisowe czy sterowanie realnymi obiektami.
Aby cyfrowy bliźniak mógł spełniać swoją funkcję, konieczne jest połączenie czterech kluczowych komponentów: wirtualnego modelu obiektu, danych, połączenia z rzeczywistym obiektem oraz możliwości monitorowania zachowania tego ostatniego.
Pierwszy element, czyli stworzenie modelu 3D, wymaga wykonania skanu laserowego obiektu, zbudowania modelu w oparciu o dokumentację albo wykorzystania, bądź przystosowania, gotowego modelu 3D, dostarczonego przez producenta maszyny czy linii.
Drugi element to dane, czyli inaczej model matematyczny, pozwalający na odwzorowanie zachowania danego obiektu. Stworzenie takiego modelu wymaga informacji dotyczących parametrów pracy, właściwości fizycznych, charakterystyki zachowania. Jeśli wprowadzimy poprawne dane, oprogramowanie będzie na ich podstawie mogło wyliczyć czas cyklu pracy urządzenia lub procesu, tworząc ich dynamiczny obraz.
Trzeci element to łączność i przepływ informacji pomiędzy obiektem wirtualnym a rzeczywistym. Przykładowo, jeśli mamy turbinę wiatrową, czujniki, które się na niej znajdują, przesyłają do cyfrowego bliźniaka informacje o prędkości wirnika, zmianach kierunku wiatru i zmianach zachowania systemu w różnych warunkach pogodowych. Bliźniak aktualizuje te dane i pozwala przeprowadzać rozmaite testy, dając dzięki temu możliwość sprawdzenia pewnych rozwiązań, zanim zostaną one zaimplementowane w rzeczywistym obiekcie. W ten sposób można zminimalizować konsekwencje ewentualnych błędów. Dostęp do danych z rzeczywistego obiektu pozwala też na korygowanie modelu matematycznego.
Czwarty element, mocno powiązany z poprzednim, to możliwość monitorowania pracy realnego obiektu, wychwytywania nieprawidłowości i szybkiego interweniowania, gdy jest to konieczne. Tu często cyfrowy bliźniak sprzęgany jest z systemami control room, które dają możliwość plastycznego zwizualizowania monitorowanych procesów.
Integracja tych czterech elementów sprawia, że cyfrowy bliźniak staje się narzędziem pozwalającym w niespotykany dotąd sposób optymalizować pracę rozmaitych urządzeń. Przykładowo w procesie produkcji pomaga redukować koszty i w efektywny sposób zarządzać poszczególnymi maszynami, zakładami produkcyjnymi czy całym przedsiębiorstwem.
Skąd pomysł na digital twin?
Idea cyfrowego bliźniaka, niezwykle gorąca, nie jest jednak nowa. Już od pewnego czasu jest obecna w takich dziedzinach jak np. aeronautyka czy astronautyka. Używane od lat symulatory lotu, na których piloci odbywają szkolenia, to w gruncie rzeczy cyfrowe bliźniaki rzeczywistych maszyn, mające tę zaletę, że w sytuacji, gdy ryzykowne powietrzne akrobacje kończą się kraksą, nie ma ofiar w ludziach, a sprzęt nie zostaje zniszczony. Podobne symulatory wykorzystuje też amerykańska agencja kosmiczna NASA przy planowaniu różnego rodzaju misji kosmicznych, testowaniu rakiet, promów, łazików i innych urządzeń, które mają sprawdzić się w trudnych warunkach.
Koncepcja cyfrowego bliźniaka w kontekście produkcyjnym również nie należy do najnowszych. W 2002 roku pojęcie to stworzył Michael Grieves, pracujący wówczas jako profesor na University of Michigan, i ogłosił podczas jednej z branżowych konferencji. Grieves zaproponował, by cyfrowy bliźniak był logicznym uzupełnieniem rozwiązań PLM (Product Lifecycle Management), a więc systemów pozwalających zarządzać cyklem życia produktu. Ponieważ funkcja cyfrowego bliźniaka dotyczy dwóch zasadniczych etapów tego cyklu – etapu projektu i etapu wdrożenia – mamy dwa zasadnicze typy cyfrowych bliźniaków:
- Typ pierwszy pełni funkcję prototypu, a więc jest tworzony zanim powstanie jakieś rozwiązanie, produkt, fabryka czy łańcuch logistyczny. Taki cyfrowy bliźniak zostaje opracowany, by testować rozmaite warianty jakiegoś obiektu czy procesu przed wdrożeniem, co pozwala oszczędzać zasoby i redukować koszty związane z testami.
- Typ drugi to bliźniak istniejącego już rozwiązania, pozwalający lepiej zarządzać prawdziwą fabryką, produktem czy łańcuchem dostaw. Tu dochodzi możliwość silnego zintegrowania cyfrowego bliźniaka z rzeczywistym rozwiązaniem i lepsze zarządzanie istniejącym już systemem.
Przez długie lata idea cyfrowego bliźniaka była jedynie konceptem, trudnym do zrealizowania ze względu na przeszkody techniczne. Dzisiaj, dzięki rozwojowi rozmaitych technik komunikacyjnych, przemysłowemu internetowi rzeczy pozwalającemu zbierać dane w niespotykanej dotąd skali i z nieznaną dotąd precyzją, ale także ze względu na rosnące zapotrzebowanie klientów na spersonalizowane produkty, dopasowane do ich potrzeb, cyfrowe bliźniaki w obu odsłonach stają się coraz bardziej popularne i potrzebne.
Jakie korzyści daje zastosowanie cyfrowego bliźniaka?
Cyfrowy bliźniak w kontekście produkcyjnym jest integralnym elementem czwartej rewolucji przemysłowej. Jest przejawem trendu polegającego na wirtualizacji i symulacji procesów i obiektów, który jest jednym z sześciu filarów Przemysłu 4.0. Pozostałe to modułowość, interoperacyjność, decentralizacja, zdolności zarządcze w czasie rzeczywistym i orientacja na usługi. Dlatego na rosnące znaczenie cyfrowego bliźniaka od niedawna wskazują największe na świecie firmy konsultingowe, badawcze czy technologiczne, takie jak Gartner czy Accenture.
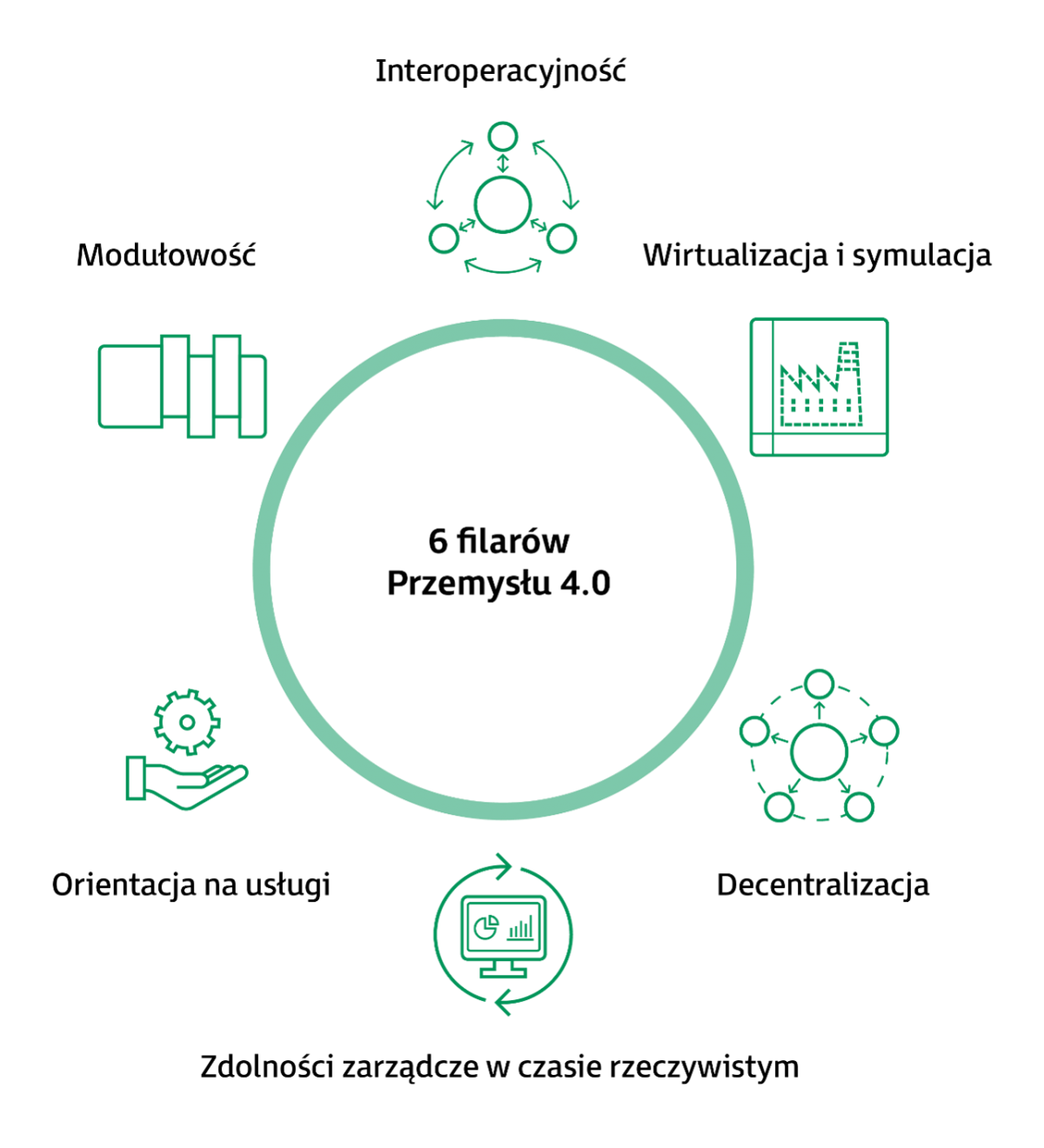
McKinsey & Company przewiduje, że do 2025 roku rynek cyfrowych bliźniaków osiągnie wartość 7 miliardów euro, z roczną stopą wzrostu na poziomie 30-45%.
Co to jednak oznacza w praktyce dla przedsiębiorców, którzy zdecydują się na implementację cyfrowych bliźniaków w swoich fabrykach? Z prognoz również przygotowanych przez McKinsey & Company wynika, że cyfrowe bliźniaki mogą przyczynić się do wzrostu przychodów firm produkcyjnych na poziomie nawet 10%, przyspieszą czas potrzebny na wprowadzenie produktu na rynek o około 50% i przyczynią się do poprawy jakości o około 25%.
Pierwsze organizacje, które postawiły na technologię cyfrowego bliźniaka, już odnoszą wymierne korzyści. Firma Evonik o 10-5% zredukowała nakłady na prace projektowe. Firma BP w Angoli zaoszczędziła 135 mln dolarów na pracach inżynieryjnych, a także 32 miliony dolarów dzięki usprawnieniu przepływu informacji i poprawie jakości danych. Chevron dzięki cyfrowym bliźniakom jest w stanie wyszukiwać dane dotyczące produkcji, utrzymania ruchu, wiarygodności i bezpieczeństwa w mniej niż 3 minuty. Firma PDO z Omanu dzięki cyfrowym bliźniakom zredukowała o 5% czas pracowników przeznaczany na poszukiwanie informacji, co jest równowartością 10 tys. dni roboczych, a tym samym ekwiwalentem zatrudnienia 50 dodatkowych, wykwalifikowanych pracowników. Unilever wspólnie z Accenture stworzył cyfrowego bliźniaka jednej z fabryk. Testy prowadzone z jego wykorzystaniem, polegające na zmianie pewnych parametrów procesu produkcji, pozwoliły dostroić fabrykę w taki sposób, by pobór energii był minimalny, a produktywność maksymalna. Modelowanie zużycia surowców naturalnych oraz półproduktów przy różnych scenariuszach pracy fabryki, to jedne z ważniejszych korzyści związane z implementacją rozwiązań typu digital twin.
W kontekście produkcyjnym, korzyści mogą polegać także na skróceniu czasu potrzebnego na nauczenie robota sekwencji ruchów, koniecznych do wykonywania konkretnych czynności np. spawania. Jeśli trening odbywa się w świecie wirtualnym, czas uczenia robota można skrócić o 80-90%.
Doskonale sprawdza się również wykorzystanie cyfrowego bliźniaka w połączeniu z technologią rozszerzonej rzeczywistości, nakładającej wirtualne obrazy na realne obiekty, czyli de facto łączące obrazy obu bliźniaków – cyfrowego i realnego. Na przykład zakładając okulary poszerzonej rzeczywistości i spoglądając na prasę w hali fabrycznej, uzyskamy dodatkowe informacje dotyczące choćby przezbrojenia maszyny, zamontowania nowego narzędzia czy też tego, gdzie i pod jakim kątem podać surowiec.
Poszerzona rzeczywistość sprzężona z cyfrowym bliźniakiem sprawdza się także jeśli chodzi o prace utrzymaniowe. Zazwyczaj dokumentacja techniczna dotycząca np. linii produkcyjnych, to kilkusetstronicowy dokument. Jeśli jednak istnieje cyfrowy bliźniak takiej linii, to w sytuacji awaryjnej albo gdy trzeba sprawdzić instalację, odpowiedzialny za jej utrzymanie inżynier zakłada okulary poszerzonej rzeczywistości i patrząc na konkretne maszyny widzi miejsca, gdzie potencjalnie mogło dojść do usterek, albo takie elementy, które wymagają konserwacji.
Wykorzystanie sztucznej inteligencji sprawia, że utrzymanie staje się jeszcze łatwiejsze, bo w ramach analiz prowadzonych na cyfrowym bliźniaku można przewidywać, kiedy konkretne układy mogą ulec awarii i z wyprzedzeniem wymieniać kluczowe elementy. Tego rodzaju predictive maintenance (czyli predykcyjne utrzymanie ruchu) jest coraz łatwiejsze dzięki masowemu wykorzystywaniu rozwiązań z obszaru przemysłowego internetu rzeczy. Oczujnikowanie przestrzeni produkcyjnej sprawia, że ilość danych do analiz rośnie. Dotyczy to nawet sprzętu w małym stopniu scyfryzowanego. Na przykład, jeśli na obudowie maszyny montujemy czujniki rejestrujące poziom wibracji i zmiany temperatury, to porównując dane bieżące z historycznymi, możemy wykrywać wszelkie anomalie, mogące sygnalizować nadchodzącą awarię.
Przewidywać można zresztą nie tylko awarie o charakterze technicznym, ale też problemy procesowe. Pomaga w tym integracja z cyfrowym bliźniakiem różnych systemów danych, np. systemu efektywności energetycznej, MES, APS, ale także BMS (system zarządzania budynkami), czy FMS (Facility Management System), a nawet sprzedaży czy e-commerce. Dzięki tym ostatnim możemy mieć np. bieżące informacje na temat ilości zgłoszeń gwarancyjnych i zwrotów produktów, które to parametry można zmniejszyć, modyfikując linię produkcyjną.
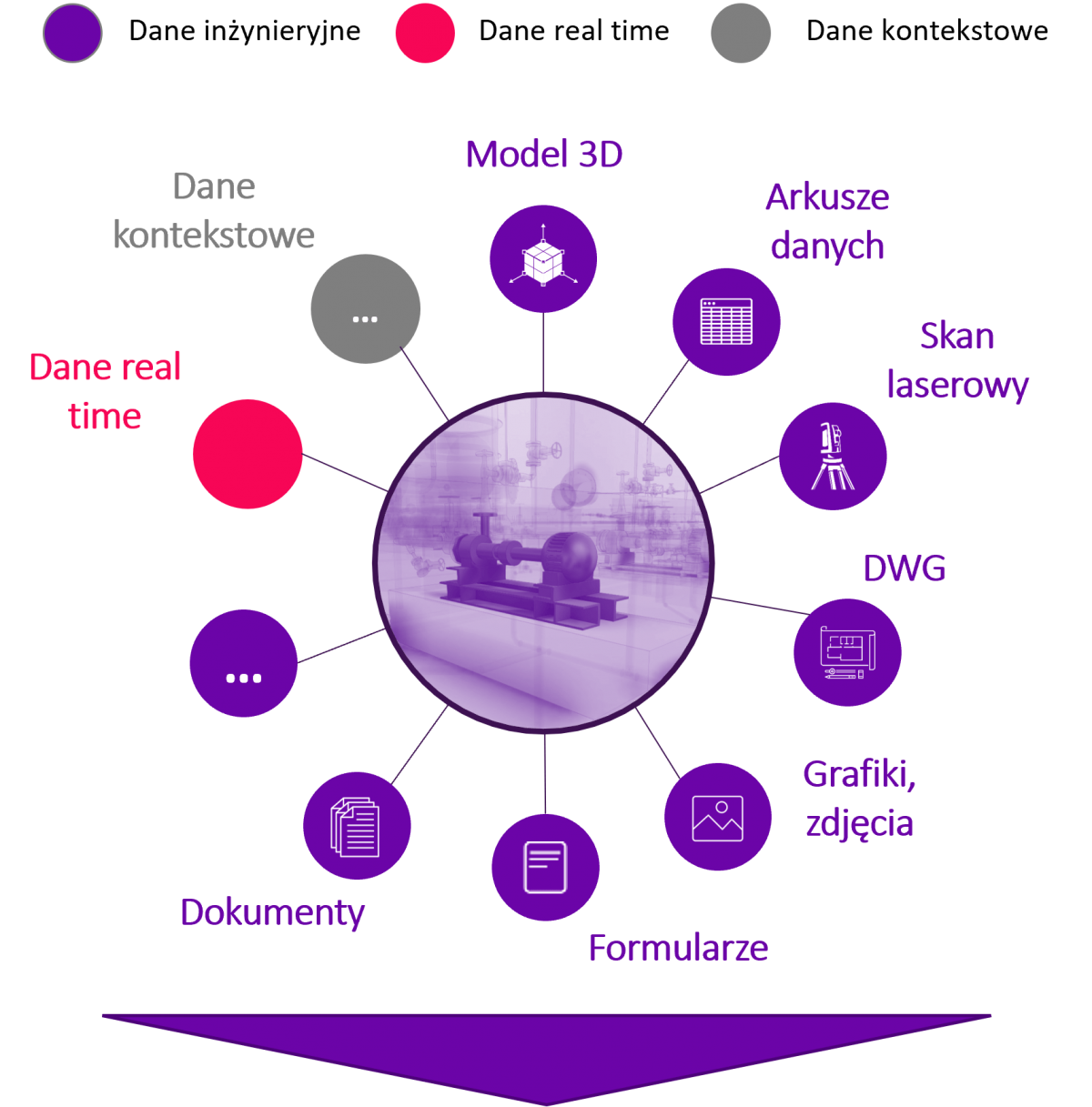
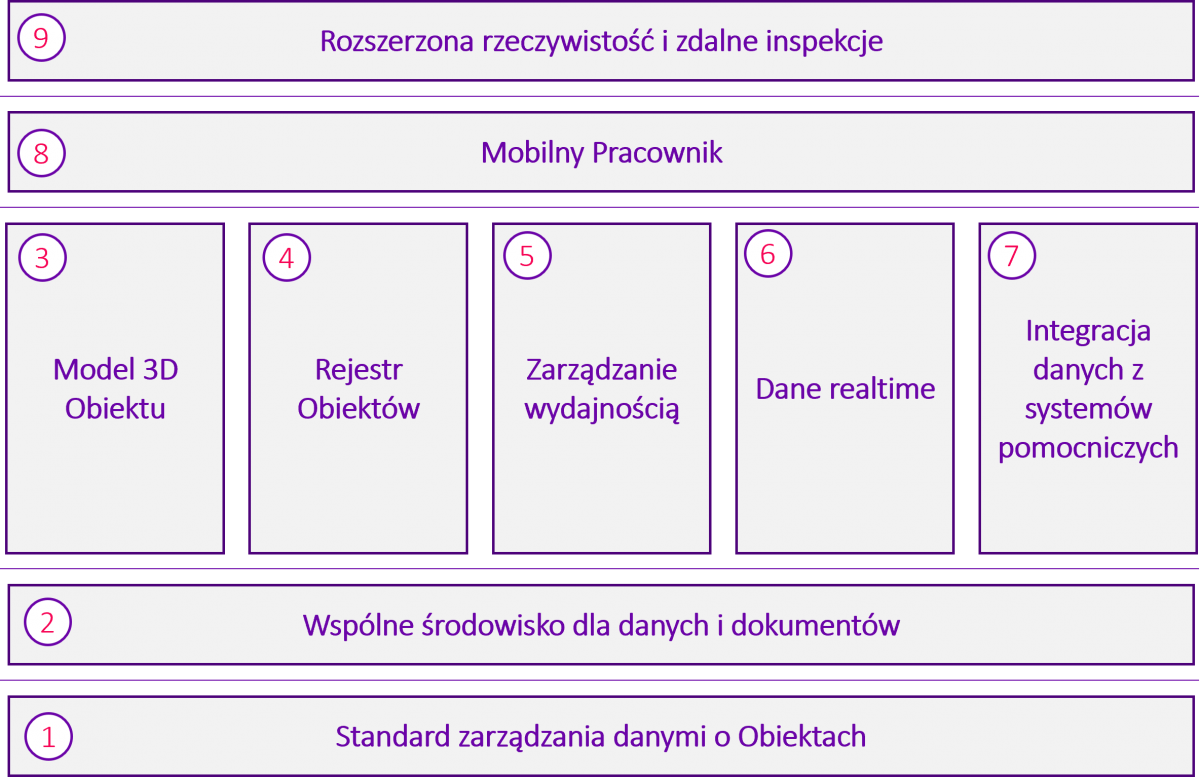
Jeśli chodzi wykorzystanie cyfrowych bliźniaków do projektowania, tu również widać wiele szans. Siły powietrzne Stanów Zjednoczonych US Air Force wykorzystując cyfrowe bliźniaki do tworzenia prototypów i testowania nowych samolotów, skróciły czas pracy nad nimi do nieco ponad roku. Wcześniej na ich opracowanie i przetestowanie potrzeba było dekad.
Jeden z producentów części motoryzacyjnych wykorzystał technologię cyfrowego bliźniaka do stworzenia konfiguratora pozwalającego projektować części z uwzględnieniem potrzeb różnych grup interesariuszy: klientów, działu finansowego, inżynierów czy działu sprzedaży. Konfigurator pozwala modyfikować rozmaite parametry produktu i sprawdzać, w jaki sposób każda z takich modyfikacji wpływa na dopasowanie produktu do potrzeb klientów, jego ostateczną cenę, a także techniczną trudność wykonania. Pomaga też wyznaczyć najbardziej kompromisową opcję, która umożliwia stworzenie produktu zadowalającej jakości, relatywnie niedrogiego i łatwego w produkcji. Wykorzystanie konfiguratora pozwoliło o 20% skrócić czas potrzebny na osiągnięcie zgody różnych interesariuszy co do koniecznych zmian projektowych. Umożliwiło też alokację 5-15% środków na produkcję części i przeznaczenie ich na wyposażenie produktu w te cechy, na których najbardziej zależy klientom.
Także twórcy autonomicznych pojazdów coraz częściej testują je w świecie wirtualnym, co pozwala uniknąć sytuacji zagrożenia dla uczestników ruchu.
Jak zaplanować wdrożenie cyfrowego bliźniaka – roadmapa
Wdrożenie technologii cyfrowego bliźniaka może być źródłem wielu korzyści, ale po pierwsze wymaga dokładnego rozpoznania potrzeb biznesowych wewnątrz organizacji, a po drugie rozłożenia w czasie samej implementacji. W tym procesie kluczowe są cztery etapy:
- Integracja danych inżynieryjnych dotyczących obiektu, obecnych w istniejących systemach (np. CMMS, dokumentacja cyfrowa).
- Optymalizacja wykorzystania obiektu przy użyciu systemów zarządzania danymi real-time (np. SCADA), systemów monitoringu (np. energii, mediów, wydajności) czy predictive maintenace.
- Stworzenie modelu i wizualizacja obiektu z wykorzystaniem systemów do modelowania 3D, symulacji procesów, skaningu laserowego czy rozszerzonej lub wirtualnej rzeczywistości.
- Interoperacyjność polegająca na współdzieleniu informacji poprzez systemy (np. Control Room, MES, APS, CMMS/EAM), procesy (projektowanie oparte na danych, optymalizacja produkcji) oraz technologie (AI, AR/VR).
Czas przeznaczony na każdy z etapów zależy od skali wdrożenia. Można jednak założyć, że implementacja cyfrowego bliźniaka dla poszczególnych maszyn to kwestia miesięcy, dla linii produkcyjnej – roku, a dla całego biznesu – kilku lat. Zawsze jednak należy zacząć od pewnej pracy kulturowej. Trzeba zrozumieć, że wiedza rozproszona w firmie powinna być nie tylko w głowach pracowników czy w różnych systemach informatycznych, ale powinna być scalona i zintegrowana w sposób przejrzysty i spójny. Temu właśnie służy cyfrowy bliźniak.
Dowiedz się więcej
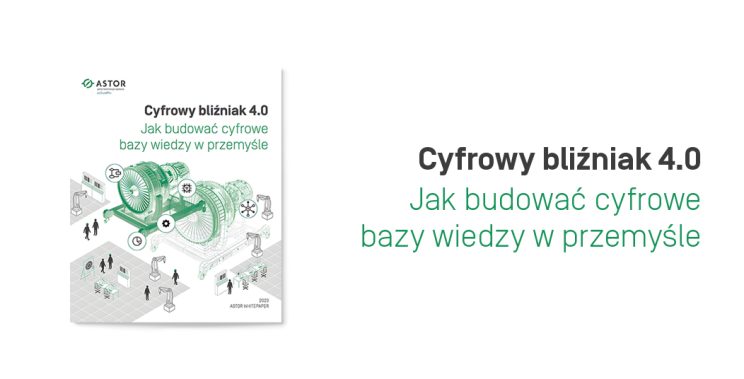
Dowiedz się więcej o cyfrowym bliźniaku w nowej publikacji „Cyfrowy bliźniak 4.0. Jak budować cyfrowe bazy wiedzy w przemyśle„