Treści
Co firmom produkcyjnym dają nowoczesne rozwiązania intralogistyczne
Co firmom produkcyjnym dają nowoczesne rozwiązania intralogistyczne
W czasach zaburzeń rynkowych intralogistyka jest spoiwem firm produkcyjnych gwarantującym przewidywalność procesów i stabilność biznesu.
Znaczenie transportu wewnątrzzakładowego we współczesnych przedsiębiorstwach jest kluczowe i stale rośnie. Choć z pozoru dotyczy on działań podejmowanych gdzieś na peryferiach procesu produkcyjnego, w istocie łączy wszystkie najważniejsze jego etapy, a przez to jest jego integralną częścią. Jeśli więc lider zmiany – menedżer średniego szczebla, który chce inicjować innowacyjne projekty technologiczne – widzi potencjał transformacyjny w obszarze intralogistyki, musi wiedzieć, że działania podjęte w tym obszarze przełożą się na długofalowe korzyści dla całego przedsiębiorstwa.
To siódmy tekst z cyklu ”Lider zmiany w przemyśle przyszłości” – przeznaczonego dla menedżerów średniego szczebla, którzy czują, że zmiana w wymiarze technologicznym, w ich przedsiębiorstwach jest konieczna, a nie wiedzą jak się do niej zabrać.
Pierwszy odcinek cyklu: Jak zostać liderem zmiany technologicznej?
Drugi: Co w twoim zakładzie produkcyjnym wymaga zmiany?
Trzeci: Sztafeta innowacji – osobowość i kompetencje liderów zmiany
Czwarty: Dlaczego twoja firma potrzebuje robotyzacji – lider zmiany w przemyśle przyszłości
Piąty: Na jakie potrzeby w firmach produkcyjnych odpowiada automatyzacja
Szósty: Co zyskują firmy dzięki oprogramowaniu przemysłowemu
Dołącz do naszego newslettera, by otrzymać kolejne teksty, gdy tylko się pojawią.
Czym więc jest intralogistyka i dlaczego jest tak ważna? To sztuka optymalizacji, integracji, automatyzacji, zarządzania przepływem materiałów wewnątrz przedsiębiorstwa. Usprawnienia w tym obszarze stają się coraz bardziej istotne w miarę wzrostu kosztów przedsiębiorstw, związanych nie tylko z utrzymaniem kadry pracowniczej, ale też podwyżkami cen mediów oraz gigantyczną konkurencyjnością na rynku także ze strony podmiotów z krajów azjatyckich. Ze względu na te wszystkie czynniki, a dodatkowo brak rąk do pracy fizycznej, automatyzacja w obszarze intralogistyki staje się koniecznością. Dobitnie pokazały to wydarzenia z ostatnich lat: począwszy od pandemii koronawirusa, przez kryzys na rynku półprzewodników, który sparaliżował część przemysłu, aż po napiętą sytuację polityczną, wojny w różnych częściach świata mające bezpośredni wpływ na nasze przedsiębiorstwa.
W tym kontekście we współczesnych zakładach produkcyjnych na pierwszy plan wysuwa się potrzeba stabilizacji biznesu rozhuśtanego przez globalne zaburzenia, zbudowania odporności na tektoniki wewnętrzne i zewnętrze. Intralogistyka zapewnia takie właśnie bezpieczeństwo. Jest spoiwem, które łączy różne obszary funkcjonowania przedsiębiorstwa i zapewnia jego stabilność przez prosty fakt, że zajmuje się dostarczaniem konkretnych towarów czy produktów w odpowiedniej ilości, we właściwe miejsce, w ściśle określonym czasie, bez uszczerbku na jakości.
Intralogistyka jest więc swoistym stabilizatorem, ponieważ łączy różne obszary wytwarzania, często nadaje rytm produkcji i bezpośrednio wpływa na jej efektywność. Umożliwia też zwiększanie wolumenu wytwarzanych towarów, ale bez obciążania pracowników dodatkowymi zadaniami czy też pracą fizyczną. Ułatwia też eliminowanie strat.
Dlaczego intralogistyka jest coraz ważniejsza?
Transport wewnątrzzakładowy zawsze był obecny w fabrykach. W ubiegłym stuleciu proces produkcji miał jednak charakter progresywny: od stacji do stacji. Oznacza to, że linie produkcyjne składały się z szeregu stanowisk ściśle od siebie zależnych, obsługiwanych zarówno przez ludzi, jak i maszyny. Proces produkcji polegał często na ręcznym transporcie detalu, co prowadziło do wielu niepotrzebnych przestojów i niskiej efektywności pracy.
Obecnie produkcja ma nieco inny przebieg. Aby zminimalizować straty, poszczególne stanowiska można szybko, często automatycznie przezbrajać do obsługi różnych produktów, a transport pomiędzy nimi odbywa się za pomocą konwencjonalnych metod przenośnikowych lub rozwiązań autonomicznych. Takie podejście sprawia, że mamy do czynienia ze swoistym renesansem transportu wewnątrzzakładowego, podsycanym dodatkowo przez dynamiczny rozwój wszelkich rozwiązań technologicznych, a zwłaszcza robotyki mobilnej.
W halach fabrycznych i magazynach dopiero przyzwyczailiśmy się do widoku automatycznych wózków bezzałogowych (AGV), a już w wielu obszarach ta technologia jest wypierana przez zupełnie nową klasę rozwiązań, czyli autonomiczne roboty mobilne (AMR). Korzystają one z rozwiązań sztucznej inteligencji i samodzielnie podejmują pewne decyzje w zakresie wskazanym przez człowieka.
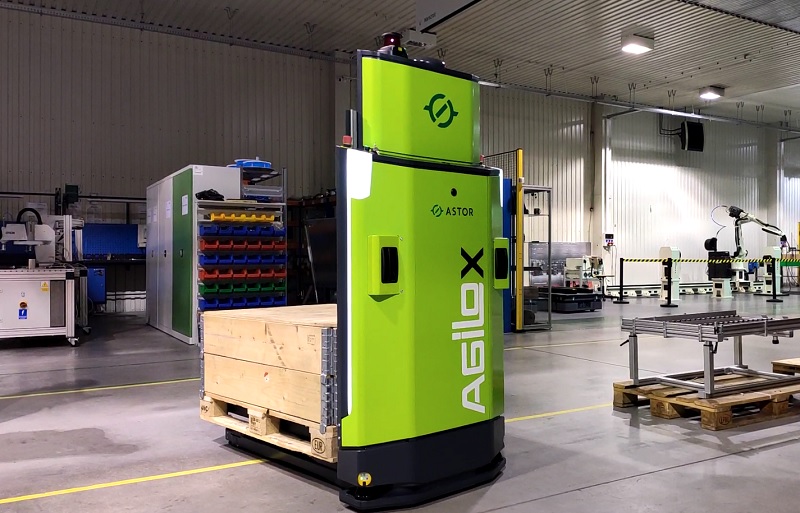
Te decyzje mogą dotyczyć na przykład wyboru ścieżki transportowej pojedynczego robota, prioretyzacji zadań czy działania całej floty robotów. W tym ostatnim przypadku autonomiczne systemy rozdzielają konkretne zadania pomiędzy poszczególne jednostki, biorąc pod uwagę obecne ich położenie, liczbę zadań, stan naładowania baterii i inne czynniki w czasie rzeczywistym.
Człowiek wciąż ma ogromne znaczenie w intralogistyce, bo to on wyznacza ramy, w jakich działają systemy autonomiczne. Systemy te jednak coraz bardziej go odciążają – czy to jeśli chodzi o autonomiczne roboty, systemy hybrydowe, w których roboty współpracują z klasycznymi systemami rolkowymi, czy to, jeśli chodzi o odciążenie w sensie fizycznym lub w podejmowaniu prostych decyzji.
Historia sukcesu
Firma Flokk produkuje meble biurowe i sprzedaje je w 80 krajach, na 4 kontynentach. Firma zarządza 9 markami, z których najstarsza (Giroflex) liczy ponad 150 lat. W portfolio firmy jest też polska marka Profim. Zarząd polskiego oddziału Flokk, gdzie produkowane są meble tej marki, postanowił zainwestować w nowoczesny system do kompletacji i transportu wewnątrzzakładowego.
System obsługuje lub ułatwia 3 podstawowe etapy procesu. Są to: kompletacja zestawów złożonych z komponentów krzesła, montaż krzeseł z elementów zestawów, pakowanie gotowych produktów.
Inwestycja w nowoczesną linię kompletacji i montażu krzeseł korzystnie wpłynęła na pozycję rynkową firmy, ponieważ zwiększyła możliwość szybkiego reagowania na potrzeby rynku i osiąganie wysokich wydajności. System międzyoperacyjny poprawiający logistykę produkcji przyspieszył montaż, sprawił, że operatorzy, którzy zajmują się nim, nie muszą myśleć o transporcie złożonych mebli czy komponentów do następnego stanowiska.
W jakich branżach intralogistyka ma największe znaczenie?
Transport wewnątrzzakładowy jest takim obszarem, który istnieje w zakładach produkcyjnych niezależnie od sektora. W każdym przedsiębiorstwie wyzwaniem jest bowiem minimalizowanie kosztów operacji non value added, a więc takich, które same z siebie nie generują wartości, ale są procesowo niezbędne i gdy źle się je zaprojektuje, mogą być źródłem dodatkowych kosztów.
Zapotrzebowanie na rozwiązania intralogistyczne jest więc uniwersalne, ale różne branże mają także pewną specyfikę. I tak na przykład w sektorze FMCG – produkcja dóbr szybkozbywalnych – konieczna jest bardzo duża szybkość działania, często są to procesy związane też z wytwarzaniem pojedynczych produktów czy krótkich serii, pakowaniem do kartonów zbiorczych, paletyzowaniem i transportem do magazynów wysokiego składowania.
Inne wyzwania pojawiają się w tych branżach, gdzie rozwiązania intralogistyczne mogą znacząco usprawnić funkcjonowanie końcówek linii produkcyjnych, jak na przykład w meblarstwie, albo kompletację zleceń i paletyzację, czyli optymalizując fazę po produkcji, ale jeszcze przed magazynem, jak chociażby w farmacji. Myśląc o innowacjach mających usprawnić działanie zakładu, lider zmiany musi wziąć pod uwagę jego specyfikę.
Historia sukcesu
Firma Postęp istnieje ponad 70 lat. Jest producentem mebli w szerokim asortymencie dostarczanych do sklepów najbardziej znanych marek, zarówno na rynek polski, jak i za granicę. Meble produkowane są z drewna, płyt wiórowych oraz MDF. Często materiały te łączone są ze sobą.
W fabryce firmy Postęp od dłuższego czasu ważną rolę odgrywa automatyzacja logistyki produkcji. Działają nowoczesne systemy do obróbki i malowania drewna oraz materiałów drewnopochodnych, do paletyzacji, transportu, owijania i etykietowania kartonów z meblami. Zarząd wciąż jednak widzi przestrzeń do usprawnień i dalszej automatyzacji przy poprawie ergonomii, bezpieczeństwa i warunków pracy.
Dlatego firma zdecydowała się na uruchomienie nowoczesnego, zautomatyzowanego systemu paletyzacji i transportu wewnątrzzakładowego z trzema gniazdami robotów Kawasaki CP180L. W wyniku implementacji znacząco skrócił się czas potrzebny na paletowanie produktów, udało się odciążyć pracowników i zwiększyć komfort ich pracy.
Inżynierowie i menedżerowie zyskali wgląd w proces paletowania. Wzrósł poziom bezpieczeństwa przeciwpożarowego. Linia transportująca palety do owijarki przechodzi przez bramę przeciwpożarową, która odcina halę produkcyjną od hali magazynowej. Gdy wybucha pożar, brama zamyka się, nie uszkadzając systemu wewnątrzzakładowego transportu.
Lider zmiany, czyli kto?
W przedsiębiorstwach produkcyjnych obserwujemy coraz większą odwagę, jeżeli chodzi wykorzystywanie nowoczesnych rozwiązań intralogistycznych. Widzimy też, że impuls do podjęcia działań modernizacyjnych czasem daje jeden z pracowników oddolnie, nawet jeśli nie miał wcześniej do czynienia z robotyką. Osoba taka sygnalizuje potrzebę zmiany i często zachęca zarząd do podjęcia inwestycji. Następnie przeobraża się w opiekuna tej zmiany i staje się jej wewnętrznym promotorem i ambasadorem. Istnienie takich osób ma kolosalne znaczenie, bo zmianę trzeba dobrze komunikować i oswoić – zwłaszcza kiedy do przedsiębiorstwa dostarczana jest nowa technologia po raz pierwszy, na przykład w postaci robota mobilnego.
Lider zmiany często odpowiada też za organizowanie akcji informacyjnych, a więc szuka sposobu na dobre przeprowadzenie zmiany w kontekście emocji pracowników produkcyjnych, na przykład przez rozwieszanie plakatów ze specjalnie zaprojektowanymi grafikami czy nawet organizowanie konkursu na imię dla nowego zrobotyzowanego członka załogi.
Co ciekawe, lider zmiany technologicznej często wyłania się w momencie, kiedy powstaje wizja czy koncepcja zmiany, zdarza się, że początkowo jest to osoba nieprzekonana, określana niekiedy kolokwialnie mianem „hamulcowego”. W miarę jak toczą się rozmowy dotyczące nie tylko części technicznej inwestycji, ale też jej wymiaru biznesowego, taka osoba przekonuje się coraz bardziej do nowych rozwiązań i staje się wręcz ich ambasadorem w rozmowach z przełożonymi i kolegami, staje się motorem napędowym do kolejnych zmian w przedsiębiorstwie.
Wejście na tę ścieżkę jest dla tej osoby często okazją do osobistego rozwoju. W trakcie wprowadzania nowych rozwiązań lider nabywa bowiem nowych kompetencji technicznych, dzięki samej implementacji, ale też towarzyszącym jej szkoleniom. Jest też postrzegany jako osoba mogąca samodzielnie przeprowadzać kolejne zmiany. Samemu może zmieniać layout hali produkcyjnej, samemu może reorganizować poszczególne stacje, dodawać, edytować i optymalizować misje dla robotów mobilnych czy też określać potrzebną wielkość floty.
Lider zmiany, nawet przy początkowych oporach, przez kontakt z technologią zaczyna się uczyć i czy to przez jej praktyczne wykorzystanie, czy przez szkolenia wchodzi na wyższy poziom kompetencyjny. Zaangażowanie się w transformację staje się dla niego impulsem do rozwoju pozwalającym na awans w strukturach firmy, także w wymiarze finansowym.
Jak poznać potrzeby, na które mogą odpowiedzieć rozwiązania intralogistyczne?
Współczesna intralogistyka to nie tylko roboty mobilne czy podajniki rolkowe, ale także systemy informatyczne, które te rozwiązania obsługują. Nie tylko monitorują ich pracę, ale też zbierają dane na temat ich funkcjonowania. Lider zmiany technologicznej może posłużyć się takim oprogramowaniem i tymi danymi, by znaleźć wąskie gardła i przyczyny przestojów, a dzięki temu odkryć potencjał transformacyjny.
Jeśli takich systemów monitorujących produkcję w firmie jeszcze nie ma, lider zmiany może posłużyć się rozwiązaniami do symulacji procesów. To bardzo ważny etap inwestycji obniżający ryzyko i pozwalający przewidywać wpływ zmian technologicznych na konkretne etapy procesu produkcyjnego, ale też holistycznie spojrzeć na całość i wykryć wąskie gardła, które ten proces spowalniają. Poza systemami i danymi bardzo ważna jest bieżąca komunikacja i wymiana doświadczeń wewnątrz przedsiębiorstwa zarówno z kadrą menedżerską, jak i pracownikami i liderami produkcji.
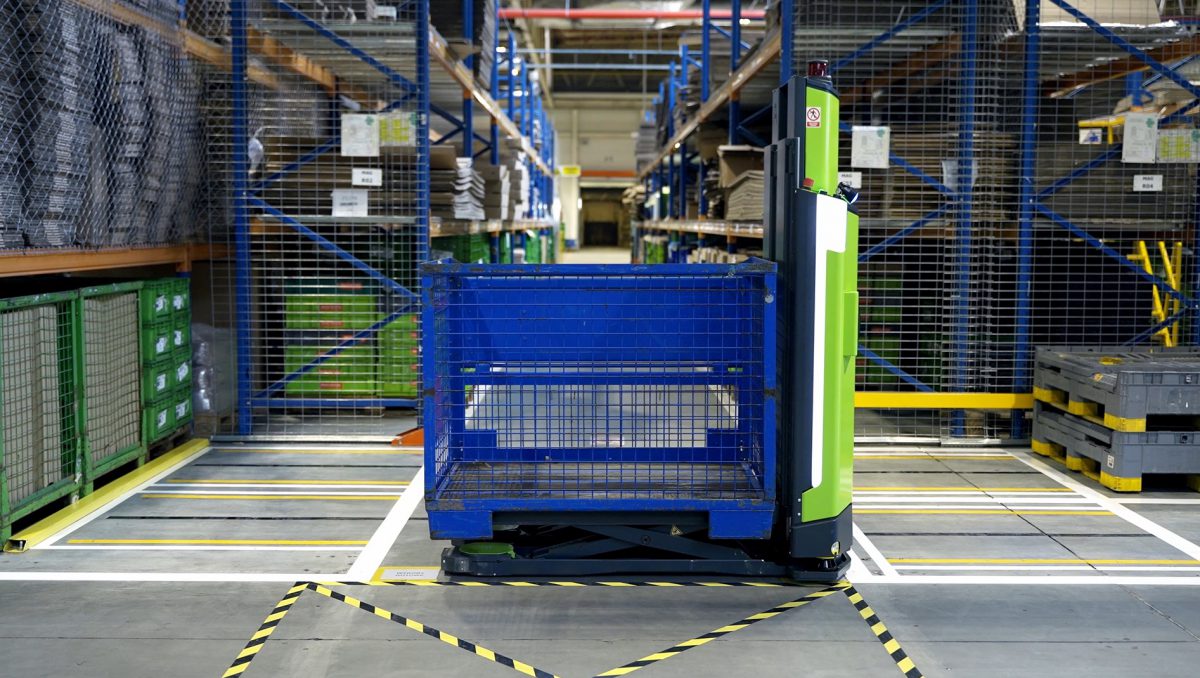
Choć często intralogistyka postrzegana jest jako proces transportu od półfabrykatu po magazyn gotowych produktów, czasem wystarczy jeden robot mobilny, by znacząco zwiększyć płynność operacyjną w pewnym obszarze i przynieść korzyści w wymiarze biznesowym. Zlokalizowanie choćby jednego miejsca, które wymaga usprawnienia, może więc przynieść skokową zmianę i sukces liderowi zmiany.
Aby takie miejsca znajdywać i rozpoznać rzeczywiste potrzeby przedsiębiorstwa w obszarze intralogistyki, lider zmiany powinien mieć bazowe kompetencje techniczne, ale może też nabywać je w procesie wdrażania nowych rozwiązań. Niezwykle ważne są w tym kontekście także zdolność nawiązywania kontaktów i dobre wyczucie wynikające z wiedzy o procesach w danej firmie i rozmów z pracownikami. Kontakty z zarządem są kluczowe do tego, żeby poznać założenia strategiczne przedsiębiorstwa. Kontakty z pracownikami w halach fabrycznych są niezbędne, by zrozumieć bazowe potrzeby i wyzwania w obszarze intralogistyki i przekonać zarząd do dalszej modernizacji, tak by transport wewnętrzny jeszcze skuteczniej mógł odgrywać rolę spoiwa i stabilizatora biznesu.