Historie sukcesu
HENKEL: redukcja kosztów w firmie produkcyjnej dzięki oszczędności zużycia energii o 9%
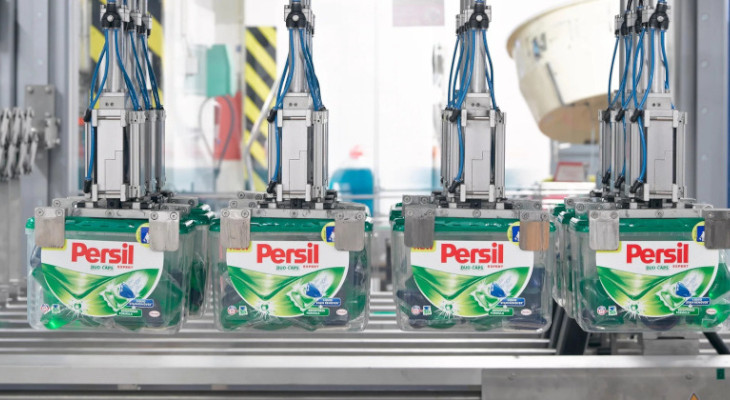
HENKEL: redukcja kosztów w firmie produkcyjnej dzięki oszczędności zużycia energii o 9%
„Firma Henkel zawsze miała dar do wdrażania kreatywnych pomysłów na efektywne oszczędzanie energii. Prawdziwym wyzwaniem jest tutaj posiadanie wiarygodnego zestawu danych.” – Dr. Johannes Holtbrügge, Menedżer projektu Environmental Management System w firmie Henkel.
Cele:
- zmniejszenie zużycia i kosztów energii oraz redukcja kosztów w firmie produkcyjnej,
- wdrożenie ISO 50001 we wszystkich zakładach produkcyjnych,
- zwiększenie efektywności łańcucha dostaw po stronie produkcji o 5 do 6% rocznie,
- wzrost wydajności produkcji o 75% do 2020 r.,
- zwiększenie efektywności o 300% do 2030 r.
Wyzwania:
- usprawnienie gromadzenia, wykorzystywania i przekazywania danych dotyczących zużycia energii i emisji w całym łańcuchu dostaw.
Rozwiązania:
- Platforma Systemowa Wonderware
- Wonderware Historian
- Wonderware MES Performance
- Wonderware Intelligence
Korzyści:
- zmniejszenie zużycia energii o 9%, co przekłada się na zaoszczędzone 15 mln EUR w kosztach energii,
- zmniejszenie ilości odpadów z linii napełniania i wyeliminowanie wszystkich błędów etykietowania spowodowało uzyskanie 100% jakości etykiet,
- poprawa OEE o 4,5% po roku wdrożenia Wonderware.
HENKEL – geneza cyfrowej transformacji
Henkel AG & Co. działa w branży pakowanych towarów konsumenckich (CPG) z siedzibą w Düsseldorfie-Holthausen w Niemczech. Została założona w 1876 roku i zatrudnia ponad 50 000 pracowników na całym świecie.
W 2016 r. firma Henkel osiągnęła 18,7 mld EUR przychodów i około 2,1 mld EUR rocznych zysków. Imponujący sukces firmy jest wynikiem jasnej, długoterminowej strategii opartej na trzech filarach: ciągłego skupienia na potrzebach klientów, zrównoważonego rozwoju i innowacji.
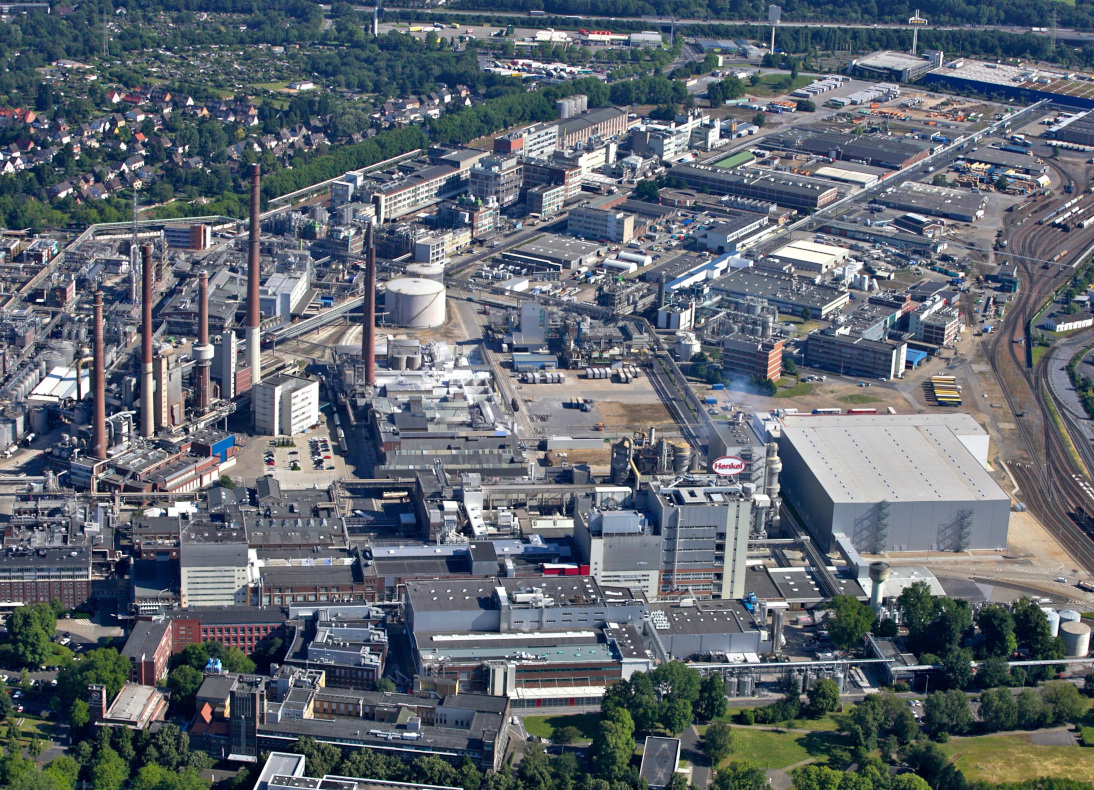
Zakłady produkcyjne Henkel w Düsseldorfie-Holthausen
Henkel działa globalnie dzięki wiodącym innowacjom, markom i technologiom w trzech obszarach: kleje konsumenckie i budowlane, pielęgnacja urody oraz środki do prania i pielęgnacji domu. Produkty z zakresu środków piorących i do pielęgnacji domu stanowi 31% całkowitej sprzedaży firmy, o wartości 5.795 milionów EUR. Produkty z działu kosmetycznego stanowią 20 procent całkowitej sprzedaży firmy o wartości 3 838 milionów EUR. Kleje to 48% całkowitej sprzedaży firmy o wartości 8 961 000 EUR.
Wprowadzając cyfrową transformację w całej firmie, Henkel dąży do osiągnięcia skutecznego wzrostu, wzmocnienia relacji z klientami i optymalizacji procesów. W tym celu wdrożono serię inicjatyw pod nazwą Henkel 2020+, które mają zostać zrealizowane do roku 2020. Inicjatywy mają wesprzeć wdrażanie zrównoważonych innowacji przy jednoczesnej poprawie efektywnego gospodarowania zasobami w tworzeniu wartości dodanej.
Geneza projektu w firmie Henkel
Henkel produkuje bardzo szeroką gamę produktów, m.in.: detergenty, produkty do zmywania naczyń, środki do czyszczenia powierzchni i środki do mycia toalet. Znane i popularne produkty to Persil, Somat, Pril i Purex. Firma produkuje je w 31 zakładach produkcyjnych na całym świecie. Ciągłe doskonalenie produkcji powoduje poszukiwanie coraz lepszych systemowych sposobów gromadzenia, wykorzystywania i udostępniania danych dotyczących zużycia i emisji w całym łańcuchu dostaw.
Kryteria wyboru systemu zarządzania energią
Pierwsza faza tworzenia cyfrowej infrastruktury – systemu zarządzania środowiskowego (Environmental Management System – EMS) – polegała na wdrożeniu systemu monitorowania zużycia energii.
Wymagania co do systemu były następujące:
- globalne rozwiązanie dla wszystkich zakładów, instalowane i utrzymywane centralnie,
- oparcie na ujednoliconej bazie danych, umożliwiając uporządkowane wyszukiwanie i agregowanie danych o użytkowaniu,
- elastyczność i uniwersalność pozyskiwania danych – możliwość integrowania wszelkiego wcześniej dostępnego oprogramowania z systemem,
- raportowanie kluczowych wskaźników efektywności (KPI) i centralna analiza porównawcza wszystkich zakładów produkcyjnych (w celu wymiany najlepszych praktyk),
- działanie w trybie online i w czasie rzeczywistym – informacje powinny być dostępne w dowolnym czasie i z dowolnego miejsca w sieci zakładów Henkel,
- skuteczny bufor w razie problemów z siecią.
Wdrożenie – modelowa redukcja kosztów w firmie produkcyjnej
W celu poprawy efektywności gospodarowania zasobami w łańcuchu dostaw po stronie produkcji o 5 do 6% rocznie i docelowo 3-krotnego zwiększenia efektywności do 2030 r. zdecydowano o wyborze rozwiązań Wonderware dla transformacji cyfrowej zakładów produkcyjnych, dostarczane obecnie przez AVEVA.
Firma Henkel powierzyła wdrożenie systemu monitorowania zużycia energii doświadczonemu niemieckiemu integratorowi, EMP GmbH, oficjalnie certyfikowanemu jako Wonderware System Integrator. EMP jest ekspertem w dziedzinie kompleksowych rozwiązań dla systemów zarządzania energią, automatyki budynkowej i wsparcia zarządzania operacyjnego.
Projekt został uruchomiony w 2013 r. i zakończony w połowie 2015 r. Wstępnie skonfigurowane rozwiązanie do monitorowania zużycia energii zostało utworzone przy użyciu Platformy Systemowej Wonderware i oprogramowania Wonderware Historian. W trakcie realizacji, do standardowej aplikacji monitorowania zużycia energii zostały dodane dodatkowe moduły.
Platforma Systemowa Wonderware to uniwersalny, skalowalny system zarządzania produkcją, umożliwiający łączenie dowolnego sprzętu, obecnego lub przyszłego, dowolnych producentów i niezależne konfigurowanie domen, baz danych, aplikacji i urządzeń, bez wpływu na architekturę systemu.
PSW umożliwia integrowanie najlepszych w swojej klasie rozwiązań sprzętowych, z pełną świadomością, że będą się one poprawnie komunikować i integrować z EMS. Obecne i przyszłe standardy komunikacji sprzętowej w różnych globalnych fabrykach, takie jak PLC, Modbus, Ethernet, serwery OPC i pliki CSV, są skutecznie wspierane w rozwiązaniu.
System monitoringu zużycia energii w firmie produkcyjnej
Głównym wyzwaniem związanym z wdrożeniem systemu monitorowania zużycia energii w firmie Henkel był standard pomiaru. Określono zatem minimalne wymogi techniczne dla połączenia z EMS dla wszystkich urządzeń na zasadzie jeden do jednego. Jednocześnie uwzględniono wszystkie właściwe dla danej fabryki wartości graniczne i konkretne funkcjonalności.
Do września 2017 r. do systemu włączono ponad 3000 punktów pomiaru zużycia energii elektrycznej, paliw kopalnych, sprężonego powietrza, pary wodnej, wody i ścieków. Pomiary te uwzględniają nie tylko zużycie energii na poziomie całej fabryki, ale także w poszczególnych obszarach produkcyjnych i technologicznych. Teraz zużycie jest mierzone dokładniej, a wyniki analizowane i oceniane pod kątem kluczowych parametrów. Dzięki temu Henkel może wdrażać działania naprawcze, co prowadzi do zmniejszenia zużycia energii. Tym samym redukcja kosztów w firmie produkcyjnej dzieje się z korzyścią dla całego przedsiębiorstwa.
Z rozwiązania korzysta obecnie 600 użytkowników. W halach produkcyjnych kluczowe dane produkcyjne są wyświetlane na panelach operatorskich i komputerach przemysłowych, dzięki czemu zespoły robocze mogą regularnie omawiać kwestie wydajności.
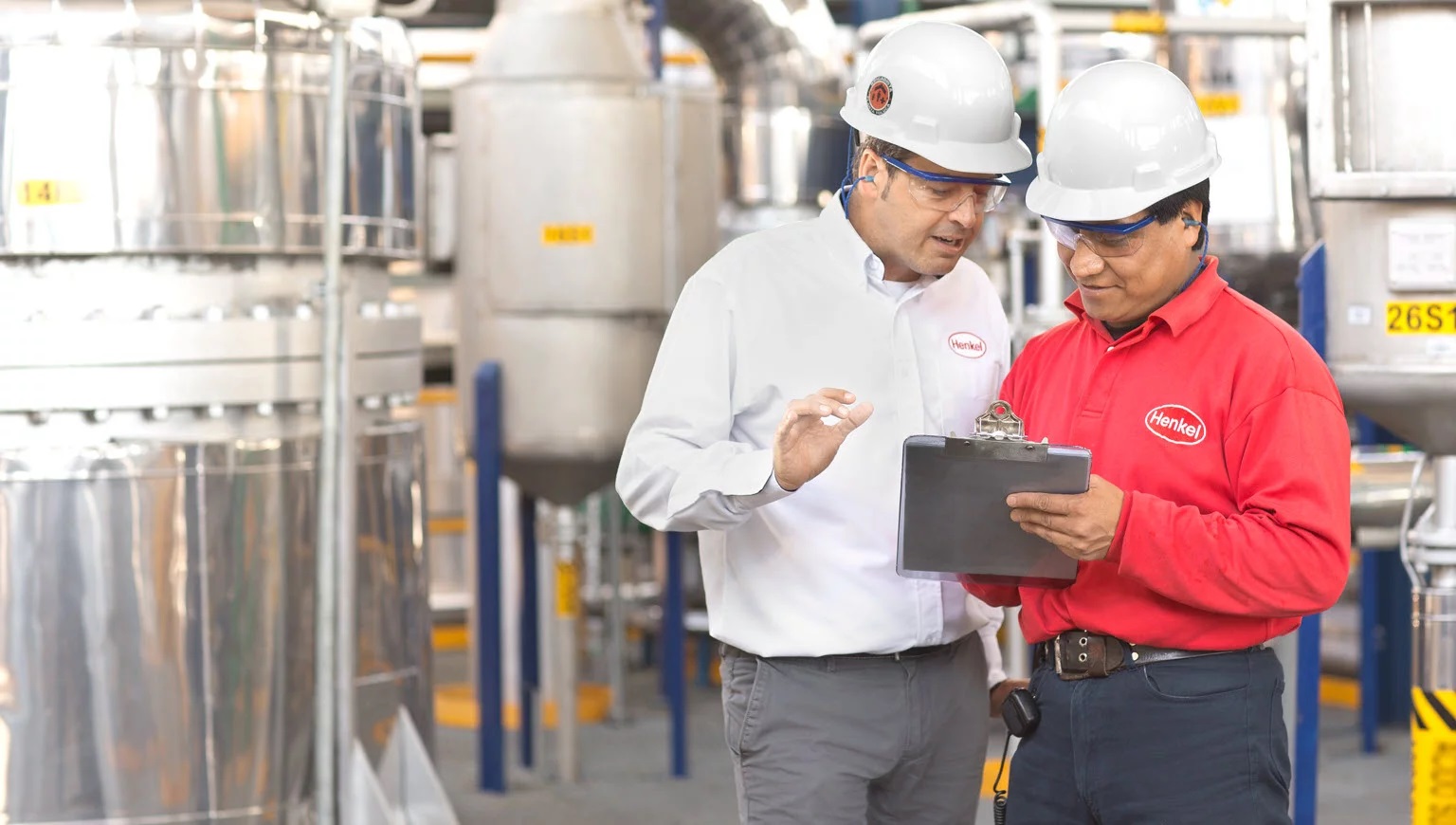
Najlepsze praktyki i standaryzacja
Udoskonalenia uzyskane dzięki dzieleniu się najlepszymi praktykami między zakładami sieci Henkel można łatwo replikować dzięki jednolitym strukturom w ramach globalnego systemu Henkel i możliwościom porównania specyfiki zakładu i procesów produkcyjnych. Specjalne sesje szkoleniowe dla użytkowników wspierają sukces wdrożenia i korzystanie z nowego systemu w trybie online.
Gromadzenie i analiza danych
Firmy z geograficznie rozmieszczonymi zakładami produkcyjnymi, które mają złożone procesy i systemy, stają przed wyzwaniem wytwarzania niezbędnych informacji, które poprawiałyby efektywność operacyjną.
Taką poprawę wydajności zapewniają następujące funkcje Platformy Systemowej Wonderware:
- jest to otwarta platforma inżynieryjno-wykonawcza, do zarządzania produkcją, procesami biznesowymi, produkcyjnymi i wytwórczymi oraz danymi, umożliwiająca wielopoziomową integrację z systemami zakładu produkcyjnego, w tym np. ERP,
- oferuje szeroką gamę aplikacji przemysłowych, umożliwiających szybką optymalizację wydajności systemów,
- zapewnia podejście obiektowe, pozwalające na wielokrotne modelowanie, uniwersalność sprzętową i integralną standaryzację procesów operacyjnych.
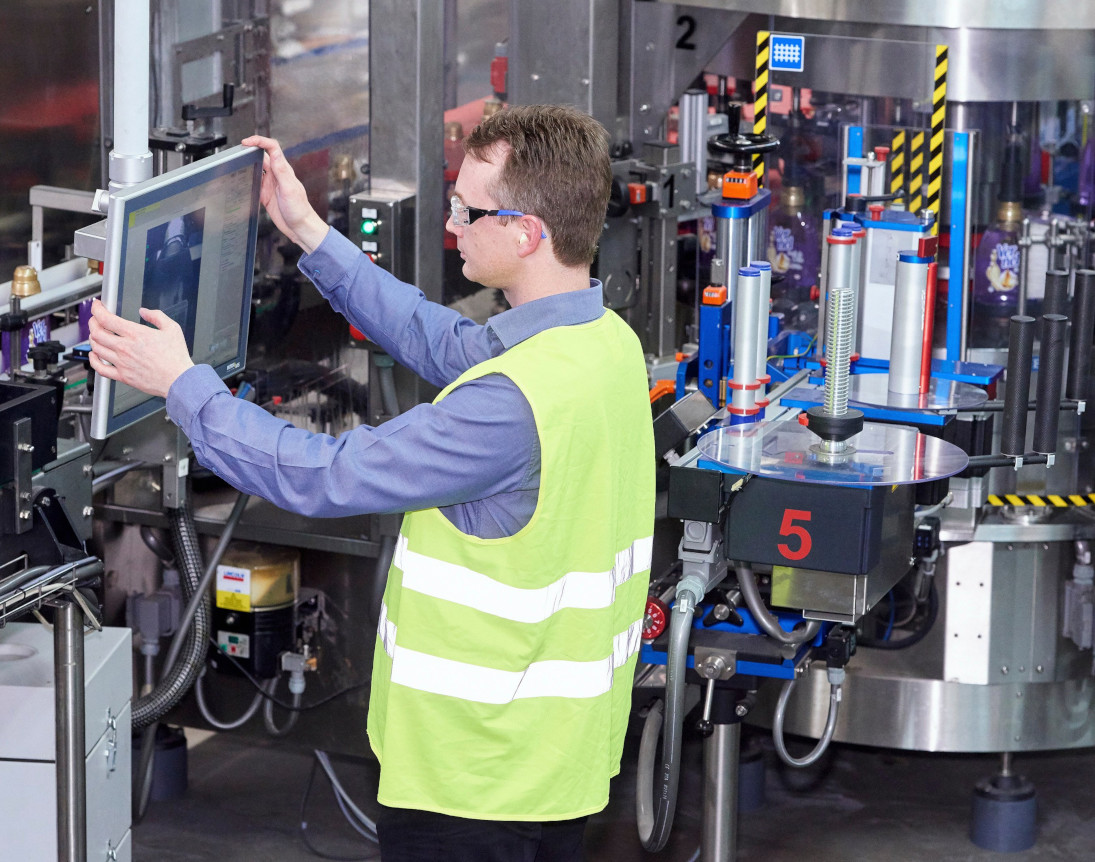
Integracja systemu etykietowania, OEE i SAP
W 2014 roku cyfrowa infrastruktura Wonderware została zintegrowana z systemem kontroli jakości etykiet. Etykiety z każdej butelki są fotografowane, a wynikowa ocena pomaga poprawić jakość i zmniejszyć ilość odpadów. Gromadzone są również dane statystyczne i przesyłane do centralnego systemu raportowania. Dzięki interfejsowi SAP, dane związane ze stanem linii i maszyn można teraz połączyć z danymi zlecenia i analizować je na potrzeby optymalizacji.
W 2015 r. Henkel wdrożył Wonderware MES do monitorowania wydajności linii napełniającej w oparciu o wskaźnik całkowitej efektywności wyposażenia (OEE). Zbierane i analizowane są także dane dotyczące m.in. mikroprzestojów.
Informacje na temat odpadów umożliwiają ukierunkowaną poprawę i oszczędności dzięki wydajnemu wykorzystaniu zasobów, usprawnieniu operacji pakowania i zmniejszonemu zużyciu energii.
Wymóg wydatków inwestycyjnych (CAPEX) jest również zredukowany do około trzech lub czterech dodatkowych linii. W 2016 roku, firma Henkel zainstalowała Wonderware Access Anywhere do wizualizacji i analizy danych gromadzonych ze wszystkich zintegrowanych ze sobą systemów.
Wykorzystanie danych pogodowych
W 2017 r. zainstalowano czujniki do rejestrowania danych pogodowych w zakładach produkcyjnych wydziału środków piorących i do pielęgnacji domu. Poprzez korelację zużycia energii z warunkami atmosferycznymi, Henkel określa, w jaki sposób temperatura zewnętrzna i wilgotność wpływają na zużycie energii. Pozwala to na dalsze udoskonalanie produkcji, zużycia energii i planowania logistycznego.
Korzyści – redukcja kosztów w firmie produkcyjnej… i więcej!
Nowy system w oparciu o rozwiązania Wonderware obniżył zużycie energii (mierzone w KWh/t) o 9 procent od 2011 r. Przyczynił się do ogólnego zmniejszenia wydatków na energię w sektorze technologii prania i pielęgnacji domu o 15 milionów euro.
Henkel jest w stanie zmniejszyć ilość odpadów z linii napełniania i wyeliminować praktycznie wszystkie nieprawidłowe etykiety (globalnie 100-procentowa jakość etykiety na zejściu z linii i > 99,8% przy pierwszym nałożeniu etykiety). Prowadzi to do znacznych oszczędności kosztów pakowania.
Cyfrowa transformacja dzięki Platformie Systemowej Wonderware wdrożona w wydziale środków piorących i do pielęgnacji domu okazała się elastycznym i skalowalnym rozwiązaniem, które pomaga firmie osiągać ambitne cele. Istniejąca infrastruktura i zbiory danych zostały zintegrowane i ujednolicone w możliwie największym stopniu. W istocie nie ma ograniczeń dla przyszłej automatyzacji i optymalizacji procesów tworzenia wartości dla klienta w firmie Henkel.
Dr. Johannes Holtbrügge Henkel, Menedżer projektu EMS w firmie Henkel.
„Firma Henkel zawsze miała dar do wdrażania kreatywnych pomysłów na efektywną redukcję kosztów w firmie produkcyjnej dzięki oszczędzaniu zużycia energii. Prawdziwym wyzwaniem jest tutaj posiadanie dobrej puli danych.”
W przyszłości Henkel będzie konsekwentnie dążyła do osiągnięcia swoich ambitnych celów w zakresie zrównoważonego rozwoju. Ta przyszłość ściśle wiąże się z cyfrową transformacją procesów tworzenia wartości dla klienta.

Stwórz własny System Zarządzania Energią.
W ten sposób dowiesz się, ile energii zużywa Twój wydział produkcji. Oszczędzisz nawet do -20% kosztów energii. Zobacz nasze referencje.
3 pytania
odpowiada dr Dirk Holbach, Wiceprezes ds. łańcucha dostaw w wydziale środków piorących i pielęgnacji domu firmy Henkel:
1. Jaka jest Pańska wizja zrównoważonego zarządzania łańcuchem dostaw w firmie Henkel?
„Zrównoważony rozwój i efektywne wykorzystanie zasobów są mocno zakorzenione w wartościach firmy Henkel – i to nie jest u nas nic nowego. Byliśmy jedną z pierwszych firm produkcyjnych, które rozpoczęły publikowanie rocznego raportu dotyczącego zrównoważonego rozwoju. Naszą ambicją są cele długoterminowe i jesteśmy dumni, że nasze zaangażowanie jest doceniane przez osoby z zewnątrz. Firma produkcyjna Henkel znalazła się już w indeksie Dow Jones Sustainability Index (DJSI) co najmniej 15 razy, a w tym roku występuje jako lider swojej grupy branżowej. Wkład łańcucha dostaw w rozwój zrównoważony jest znaczący, ponieważ dzięki naszym licznym fabrykom i magazynom mamy ogromny potencjał do wprowadzania ulepszeń, którymi dysponujemy”
2. Jakie korzyści dla Henkel płyną z projektu systemu zarządzania energią EMS?
„W projekcie tym z powodzeniem udostępniamy w czasie rzeczywistym dane dotyczące naszego globalnego zużycia energii menedżerom łańcucha dostaw. Jest to ogromny krok naprzód. Szczególnie po wprowadzeniu jasnych działań optymalizacyjnych w ciągu ostatnich kilku lat, coraz bardziej skupiamy się na analizie porównawczej. Dzięki temu możemy nadal znacząco przyczyniać się do osiągania naszych celów w zakresie zrównoważonego rozwoju”.
3. Dlaczego wybraliście rozwiązania Wonderware do transformacji cyfrowej?
„Dla firmy Henkel ważne jest posiadanie globalnego partnera, który czynnie nas wspiera w naszej działalności w zakresie produktów szybkozbywalnych (FMCG). Jedną z głównych zalet była modułowa struktura rozwiązań Wonderware, pozwalająca na wybieranie modułów w oparciu o indywidualne wymagania i szybkie ich wdrażanie”.
Opracowano na podstawie materiałów firmy AVEVA – www.aveva.com
Przeczytaj o tym jak zminimalizować skutki podwyżki cen energii elektrycznej.