Treści
Jak wykorzystać technologię cyfrowego bliźniaka w produkcji wsadowej i hybrydowej
Jak wykorzystać technologię cyfrowego bliźniaka w produkcji wsadowej i hybrydowej
Symulacja procesów produkcji wsadowej w tzw. cyfrowym bliźniaku pozwala lepiej dostosowywać ofertę fabryk do zmieniających się potrzeb rynku.
Produkcja materiałów budowlanych, przemysł chemiczny, farmaceutyczny czy spożywczy, to przykładowe sektory, w których wykorzystywana jest produkcja wsadowa. Pozwala tworzyć końcowy produkt poprzez poddanie surowców wejściowych sekwencji procedur oraz takie ich przetworzenie w wybranej jednostce czasu, by osiągnąć pożądane parametry. Te procesy przebiegają według ściśle określonej specyfikacji, tzw. receptur.
Pierwszym etapem jest dozowanie surowców do naczynia przetwarzającego, drugim jest poddanie ich rozmaitym formom oddziaływania (ogrzewanie, ochładzanie, zmiana ciśnienia, reakcje chemiczne). Trzecim – odebranie gotowego produktu. Wytwarzanie produktów w krótkich partiach, charakterystyczne dla produkcji wsadowej, ułatwia kontrolę jakości. Jeśli wada ujawni się w jednej partii, można poddać produkt dodatkowej obróbce w celu uzyskania oczekiwanej jakości lub dokonać korekty w następnej partii. Inną cechą produkcji wsadowej jest mniejsze ryzyko niepowodzenia przy wprowadzaniu nowych produktów na rynek. Jeśli efekty innowacyjnych działań okażą się niezadowalające, można je łatwo poprawić. Minusem tego typu produkcji są jednak przestoje pomiędzy poszczególnymi partiami, z którymi trzeba się liczyć, zwłaszcza, kiedy produkt jest modyfikowany. Zredukowanie tych przestojów, a także sprawienie, by produkcja wsadowa była płynna, wymaga planowania i analizowania danych.
Modyfikacje produktów są obecnie coraz częstsze, ponieważ niezależnie od gałęzi przemysłu, fabryki dążą do zwiększenia swojej konkurencyjności na rynku oraz do poprawy efektywności operacyjnej. Sprowadza się to do tego, że chcą nie tylko produkować towary o jak najwyższej i powtarzalnej jakości, ale też mieć możliwość szybkiej zmiany oferty produktowej, aby nadążyć za zmieniającymi się trendami rynkowymi i wymaganiami klientów. Wszystko to przy utrzymaniu możliwie najmniejszych stanów magazynowych surowców i produktów gotowych. Cyfrowy bliźniak, a więc wirtualna kopia realnych maszyn i procesów, może pomóc w realizacji tych celów.
Cyfrowy bliźniak w produkcji wsadowej:
- Pozwala zapewnić najwyższą wydajność instalacji
- Ułatwia uzyskanie precyzyjnej kontroli parametrów procesu
- Zapewnia ciągłość śledzenia produkcji
- Minimalizuje ryzyko wystąpienia błędów wynikających z ręcznie wykonywanych czynności lub manualnie rejestrowanych danych
- Zwiększa powtarzalność produkcji
- Ułatwia prowadzenie procesów i tworzenie nowych receptur dzięki intuicyjnym interfejsom
Konkretne zadania dla cyfrowych bliźniaków
Budowa i poprawne wykorzystanie cyfrowego bliźniaka we wdrażaniu systemów sterowania procesami produkcji wsadowej pozwala na skuteczne przeprowadzenie modernizacji lub uruchomienie nowej instalacji w krótkim czasie. Integracja cyfrowego bliźniaka z systemem sterującym procesem produkcyjnym pozwala na testy urządzeń, testy blokad procesowych i blokad bezpieczeństwa, testy faz i sekwencji, tworzenie receptur, wirtualne prowadzenie produkcji z utrzymaniem zadanych parametrów procesowych oraz szkolenie operatorów.
Przygotowane i przetestowane oprogramowanie umożliwia wdrożenie systemu sterowania, który w przemyślany sposób zarządza precyzyjnym utrzymaniem parametrów procesu produkcyjnego.
Najczęstsze problemy, z jakimi spotykają się użytkownicy starszych systemów sterowania produkcją wsadową oraz sposoby na ich rozwiązanie dzięki wykorzystaniu technologii cyfrowych bliźniaków:
Skomplikowany system tworzenia receptur
Wiele starszych systemów sterowania produkcją wsadową zostało opracowanych w czasach, gdy programowanie było złożonym procesem i wymagało specjalistycznej wiedzy. Dlatego ich interfejs był projektowany z myślą o specjalistach, którzy mieli doświadczenie w programowaniu. Jednak z biegiem czasu technologia uległa zmianie i najnowsze systemy sterowania produkcją wsadową oferują graficzny, bardziej intuicyjny i łatwiejszy w obsłudze interfejs użytkownika.
Poza ułatwieniem samego sposobu tworzenia receptur, wykorzystanie symulatora procesów produkcyjnych pozwala na przeprowadzenie testów oraz dopasowanie nowych receptur do istniejącej instalacji. To znacznie skraca czas projektowania nowych produktów i minimalizuje ryzyko wystąpienia błędów w pierwszych partiach.
Cyfrowy bliźniak procesu produkcyjnego jest wirtualną reprezentacją całej instalacji produkcyjnej i wszystkich procesów w niej zachodzących (np. symulacja reakcji chemicznych).
Problemy ze stabilnością utrzymania parametrów procesowych
Wytworzenie danego produktu wymaga utrzymania wielu parametrów procesu produkcyjnego w ściśle określonych wartościach. Dobór odpowiednich parametrów procesowych można wykonać na dwa różne sposoby: metodami prób i błędów na pracującej instalacji lub wykorzystując symulator procesu produkcyjnego – cyfrowego bliźniaka. Oba sposoby są dobre, przy czym wykorzystanie symulatora procesu pozwoli osiągnąć ten sam cel, oszczędzając czas i ograniczając możliwe straty surowców, przy zachowaniu najwyższego bezpieczeństwa ludzi i instalacji.
Ograniczona powtarzalność jakości produktów gotowych
Kiedy parametry procesu wytwarzania nadzorowane są przez technologów, często trudno je utrzymać na stałym przewidywalnym poziomie. Symulator procesu produkcyjnego – cyfrowy bliźniak – pozwala osiągnąć ten cel po ustaleniu najbardziej odpowiednich warunków wytwarzania produktu. Dodatkowo odpowiednio wdrożony system sterowania, czerpiący informacje z cyfrowego bliźniaka, pozwala w powtarzalny sposób utrzymać zadane parametry na każdym etapie produkcji. Nawet jeśli pewne czynności muszą zostać wykonane manualnie przez operatora, system w przejrzysty sposób daje wskazówki, polecenia i weryfikuje poprawność wykonanych operacji.
Brak systemu raportowania lub system, który nie spełnia norm i wymagań odbiorców
W wielu gałęziach przemysłu, gdzie jakość wyrobu końcowego ma kluczowe znaczenie, istotną rolę odgrywa możliwość śledzenia historii procesów produkcyjnych, od chwili pozyskania surowców, poprzez przetwarzanie, aż do momentu końcowej produkcji i dystrybucji.
Wykorzystując dane historyczne do odtworzenia danego scenariusza na symulatorze procesu produkcyjnego – cyfrowym bliźniaku – użytkownik jest w stanie szybciej zlokalizować źródło nieprawidłowości, a także wykonać odpowiednie zmiany i testy w celu uniknięcia pomyłek w przyszłości.
Wysokie koszty utrzymania systemów sterowania i ograniczona dostępność wsparcia technicznego
Wykorzystanie symulatora linii produkcyjnej lub całego zakładu produkcyjnego ułatwia utrzymanie i rozbudowę systemu sterowania. Mając możliwość symulowania planowanych zmian, użytkownik może sprawdzić, jaki będą one miały wpływ na bieżący proces, a następnie zaplanować i wdrożyć wcześniej sprawdzone rozwiązania. Cyfrowy bliźniak może też służyć do analityki predykcyjnej.
Ograniczone możliwości rozbudowy
Systemy i aplikacje kontrolujące złożone procesy technologiczne z natury rzeczy są rozległe i skomplikowane. W przypadku rozbudowy lub modyfikacji linii produkcyjnej, zmiana i dopasowanie oprogramowania do implementowanych zmian mogą być trudne i czasochłonne. Dlatego wykorzystanie wirtualnej kopii tych systemów ułatwia rozbudowę, skalowanie i powielanie sprawdzonych rozwiązań w kolejnych liniach produkcyjnych i w innych lokalizacjach w organizacji.
Wszystkie te zastosowania technologii cyfrowego bliźniaka są odpowiedzią na konkretne wyzwania produkcji wsadowej, ale efekty ich działania sumują się. Prowadzą do poprawy zarządzania procesem produkcji, zarówno na poziomie operacyjnym jak i biznesowym, co w rezultacie przekłada się na lepsze wyniki finansowe firm produkcyjnych i większą satysfakcję klientów.
STUDIA PRZYPADKU:
PROJEKT GREENFIELD
System sterowania instalacją do kondensacji żywic
Na etapie tworzenia systemu sterowania powstał symulator procesu produkcji żywic, przeszkolono inżynierów procesu i operatorów na długo przed uruchomieniem systemu. W efekcie już pierwsza próba wyprodukowania żywicy przy wykorzystaniu nowego reaktora zakończyła się uzyskaniem produktu o bardzo wysokiej jakości.
PROJEKT BROWNFIELDS
System sterowania instalacją do produkcji polioli poliestrowych
Obejmował kompleksową wymianę systemu sterowania w zakładzie produkującym poliole poliestrowe, włącznie z projektem i dostawą sieci przemysłowej i szaf sterowniczych. Tworzenie systemu rozpoczęło się od zbudowania symulatorów procesów produkcyjnych w reaktorach oraz przeszkolenia inżynierów procesu i operatorów.
W efekcie uruchomienie gotowego, fizycznego systemu sterowania odbyło się w ciągu zaledwie dwudniowego, weekendowego przestoju. Już przy produkcji pierwszego wsadu można było osiągnąć bardzo wysoką jakość, a dodatkowo dzięki testom prowadzonym na cyfrowym bliźniaku udało się skrócić cykl produkcyjny o ok. 10%.
Dowiedz się więcej
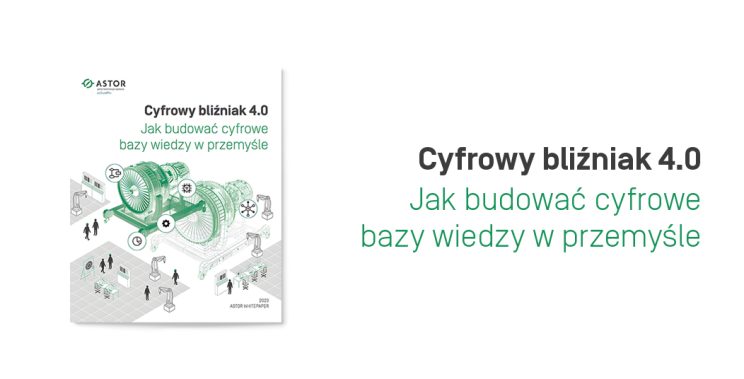
Dowiedz się więcej o cyfrowym bliźniaku w nowej publikacji „Cyfrowy bliźniak 4.0. Jak budować cyfrowe bazy wiedzy w przemyśle.„