Treści
Wdrożenie systemu MES. Co należy wiedzieć przed rozpoczęciem projektu?
Wdrożenie systemu MES. Co należy wiedzieć przed rozpoczęciem projektu?
Cyfryzacja firm produkcyjnych nie jest koncepcją nową. Systemy takie jak MES wspierające przedsiębiorstwa produkcyjne na różnych poziomach ich funkcjonowania, są rozwijane i wdrażane od dawna. W ostatnich latach obserwujemy jednak znaczące zwiększenie zainteresowania tym tematem. Dlaczego warto właśnie w ten sposób inwestować w transformację cyfrową i jak najskuteczniej ją przeprowadzić?
Czasy, kiedy wystarczyło „po prostu produkować” dobre produkty, aby zarabiać pieniądze i rozwijać firmę, minęły bezpowrotnie. Najpoważniejszym wyzwaniem, przed jakim stoją przedsiębiorstwa produkcyjne, jest dynamiczna zmienność środowiska rynkowego, w tym w szczególności wymagań klientów. Poziom konkurencyjności jest bardzo wysoki i wciąż rośnie. Firmy muszą mierzyć się jednak nie tylko z bezpośrednią konkurencją, ale także z rosnącymi wymaganiami dotyczącymi bezpieczeństwa i ochrony środowiska, a także z ogólną niepewnością, wynikającą z niestabilnej sytuacji geopolitycznej i gospodarczej. Jest to efekt problemów, z którymi świat musi się obecnie zmagać, takich jak pandemia, kryzys na rynku półprzewodników, a także wydarzenia polityczne i konflikty międzynarodowe.
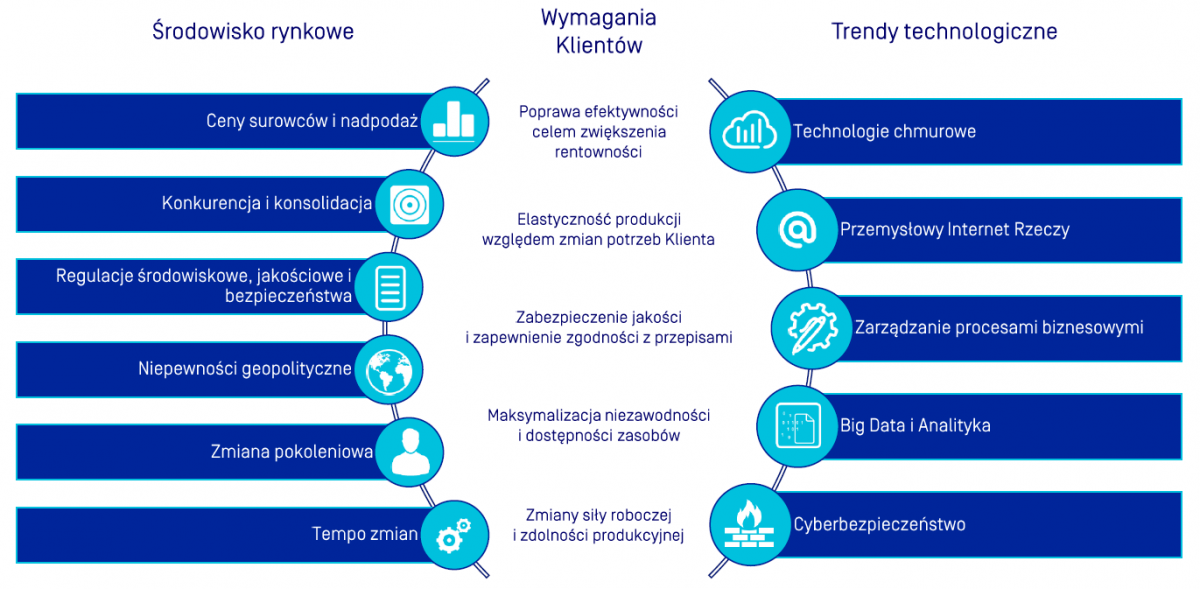
Aby sprostać tym wszystkim wyzwaniom, konieczne jest nieustanne doskonalenie procesów produkcyjnych. W efekcie wiele firm decyduje się na podjęcie działań, które do tej pory były odkładane na później.
Najważniejszy jest przepływ informacji
Główną barierą w skutecznym zarządzaniu produkcją i podnoszeniu jej efektywności jest pozyskiwanie informacji i ich późniejsze wykorzystywanie. Do tego sprowadzają się właściwie wszystkie wyzwania, przed którymi stają osoby odpowiedzialne za doskonalenie procesów produkcyjnych. Niezależnie bowiem od tego, czy chodzi o podnoszenie wydajności, obniżanie kosztów, czy o jakiekolwiek inne usprawnienie – niezbędne jest posiadanie właściwych informacji, dzięki którym będziemy wiedzieć, dokładnie co, gdzie i dlaczego się dzieje. Podejście takie nazywamy zarządzaniem przez fakty.
Jeżeli przedsiębiorstwo nie nadąża z realizacją zamówień, potrzebne są informacje o rzeczywistej wydajności i wykorzystaniu maszyn. Dzięki nim możemy zidentyfikować „wąskie gardła” – obszary, w których wydajność, dostępność lub jakość wymaga poprawy. W konsekwencji jesteśmy w stanie zwiększyć zdolności produkcyjne zakładu wyłącznie poprzez optymalne wykorzystanie potencjału dostępnego parku maszynowego, bez konieczności zakupu nowych urządzeń.
Podobnie jeżeli mamy problem ze zbyt wysokimi kosztami, chcemy je obniżyć, ale w taki sposób, aby nie odbiło się to na jakości. Aby to było możliwe, musimy dysponować informacjami o tym, gdzie „ucieka” najwięcej pieniędzy. Musimy znać Techniczny Koszt Wytworzenia, a więc koszt komponentów (surowców) i mediów, a także koszt pracy maszyn oraz ludzi. Musimy też wiedzieć, gdzie i dlaczego pojawiają się problemy z jakością, skutkujące nadmierną ilością zwrotów i reklamacji.
Cyfryzacja odpowiedzią na problemy przedsiębiorstw produkcyjnych
W jaki sposób cyfryzacja procesu produkcyjnego może pomóc sprostać tym wszystkim wyzwaniom? Przedsiębiorstwo produkcyjne to bardzo złożony organizm, a więc naturalnie proces przepływu informacji też jest złożony. Prawda jest taka, że przedsiębiorstwo funkcjonuje tak dobrze, jak efektywny jest przepływ informacji. Istnieje nawet popularna anegdota branżowa, która mówi, że – przez analogię do znanego m.in. w logistyce terminu FIFO (First In, First Out) – w przypadku systemów informatycznych dla przemysłu możemy wprowadzić pojęcie GIGO (Garbage In, Garbage Out – śmieci na wejściu, śmieci na wyjściu). Słowem: jeżeli dane wejściowe są niskiej jakości, to efekt działania systemu również będzie słaby.
Dlatego transformacja cyfrowa przedsiębiorstwa jest to de facto digitalizacja informacji oraz procesów ich przepływu, z wykorzystaniem systemów IT. Realizowana zwykle krok po kroku w kolejnych obszarach ma ostatecznie doprowadzić do kompleksowej cyfryzacji, czyli cyfrowego obiegu informacji. Celem jest osiągnięcie stanu, w którym – dzięki systemom informatycznym – możliwe jest zbieranie i właściwe organizowanie danych produkcyjnych w taki sposób, aby były one zawsze czytelne i użyteczne. Cyfryzacja radykalnie ułatwia proces dokumentowania produkcji i śledzenia genealogii produktów. Umożliwia też zautomatyzowane i bezbłędne wyliczanie wskaźników efektywności produkcji, takich jak np. OEE (Overall Equipment Effectiveness).
Fazy cyfrowej transformacji
Analizując procesy cyfrowej transformacji przedsiębiorstw produkcyjnych można wyróżnić kilka typowych faz takiej transformacji. W pierwszej fazie często wciąż jeszcze mamy do czynienia z papierem oraz danymi ręcznie wprowadzanymi np. do arkuszy kalkulacyjnych lub bezpośrednio do systemów biznesowych. Zdarza się tak nawet pomimo tego, że na niższym poziomie produkcja jest całkowicie zautomatyzowana.
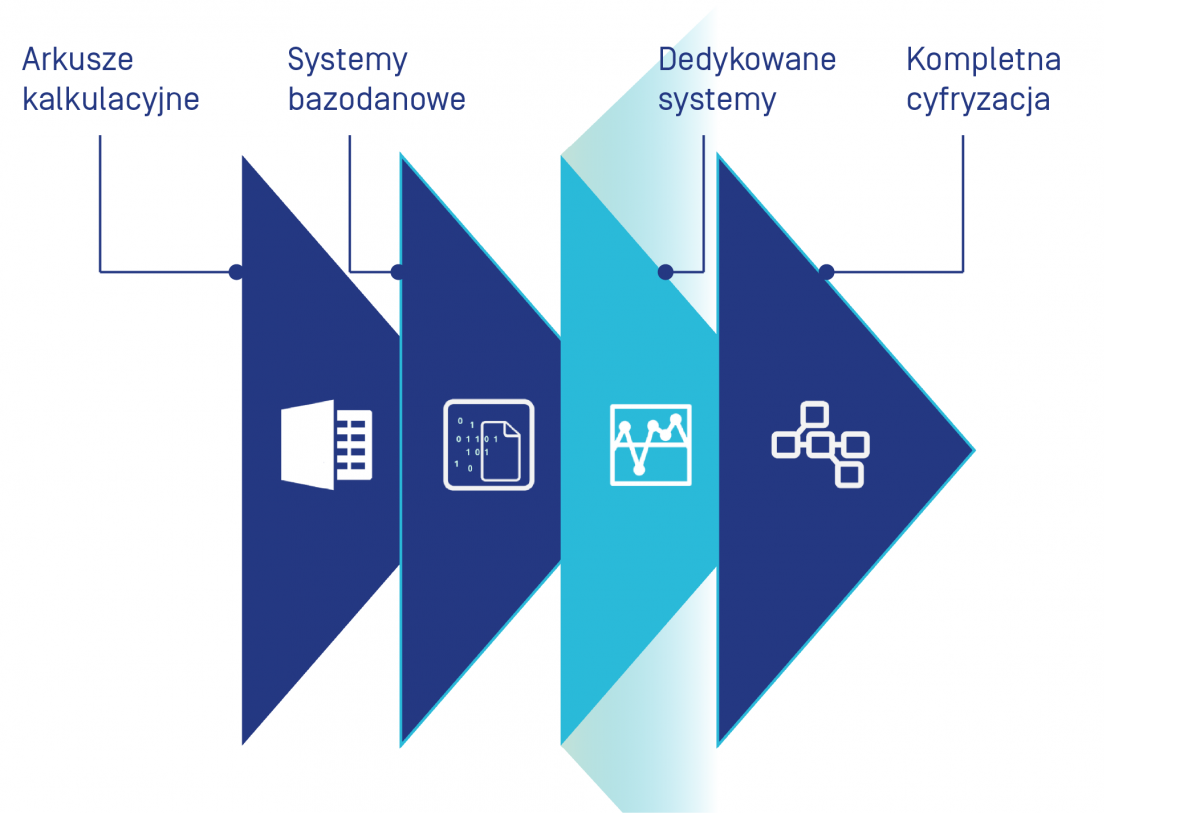
Takie „ręczne” systemy obiegu informacji są zwykle w pierwszej kolejności uzupełniane o bazę danych, której zadaniem jest zbieranie i udostępnianie informacji, a tym samym całkowite wyeliminowanie papierowych dokumentów. Jest to pierwszy krok do zbudowania scentralizowanego systemu informatycznego, ale by można było myśleć o kompletnej cyfryzacji przedsiębiorstwa, konieczne jest przejście przez etap dedykowanych systemów informatycznych. Systemy takie z jednej strony powinny realizować konkretne zadania z zakresu zarządzania produkcją, a jednocześnie powinny być na tyle otwarte, aby wspierać kolejne etapy transformacji.
Więcej na ten temat można przeczytać w artykule „Początek zarządzania przez fakty, czyli gromadzenie danych”.
Cechy otwartych systemów informatycznych
Jak należy rozumieć pojęcie otwartych dedykowanych systemów IT? Zwykle spełniają one zadania takie, jak:
- realizowanie specjalistycznych funkcji oprogramowania, m.in.:
- zarządzanie produkcją,
- zarządzanie efektywnością produkcji,
- zarządzanie utrzymaniem ruchu,
- zarządzanie flotą wózków lub innych urządzeń transportowych,
- planowanie i harmonogramowanie,
- monitoring mediów,
- łatwość wdrożenia i użytkowania oprogramowania,
- zapewnienie możliwości automatycznego zbierania danych i generowania kontekstowej informacji,
- otwartość na integrację z innymi systemami,
- dopasowanie do firmowej strategii IT i istniejącej infrastruktury IT.
Cele te można zrealizować stosując różne podejścia i różne scenariusze, wdrażając poszczególne elementy etapami, w takiej kolejności, by uzyskać jak najlepsze efekty. Innymi słowy – proces transformacji cyfrowej warto w odpowiedni sposób zaplanować. Otwartość systemu polega na łatwości integracji i możliwości rozbudowy, ale żaden system, nawet otwarty, nie spełnia tych wszystkich punktów jednocześnie. Jest on raczej środowiskiem systemowym, platformą do cyfryzacji różnych obszarów przedsiębiorstwa, a nie kompletnym, pojedynczym rozwiązaniem.
Digitalizacja procesu zbierania danych
Aby możliwe było efektywne wykorzystanie narzędzi IT w zarządzaniu produkcją, dane powinny być w jak największym stopniu zbierane i gromadzone cyfrowo. W praktyce oczywiście zawsze część informacji jest zbierana i wprowadzana ręcznie, ale jej źródłem są też interfejsy HMI lub rozmaite aplikacje zarządcze, a przede wszystkim konieczne jest pozyskiwanie danych z maszyn i urządzeń produkcyjnych.
Informacje zebrane w warstwie wykonawczej najlepiej i najdokładniej odzwierciedlają przebieg procesu produkcyjnego. Mogą one posłużyć do precyzyjnego przeanalizowania tego procesu, znalezienia obszarów nieefektywnych lub problematycznych, a w konsekwencji do jego zoptymalizowania.
Funkcje systemu MES jako dedykowanego systemu IT
Wg międzynarodowego standardu ANSI/ISA-95, który precyzuje pojęcia związane z systemami zarządczymi w przedsiębiorstwie i opisuje, w jaki sposób powinien być zorganizowany przepływ danych pomiędzy nimi, można wyróżnić cztery poziomy przedsiębiorstwa. Najniższy z nich to po prostu fizyczna warstwa produkcyjna: maszyny i urządzenia, a także czujniki. Wyżej znajduje się warstwa sterowania – tutaj pracują sterowniki i kontrolery obiektowe, a także urządzenia i oprogramowanie do monitoringu i wizualizacji (panele operatorskie, stacje HMI/SCADA).
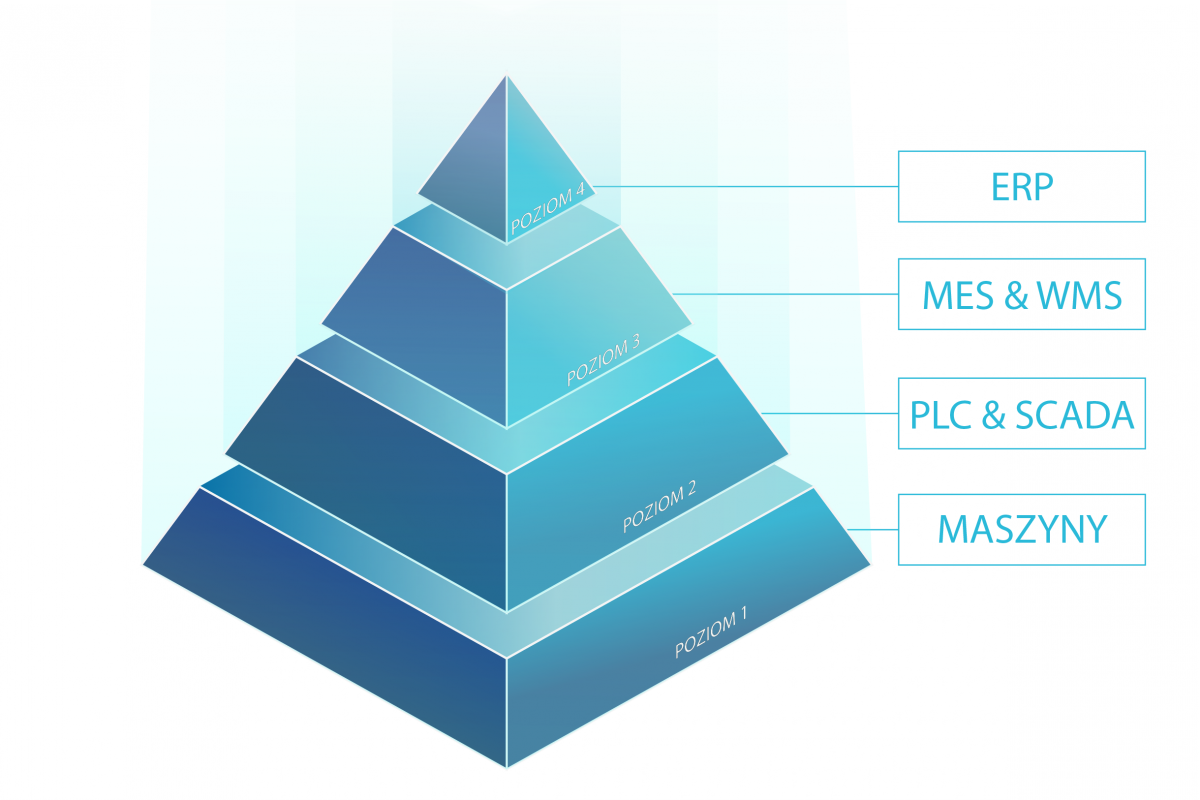
Dwa najwyższe poziomy to warstwa zarządzania. Szczyt struktury to systemy zarządzające całością przedsiębiorstwa – finansami, planowaniem i logistyką. Tu umiejscawiamy m.in. oprogramowanie ERP (z ang. Enterprise Resource Planning, czyli Systemy Zarządzania Przedsiębiorstwem). Natomiast poziom 3 to zarządzanie procesem produkcyjnym, a więc harmonogramowanie, monitorowanie realizacji poszczególnych zadań oraz optymalizacja procesu produkcyjnego. To jest właśnie miejsce, gdzie pozycjonujemy systemy MES. Jak widać, stanowi on swoisty pomost pomiędzy warstwą produkcyjną a biznesową.
Zadania realizowane przez MES można w uproszczeniu podzielić na trzy główne obszary:
- zarządzanie efektywnością produkcji,
- zarządzanie zleceniami produkcyjnymi i zadaniami,
- zarządzanie jakością.
Funkcjonalność pokrywająca wszystkie te obszary zapewnia pełną kontrolę nad całym procesem produkcyjnym. Warto jednak pamiętać, że możliwe jest wdrożenie systemu, który będzie obejmował tylko część zadań typowych dla MES.
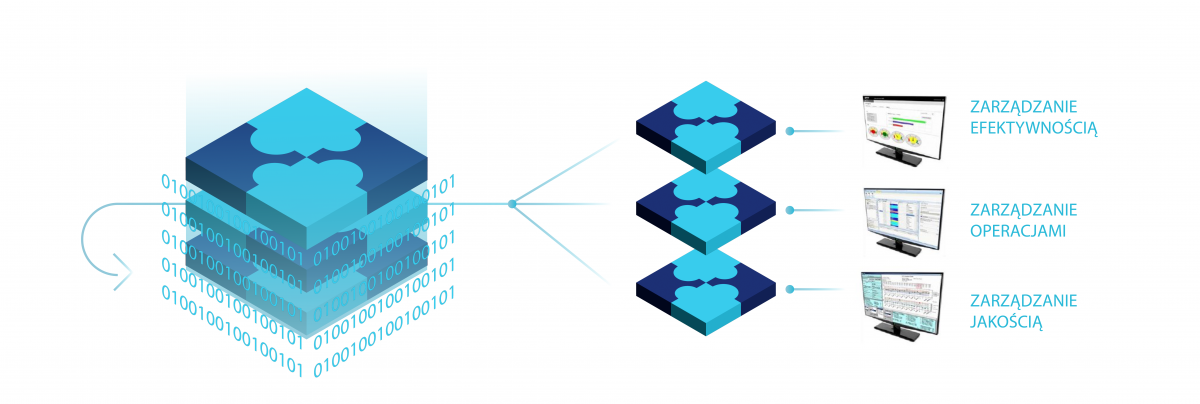
Zarządzanie efektywnością produkcji
System MES zapewnia wgląd w czasie rzeczywistym w kluczowe wskaźniki efektywności produkcji (KPI), takie jak np. OEE, zarówno dla poszczególnych maszyn, stanowisk roboczych, jak i całych linii. Oferuje również funkcje raportowe i diagnostyczne, obejmujące wyniki dla urządzeń i linii, poziom wykorzystania poszczególnych stanowisk oraz informacje takie, jak średni czas między awariami, średni czas do naprawy itp. Pozwala to na łatwe i skuteczne analizowanie przyczyn problemów z wydajnością maszyn i dostępnością zasobów.
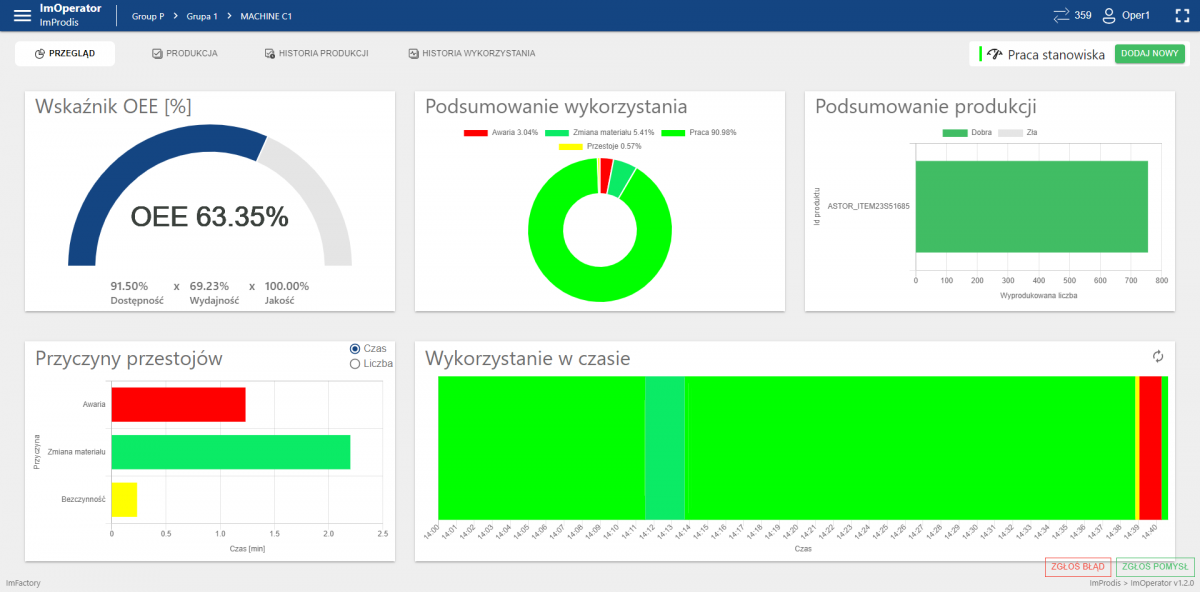
Najważniejszymi zadaniami realizowanymi przez system MES w tym obszarze są:
- Monitorowanie stanu zleceń produkcyjnych i przestrzegania harmonogramu z widocznością bieżących wyników produkcyjnych w porównaniu z planowanym tempem i czasem trwania produkcji.
- Automatyczne określanie bieżącego wąskiego gardła procesu poprzez weryfikację wydajności w rozbiciu na poszczególne operacje.
- Wykrywanie, przechwytywanie i przeglądanie zdarzeń związanych z użytkowaniem, takich jak przestoje sprzętu lub krótkie przerwy (mikroprzestoje) mające wpływ na dostępność.
- Automatyczne zbieranie danych poprzez integrację z systemami sterowania oraz interfejs użytkownika, umożliwiający efektywne zbieranie i uszczegóławianie danych przez operatorów i osoby nadzorujące.
Zarządzanie procesami produkcyjnymi i operacjami
System MES umożliwia dysponowanie, a także elastyczne zarządzanie zaplanowanymi zleceniami produkcyjnymi. Pozwala też nadzorować realizację zadań, zapewniając wgląd w czasie rzeczywistym w przebieg i aktualny stan produkcji oraz stanów magazynowych.

Najważniejszymi zadaniami realizowanymi przez system MES w tym obszarze są:
- Importowanie zleceń pracy z aplikacji zewnętrznej (np. ERP czy APS) lub tworzenie zleceń produkcyjnych ręcznie na podstawie zdefiniowanych wzorców tzw. procesów.
- Kolejkowanie zleceń produkcyjnych na maszynach.
- Określanie marszrut (BOR), list materiałowych (BOM), operacji i kroków.
- Przechwytywanie wszystkich zdarzeń związanych z realizacją zlecenia i zadania (np. zmiana statusu, zużycie, produkcja) w każdej operacji w ramach procesu.
- Rejestracja rozchodów i przychodów, budowanie genealogii produktu.
- Raportowanie przebiegu produkcji, zużycia materiałów itp. do aplikacji zewnętrznych (np. ERP) po zakończeniu zlecenia, na koniec zmiany lub w dowolnym momencie.
Zarządzanie jakością produkcji
Cyfrowe zarządzanie jakością zapewnia wszystkie możliwości niezbędne do tego, aby wdrożyć proces ciągłego doskonalenia jakości produkcji. Najważniejszymi zadaniami realizowanymi przez system MES w tym obszarze są:
- Realizacja planów prób jakościowych dzięki pełnej funkcjonalności automatycznego i ręcznego gromadzenia danych oraz dopasowania do zdarzeń związanych z realizacją zleceń roboczych.
- Wizualizacja stabilności procesu z wykorzystaniem kart kontrolnych.
- Integracja z oprogramowaniem do zarządzania przepływem pracy wspomagająca automatyzację procesów ręcznego gromadzenia danych oraz procedury dotyczące działań korygujących lub zapobiegawczych, co pozwala znacząco skrócić czas podejmowania działań.
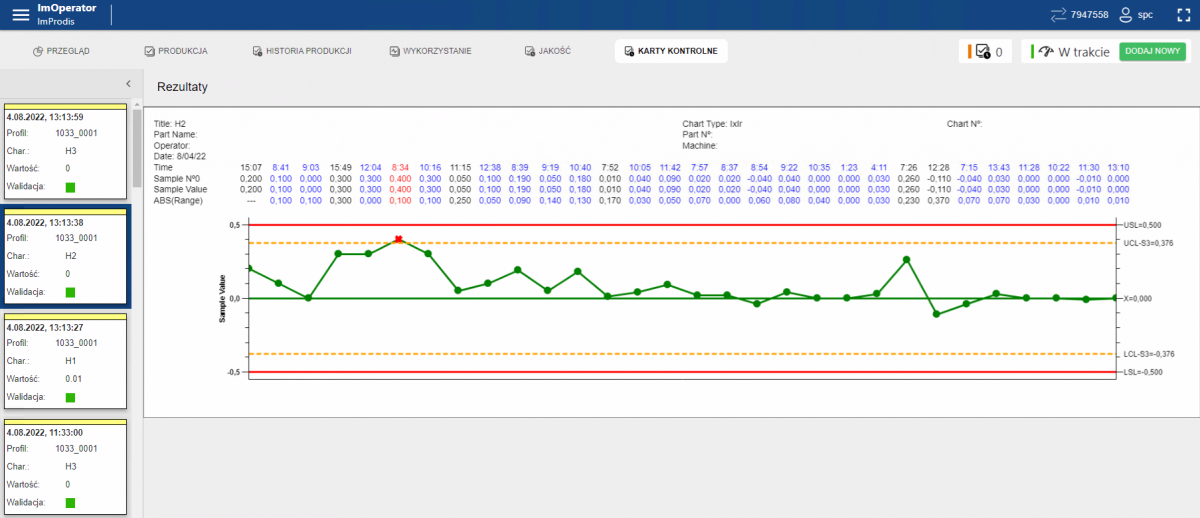
Korzyści z wdrożenia systemu MES
Możemy wskazać trzy główne obszary korzyści z zastosowania systemu MES do zarządzania procesem produkcyjnym. Są to:
- Zmniejszenie kosztów, a jednocześnie zwiększenie produktywności i jakości dzięki funkcjom MES
- Rozwój kompetencji decyzyjnych i wsparcia procesów decyzyjnych dzięki lepszej widoczności łańcucha dostaw i zmniejszeniu opóźnień w raportowaniu.
- Zapewnienie wiarygodnego źródła danych dla programów ciągłego doskonalenia produkcji.
Każda z nich jest istotnym przyczynkiem do uzyskania wymiernych korzyści finansowych, a tym samym szybkiego zwrotu z inwestycji.
Perspektywiczne spojrzenie na cyfryzację produkcji
Jak zatem we właściwy sposób przeprowadzić proces cyfryzacji przedsiębiorstwa? Jakie cechy powinny mieć aplikacje IT, aby efektywnie wspierać digitalizację zarówno w horyzoncie krótkoterminowym jak i długoterminowym?
Załóżmy, że mamy bieżącą potrzebę związaną z koniecznością monitorowania efektywności produkcji. Z łatwością znajdziemy na rynku kilka systemów „MES”, które w identyczny sposób będą tę potrzebę spełniać – biorąc pod uwagę funkcjonalność czy interfejs użytkownika. Ale czy wszystkie te systemy będą w równie dobry sposób wspierać kolejne kroki w cyfryzacji, a więc podejmowanie kolejnych wyzwań i spełnianie innych potrzeb?
Jeżeli skoncentrujemy się tylko na bieżącej potrzebie i nie będziemy patrzyć perspektywicznie, może okazać się, że nie. Dlatego tak istotne jest, aby myśleć o cyfryzacji jako procesie realizowanym krok po kroku, nie tracąc z pola widzenia docelowej wizji i stanu, do którego zmierzamy. Biorąc to pod uwagę możemy wyróżnić trzy podstawowe modele przeprowadzania transformacji cyfrowej. Przyjrzyjmy się im bliżej.
Metoda 1: Integracja wielu aplikacji
Metoda ta polega na wyszukiwaniu specjalizowanych aplikacji przeznaczonych do wykonywania konkretnych zadań, które wynikają z bieżących potrzeb na danym etapie procesu transformacji. Przykładowo identyfikujemy pewną potrzebę – problem lub wyzwanie, któremu należy sprostać, a następnie przeglądając ofertę rynkową znajdujemy aplikację, która tę potrzebę zaspokaja. Wdrażamy tę aplikację i obserwujemy efekty.
W kolejnym etapie pojawia się oczywiście kolejna potrzeba, którą należy zaspokoić. Ponownie zatem wyszukujemy odpowiednią aplikację i ją wdrażamy, jednocześnie integrując ją z pierwszą aplikacją, wdrożoną wcześniej. W następnym etapie pojawia się kolejne wyzwanie, a za nim kolejna, trzecia już aplikacja. Wdrażamy ją i oczywiście integrujemy z pozostałymi. W miarę pojawiania się kolejnych potrzeb konsekwentnie powtarzamy ten proces.
W efekcie potrzeby zostały zaspokojone, ale uzyskujemy system, który jest zbudowany z różnych aplikacji, połączonych złożoną siecią powiązań. Słowem – jest bardzo skomplikowany. Oznacza to, że zarówno jego bieżące utrzymanie, jak i dalszy rozwój są bardzo utrudnione. Stanowi to istotne ograniczenie dla dalszych kroków digitalizacji cyfrowej i procesów dostosowywania się do zmiennych potrzeb rynku.
Pewną zaletą tej metody może być fakt, że koszty inwestycji są niższe, niż w przypadku pozostałych metod. Z drugiej strony długofalowy potencjał korzyści jest tu zdecydowanie najniższy.
Metoda 2: Pakiet zintegrowanych, specjalizowanych modułów
Drugą możliwością jest wdrożenie jednego, zintegrowanego pakietu specjalizowanych aplikacji. Pakietem takim może być np. rozbudowany wielomodułowy system MES lub system ERP z dodatkowymi opcjami. Podstawowa zaleta tego rozwiązania polega na tym, że wiele obszarów produkcji objętych jest spójnym, zintegrowanym środowiskiem. Taki system po prostu zaspokaja wiele potrzeb jednocześnie, zwykle jednak i tak nie zaspokaja wszystkich. Prędzej czy później trzeba do niego dodawać dodatkowe aplikacje, odpowiadające na nowe pojawiające się potrzeby.
Tymczasem rozbudowa takiego zintegrowanego systemu często bywa utrudniona, albo wręcz nie jest możliwa bez udziału jego producenta. Tym samym uzyskaliśmy bardziej spójne środowisko, ale jednocześnie ograniczone – i tym samym wciąż niezadowalające. Dodatkowo najczęściej pakiety tego rodzaju składają się z modułów, które dość sztywno definiują określony interfejs oraz sposób pracy z nimi. Można je konfigurować, ale nie zawsze w pełni i nie w każdym aspekcie. Może się zatem okazać, że konieczne jest dostosowanie niektórych procesów w przedsiębiorstwie do aplikacji, bo odwrotnie się nie da.
W przypadku tej metody koszty inwestycji są zauważalnie wyższe, niż w przypadku metody pierwszej. Potencjał uzyskiwany w dłuższej perspektywie korzyści jest jednak w tym przypadku również wyższy.
Metoda 3: Elastyczne platformy digitalizacji ze specjalizowanymi modułami
Systemy budowane wg tego modelu pozornie mogą wyglądać podobnie do tych realizowanych metodą drugą (zintegrowanych pakietów). Składają się one również z modułów, które oferują gotowe funkcjonalności, odpowiadające za poszczególne obszary charakterystyczne dla systemów MES. Istotna różnica kryje się jednak „pod maską” takiego systemu. Każdy z jego elementów jest gotowym rozwiązaniem, ale jednocześnie zapewnia bardzo szeroki zakres konfiguracji i możliwość dostosowania do konkretnych potrzeb i wymagań. Dzięki temu nie musimy dostosowywać procesów firmowych do systemu informatycznego, bo każdy z elementów tego systemu można w pełni dostosować do istniejących procesów.
Elastyczne systemy dają użytkownikom możliwość tworzenia własnych samodzielnych aplikacji lub obiektów aplikacyjnych, zapewniając wszystkie niezbędne do tego celu narzędzia. Stanowią one tym samym platformę pozwalającą zbudować system informatyczny, który będzie nie tylko odpowiadał dokładnie naszym potrzebom, ale będzie też otwarty na modyfikacje i dalszą rozbudowę. Taka obiektowość platformy sprawia, że łatwo możemy dodawać do naszego systemu kolejne funkcjonalności i aplikacje, a także potem łatwo powielać je na kolejne maszyny, linie czy nawet całe zakłady produkcyjne.
W efekcie uzyskujemy system, w którym nie ma aż tak wielu trudnych w zarządzaniu połączeń między systemami. Jest więc łatwiejszy w utrzymaniu, ale także w rozbudowie, która z całą pewnością może być wymagana w kolejnych etapach cyfryzacji. Elastyczne platformy zapewniają też specjalizowane magistrale komunikacyjne, tzw. szyny danych (z ang. Enterprise Service Bus), pomiędzy systemami na różnych poziomach, z jednej strony biznesowych (ERP), a z drugiej produkcyjnych.
Transformacja realizowana w tym modelu wiąże się najczęściej z większymi kosztami inwestycji, niż w przypadku metod opisywanych wcześniej. W zamian jednak w dłuższej perspektywie czasowej przynosi ona przedsiębiorstwu zdecydowanie większe korzyści.
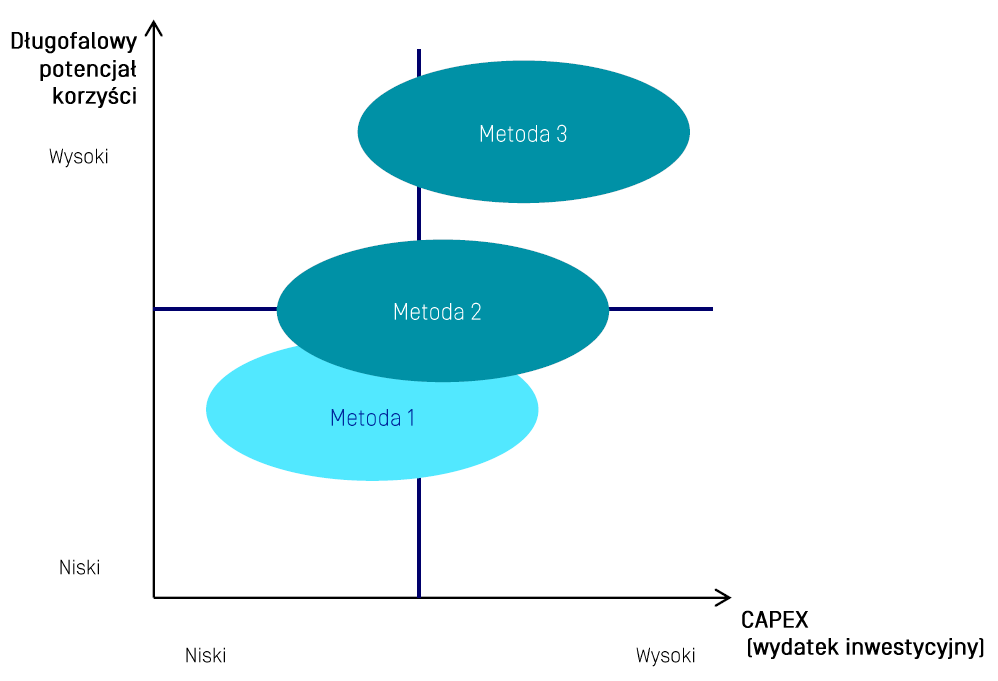
Wybór właściwego partnera transformacji cyfrowej
Niewątpliwie ważnym elementem projektu transformacji cyfrowej przedsiębiorstwa jest wybór odpowiedniego partnera, czyli specjalistycznej firmy, która będzie nas wspierała w realizacji tego procesu. Trzeba pamiętać, że na transformację cyfrową nie składa się wyłącznie wdrożenie takich czy innych systemów informatycznych. Niezwykle istotnym jej elementem jest również etap przygotowania cyfryzacji, a także wszystko to, co dzieje się po zakończeniu prac wdrożeniowych.
Biorąc to pod uwagę ważne jest, aby partner cyfryzacji nie tylko wspierał samo wdrożenie, ale też aby wspomógł jego przygotowanie oraz zapewnił opiekę powdrożeniową. Dlatego musi on rozumieć metody doskonalenia produkcji (takie jak Lean Manufacturing, Six Sigma, World Class Manufacturing, Continuous Improvement), a także potrafić „przełożyć” potrzeby biznesowe klienta na konkretne rozwiązania techniczne. Solidny partner pomaga klientowi dobrać rozwiązanie nie tylko w zakresie bieżącej potrzeby, ale także pod kątem kolejnych etapów cyfryzacji, tak aby wdrażany system nie stał się ograniczeniem w przyszłości.
Na etapie przygotowania procesu partner cyfryzacji wspiera klienta w zakresie:
- profesjonalnej oceny stanu przedsiębiorstwa, w tym dojrzałości cyfrowej organizacji,
- doboru rozwiązania odpowiadającego rzeczywistym potrzebom klienta,
- przygotowania klienta na zmianę.
Na etapie samego wdrożenia partner zapewnia:
- gruntowną wiedzę z zakresu przenoszenia procesów biznesowych, produkcyjnych oraz wspierających na poziom IT,
- wsparcie integracji systemów,
- wiedzę o najlepszych praktykach projektowych,
- aktywne wsparcie w realizacji trudnych etapów wdrożenia.
Z kolei po zakończeniu wdrożenia rolą partnera jest:
- serwisowanie systemu w ramach umowy serwisowej,
- tworzenie wizji i programu rozwoju w dłuższym horyzoncie czasowym,
- wszechstronne wsparcie klienta w jak najefektywniejszym wykorzystaniu wdrożonych narzędzi.
Istotną kompetencją partnerów cyfryzacji jest również znajomość metodyk zarządzania projektami – zarówno klasycznych (kaskadowych), jak i zwinnych (agile). Proces cyfryzacji z reguły jest długi i powinien być wdrażany fazami, a dobór metodyki zarządzania projektem powinien być dostosowany do skali wdrożenia oraz potrzeb klienta.
Redakcja: Mateusz Pierzchała
Autorzy: Paweł Firek, Adrian Szczypski, Aleksander Paul, Artur Masłowski, Michał Zieliński
O ImFactory
Improvement Factory [w skrócie ImFactory] część Grupy ASTOR, która powstała na fundamencie wewnętrznego centrum kompetencyjnego, MES Solutions by ASTOR, wyspecjalizowanego w systemach MES. Po 6. latach, z uwagi na dynamiczny rozwój rynku cyfrowych rozwiązań dla usprawniania procesów produkcyjnych w zakładach i fabrykach, spółka rozszerza swoją działalność w tym zakresie. Dostarcza Centralne Systemy IT dla produkcji, do których należą systemy klasy MES (Manufacturing Execution System), systemy do planowania produkcji APS (Advance Planning and Schedulling) oraz integracje systemów IT (Enterprise Service Bus). Zespół tworzą Inżynierowie – specjaliści w zakresie systemów IT dla przemysłu, kierownicy projektów oraz konsultanci w zakresie konsultingu technicznego i procesowego, co w efekcie pozwala firmom produkcyjnym na kompleksowe przeprowadzenie cyfryzacji procesów i ich usprawniania, a tym samym podnoszenia wartości przedsiębiorstw . Od 2021 r. ImFactory jest także Centrum Kompetencji AVEVA MES, które wspiera rozwój rynku MES w Europie Środkowo-Wschodniej