Historie sukcesu
Jak podwoić efektywność linii produkcyjnej
Jak podwoić efektywność linii produkcyjnej
Dzięki zrobotyzowanemu stanowisku do pakowania linia produkcji preparatów do pielęgnacji obuwa w firmie KAPS stała się wydajniejsza o 50%.
Firma KAPS mieszcząca się w małopolskiej Rzezawie działa od 25 lat. Specjalizuje się w tworzeniu preparatów do impregnacji pielęgnacji i czyszczenia obuwia wykonanego z różnych materiałów. 90% produktów firmy KAPS jest wytwarzanych w Polsce. W procesie ich opracowywania i wdrażania bierze udział grupa działających lokalnie technologów i projektantów wspieranych wiedzą i doświadczeniem renomowanych instytucji badawczo naukowych. Dotąd proces pakowania realizowany był ręcznie, co wiązało się z dużą ilością monotonnej pracy. Firma postanowiła go jednak zautomatyzować.
Założenie było takie, by jedną linię produkcyjną mogła obsługiwać jedna osoba. Realizację tego celu rozpoczęto od wprowadzenia zautomatyzowanego stanowisko do pakowania. Składa się ono z robota EPSON VT6L, magazynu kartonów, stacji formowania kartonów, transportera zasilającego oraz transportera odbierającego pełne kartony.
Opakowania z preparatem do pielęgnacji obuwia po napełnieniu zakręceniu i naklejeniu etykiety transportowane są na stanowisko pakowania. Zrobotyzowane stanowisko pakujące jest zintegrowane z linią intralogistyczną pozwalającą na transport gotowych opakowań do stanowiska a następnie do magazynu, gdzie oczekują w kolejce do wysyłki.
Opracowaniem tego rozwiązania zajęła się firma Nandor z Bochni, a sprzęt i doradztwo zapewniła firma ASTOR. Inżynierowie z firmy Nandor opracowali wielofunkcyjny chwytak i zaprogramowali robota w taki sposób, aby na jednym stanowisku było realizowanych 5 różnych zadań.
Jak teraz wygląda proces pakowania?
- Robot pobiera jeden z kartonów z magazynku.
- Składa go i formuje opakowanie, podkleja.
- Odkłada w miejsce, gdzie na transporterze zasilającym podjeżdżają produkty do pakowania.
- Robot pobiera trzy puszki z preparatem do pielęgnacji obuwia i wkłada do kartonu. Czynność powtarza jeszcze trzy razy, by zapełnić cztery rzędy w opakowaniu.
- Zapakowany produktu odjeżdża na transporterze do magazynu.
Kluczową cechą wykorzystanego robota jest zintegrowany kontroler, który pozwala na dodatkową oszczędność miejsca na hali – nie ma konieczności podłączania zewnętrznego układu sterowania. Warto też zwrócić uwagę na przelotowy „nadgarstek” robota pozwalający na ukrycie przewodów a tym samym zwiększenie bezpieczeństwa pracy.
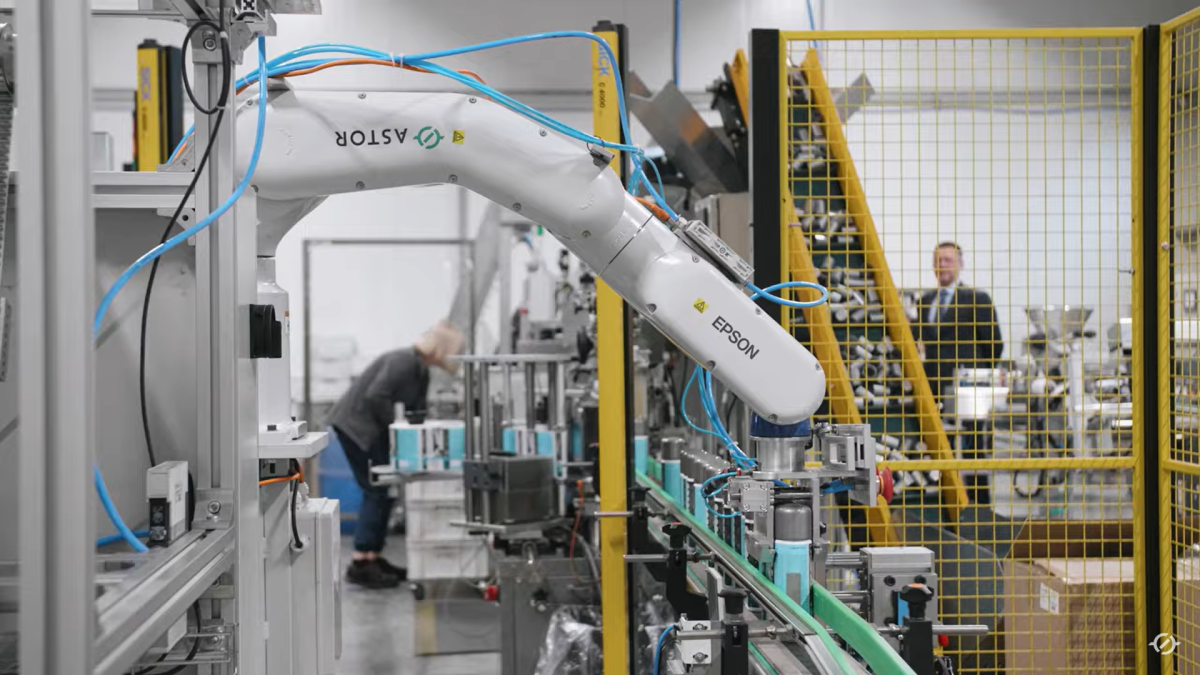
Korzyści
Przedstawiciele zarządu przekonują, że wykorzystanie robota pakującego EPSON zapewniło zwiększenie produkcji o 50% i znaczące odciążenie pracowników. Twierdzą, że inwestycja okazała się przełomem umożliwiającym lepsze dostosowanie się do wymagań rynku i poprawienie komfortu pracy zespołu.
Dzięki niskim kosztom zakupu i użytkowania robot świetnie sprawdza się jako alternatywa dla prostych samodzielnie wbudowanych manipulatorów. Inwestycja opłaca się również w przypadku linii pracujących na jedną zmianę.
Firma KAPS myśli o dalszej robotyzacji linii produkcyjnej.