Treści
Początek zarządzania przez fakty, czyli gromadzenie danych
Początek zarządzania przez fakty, czyli gromadzenie danych
Całkiem niedawno pisaliśmy na łamach bloga Biznes i Produkcja o podejmowaniu decyzji, które zaczynają się od gromadzenia danych. Dziś postanowiliśmy pokazać, przez jakie etapy przechodzi większość firm w procesie ewolucji gromadzenia danych. Spróbujemy także odpowiedzieć, czy proces zmiany można skrócić w warunkach Państwa firm.
Gromadzenie danych = proces strategiczny
W pierwszej kolejności musimy oczywiście rozróżnić proces, gdzie gromadzenie danych ma za zadanie zainicjować budowę spójnego systemu raportowego, mającego funkcjonować przez dłuższy okres czasu, od działań ad hoc, gdzie kluczowe jest przygotowanie raportu tu i teraz, pod potrzeby danej decyzji. Bardzo często jednak właśnie w takich sytuacjach zaczynamy dostrzegać błędy w przygotowaniu danych, ich rejestracji, kompletności czy wręcz czytelności niektórych zapisów, np. w przypadku formy rejestrów papierowych.
Właściwe przygotowanie tego pierwszego kroku, jakim jest gromadzenie danych, to forma szacunku, jaki okazuje się organizacji czy wręcz swoim pracownikom, bo to osoby operacyjnie odpowiedzialne za wprowadzenie danych będą poświęcały swój czas dla potrzeb firmy. To także wyraz szacunku dla właścicieli firm lub Zarządów, bo im efektywniejsze procedury gromadzenia danych, tym mniej czasu zajmują, a co ważniejsze – mniej kosztują organizację.
W swojej praktyce konsultanta, a ostatnio Interim Managera odpowiedzialnego za zarządzanie spółką produkcyjną, dostrzegam jeszcze dogłębniej rolę tego ostatniego aspektu, czyli kwestii finansowania zmian w gromadzeniu danych. Nie zawsze spółkę stać na drastyczne i kosztowne kroki, mające na celu zagwarantować skokową poprawę jakości danych, redukcję administracji oraz szybkość i precyzję ich przetwarzania. Czasami droga ewolucyjnych, a nie rewolucyjnych zmian, jest tą, jaką wybiera organizacja… i nie zawsze jest to droga gorsza!
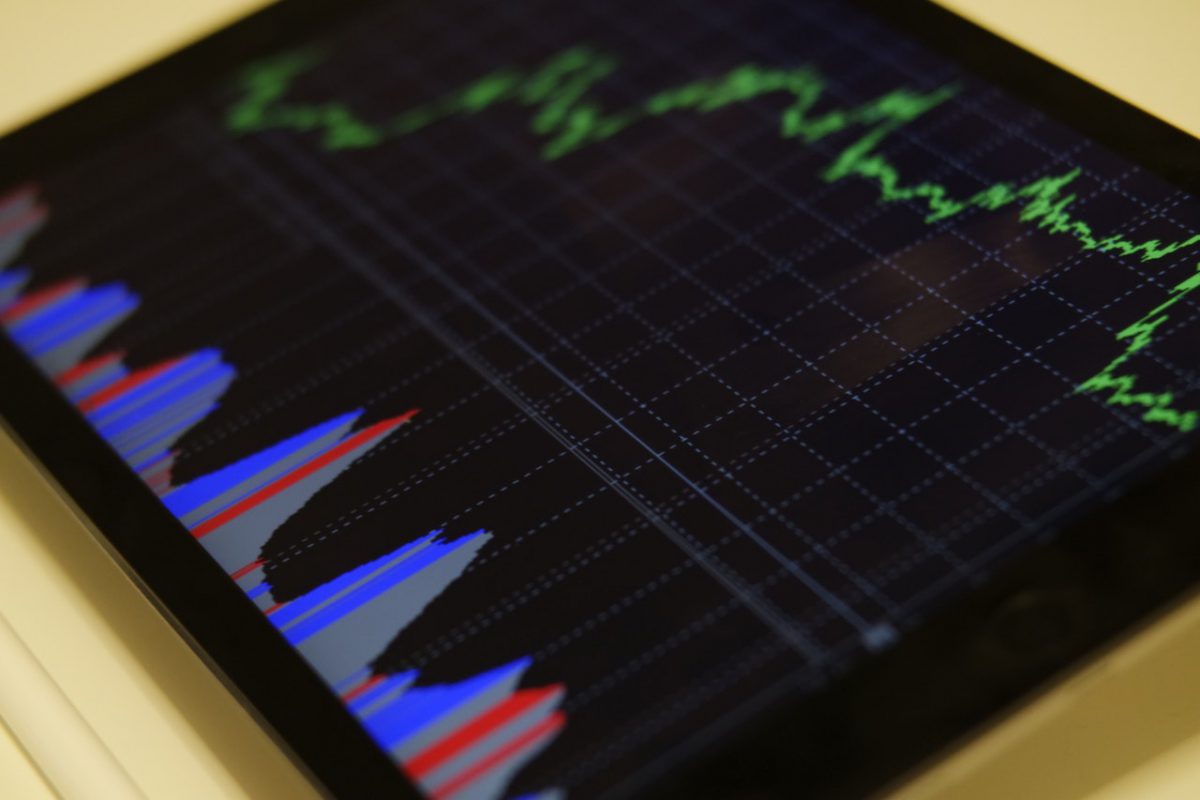
Etap 1. gromadzenia danych: Papier
Pierwszą z dróg, którą wybierają organizacje na drodze zbierania danych, jest papier. W ostatnich czasach nie zawsze mówimy dosłownie o papierze, gdyż może być to forma rejestracji danych na tablicach dostosowanych do zapisywania danych w odpowiedniej formie. Zawsze jednak kluczowym aspektem tego etapu jest ulotność powstających zapisów, wynikająca z braku jakichkolwiek ustrukturyzowanych analiz, a powstający papier jedynie zasila kilogramami swojej wagi archiwum firmy lub szafę konkretnego menedżera w organizacji. Powstający zapis ma jedynie „zagwarantować spokój ducha” danego menedżera odpowiedzialnego za wskazany kawałek organizacji, że proces jest kontrolowany.
Drugim aspektem świadczącym, że firma jeszcze jest na etapie „papieru”, to sytuacja, że proces rejestracji danych jest dublowany – najpierw zgłoszenie zdarzeń następuje na papierze, a potem występuje mozolne przepisywanie do raportów elektronicznych – czasochłonne, obarczone błędami, pomijające wiele szczegółów. To ostatnie ma miejsce, gdy „przepisuje” inna osoba niż ta rejestrująca dane. Szczególnym przypadkiem etapu „papieru” jest sytuacja, w której zbierane w nieustrukturyzowanej formie dane na papierze przepisywane są „na czysto” do zeszytów zmianowych lub np. Rejestru Awarii.
Oczywiście rejestrowanie danych na papierze w niektórych przemysłach produkcji ciągłej, np. chemicznym, petrochemicznym ma charakter nie tyle zbierania danych, bo większość parametrów i tak kontrolowana jest przez nadrzędne systemy produkcyjne, ale utrzymywania operatora instalacji w gotowości i pewnym reżimie kontroli kluczowych parametrów procesu produkcyjnego we wcześniej zdefiniowanych odstępach czasu. Jednakże i tutaj następuje postęp i zmiana miejsca składowania danych z papieru na arkusze kalkulacyjne.
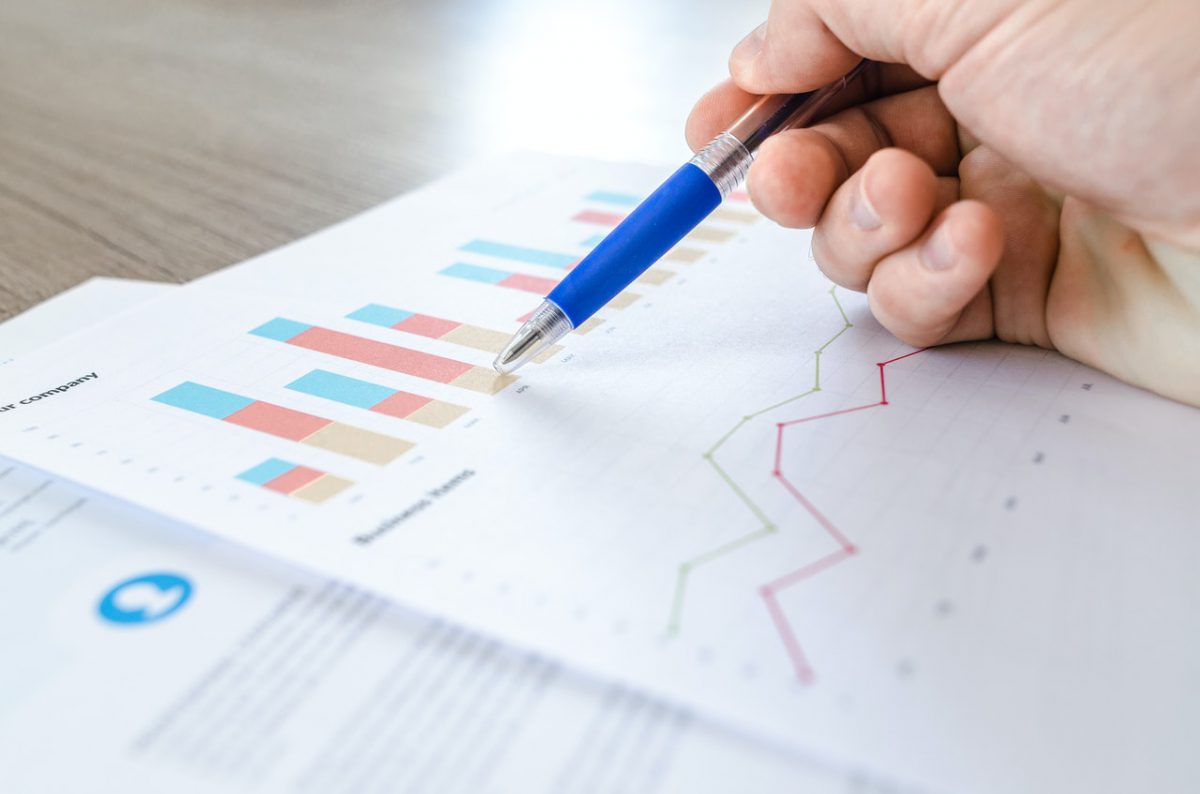
Na koniec chciałbym się podzielić pewną zagraniczną obserwacją, która najprawdopodobniej zaskoczy wielu czytelników. Po którym z państw świata spodziewalibyście się Państwo największego poziomu „papierologii”? Otóż uznawany przez nas w Europie za najbardziej scyfryzowany kraj kwitnącej wiśni zaskoczył mnie największą ilością „produkcji” raportów papierowych! Duży biurowy open space miał jedną ze ścian wyposażoną w znane nam z przychodni zdrowia szafy na karty pacjentów, w których przechowywane były wszelakie raporty – od efektywności produkcji, do raportów procesu kontroli jakości.
Etap 2. gromadzenia danych: Pierwsze szablony oraz transfer danych do Excela
Najczęściej jest to etap firm, które w ramach monitorowania danych danego procesu, zaczynają dostrzegać potrzebę ich analizowania, a nie jedynie okresowego przeglądania czy weryfikowania niezgodności. Wraz z przejściem do etapu 2. poprawia się głównie jakość danych w wyniku standaryzacji papierowych formatek rejestracji danych.
Krok w kierunku etapu 2. jest pozytywną zmianą w firmach, które czują potrzebę poprawy swoich procesów, dostrzegając nieefektywności, ale głównie potencjał poprawy w nich drzemiący. Kontynuacją tych działań jest zapoczątkowanie w mniej lub bardziej ustrukturyzowany sposób zmiany kulturowej w organizacji pod płaszczem projektów Lean, TPM czy WCM. Istotą tych programów jest identyfikacja strat (japońskie muda) oraz przeobrażanie organizacji w myśl zasady Ciągłego Doskonalenia.
Zbieranie danych zaczyna być powszechne, a menedżerowie dostrzegają wartość w sformułowaniu „nie można zarządzać czymś, czego nie da się zmierzyć” (W. Edwards Deming).
Etap 3. gromadzenia danych: Eliminacja papieru – komputeryzacja procesu
Naturalnym przejściem pomiędzy etapami 2 i 3 jest eliminacja papieru, czyli raportowanie bezpośrednio do systemów komputerowych lub zautomatyzowanych raportów arkuszy kalkulacyjnych. Firmy, dostrzegając ewidentną stratę czasu oraz dodatkowy koszt raportowania papierowego, zaczynają wykorzystywać kioski na produkcji, tablety czy systemy mobilne wspierające pracowników. W kilku organizacjach kioski dla rejestracji danych pracownicy nazywali humorystycznie bankomatami – może bliżej im do wpłatomatów, gdyż z reguły nacechowane są na „przyjmowanie” danych.
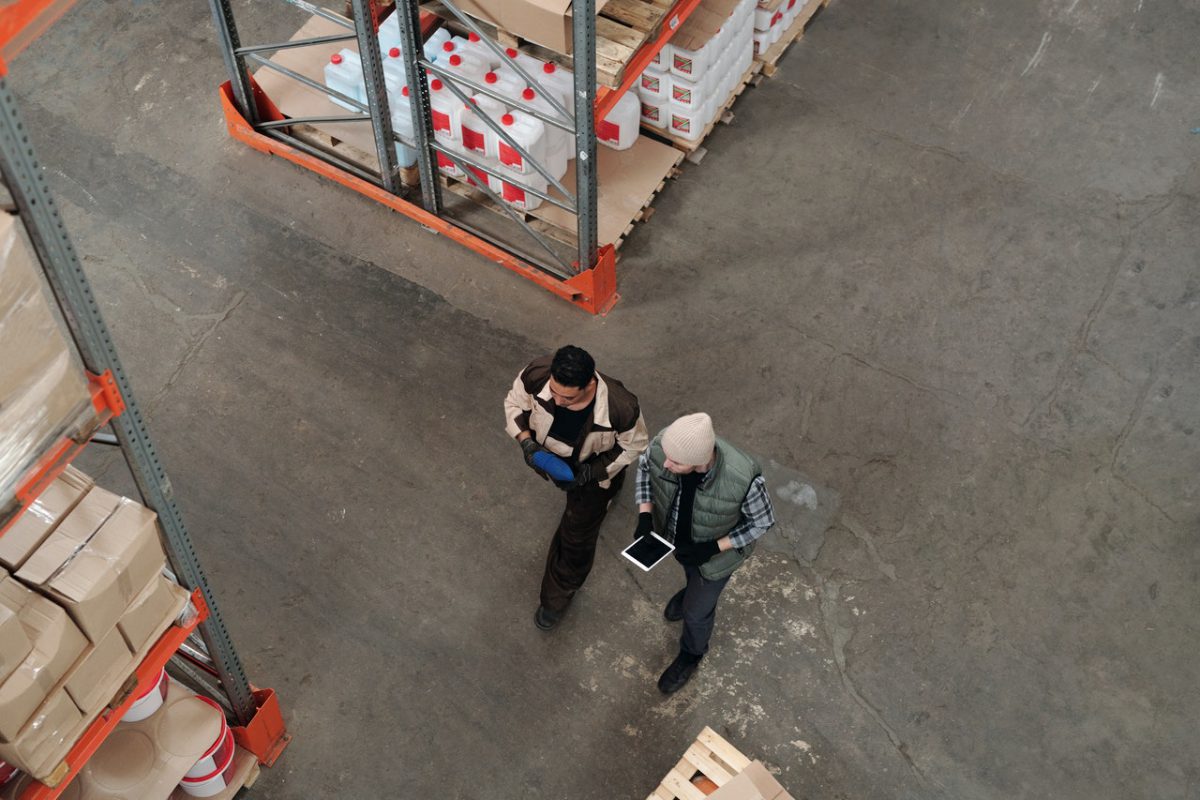
Czy firma może zrobić skrót i rozpocząć proces gromadzenia danych od tego etapu? Jak najbardziej, aczkolwiek wymaga to dużej samodyscypliny. Kioski dla rejestracji danych można zastąpić komputerami w mistrzówkach z predefiniowanymi formularzami czy systemami, zazwyczaj jeszcze nie czasu rzeczywistego. W efektywności działań firm w ramach etapu 3 kluczowa jest zasada, że im bliżej kiosk/komputer stanowiska pracy, tym szybsza i precyzyjniejsza (brak opóźnienia) informacja w procesie podejmowania decyzji czy raportowaniu.
Jakie są plusy przejścia organizacji na etap 3. rozwoju procesu gromadzenia danych?
- szybkość pojawienia się w systemie analitycznym,
- prostota rejestracji (uwaga na zdolności „informatyczne” pracowników),
- standaryzacja procesu i/lub gromadzonych danych,
- oszczędność kosztów (np. wydruki).
Oczywiście z eliminacją papieru w etapie 3 wiążą się pewne wymagania:
- pierwsze inwestycje w sprzęt komputerowy na produkcji,
- szkolenia dla ludzi – merytoryczne i czasami techniczne,
- stworzenie struktury archiwizacji danych i wiedzy raportowej (początki Zarządzania Wiedzą w organizacji),
- konieczność przygotowywania formularzy w takiej formie, aby dane można było w sposób łatwy przetwarzać.
Etap 4. gromadzenia danych: Automatyzacja, czyli precyzja
Początek XXI wieku, nazywanego erą komputerów i cyfrowego świata, nie od razu znalazło odzwierciedlenie na produkcji, zarówno w dużych, jak i małych firmach. Na szczęście coraz więcej organizacji zaczyna dostrzegać potrzebę posiadania danych, a następnie informacji tu i teraz, w czasie rzeczywistym, bez dodatkowej ingerencji ludzi, gdyż ona generuje szum informacyjny, błędy i brak zaufania do tego, co zostaje przetworzone i przekazane do góry.
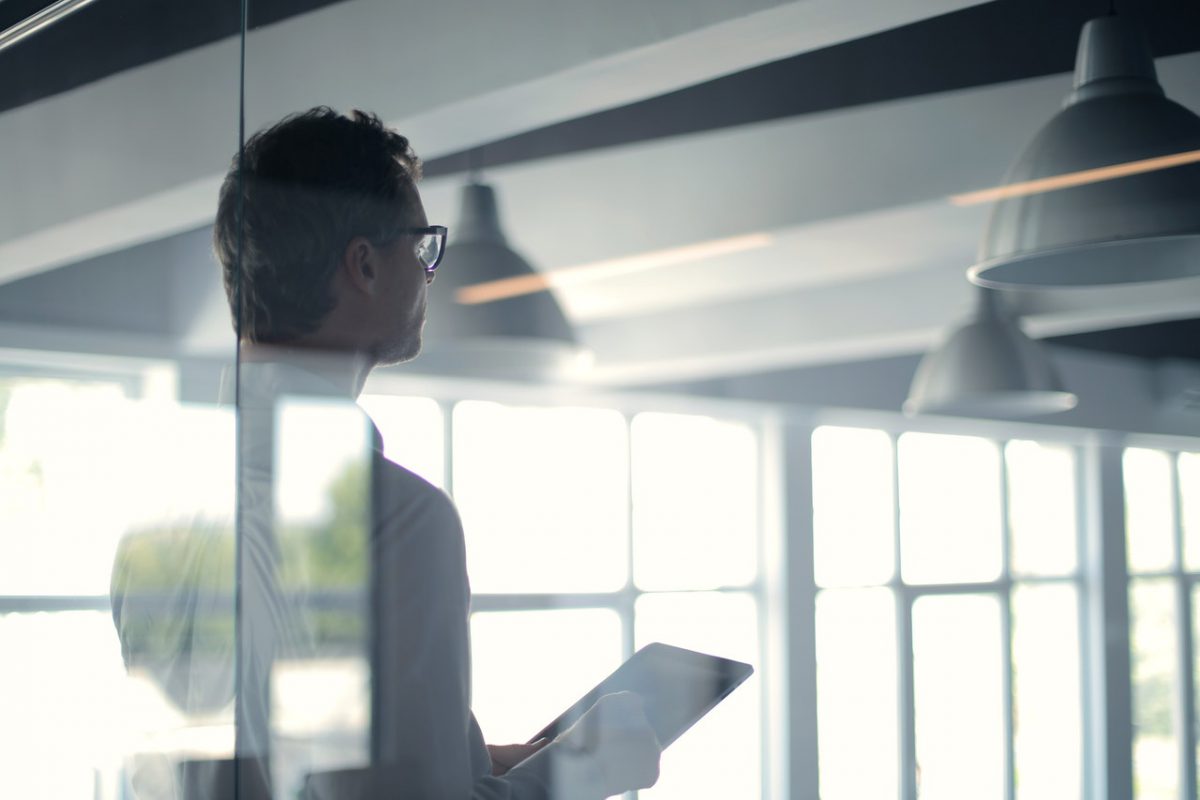
W ramach swoich projektów w branży meblowej, które zrealizowałem, w ciągu ostatnich kilku lat dostrzegłem także… nieświadome wejście w etap 4. Ma to miejsce wraz z postępem, jaki niosą za sobą inwestycje w park maszynowy, których dokonują firmy. Maszyny są coraz bardziej zinformatyzowane, dające możliwości podglądu parametrów pracy praktycznie z każdego miejsca na świecie, ale jednak firmy cały czas z tego nie korzystają. Dlaczego? Wyróżnić należy 3 przypadki:
- nieświadomość posiadanych możliwości oprogramowania dostarczanego z zakupionym sprzętem w jednym pakiecie,
- przeniesienie odpowiedzialności za zarządzanie danymi w maszynie działom IT, które później administrują od strony technicznej, ale dane cały czas są niedostępne dla menedżerów produkcji, np. „kody dostępu posiada zewnętrzna firma serwisowa, więc nie możemy wyciągnąć danych”,
- firmy, koncentrując się na technicznych parametrach maszyn produkcyjnych, oszczędzają na modułach do gromadzenia i transferu danych, w myśl zasady „zrobi to przecież pracownik, którego mamy od tego”.
Z drugiej strony jest świadoma automatyzacja gromadzenia danych poprzez włączanie dodatkowych czujników w oprzyrządowanie maszyn, czasami bardzo wiekowych, a następnie standaryzacja i kalibracja sygnałów oraz zdarzeń, aby w sposób niezależny od pracownika, w trybie rzeczywistym gromadzić i przetwarzać dane produkcyjne.
Etap 4. rozwoju procesu gromadzenia danych jest elementem postępu, jaki dzieje się na naszych oczach, czyli Przemysłu 4.0. Kluczowymi aspektami systemów wspierających ww. zadania są m.in.
- międzyoperacyjność, czyli integracja z innymi systemami w organizacji, np. do planowania produkcji, połączenie produkcji z utrzymaniem ruchu),
- decentralizacja, która pozwala na zbieranie danych o większej szczegółowości i „u źródła”,
- zdolności zarządcze w czasie rzeczywistym, związane z przetwarzaniem danych w trybie on-line i takim podejmowaniem decyzji,
- orientacja na usługi, czyli oferowanie przez firmy sprzętowe także rozwiązań miękkich czy doradczych, jak efektywnie wykorzystać potencjał sprzętu i analizy danych.
Firma ASTOR wraz z organizacją, którą ja reprezentuję, wychodzi naprzeciw potrzebom organizacji zastanawiających się, jak sprawnie przejść do etapu 4., oferując m.in. kompleksowe rozwiązanie ImProdis, czyli element systemu wspierający zarówno gromadzenie, monitorowanie danych, a przede wszystkim wspierający podejmowanie decyzji w obszarze produkcji i utrzymania ruchu.
Czy można skrócić proces ewolucji?
Oczywiście, że TAK! Jednak trzeba zadać sobie pytanie, na jakim etapie rozwoju kultury zbierania danych jest nasza organizacja oraz ile czasu i środków chcemy jako organizacja zainwestować. I to nie tylko w sprzęt, a szerzej – infrastrukturę IT w firmie, ale nawet bardziej: w rozwój ludzi, aby systemy zaimplementowane były wykorzystywane w takim zakresie, dla jakiego zostały stworzone.
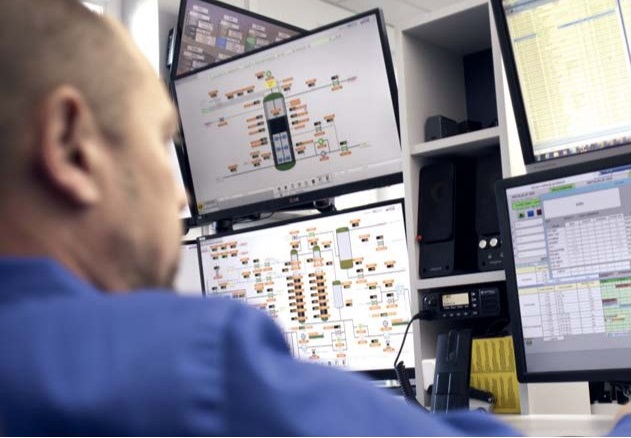
Wielokrotnie w swojej pracy spotykałem się z sytuacją, gdy organizacja zaangażowała znaczne zasoby (pieniądze, czas, ludzi), aby wdrożyć rozwiązania „Best-in-Class”, ale po etapie euforii „wyższego” szczebla, ścisłego monitoringu wdrożenia, przychodzi szara rzeczywistość, w której pracownicy wykorzystują ułamek możliwości wdrożonego rozwiązania.
Powstaje pytanie: gdzie był błąd? Czy firma wdrożeniowa, czy narzędzia? Stawiam tezę, z którą, mam nadzieję, Państwo się zgodzicie, że czasami to organizacja nie dorosła do tak zaawansowanego rozwiązania! Zamiast stopniowo „przyzwyczajać” pracowników do nowych obowiązków w ramach każdego z etapów rozwoju procesu gromadzenia danych, organizacja wybiera drogę na zbyt duże skróty. Powstaje opór przed nowym, gdyż brakuje właściwego zarządzania zmianą. Pracownicy zaczynają nowe postrzegać jako zło burzące wygodną rzeczywistość, narzędzie kontroli i represji poprzez większą transparentność danych i informacji – „góra chce nas kontrolować”.
W mojej ocenie kluczowe jest, aby pracownicy stopniowo rozwijali się z narzędziami i sami dostrzegali ich wartość, jak redukcję biurokracji i „papierologii”, na którą utyskują wszyscy. Takie stopniowe uczenie się organizacji pozwala jej dostrzegać i właściwie nazywać potrzeby, których jeszcze do niedawna nie identyfikowała. W tym miejscu kluczowe jest właściwe ukierunkowanie tej energii w zmianę, ale zawsze z dobrym i odpowiedzialnym partnerem procesowo-narzędziowym, aby nie zawieść oczekiwań i nie przerodzić ich w frustrację.
Podsumowanie:
- Właściwe gromadzenie danych to szacunek dla własnych pracowników i siebie – mniejsza biurokracja oraz precyzyjniejsze informacja, a w konsekwencji skuteczniejsze decyzje.
- Typowe organizacje przechodzą przez 4 etapy rozwoju systemów gromadzenia danych, t.j. od papieru do pełnej automatyzacji.
- Organizacje w XXI wieku oczekują informacji natychmiast, więc jedynym kierunkiem jest przybliżanie się do pełnej automatyzacji zbierania, a następnie przetwarzania danych.
- Nowe narzędzia czy formy gromadzenia danych należy traktować jak zmianę w organizacji i skutecznie nimi zarządzać.
- Właściwe narzędzia i partnerzy wdrożeniowi są kluczowi dla precyzyjnego zaadresowania i zaspokojenia potrzeb zarówno organizacji, jak i poszczególnych pracowników.