Treści
Co CEO powinni wiedzieć o cyfrowych bliźniakach? #1 Jak cyfrowy bliźniak usprawnia fabrykę przyszłości?
Co CEO powinni wiedzieć o cyfrowych bliźniakach? #1 Jak cyfrowy bliźniak usprawnia fabrykę przyszłości?
W przedsiębiorstwach z obszaru przemysłu 4.0 coraz rzadziej wykorzystuje się tradycyjne maszyny, które działają tylko w obrębie hali produkcyjnej. Na znaczeniu zyskują nowoczesne rozwiązania, które znacząco zwiększają możliwości firm, jednocześnie ułatwiając zarządzanie urządzeniami. Popularne staje się chociażby wdrażanie tak zwanych cyfrowych bliźniaków, których potencjał można dostrzec w niemal każdej fabryce przyszłości!
Czym jest cyfrowy bliźniak?
Pod pojęciem cyfrowego bliźniaka kryje się utworzony wirtualny odpowiednik fizycznego obiektu lub procesu. Jest to wirtualna replika maszyny, poszczególnych komponentów lub cyklu czynności, które są realizowane wewnątrz przedsiębiorstwa produkcyjnego. W pewnym sensie jest to odzwierciedlenie realnych procesów i obiektów w wirtualnej wersji, na przykład na ekranie smartfona lub komputera.
Pierwsze przejawy koncepcji cyfrowego bliźniaka można dostrzec już w roku 2002. Początkowo było to pojęcie związane z przedstawieniem na trójwymiarowym modelu maszyn lub produktów, które są wytwarzane lub których produkcja dopiero miała się zacząć. Wykorzystanie takich technologii w nowoczesnych fabrykach pozwoliło na dokładne poznanie konkretnych obiektów bez konieczności fizycznego kontaktu z nimi.
W tym momencie pojęcie cyfrowego bliźniaka tak naprawdę łączy w sobie trzy niezbędne elementy. Poza fizycznym obiektem i jego odpowiednikiem w wersji wirtualnej, niezwykle ważnym komponentem jest łączność między tymi dwoma wymiarami. Pozwala to na błyskawiczną wymianę danych pomiędzy realnym i cyfrowym urządzeniem, co daje możliwość monitorowania i kontrolowania pracy maszyn produkcyjnych.
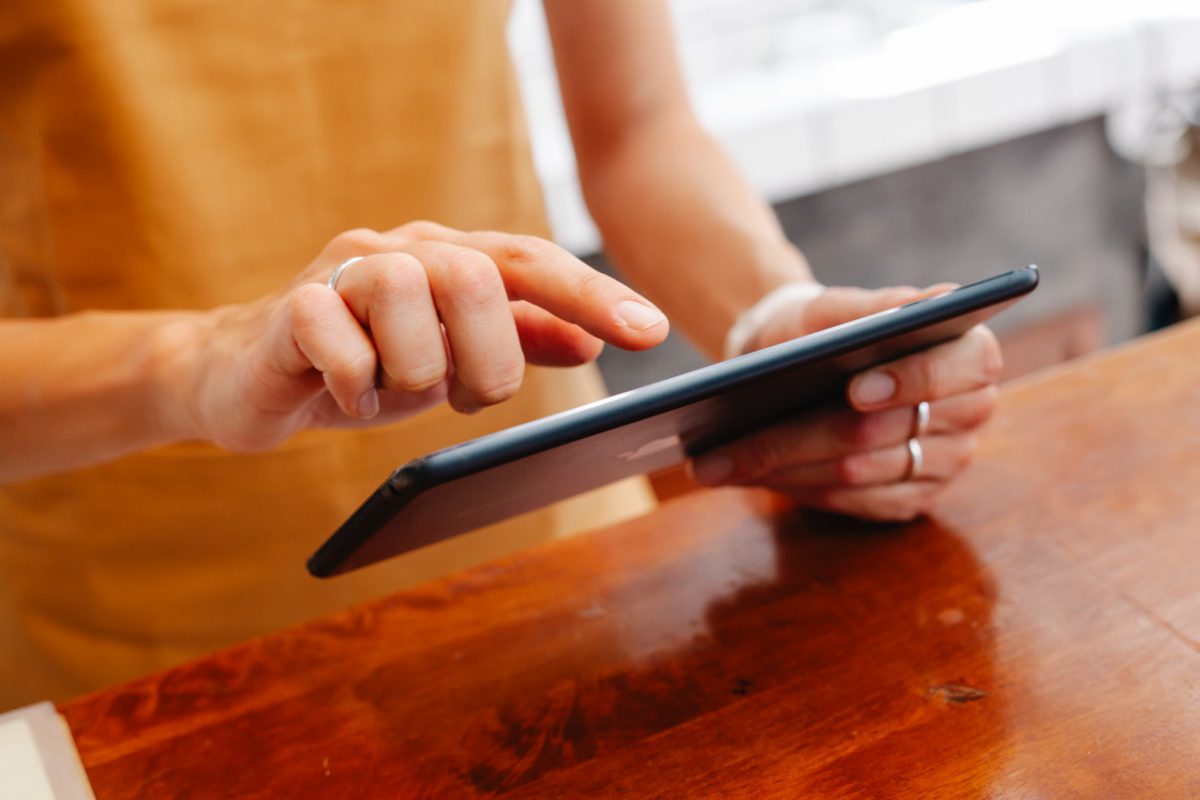
Cyfrowy bliźniak w monitorowaniu pracy urządzeń
Poprzez nawiązanie łączności między fizyczną maszyną (lub procesem wewnątrz przedsiębiorstwa produkcyjnego) a wirtualnym odpowiednikiem, możliwe jest zarządzanie pracą urządzeń w czasie rzeczywistym. Wykorzystując w tym celu dedykowane aplikacje, możemy monitorować bieżący stan produkcji. Co więcej – w wielu przypadkach, systemy są dostosowane do wchodzenia w interakcję z maszyną, co pozwala na zmianę parametrów działania czy reagowanie na ewentualne awarie i błędy w funkcjonowaniu.
Częstotliwość występowania takich sytuacji można jednak zminimalizować dzięki funkcjom pozwalającym przewidzieć przyszłe działanie urządzeń. Dzięki zbieranym danym cyfrowy bliźniak może przewidywać kolejne aktywności fizycznych maszyn z zakresu realizowania bieżących i przyszłych zadań, co pozwala przewidywać najbliższe działanie. Daje to szansę na szybką reakcję w obliczu problemów w funkcjonowaniu, nawet przed faktycznym wystąpieniem takiej sytuacji.
Cyfrowy bliźniak w służbie predictive maintenance
To działanie wpisujące się w koncepcję predictive maintenance, czyli szacowania problemów i niespodziewanych awarii. Stosowane systemy z dużym prawdopodobieństwem mogą przewidzieć, który z elementów maszyn stosowanych w firmach produkcyjnych może ulec awarii w najbliższej przyszłości. W przypadku pojawienia się takich przesłanek użytkownik otrzyma stosowną informację o konieczności podjęcia odpowiednich działań.
Tego typu rozwiązania stosowane są chociażby w kontrolerach IICS, na przykład w modelu CPE400. Poza szacowaniem możliwości pojawienia się problemów w działaniu pozwala on także na obsługę wszystkich maszyn, zbieranie niezbędnych danych oraz automatyzację niektórych procesów. Jest to możliwe dzięki stałemu połączeniu maszyn do sieci oraz stosowaniu czujników, które bez przerwy monitorują pracę urządzeń.
Planowanie przyszłych działań z cyfrowym bliźniakiem
Stosowanie cyfrowego bliźniaka w fabrykach przyszłości nie ogranicza się jednak jedynie do bieżącego działania i poznawania możliwości maszyn. Cyfrowe repliki urządzeń pozwalają także zweryfikować stopień dopasowania wdrażanych zmian i nowości w ramach działań produkcyjnych. W wirtualnym odpowiedniku urządzeń możemy sprawdzić potencjalny sposób działania nowych rozwiązań i weryfikować możliwości produkcyjne symulując maksymalne obciążenie.
Cyfrowy bliźniak pozwala na testowanie różnych scenariuszy działania w zakresie operacyjnym i dobór najbardziej efektywnego na realnym urządzeniu. Wpływa to na poziom dopasowania planowanych zmian do konkretnych maszyn. Ogranicza też koszty, eliminując ryzyko niepowodzenia oraz optymalizując sposób i czas wykonywania poszczególnych akcji. Całość opiera się na konkretnych danych zbieranych przez stosowane czujniki i dopasowane do nich systemy. Eliminowany jest więc czynnik błędu ludzkiego, możliwość podjęcia decyzji na podstawie emocji i błędnej interpretacji zdarzeń.
W dłuższej perspektywie testowanie nowych możliwości na cyfrowych bliźniakach pozwala na opracowanie długofalowych planów działania i stopniowego wdrażania usprawnień. Stosowane systemy pozwalają na określenie granic obszaru roboczego poprzez symulację pracy maszyn z biegiem czasu, wraz ze zwiększającym się obciążeniem i zmianą parametrów stosowanych procesów.
***
W drugiej części artykułu na temat cyfrowych bliźniaków opiszemy kolejne czynniki, które sprawiają, że potencjał tej technologii jest tak ogromny. Przyjrzymy się także raportowi firmy AVEVA, w którym zawartych jest mnóstwo wartościowych informacji, które przydadzą się każdemu CEO fabryki przyszłości.