Treści
Ciągłość Przemysłu 4.0 w postcovidowym świecie
Ciągłość Przemysłu 4.0 w postcovidowym świecie
Zapewnienie ciągłości biznesu zawsze było kwestią o kluczowej wadze, jednak dziś jest to niekwestionowany temat numer jeden. Jakie czynniki sprawiły, że w wielu przedsiębiorstwach produkcyjnych udało się ją utrzymać mimo pandemii?
O ile przed pandemią COVID-19 zmiany w środowisku biznesowym następowały bardzo szybko, to obecnie można mówić o wręcz ekstremalnym przyspieszeniu. To, co pozytywne w całej tej sytuacji, to niezwykły wzrost innowacyjności i postęp procesów cyfryzacji przedsiębiorstw w ostatnich miesiącach. Właśnie po to, by ową ciągłość biznesu utrzymać – czytamy w jednym z najnowszych wpisów na blogu firmy AVEVA.
Wiele firm produkcyjnych, wbrew wszelkim przeciwnościom, zdołało bardzo szybko dostosować się do nowych warunków. Co przede wszystkim zaważyło na ich sukcesie?
Po pierwsze: chmura
Całokształtu zmian, które nastąpiły w tak krótkim czasie, nie sposób wyobrazić sobie bez dostępu do chmury danych – dość powiedzieć, że bez tej technologii przejście na zdalną pracę nie byłoby w zasadzie możliwe. Pandemia i lockdown uwidoczniły, jak ogromną odgrywa rolę, bo w żadnym momencie wcześniej nie było tak wielkiej i natychmiastowej potrzeby dostępności zasobów IT w chmurze.
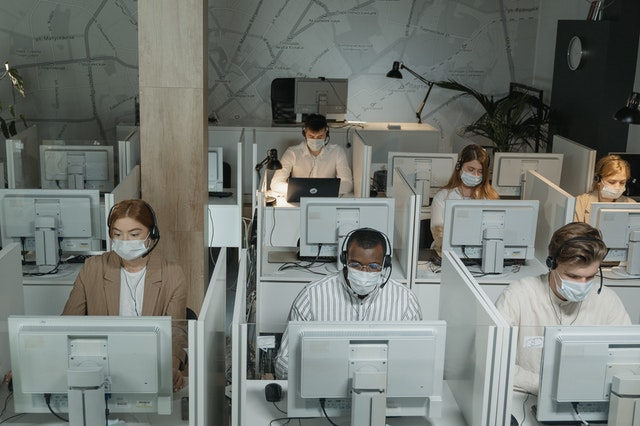
Chmura jest wszędzie: w naszych samochodach, telewizorach, telefonach. Chmura zapewnia łączność pomiędzy ludźmi i firmami produkcyjnymi w skali globalnej. Daje szansę na oszczędność kosztów i czasu, a także umożliwia wysoką skalowalność biznesu. Bez chmury wiele przedsiębiorstw nie byłoby w stanie wykonywać zadań, które robią każdego dnia – pandemia Covid-19 sprawiła jednakże, że lista tych zadań wydłużyła w nadspodziewany sposób.
Po drugie: zdalny dostęp do miejsca pracy
W nowoczesnym przedsiębiorstwie pracownicy nie muszą być na miejscu. Zdalny dostęp umożliwia pracę z dowolnego miejsca na świecie – oczywiście pod warunkiem, że jest tam Internet. Big data, sztuczna inteligencja, machine learning, wirtualna rzeczywistość – wszystkie te technologie pozwoliły pracownikom na zdalny dostęp do swojego miejsca pracy.
W przypadku przemysłu można powiedzieć wręcz o stworzeniu – za pomocą danych – cyfrowej repliki maszyn, a nawet całych fabryk. Zarządzanie, konserwacja i kontrola produkcji mogą odbywać się dzięki temu zdalnie. Modelowanie 3D i zaawansowane narzędzia wizualizacyjne sprawiają, że do wykonywania wielu zadań wystarczy dobrze zaprojektowany interface.

Po trzecie: zarządzanie wydajnością zasobów
Gdyby epidemia wybuchła kilka czy kilkanaście lat temu, byłoby znacznie gorzej. A to dlatego, że w tym czasie wiele przedsiębiorstw zaczęło wdrażać APM, czyli zaawansowane rozwiązania w zakresie zarządzania wydajnością majątku trwałego. Technologia ta umożliwiła wgląd w dane powiązane bezpośrednio z bezpieczeństwem aktywów i ich wydajnością. Pomogła w zarządzaniu ryzykiem, przewidywaniem awarii i ograniczaniu kosztownych przestojów produkcji.
Co więcej, procesy te można monitorować w czasie rzeczywistym i w sposób ciągły. Nie ma zatem wątpliwości, że gdyby nie technologie APM, w sytuacji pandemii jedynym wyjściem byłoby albo czasowe wstrzymanie produkcji, albo narażanie pracowników na kontakt z wirusem.